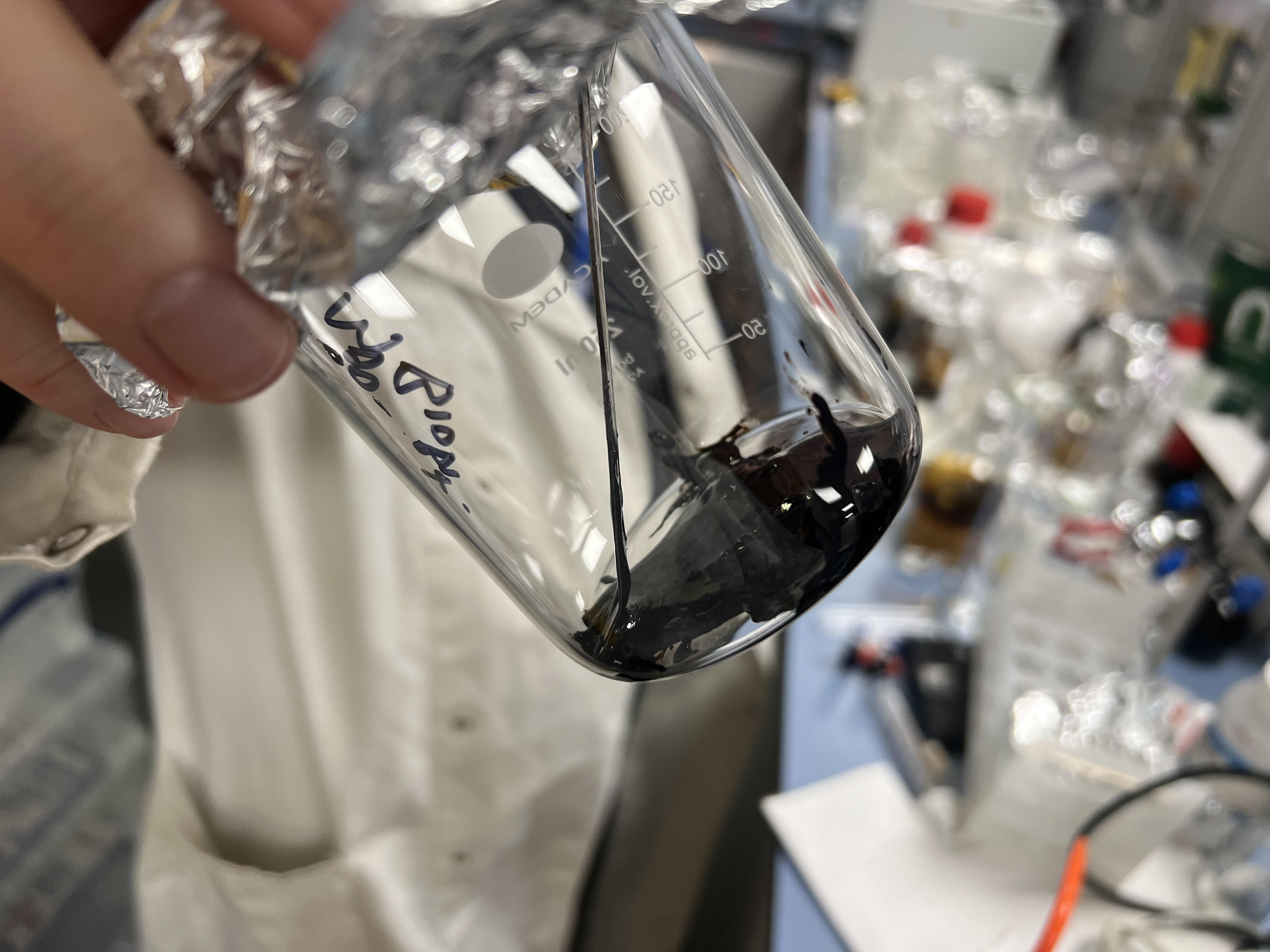
Customers are increasingly demanding it. Meanwhile, asphalt producers are hard at work sourcing it. Bitumen and bitumen additives that help lower a carbon footprint when paving a road is a high priority for many national and local road authorities around the world. Product trials are underway and in the case of bio-bitumen, UK researchers are keen to prove that algae has a future in the sector.
Aggregate Industries has launched Foamix Eco, a cold mix asphalt which can combine cold mix technology, a polymer modified bitumen (PMB) containing biogenic components, aggregate made from waste and recycled asphalt planings (RAP).
According to Aggregate Industries, this can lead to net zero or even negative carbon emissions, without offsetting, across stages A1 to A5 of the construction life cycle - up to when the road has been laid. The technology builds on Aggregate Industries’ existing Foamix technology. The binder is Nynas’ Nyfoam RE, which contains biogenic material – from plants. This gives it the same carbon footprint as an unmodified bitumen binder, but with the additional performance benefits of a PMB.
The aggregates come from OCO Technology, which uses its Accelerated Carbon Technology to treat byproducts coming predominantly from energy from waste plants with carbon dioxide gas. OCO Technology won a UK's King’s Award for Enterprise in May 2024 in recognition of its carbon capture technology which creates carbon-negative manufactured limestone aggregate.
Aggregate Industries completed a trial of Foamix Eco earlier this year when it was laid on a slip road to the M65 motorway in Lancashire, England. The trial involved the use of OCO Technology’s carbon-negative aggregate, RAP and recycled filler which Aggregate Industries says delivered net zero carbon emissions for stages A1 to A3 without carbon offsetting. The mix had over 90% recycled content.
Foamix is already a lower carbon solution since it allows the use of RAP. Using both RAP and the carbon-negative aggregate could lead to negative carbon emissions.
Foamix Eco for the Lancashire trial was produced using Aggregate Industries’ mobile mixing plant, Sitebatch Technologies. This can be situated on or near a site, using planings from the road being surfaced or from RAP stockpiles. According to Aggregate Industries, Foamix Eco can be laid in a single lift up to 150mm thick using conventional surfacing equipment. Extensive pre- and post-testing ensures that compaction can be achieved with traditional plant and equipment.
Cold mix asphalt is generally made from three components: aggregate, an emulsion of bitumen binder and water and additives such as polymers and rejuvenators. Some of the factors required for achieving good performance include tight control of material properties and conditions – such as water content – and adequate compaction, as it can be more difficult to achieve the desired amounts of compaction when compared to a standard hot mix asphalt.
Another consideration is that cold mix asphalt can take longer to set than hot mix asphalt. However, Aggregate Industries says that after compaction Foamixc Eco can be trafficked in the same way as hot asphalt.
Sripath’s new warm mix
Sripath Technologies has expanded its range of environmentally conscious asphalt additives with the addition of warm mix technology KoolTEQ. Launched in Australia early this year, KoolTEQ has been designed to give excellent performance at lower compaction temperatures.
According to Sripath’s chief marketing and business development officer Deepak Madan, the development of KoolTEQ, which began in the fourth quarter of 2022, came in response to demand from its Australian customers who were already using the company’s existing additives, such as its bio-based ReLIXIR rejuvenator and rut-resisting PGXpand polymer.
“When we develop our products, we aim to make sure we have something that's more environmentally friendly than competing products and gives the right performance. But it has to deliver cost savings or at least neutral costs,” says Madan. “In Australia and in Europe customers are very conscious about the carbon footprint but, at the same time, nobody wants to pay more.”
The Australian city of Brisbane recently agreed to conduct a trial using KoolTEQ after it was evaluated at RMTI (Royal Melbourne Technical Institute) and by Brisbane itself. “They started with half a dozen products and then narrowed it down,” says Madan.
Tests by RMTI involving an M1000 multigrade binder with 0.25% KoolTEQ compacted at 130°C showed that it achieved a comparable compaction to a control mix, without the additive, compacted at 155°C. And tests on a polymer modified bitumen (PMB) A15E with 0.25% KoolTEQ showed superior compactability at both 155°C and 115°C, compared to a control mix.
Sripath is also preparing for UK trials of its PGXpand polymer, designer to improve the rutting resistance of roads. A contractor working on night-time repairs on one of the UK’s most heavily trafficked motorways has been conducting laboratory tests and plans to trial it in the coming months, says Ranjeet Sandhu, head of sales for Europe at Sripath Innovations, the UK affiliate of Sripath Technologies.
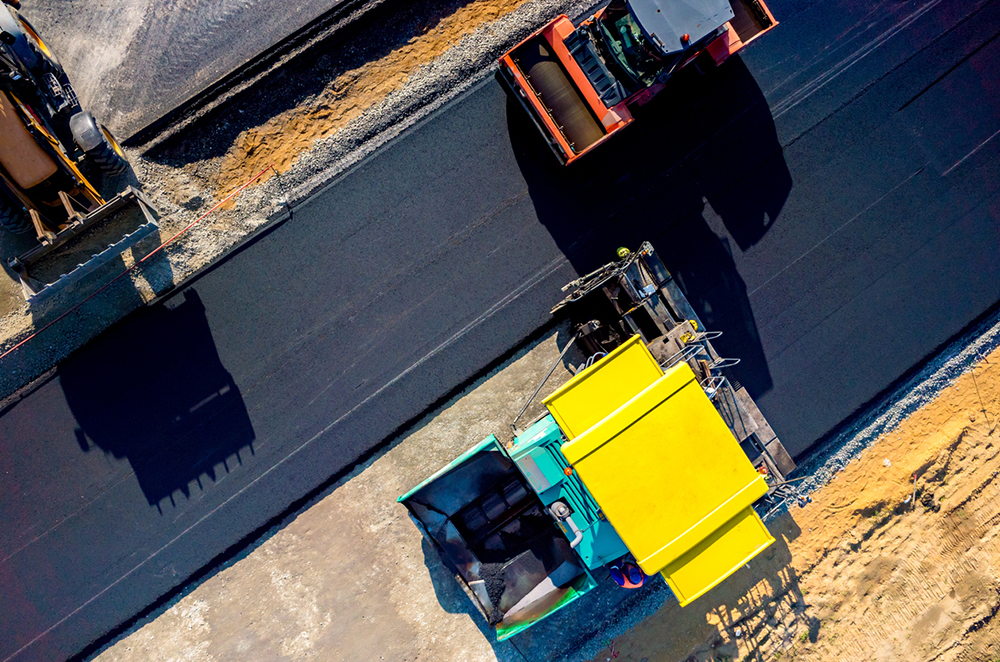
PGXpand also has practical benefits when compared to traditional polymers. “Its storage stability is very good and mixing it is substantially easier. You don't need a shear mixer,” he says. “For instance, we are talking to one customer who does not have the mixing capability to produce PMB. If he were to put the PGXpand into the bitumen tanker and drive to site one hour away, then that would help to mix it. This is a significant plus.”
PGXpand can be used to create a PMB or used to substitute some of the SBS (styrene-butadiene-styrene) polymer in a PMB to give improved rutting resistance and a lower carbon footprint. “Its carbon footprint is significantly lower than that of an SBS molecule,” says Madan. “In addition, you need to use less compared to a traditional polymer which further reduces the contribution to carbon dioxide generation.”
All Sripath’s additives have environmental product declarations (EPDs) which have been audited. “Transportation agencies are looking at EPDs and sustainability reports because they are looking for ways to meet their carbon reduction goals,” says Madan. “Europe, UK, Australia and more areas of the US have started to focus on EPDs and sustainability goals. Countries like India are further behind, but they will get there.”
PGXpand has been used in the US for around a decade and more recently has been introduced into Australia. Following on from the UK, Sripath will be introducing it into other European countries whenm it attains REACH - registration, evaluation, authorisation and restriction of chemicals - accreditation for the EU.
Colouring cold mix
Sika company Colorbiotics has introduced a colourant solution for its cold mix asphalt Easy Pave, which it says it is a first-of-a-kind product. Rather than the colour being applied to the top of the asphalt, the pigment comes in liquid form. This means that the colour runs all the way through the pavement to retain the same intensity, even if the surface of the path or drive wears away.
Easy Pave is a cold mix asphalt, combining 100% RAP with Colorbiotic’s Invigorate Plus rejuvenator, designed for use on low-volume roads, pedestrian and bike lanes, car parks and drives. The Colorbiotics pigment solution is added to the pugmill during the mixing process. Currently available in 11 colours but the company plans to offer custom colours in the future. “We’re addressing a need in the marketplace and we’re adding value,” says Ryan Lynch, national sales manager at Colorbiotics. “It’s easy to put down and it’s environmentally friendly because it’s all RAP. It uses bio-based ingredients and it looks great.”
The new Colorbiotics solution for Easy Pave is currently offered in the US and Canada but could be launched in other regions if there is demand, according to a spokesperson.
Algae to the rescue
Bio-bitumens are often produced from plants such as pine or soybean oil. But could bio-bitumen be produced from algae? A research partnership of Tarmac, CO2CO and Nanolyse Technologies and which includes the UK's Imperial College and the University of Sheffield, aims to find out.
CO2CO, a start-up company founded by academics from Imperial College, has developed a way to grow algae which sequesters carbon as it grows. Researchers are developing a method that transforms algae biomass into a black, viscous, water-repellent material which resembles bitumen.
Tim Smith, Tarmac's regional technical manager for South East England, says it provides the same properties but offers significant carbon savings when compared to petroleum-derived bitumen. "However, to maximise the environmental benefits, we also need to complete thorough testing and development to ensure these new bio-bitumens are as durable and recyclable as possible and do not affect the performance of the finished asphalt material.”
However, research is at an early stage, explains Imad Ahmed, chief executive of Nanolyse Technologies, a clean tech innovations company. But if successful, there could be many other applications for the algae-based material. “We’ve only scratched the surface with the potential applications of our bio-bitumen material. Our ability to fine-tune this material's chemical structure and viscoelastic properties provides sustainable solutions for various industrial applications, including construction, waste management, catalysis and agriculture.”