Special bitumen mixes and machines are capable of improving the service life of roads and reducing noise. Mike Woof and Patrick Smith report. The need to improve traffic flow in an important part of the City of Poznan, Poland, led to the decision to build a new 1.13km long dual carriageway.
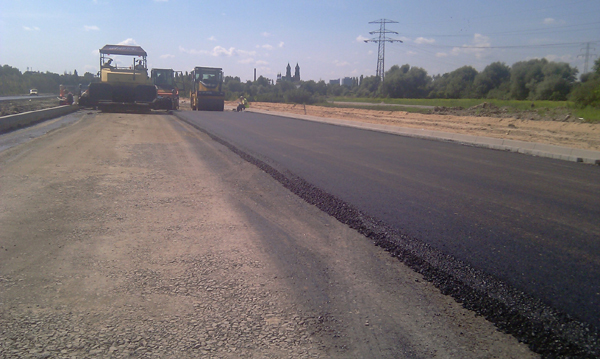
An asphalt pavement with a high modulus of rigidity was specified in Poznan using Nynas' Nypave FX25 Pl bitumen binder
RSS
The route, known as Nowe Zawady, connecting the Sródka Roundabout with the crossroads at Prymasa Hlonda and G?ówna Streets, has a contract value of PLN40 million US$14 million). The client was ZDM Poznan and Poldrog Pila was the main contractor, asphalt producer and surfacing contractor.
In view of the projected intense traffic flows, with a high proportion of heavy vehicles, an asphaltic concrete pavement characterised by a high modulus of rigidity (HMR, French class EME/enrobé a module élevé) was specified using Nypave FX25 PL bitumen binder.
This binder, from the294 Nynas Performance Programme's Extra range, is specially designed for mixtures of HMR, and is in accordance with European standard EN 12591 and Nynas' quality specifications.
The design of a pavement characterised by a HMR is intended to provide base and binder courses of asphaltic concrete with exceptional qualities of load bearing, longevity and resistance to deformation, and also of resistance to thermal and fatigue cracking.
For the Poznan link road, a number of mechanical requirements were specified for the pavement, including an integrated modulus of rigidity of at least 16,000MPa at 10°C; resistance to rutting of the base course, maximum 7.5%, and a resistance to rutting of the binder course, maximum 5%.
A mix of asphaltic concrete was designed based on 0-16mm crushed basalt stone aggregate plus Nypave 25XPL binder, to ensure that the high parameters of the specification were met.
The pavement comprises a binder course of 80mm above a 120mm thick base course.
With noise limitation in mind, a 30mm thin layer surface course of stone mastic asphalt (SMA) was applied, containing Nypol 86.
Compaction was carried out using two vibratory steel rollers of 10tonnes and 8tonnes respectively.
The chosen solution (to use a pavement of HMR) meant that the base and binder courses could be reduced from the traditional 250mm thickness to 200mm while maintaining high load bearing capability, durability and longevity, plus resistance to surface cracking.
252 Iterchimica is continuing with its developments in the field of bitumen technology and is working on some innovative projects at present.
The company has been playing a role in a project to build a new international airport in Oman, working with Greek and Turkish companies.
Alessandro Giannattasio, Iterchimica's deputy chairman, said: "We got the contract for a technology transfer of polymer-modified bitumen (PMB). For us it's one of the most important awards.
"Our technicians stay on site for a year and we supply the know-how for the PMB. We have the responsibility for checking the mix design and the quality but this contract is not the traditional deal with a sale of chemicals." The project will see the production of some 50,000tonnes of PMB material over a two-year period from the6805 Massenza plant, with Iterchmica's technicians continuously monitoring the output.
Meanwhile Iterchimica has also been working for the last three years on a new type of fibre for use in asphalt. This project has been run in partnership with Milan University and uses recycled materials in the fibres, which are designed to increase the mechanical performance of the asphalt mixture according to Giannattasio.
Another important development is the warm asphalt system the company is working on in partnership with the2779 Fayat Group. This includes a liquid additive that helps reduce the mix temperature by 40°C to 120°C (and in some cases, as low as 95°C), with a major benefit in terms of reducing fuel consumption during production and emissions from the plant.
Giannattasio said that the road authorities in Milan have now accepted the use of warm asphalt as this technology is well-suited to use in urban areas.
The warm asphalt approach can even allow effective paving and compaction operations in colder weather, extending the road repair cycle throughout the year.
The 700km A14, which connects Bologna in northern Italy with Bari in the south of the country, is being widened with the addition of a third lane and this will also feature the warm asphalt technology according to Giannattasio.
The surface was laid with the help of a1194 Vögele paver equipped with the company's sophisticated SprayJet system, and is one of several rehabilitation projects to reduce traffic noise in the city.
To reduce noise, the number of joints in the asphalt pavement has to be minimised, although as the flow of traffic has to be taken into account when resurfacing a road the paving job has to be carried out in several narrow strips.
Local contractor Franz Schelle was able to avoid this by taking advantage of an existing closure of a traffic lane on one road, and this allowed paving in just three strips along the full length of the 550m stretch. The disadvantage though was a cramped job site, separated from traffic by beacons.
First, the team removed the old wearing and binder courses to an average depth of 135mm using2395 Wirtgen milling machines, and a new binder course was laid.
For paving the new wearing course of low-noise SMA, a Vögele SUPER 1800-2 fitted with an AB500-2 screed and a SprayJet module was employed. This equipment operated with a maximum spray width of 6m and the screed was set-up with bolt-on extensions. In this configuration, the spray paver placed a wearing course, 25mm thick.
The contractor explained that in order to leave the noise-absorbing cavities in the wearing course, the mix cannot be compacted to the same degree as conventional asphalt: an effective solution to laying a durable wearing course with an optimum bond of layers is to use a spray paver.
The SUPER 1800-2 with its SprayJet module spreads bitumen emulsion and paves asphalt in a single pass, delivering a high quality surface compared with the conventional method of spraying emulsion and paving asphalt in two operations, according to the contractor.
Another reason for the efficiency of the Vögele SprayJet Technology is the cleanliness of the system, as the spray system is designed to maximise efficiency and minimise materials waste. The spray system operates at a low pressure of just 3bars to reduce the formation of mist and the device delivers the material in pulses that are controlled automatically. Because the emulsion is immediately overlaid with asphalt, it is not damaged by transport vehicles, feeders or pavers and ensures an effective bond.
Using the SprayJet system for pavement rehabilitation is also said to be economical, as the wearing course is thinner than for conventional roadworks, and this can deliver material savings of up to 50% while allowing for fast working and reduced road closure periods.
The SprayJet module can be fitted quickly to the SUPER 1800-2 when required and removed when it is not needed, boosting versatility and utilisation.RSS
Special bitumen mixes and machines are capable of improving the service life of roads and reducing noise. Mike Woof and Patrick Smith report
The need to improve traffic flow in an important part of the City of Poznan, Poland, led to the decision to build a new 1.13km long dual carriageway.The route, known as Nowe Zawady, connecting the Sródka Roundabout with the crossroads at Prymasa Hlonda and G?ówna Streets, has a contract value of PLN40 million US$14 million). The client was ZDM Poznan and Poldrog Pila was the main contractor, asphalt producer and surfacing contractor.
In view of the projected intense traffic flows, with a high proportion of heavy vehicles, an asphaltic concrete pavement characterised by a high modulus of rigidity (HMR, French class EME/enrobé a module élevé) was specified using Nypave FX25 PL bitumen binder.
This binder, from the
The design of a pavement characterised by a HMR is intended to provide base and binder courses of asphaltic concrete with exceptional qualities of load bearing, longevity and resistance to deformation, and also of resistance to thermal and fatigue cracking.
For the Poznan link road, a number of mechanical requirements were specified for the pavement, including an integrated modulus of rigidity of at least 16,000MPa at 10°C; resistance to rutting of the base course, maximum 7.5%, and a resistance to rutting of the binder course, maximum 5%.
A mix of asphaltic concrete was designed based on 0-16mm crushed basalt stone aggregate plus Nypave 25XPL binder, to ensure that the high parameters of the specification were met.
The pavement comprises a binder course of 80mm above a 120mm thick base course.
With noise limitation in mind, a 30mm thin layer surface course of stone mastic asphalt (SMA) was applied, containing Nypol 86.
Compaction was carried out using two vibratory steel rollers of 10tonnes and 8tonnes respectively.
The chosen solution (to use a pavement of HMR) meant that the base and binder courses could be reduced from the traditional 250mm thickness to 200mm while maintaining high load bearing capability, durability and longevity, plus resistance to surface cracking.
Advanced options
Meanwhile, Italian specialistThe company has been playing a role in a project to build a new international airport in Oman, working with Greek and Turkish companies.
Alessandro Giannattasio, Iterchimica's deputy chairman, said: "We got the contract for a technology transfer of polymer-modified bitumen (PMB). For us it's one of the most important awards.
"Our technicians stay on site for a year and we supply the know-how for the PMB. We have the responsibility for checking the mix design and the quality but this contract is not the traditional deal with a sale of chemicals." The project will see the production of some 50,000tonnes of PMB material over a two-year period from the
Meanwhile Iterchimica has also been working for the last three years on a new type of fibre for use in asphalt. This project has been run in partnership with Milan University and uses recycled materials in the fibres, which are designed to increase the mechanical performance of the asphalt mixture according to Giannattasio.
Another important development is the warm asphalt system the company is working on in partnership with the
Giannattasio said that the road authorities in Milan have now accepted the use of warm asphalt as this technology is well-suited to use in urban areas.
The warm asphalt approach can even allow effective paving and compaction operations in colder weather, extending the road repair cycle throughout the year.
The 700km A14, which connects Bologna in northern Italy with Bari in the south of the country, is being widened with the addition of a third lane and this will also feature the warm asphalt technology according to Giannattasio.
Clean course
Munich's popular Haidhausen district, which carries heavy traffic volumes on its main thoroughfares, is benefiting from a new road surface. The low-noise, stone mastic asphalt (SMA) wearing course will reduce traffic noise for residents, an important factor in the choice of this high quality surface by the local authorities.The surface was laid with the help of a
To reduce noise, the number of joints in the asphalt pavement has to be minimised, although as the flow of traffic has to be taken into account when resurfacing a road the paving job has to be carried out in several narrow strips.
Local contractor Franz Schelle was able to avoid this by taking advantage of an existing closure of a traffic lane on one road, and this allowed paving in just three strips along the full length of the 550m stretch. The disadvantage though was a cramped job site, separated from traffic by beacons.
First, the team removed the old wearing and binder courses to an average depth of 135mm using
For paving the new wearing course of low-noise SMA, a Vögele SUPER 1800-2 fitted with an AB500-2 screed and a SprayJet module was employed. This equipment operated with a maximum spray width of 6m and the screed was set-up with bolt-on extensions. In this configuration, the spray paver placed a wearing course, 25mm thick.
The contractor explained that in order to leave the noise-absorbing cavities in the wearing course, the mix cannot be compacted to the same degree as conventional asphalt: an effective solution to laying a durable wearing course with an optimum bond of layers is to use a spray paver.
The SUPER 1800-2 with its SprayJet module spreads bitumen emulsion and paves asphalt in a single pass, delivering a high quality surface compared with the conventional method of spraying emulsion and paving asphalt in two operations, according to the contractor.
Another reason for the efficiency of the Vögele SprayJet Technology is the cleanliness of the system, as the spray system is designed to maximise efficiency and minimise materials waste. The spray system operates at a low pressure of just 3bars to reduce the formation of mist and the device delivers the material in pulses that are controlled automatically. Because the emulsion is immediately overlaid with asphalt, it is not damaged by transport vehicles, feeders or pavers and ensures an effective bond.
Using the SprayJet system for pavement rehabilitation is also said to be economical, as the wearing course is thinner than for conventional roadworks, and this can deliver material savings of up to 50% while allowing for fast working and reduced road closure periods.
The SprayJet module can be fitted quickly to the SUPER 1800-2 when required and removed when it is not needed, boosting versatility and utilisation.RSS