While one leading asphalt plant manufacturer is claiming a RAP production first, another is proving a big success in one part of Eastern Europe. Guy Woodford reports Astec Industries is continuing its track record for innovation by claiming it is the only asphalt plant manufacturer offering asphalt mix producers a 100% RAP [Recycled Asphalt Pavement] plant. With the addition of the Conexpo 2014 launched RAP KING plant to its product line, Astec says it is now able to offer a complete array of plants coverin
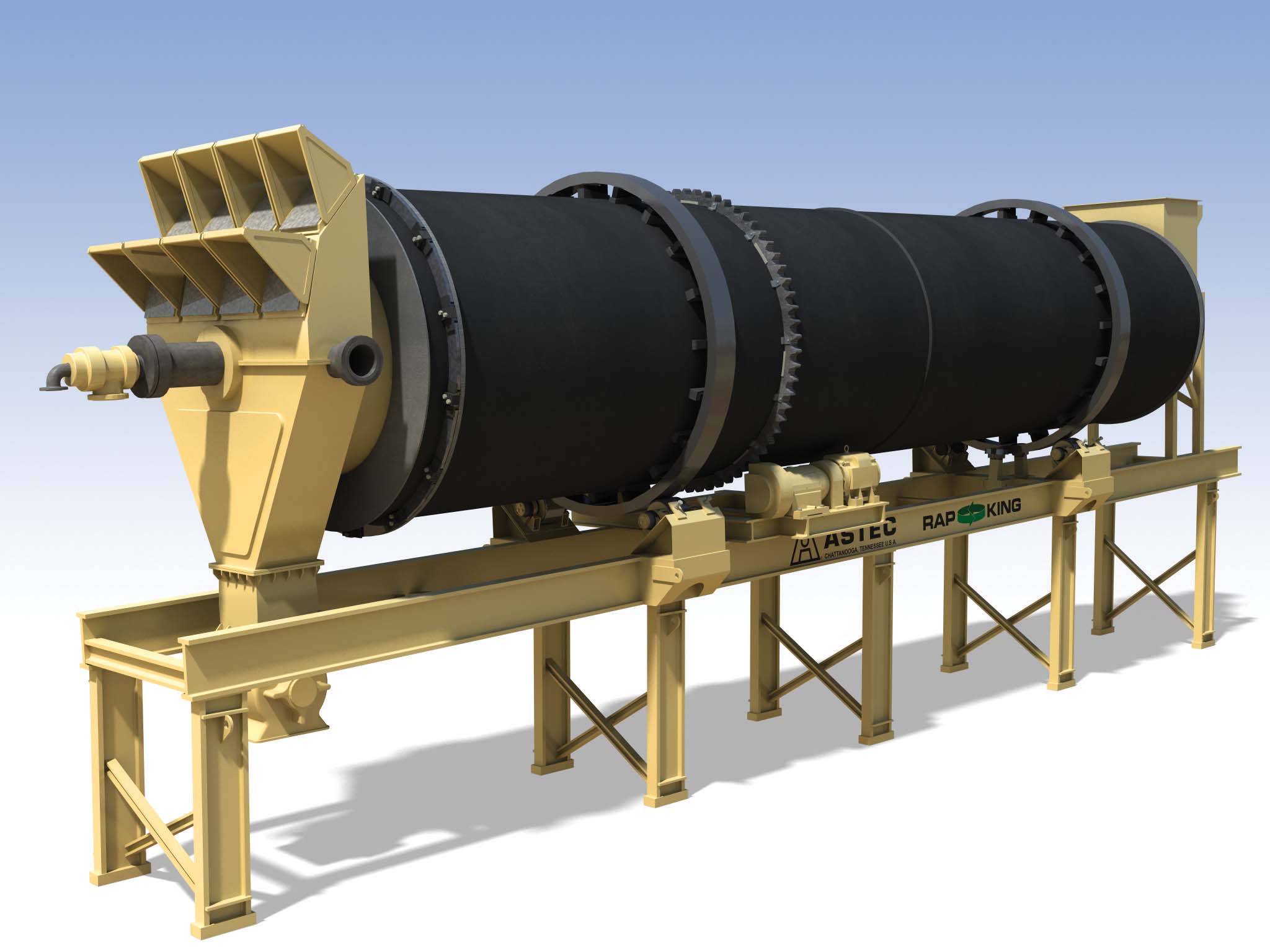
Astec’s Conexpo 2014 launched RAP KING is said by the US firm to be capable of 100% RAP production
While one leading asphalt plant manufacturer is claiming a RAP production first, another is proving a big success in one part of Eastern Europe. Guy Woodford reports
681 Astec Industries is continuing its track record for innovation by claiming it is the only asphalt plant manufacturer offering asphalt mix producers a 100% RAP [Recycled Asphalt Pavement] plant.
With the addition of the Conexpo 2014 launched RAP KING plant to its product line, Astec says it is now able to offer a complete array of plants covering the spectrum from 0%-100% RAP usage.
Astec president Malcolm Swanson said, “The RAP KING 100% RAP plant represents the culmination of efforts to offer producers a viable option for safely and efficiently producing a mix with only RAP.”
Meanwhile as RAP usage continues to increase as a way for producers to keep costs down while utilising stockpiles of reclaimed asphalt pavement, Astec has also increased the ability of its signature Double Barrel drum dryer/mixer to handle RAP. The Astec Double Barrel HR now includes enhancements to the drum which allows use of up to 65% RAP. A 1/8 model of the new high RAP Double Barrel drum was on display during Conexpo 2014 in March 2014.
“The Double Barrel HR is a key product in the Astec line. It fulfils a need for those producers who already run high percentages of RAP and in whose markets the trend toward running more recycle is expected to increase,” said Swanson.
The 120 MTPH Voyager plant has also recently been unveiled by Astec. The Voyager 120 offers a compact, highly portable design. It is said to be the first plant in its class with the ability to run up to 30% RAP.
The Astec Voyager 120 is built around a counter flow drum featuring Astec v-fights. The v-flights provide greater uniformity of the aggregate veil during the drying process, which results in better heat transfer, a reduction of fuel use and increased productivity.
To enhance portability, a hydraulically driven swing out drag and batcher can be set and ready to go in about 10 minutes. Other features include a reverse pulse baghouse, a controls cab with fully automated PLC controls, gravity take-up with direct drive, air ride suspension and up to five cold feed bins and two RAP bins.
Astec executive vice president Steve Claude said, “Astec is excited about the opportunities for the Voyager 120. Initial feedback from the industry has been extremely positive. Several orders for this plant have already been booked with the first production model set to ship immediately.”
The Black Sea Group company was founded in April 2005 and since then it has implemented numerous road construction projects throughout the Georgian market.
After being assigned major construction projects including the Zahesi – Natahtari section of the international road Tbilisi – Seneki – Leselidze, and the rehabilitation of the Qveda Saqara-Sazano road, in September 2013 the group decided to make a key investment by purchasing a high performance asphalt plant Marini Top Tower 3000 P (production up to 240 tonnes/hour) including a sizeable bitumen park (8 bitumen tanks – 2 of them having agitators for modified bitumen) in order to successfully manage production peaks and all the difficulties related to bitumen supply.
Another very important issue in plant definition was the possibility of RAP use.273 Marini’s technical team were asked by the Black Sea Group for a plant that would give them maximum flexibility, while also being capable of using very high RAP percentages. For this reason, Black Sea Group initially decided to pre-treat the RAP in order to guarantee the quality of the old bitumen and the size of the recovered aggregates. The firm chose its Marini Top Tower 3000 P plant solution with one line to the dryer (recycling ring), offering up to 35% RAP recycling.
In order to be as innovative as possible, Black Sea also bought a polymer modifier bitumen plant modiFALT20 (production up to 20tonnes/hour) and a cold mix asphalt plant coldFALT (production up to 400tonnes/hour), which were specially produced and custom built by Marini MAKINA, then installed in Agaiani – the company’s production base.
The above mentioned plant park enables Black Sea to fully satisfy existing international market requirements and to guarantee successful implementation of international projects. The cold mix asphalt plant allows production of asphalt concrete pavement throughout all seasons, with consequent quick, uninterrupted and qualified project performance.
Advanced technical equipment and modern laboratory services meet the most stringent criteria in terms of mix design, preparation of trial samples, field laboratory investigations and testing, and provide fast and qualified supply of multi-design materials (open graded mastic asphalt, modified asphalt and bitumen, cold and recycled asphalt) for Black Sea’s ongoing projects.
In order to promote the use of advanced technical solutions with high performance, flexibility and versatility, Amiran Mamutchadze, director of Black Sea, organised the ‘Asphalt Pavement 2014’ event at its headquarters on 6-7 March 2014, attended by all the major authorities and construction firms in Georgia’s road sector, where all the company’s equipment and innovative products were on show.
NAPA survey shows US warming to warm-mix asphalt
According to a recent survey measuring the use of recycled materials and warm-mix asphalt usage in the United States, almost 25% of mixtures used during the 2012 construction season were reported to incorporate warm-mix asphalt (WMA) technologies.
There was approximately 78.65 million tonnes of WMA produced by 1,141 asphalt plants in the US during the same period, according to the survey, which was conducted by the3464 National Asphalt Pavement Association (NAPA) and contracted to the 2410 Federal Highway Administration (FHWA).
It represents a 416% jump in warm mix use since a 2009 survey.
The report notes that WMA uses less energy to produce, leading to lower emissions and better worker safety
According to US Secretary of Transportation Anthony Foxx, the use of WMA is expected to create US$3.6 billion in energy cost savings by 2020.
The survey also found an increase in the use of reclaimed asphalt pavement (RAP) and recycled asphalt shingles (RAS), 61.96 million tonnes and 1.68 million tonnes collectively.
“Ensuring high performance roads at a cost-effective price has always been a goal for the asphalt pavement industry. It has spurred us to continue to look for new solutions and to put innovations into practice,” said NAPA president Mike Acott.
“This survey reflects how the industry is rapidly putting sustainable innovations, such as warm-mix asphalt, to use to ensure that drivers get the smooth, dependable roads they want at a price taxpayers can afford.”
The use of RAS has shot up 56% since 2011 and 165% since 2009, while RAP usage grew almost 22% since 2009.
The survey reported 98% of producers used RAP in their mixes.
Also, for the first time, the survey took a look at the use of ground tyre rubber, steel and blast furnace slags and other recycled materials, though estimates were not calculated.
With the addition of the Conexpo 2014 launched RAP KING plant to its product line, Astec says it is now able to offer a complete array of plants covering the spectrum from 0%-100% RAP usage.
Astec president Malcolm Swanson said, “The RAP KING 100% RAP plant represents the culmination of efforts to offer producers a viable option for safely and efficiently producing a mix with only RAP.”
Meanwhile as RAP usage continues to increase as a way for producers to keep costs down while utilising stockpiles of reclaimed asphalt pavement, Astec has also increased the ability of its signature Double Barrel drum dryer/mixer to handle RAP. The Astec Double Barrel HR now includes enhancements to the drum which allows use of up to 65% RAP. A 1/8 model of the new high RAP Double Barrel drum was on display during Conexpo 2014 in March 2014.
“The Double Barrel HR is a key product in the Astec line. It fulfils a need for those producers who already run high percentages of RAP and in whose markets the trend toward running more recycle is expected to increase,” said Swanson.
The 120 MTPH Voyager plant has also recently been unveiled by Astec. The Voyager 120 offers a compact, highly portable design. It is said to be the first plant in its class with the ability to run up to 30% RAP.
The Astec Voyager 120 is built around a counter flow drum featuring Astec v-fights. The v-flights provide greater uniformity of the aggregate veil during the drying process, which results in better heat transfer, a reduction of fuel use and increased productivity.
To enhance portability, a hydraulically driven swing out drag and batcher can be set and ready to go in about 10 minutes. Other features include a reverse pulse baghouse, a controls cab with fully automated PLC controls, gravity take-up with direct drive, air ride suspension and up to five cold feed bins and two RAP bins.
Astec executive vice president Steve Claude said, “Astec is excited about the opportunities for the Voyager 120. Initial feedback from the industry has been extremely positive. Several orders for this plant have already been booked with the first production model set to ship immediately.”
The Black Sea Group company was founded in April 2005 and since then it has implemented numerous road construction projects throughout the Georgian market.
After being assigned major construction projects including the Zahesi – Natahtari section of the international road Tbilisi – Seneki – Leselidze, and the rehabilitation of the Qveda Saqara-Sazano road, in September 2013 the group decided to make a key investment by purchasing a high performance asphalt plant Marini Top Tower 3000 P (production up to 240 tonnes/hour) including a sizeable bitumen park (8 bitumen tanks – 2 of them having agitators for modified bitumen) in order to successfully manage production peaks and all the difficulties related to bitumen supply.
Another very important issue in plant definition was the possibility of RAP use.
In order to be as innovative as possible, Black Sea also bought a polymer modifier bitumen plant modiFALT20 (production up to 20tonnes/hour) and a cold mix asphalt plant coldFALT (production up to 400tonnes/hour), which were specially produced and custom built by Marini MAKINA, then installed in Agaiani – the company’s production base.
The above mentioned plant park enables Black Sea to fully satisfy existing international market requirements and to guarantee successful implementation of international projects. The cold mix asphalt plant allows production of asphalt concrete pavement throughout all seasons, with consequent quick, uninterrupted and qualified project performance.
Advanced technical equipment and modern laboratory services meet the most stringent criteria in terms of mix design, preparation of trial samples, field laboratory investigations and testing, and provide fast and qualified supply of multi-design materials (open graded mastic asphalt, modified asphalt and bitumen, cold and recycled asphalt) for Black Sea’s ongoing projects.
In order to promote the use of advanced technical solutions with high performance, flexibility and versatility, Amiran Mamutchadze, director of Black Sea, organised the ‘Asphalt Pavement 2014’ event at its headquarters on 6-7 March 2014, attended by all the major authorities and construction firms in Georgia’s road sector, where all the company’s equipment and innovative products were on show.
NAPA survey shows US warming to warm-mix asphalt
According to a recent survey measuring the use of recycled materials and warm-mix asphalt usage in the United States, almost 25% of mixtures used during the 2012 construction season were reported to incorporate warm-mix asphalt (WMA) technologies.
There was approximately 78.65 million tonnes of WMA produced by 1,141 asphalt plants in the US during the same period, according to the survey, which was conducted by the
It represents a 416% jump in warm mix use since a 2009 survey.
The report notes that WMA uses less energy to produce, leading to lower emissions and better worker safety
According to US Secretary of Transportation Anthony Foxx, the use of WMA is expected to create US$3.6 billion in energy cost savings by 2020.
The survey also found an increase in the use of reclaimed asphalt pavement (RAP) and recycled asphalt shingles (RAS), 61.96 million tonnes and 1.68 million tonnes collectively.
“Ensuring high performance roads at a cost-effective price has always been a goal for the asphalt pavement industry. It has spurred us to continue to look for new solutions and to put innovations into practice,” said NAPA president Mike Acott.
“This survey reflects how the industry is rapidly putting sustainable innovations, such as warm-mix asphalt, to use to ensure that drivers get the smooth, dependable roads they want at a price taxpayers can afford.”
The use of RAS has shot up 56% since 2011 and 165% since 2009, while RAP usage grew almost 22% since 2009.
The survey reported 98% of producers used RAP in their mixes.
Also, for the first time, the survey took a look at the use of ground tyre rubber, steel and blast furnace slags and other recycled materials, though estimates were not calculated.