When the main commuter route into Cardiff, the Welsh capital, began to suffer from acute deformation, the Vale of Glamorgan Council required a durable and faster alternative to hot rolled asphalt to ensure minimum disruption for local road users.
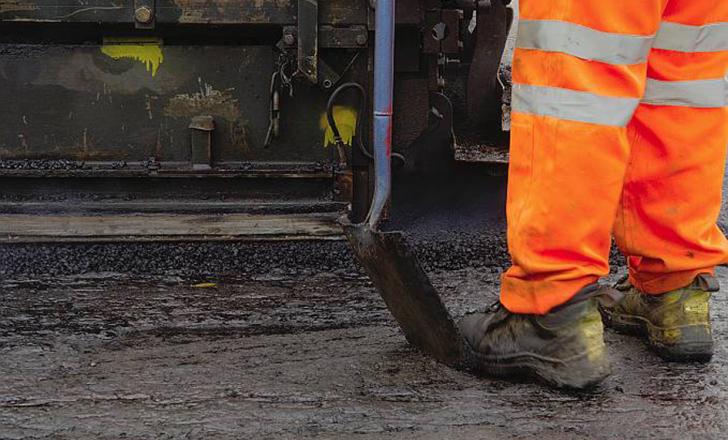
The Masterlayer surface is trafficable within an hour
RSSWhen the main commuter route into Cardiff, the Welsh capital, began to suffer from acute deformation, the Vale of Glamorgan Council required a durable and faster alternative to hot rolled asphalt to ensure minimum disruption for local road users.
Ken Evans, the council's senior highway maintenance officer, said: "The initial plan to resurface the 1km stretch of road with traditional HRA would have required full closure. This would have caused significant disruption for residents and businesses resulting in a 12.8km diversion for workers requiring access to a nearby chemical plant.
"Water running under the surface to the sub-base of the road was washing away fine pieces of aggregate, compromising the integrity of the existing hot rolled asphalt where it had begun to crumble under heavy use and crack when frozen."
The council, which has an annual resurfacing contract with2399 Tarmac National Contracting, worked in partnership with Tarmac to find a solution.
Tarmac recommended its Masterlayer as an alternative to HRA, which would allow the road to remain fully open at peak times, and would also address the problem of water erosion as its composition is said to be much harder and more durable than HRA, increasing the structural stability of the road.
Designed by Tarmac's technical team, Masterlayer is an innovative binder and surfacing material that uses a high performance, heavy duty, polymer modified bitumen (PMB) supplied by Nynas Bitumen that has been used extensively on very heavily trafficked sites with high loads. It is formulated using a combination of specialist additive technology together with high quality rheologically-enhanced bitumen that is designed to increase the asphalt's elastic and cohesive performance.
The new 45mm thick Masterlayer was laid on a planed surface using a 10mm hardwearing polymer modified surface course to provide a closed finish. The design incorporated variations in the depth of the construction of the road, particularly to address minor reflective cracking near the chemical plant.
The new Masterlayer surface, trafficable within an hour, was laid in one application and reduced the project construction time by half and costs by around 30%.
Ken Evans, the council's senior highway maintenance officer, said: "The initial plan to resurface the 1km stretch of road with traditional HRA would have required full closure. This would have caused significant disruption for residents and businesses resulting in a 12.8km diversion for workers requiring access to a nearby chemical plant.
"Water running under the surface to the sub-base of the road was washing away fine pieces of aggregate, compromising the integrity of the existing hot rolled asphalt where it had begun to crumble under heavy use and crack when frozen."
The council, which has an annual resurfacing contract with
Tarmac recommended its Masterlayer as an alternative to HRA, which would allow the road to remain fully open at peak times, and would also address the problem of water erosion as its composition is said to be much harder and more durable than HRA, increasing the structural stability of the road.
Designed by Tarmac's technical team, Masterlayer is an innovative binder and surfacing material that uses a high performance, heavy duty, polymer modified bitumen (PMB) supplied by Nynas Bitumen that has been used extensively on very heavily trafficked sites with high loads. It is formulated using a combination of specialist additive technology together with high quality rheologically-enhanced bitumen that is designed to increase the asphalt's elastic and cohesive performance.
The new 45mm thick Masterlayer was laid on a planed surface using a 10mm hardwearing polymer modified surface course to provide a closed finish. The design incorporated variations in the depth of the construction of the road, particularly to address minor reflective cracking near the chemical plant.
The new Masterlayer surface, trafficable within an hour, was laid in one application and reduced the project construction time by half and costs by around 30%.