Proven polyester bridge deck surfacing technology is now being used more widely – Mike Woof writes. The benefits of using polymer concrete bridge deck overlays are well known and this technology is becoming widely used in the US. The system can improve protection for bridge surfaces and help extend the life of a bridge deck, as well as increasing skid resistance. In the last 25 years the use of these overlays has increased significantly in the US. These perform best when installed on bridge decks that are i
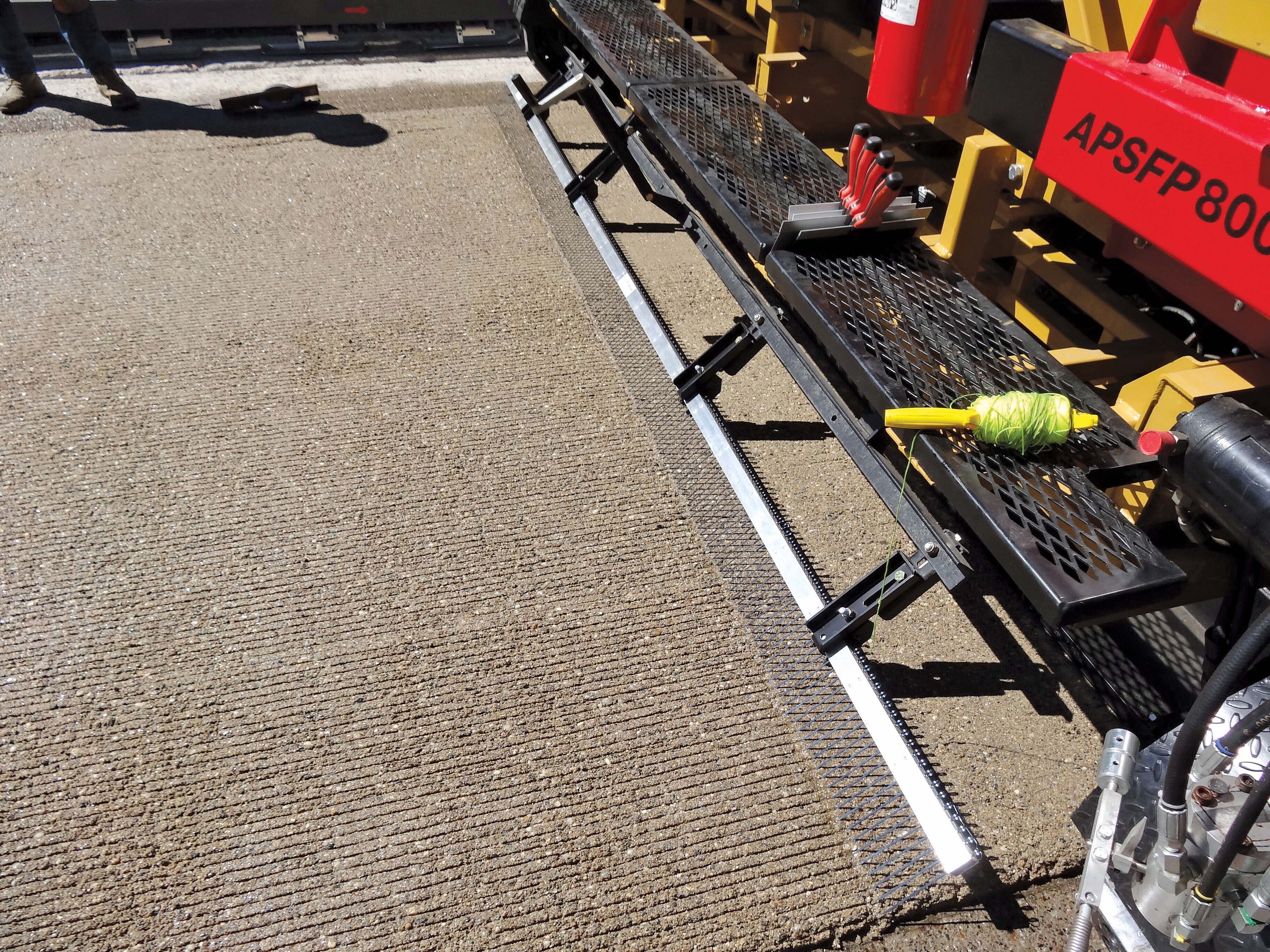
Using the equipment has allowed the contractor to lay a new skid-resistant road surface that will also be resilient and long lasting
Proven polyester bridge deck surfacing technology is now being used more widely – Mike Woof writes
The benefits of using polymer concrete bridge deck overlays are well known and this technology is becoming widely used in the US. The system can improve protection for bridge surfaces and help extend the life of a bridge deck, as well as increasing skid resistance. In the last 25 years the use of these overlays has increased significantly in the US. These perform best when installed on bridge decks that are in good condition, with a report by the National Cooperative Highway Research Program (NCHRP) having written an extensive report giving in-depth analysis of the benefits of the technology.
The technology is versatile as road authorities can use polymer concrete when carrying out new surfacing works as well as for repairing existing concrete surfaces. This is because the material has adhesive properties, allowing it to bond effectively to an existing surface and it can be used to repair previously installed polymer concrete layers as well as conventional cement type concrete. With polymer concrete technology, the polymers are used to either supplement or even replace the use of cement as a binder. Thermosetting resins are used, along with conventional high-quality, dry aggregate that does not contain dust.
In the past the use of polymer concrete has been limited on grounds of cost, as well as due to shortcomings with materials production. But improvements in production have reduced the cost levels opening the way for road authorities to make wider use of the technology.
The technology is also now being used widely in the US for highway overlays due to advantages that include shorter lane closures, increased live load capacities, higher tensile strength and a greater impact resistance. When applied properly the polymer concrete layers can deliver a service life of 20 to 25 years and even in applications where they are carrying heavy traffic loads. The polyester concrete overlay is versatile too as it can be laid in thicknesses from 19mm up to 311mm, in a single lift. Good preparation is important as the method works effectively when applied to a clean and dry surface that has been sufficiently textured.
Due to these benefits, many states are resurfacing their bridges as well as roads with polyester concrete overlays. In 2014, the authorities in the state of Colorado awarded contractor Truesdell Corporation a package of works that included joint repair and resurfacing of 20 bridges on a 14.5km stretch of I70 West through Glenwood Canyon. The contractor approached156 Allen Engineering to develop equipment able to carry out the work efficiently and the firm developed the Polyester Slip Form Paver as a result of the request. This compact slip form paver is capable of placing the polyester concrete in 19mm-152mm thick lifts and at 3.66m wide, as required by the contractor. The paver is equipped with automatic grade control that can be used with string-line or by using Allen’s 9.14m averaging skis. The Allen APSFP-800 Polyester Paver also features a standard dolly jack system that allows for easy loading and unloading in existing lane closures. The machine’s design is said to allow for good quality paving processes and the manufacturer claims that this makes for quicker lane openings once the job is finished.
Allen is not new to the polyester concrete overlay industry, and has been involved with polyester concrete since its genesis in the 1980s. The company has also developed a larger polyester concrete slip form paver that can handle lifts greater than 162mm thick lifts and 3.66m widths for which the more compact Model APSFP-800 is designed.
The technology does offer several advantages but does still have room for further development in some key areas. And according to the NCHRP, there are key issues to be addressed however. Further research should help develop new resins that can cope with extremes of low and high temperatures, as well as greater traffic volumes or heavier axle loads. New resin technology could also deliver materials featuring self-healing properties to prevent cracking or delamination from causing failures. There is a need for new testing technologies that can more accurately predict the life of polymer concrete surfaces when handling differing traffic volumes, vehicle loads or climactic conditions. Better analysis of application requirements could also deliver material properties and thicknesses that are more suited to specific duties.
The benefits of using polymer concrete bridge deck overlays are well known and this technology is becoming widely used in the US. The system can improve protection for bridge surfaces and help extend the life of a bridge deck, as well as increasing skid resistance. In the last 25 years the use of these overlays has increased significantly in the US. These perform best when installed on bridge decks that are in good condition, with a report by the National Cooperative Highway Research Program (NCHRP) having written an extensive report giving in-depth analysis of the benefits of the technology.
The technology is versatile as road authorities can use polymer concrete when carrying out new surfacing works as well as for repairing existing concrete surfaces. This is because the material has adhesive properties, allowing it to bond effectively to an existing surface and it can be used to repair previously installed polymer concrete layers as well as conventional cement type concrete. With polymer concrete technology, the polymers are used to either supplement or even replace the use of cement as a binder. Thermosetting resins are used, along with conventional high-quality, dry aggregate that does not contain dust.
In the past the use of polymer concrete has been limited on grounds of cost, as well as due to shortcomings with materials production. But improvements in production have reduced the cost levels opening the way for road authorities to make wider use of the technology.
The technology is also now being used widely in the US for highway overlays due to advantages that include shorter lane closures, increased live load capacities, higher tensile strength and a greater impact resistance. When applied properly the polymer concrete layers can deliver a service life of 20 to 25 years and even in applications where they are carrying heavy traffic loads. The polyester concrete overlay is versatile too as it can be laid in thicknesses from 19mm up to 311mm, in a single lift. Good preparation is important as the method works effectively when applied to a clean and dry surface that has been sufficiently textured.
Due to these benefits, many states are resurfacing their bridges as well as roads with polyester concrete overlays. In 2014, the authorities in the state of Colorado awarded contractor Truesdell Corporation a package of works that included joint repair and resurfacing of 20 bridges on a 14.5km stretch of I70 West through Glenwood Canyon. The contractor approached
Allen is not new to the polyester concrete overlay industry, and has been involved with polyester concrete since its genesis in the 1980s. The company has also developed a larger polyester concrete slip form paver that can handle lifts greater than 162mm thick lifts and 3.66m widths for which the more compact Model APSFP-800 is designed.
The technology does offer several advantages but does still have room for further development in some key areas. And according to the NCHRP, there are key issues to be addressed however. Further research should help develop new resins that can cope with extremes of low and high temperatures, as well as greater traffic volumes or heavier axle loads. New resin technology could also deliver materials featuring self-healing properties to prevent cracking or delamination from causing failures. There is a need for new testing technologies that can more accurately predict the life of polymer concrete surfaces when handling differing traffic volumes, vehicle loads or climactic conditions. Better analysis of application requirements could also deliver material properties and thicknesses that are more suited to specific duties.