Mixtures with special additives are being produced for roads, offering noise reduction and aiding recycling. Patrick Smith reports. Noise-reducing road surfacings have been used in motorway construction for some time. But relatively new are noise-optimised surfacings used on roads in towns that do not follow a standard concept.Road trials with these materials have taken place in Germany since 2007 and have been prioritised due to the European Union Guidelines on the Assessment and Management of Environmenta
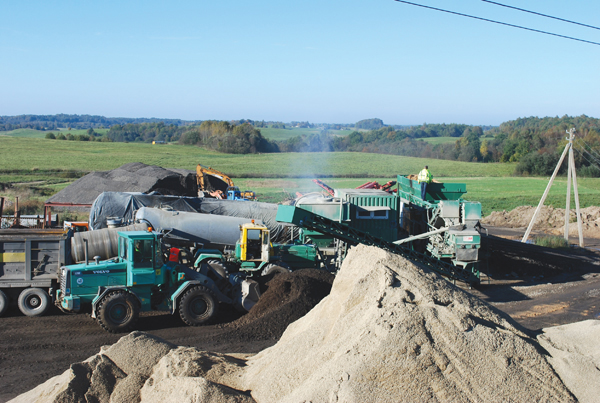
Zemaitijos Keliai's cold mix plant, which was set up a short distance from the site
Mixtures with special additives are being produced for roads, offering noise reduction and aiding recycling. Patrick Smith reports
Noise-reducing road surfacings have been used in motorway construction for some time. But relatively new are noise-optimised surfacings used on roads in towns that do not follow a standard concept.Road trials with these materials have taken place in Germany since 2007 and have been prioritised due to the
Since then, noise maps for all regions have been produced and new construction measures have been put into practice.
Momentum was gained at local level in Germany in 2009 due to financial assistance provided to local government by the federal state as part second-phase measures designed to boost the economy.
The relevant Act stipulates that financial assistance will only be provided for measures related to noise protection. In such cases the noise reduction must be improved and also demonstrated.
One of the measures financed through the Act is the renovation of the wearing and binder course layers of Stockumer Straße in the city of Dortmund, Germany.
The surface is based on the asphalt concept designed by the Department of Road Construction at Bochum University, which aims to achieve noise reduction using a dense wearing course with a concave surface texture. This special surface texture allows air trapped between the tyres and the road surface to escape freely without the usual associated noise. This effect is the major source of noise at speeds over 40km/hour.
The noise-optimised surface layer (LOA 5 D), with a maximum nominal stone size of 6mm, is applied in a thin layer between 2-2.5cm, and this usually requires that the asphalt binder course also has to be relaid. To ensure long lasting performance of Stockumer Straße, a very stable 8cm thick binder course with maximum stone size of 16mm was constructed incorporating polymer modified bitumen (PMB), all in line with the Bochum University asphalt concept (%$Linker:
The target noise reduction of the LOA 5 D is up to 4dB (A) for inner-city traffic (travelling at around 50km/hour). It was laid on Stockumer Straße in a residential area, a road that provides the main access to a hospital, as well as being an important alternative route to the east-west A40/B1 motorway, one of the largest arterial roads in Germany. The section had an overall length of 250m and was approximately 10m wide, with two uphill traffic lanes and one downhill lane.
Due to the high traffic volume, paving operations were only allowed during weekends. The local authority approved a plan to close off the road in one direction at a time, with traffic being diverted onto neighbouring main roads. This way construction work took place over two consecutive weekends.
The new pavement level had to remain at the same height as the old pavement, so the existing asphalt surface and binder course layers were milled off to prepare for the new surfacing.
After the new heavy duty binder course (8cm AC 16BS) was paved, it was sprayed with C 60BP1-S before the new LOA 5 D surface was laid. An Olexobit NV 45 binder from
The mix was delivered at a temperature of approximately 180°C (measured at the hopper) in normal articulated trucks, and emptying the tipper was not a problem, with no run-off of the Olexobit NV 45 binder being observed. The paver applied the LOA 5 D thinly and at a speed of 3-4m/min, with the vibration of the compaction screed set low. Further roller compaction was carried out using two 10tonne tandem rollers working one behind the other. As LOA 5 D can only be compacted statically (no vibration), the final compaction was only achieved after 10-15 roller passes. Grit spreaders were not used as LOA cannot (under any circumstances) be gritted. However, as the surface texture is markedly rougher in comparison with traditional AB 0/5 surfacing, the initial friction resistance is sufficient without gritting.
As a result of the low paver speed and the low screed vibration the longitudinal surface was particularly even and homogeneous, and as intended with the Bochum concept, a rough macro-texture was achieved for the surfacing layer providing an audible reduction in noise.
Olexobit NV 45 is a further development of Olexobit 45, which has already proven itself over many years. The positive features of polymer modification have remained unaltered and the additives also improve the stability of the asphalt mixture against deformation during service life.
Lithuanian Cold Mix
In Lithuania, cold mix asphalt containing recycled asphalt pavement has been installed in a new base course overlay for a section of the A1, the country's most heavily trafficked motorway.
The A1 is Lithuania's main cross-country route, linking the capital Vilnius in the east, westwards to Kaunas and then Klaipeda by the Baltic Sea. Maximum traffic density along the 300km long, dual four-lane highway is 40,000 vehicles/day.
It is towards Klaipeda that a 3.4km stretch of the motorway's eastbound carriageway was giving particular trouble. Built in the mid-1980s this portion of road had an experimental 200mm thick base course of fly ash stabilised gravel, mixed to meet the then prevailing Soviet standards. But 25 years on, the bitumen bound layers above the base course displayed extensive reflected cracking.
"Over time, the base course has developed considerable strength, becoming a semi-rigid pavement rather than the flexible one it was supposed to be," says deputy director of the Lithuanian Road Administration (LRA) Petras Tekorius.
Weather-induced movement caused the rigid material to crack, with a detrimental effect on the asphalt above.
"We had two problems in reinstating the carriageway: what to do with the base course, and how to rebuild the pavement in the best way." The original base course had considerable residual bearing capacity, despite the cracks. "So we decided to leave the original base course in situ, but to cap it first with a 120mm thick unbound layer of crushed stone to form an anti-cracking and levelling medium, and then a new 200mm base course of cold recycled asphalt," says Tekorius.
This would introduce to the carriageway sufficient elasticity, according to LRA's head of Roads Division Zigmantas Perveneckas. As to the choice of recycled cold mix asphalt, this seemed the natural thing to do.
"We are doing our utmost to implement sustainable technologies in the roads industry," he says.
The LRA has used cold mix recycling on a number of road projects since the early 2000s, prompted by European bitumen specialist Nynas. Although the roads involved were of a lesser nature than the A1, their successful refurbishment has bred sufficient confidence for a more substantial challenge to be undertaken. Certainly, the A1 is the big one, in terms of cold recycling.
Roads civil engineering contractor responsible for the A1 recycling is
"Our investment is paying off: we have had to build the market for cold mix recycled asphalt but now the contracts are coming through," says the company's deputy director Alvydas Peldzius, who pays tribute to the assistance given by Nynas in providing technological guidance and training.
The A1 section under repair first had its three existing asphalt layers milled off and the planings graded and stockpiled at a temporary mixing plant set up 2km from the site. Crushed stone was placed on the original base course, to form the stress absorbing layer. Then production of the cold mix for the new base course began, using the reclaimed asphalt; an amount of virgin aggregate to make up the required volume; fillers and the Nymuls RX bitumen emulsion, to create the base course.
After this material had been placed, in two layers each of 100mm, amounting to 30,000tonnes, an 80mm thick hot asphalt concrete binder course was added, followed by a 40mm stone mastic asphalt surface course.
The direct cost saving of the recycled solution over conventional construction was around 20%, much more when sustainability and environmental benefits are added.