Special additives are used in asphalt mixes to give them added benefits as Patrick Smith reports
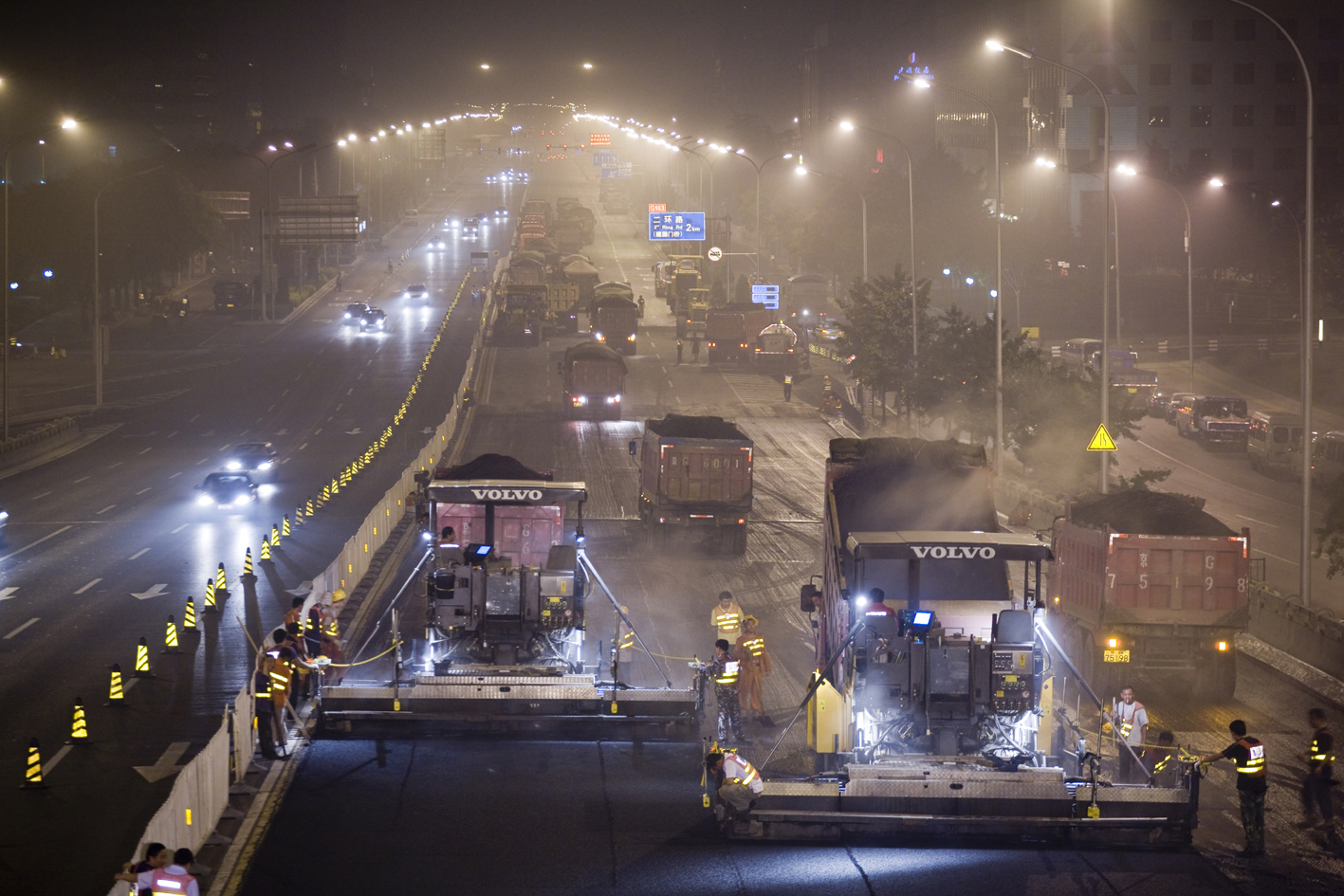
Volvo equipment was used to help give a makeover to Beijing's Chang'an Avenue where SBS-modified asphalt and PR asphalt was used for the lower layer
Special additives are used in asphalt mixes to give them added benefits as Patrick Smith reports
It is estimated that over 80% of world's consumption of bitumen (around 110 million tonnes) has been used for paving applications, and the construction and maintenance of roads.
According to
The company says that modern road design and construction techniques are aimed at building flexible road layers or courses so that the tensile and compressive stresses imposed by passing traffic are distributed evenly through these layers according to their relative strengths. Therefore, neither the ground supporting the road nor the individual layers are permanently deformed by these concentrated stresses.
"The courses must also be made weather resistant and durable, and bitumen plays a major part in meeting this requirement because it strongly binds the aggregate particles and seals and fills in the voids between them. Its effectiveness depends on the aggregate specification, the size and number of voids and the type of bitumen. By sealing the gaps, bitumen makes it difficult for water to penetrate the road courses and damage the natural foundation of the road," says BP Bitumen.
When the condition of a 3km stretch of the A404 main road near Maidenhead in County Berkshire, southern England, became a serious problem, resurfacing the carriageway with traditional materials was not the only route forward.
EnterpriseMouchel, managing agents for Area 3 on behalf of the
To give the road a new lease of life between Junctions 8 and 9 of the M4 motorway and the A4, Tarmac's technical team was tasked with providing a quick, effective and durable solution to repair the road. Around 6,600tonnes of Masterlayer, a strong, flexible binder course, and Masterflex, a thin surface course, was laid by Tarmac National Contracting.
Working in close partnership with EnterpiseMouchel, a combination of Tarmac products provided enhanced durability. Tim Smith, technical manager at Tarmac National Contracting, explains: "Lane one on both the northbound and southbound carriageways had deteriorated most and there was also a serious problem with reflective cracking here.
"The lean concrete underneath the asphalt layers had broken down and cracks were appearing from the bottom upwards. This was exacerbated by water permeating the cracks in the carriageway, enlarging them further. Lane two on both carriageways was also not immune to deterioration and transverse cracks were apparent.
"The Highways Agency was concerned that the carriageway was deteriorating quickly and so time was a key issue. Our technical team analysed data provided by EnterpriseMouchel, which had been compiled following investigations on the condition. We also carried out an extensive assessment of its current condition to gain a better understanding of what we were facing.
"We discussed the options with EnterpriseMouchel and after working closely together we came up with an effective solution. As a full depth reconstruction was not possible due to time and budgetary constraints, we recommended replacing the asphalt layers with polymer modified materials, which have enhanced crack resisting properties." "To deal with deformation of the A404, the resurfacing asphalt needed to utilise strong and flexible asphalt materials, which would provide enhanced resistance.
"We suggested our Masterlayer binder course, which has high structural strength and can also deal effectively with reflective cracking problems. Its low void content reduces the potential of water ingress to the pavement structure and enhances durability. Its performance is also superior to using standard materials," said Smith.
"As the A404 is a fast road, an asphalt surface course was needed to deliver low noise levels. Tarmac Masterflex, a thin asphalt resurfacing course, was the ideal product for the job as it is a polymer modified material which delivers excellent noise reduction." The polymer modified binder was added to the bitumen in the mix.
Miles Williamson, bitumen sales manager at
"Because the polymer binder is highly flexible, there is also less likelihood of reflective cracking appearing in the surface course. Thin surfacing materials cool quickly, leaving less time for effective compaction and so the polymer binder reduces its viscosity and improves its resistance to cracking at very low temperatures." Two quarries produced the binder and surface courses for the works. Works on lane one of the northbound carriageway required 2,900tonnes of binder course from both quarries. When Tarmac National Road Planing had completed the removal of 140mm of existing material, the National Contracting surfacing team was on standby for deliveries of Masterlayer binder. A further delivery of 1,150tonnes of surface course material was laid. Resurfacing on the southbound carriageway required 2,600tonnes of materials.
Meanwhile, thousands of kilometres away in China, the country's most famous street, Beijing's Chang'an, had a complete makeover using two special asphalt materials for the lower layer, SBS (styrene butadiene styrene)-modified asphalt and PR asphalt, to provide a solid foundation, while stone mastic asphalt was used for the top layer.
A variety of Volvo Construction Equipment machines played an integral part in the 4 billion RMB (US$585 million) road project, having been selected almost exclusively to provide the road machinery to complete the work.
A 26km stretch of the 40m wide, 40.4km long Chang'an Avenue was closed for repaving every night between 11pm and 6am for six months.
Crowned 'the first avenue in China', Chang'an is one of the world's longest and widest streets, and is flanked by two of China's most famous landmarks, The Forbidden City and the vast Tiananmen Square.
After milling machines were used to prepare the surface of the existing worn road, compaction work was performed during the last two hours. Often, three pavers would work simultaneously to resurface one side of the road in order to make the most of the time. Two new 40mm layers of asphalt were laid over the original surface to make it durable.
In Australia,
Over the years this ongoing collaboration has led to the use of high performance bitumen products such as the Shell Cariphalte range of modified binders.
These bitumen products have been specifically developed for situations where demand on the road pavement exceeds the performance offered by standard grade bitumens.
They are manufactured by blending high performing polymers with carefully chosen base bitumen to help create longer life pavements. The different rheological characteristics of Shell Cariphalte asphalt binders facilitate their use in open graded asphalt, where thicker binder films are required on the aggregate skeleton.
In Victoria, the city of Mildura was experiencing some of the hottest weather possible with the temperature reaching 49?C. Such high temperatures are not uncommon in north-west Victoria, and with corresponding road surface temperatures well in excess of 60?C, spray sealed roads are really put to the test.
The city council operates its own spray sealing crew for its roadwork programme, and also tenders on re-sealing contracts in surrounding areas. In the past few years the team at Mildura has embraced new PMB binder technology to address its summer road-bleeding problems.
Having had great success with Shell Cariphalte S35E it now uses it a lot of its reseal projects.
The polymers in the Shell Cariphalte S35E binder work to reduce temperature susceptibility by increasing the bitumen viscosity at high temperatures and improve elastic recovery under high stress loads. This binder is ideal for roads with existing repairs and light cracking, and where bitumen bleeding due to environmental temperatures is a problem.