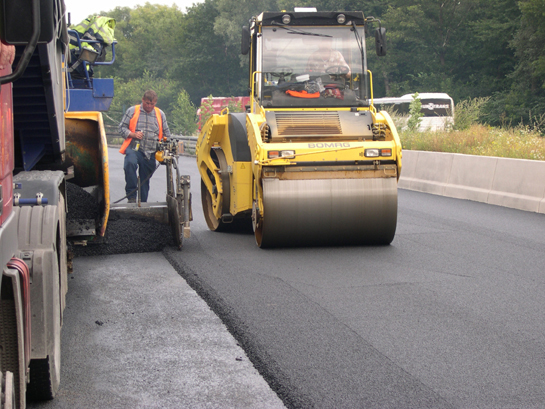
A construction project on the A40 Essen and Mühlheim motorway using porous asphalt where the BP binder Olexobit SMA was used.
Bitumen may be something which is taken for granted driving along the highway. But it is an increasingly sophisticated product, and technical know-how stands right behind it.
As overall traffic volumes increase, the contribution from commercial vehicles with increased axle loads is growing, putting ever more strain on roads and highway maintenance budgets.Highway authorities are looking for products that will be able to cope better and are more cost effective over the life of a road. Technical innovation is the only way to answer this challenge effectively, says
The company says its bitumen specialists are well placed to tackle innovation following the recent opening of its new technology centre in Gelsenkirchen, Germany, which takes advantage of being close to some of the largest, most developed, and technically advanced bitumen markets in the world.
Increasingly, the properties of bitumen are being enhanced by blending it with polymer additives. In some markets up to 25% of asphalt roads are already built with asphalt mixtures using polymer modified bitumen (PMB) and this market is growing due to the improved performance that PMBs deliver: lower emissions, time savings, noise reduction and spray reduction are just some of the benefits. PMBs give road designers the option of applying special porous asphalt materials or using thinner layers of asphalt.
For example, the recent renewal of 1.6km of the motorway from Munich to Nuremberg in Germany used BP's Olexobit NV 25 polymer modified product. Olexobit NV is a range of polymer modified road binders with low viscosity and environmentally friendly aspects, including mix production at lower temperatures (over 20°C lower than normal), not only saving on energy but also improving the working environment by reducing fumes and emissions during mixing and laying. Although the mixture is produced at lower temperature, workability is not compromised and asphalt stability is improved. Furthermore, lower application temperatures allow the new surfacing to be ready for traffic sooner, minimising disruption to traffic.
A more porous surface provides the dual benefits of reduced traffic noise and improved drainage. One recent BP Bitumen project focused on a busy motorway between Essen and Mühlheim in Germany, where heavy traffic rumbles past housing just 14m away making noise reduction to a priority. The BP binder Olexobit SMA has the right mechanical characteristics to achieve a durable porous surface with a void content around 24% per volume, leading to substantial noise reduction. In addition, improved drainage from the surface (water can run inside the porous surface layer without any problems) results in less splash and spray, giving better driver visibility when it is raining and hence safer driving conditions.
Olexobit SMA is characterised by good adhesion to the aggregate as well as having well balanced viscoelastic behaviour.
The ability to opt for thinner asphalt layers with high performance PMBs can deliver material savings and corresponding cost benefit during construction, as well as reducing maintenance costs over the life of the road.
"The initial cost per kilogram may be higher but the costs per unit area or the cost over the lifetime of the pavement can be lower," says Carl Robertus, global technology manager for BP Bitumen.
"We are committed to understanding and quantifying factors that influence product quality and performance of bitumen and end use applications, such as road surfacings."
To improve understanding, extensive rheological characterisation of bitumen and extensive mechanical testing of the asphalt mixture, are undertaken
"It's our task to provide the right binder tailored to the local requirements," Robertus notes.
An enormous benefit of asphalt materials is that they are 100% recyclable, and a PMB product that supports this is BP's Olexobit RC, which is specifically designed to be used in combination with recycled asphalt materials. (Based on an article in BP Frontiers magazine).
High polymer content
Meanwhile,It has the capability to reduce aggregate loss (ravelling), which often results in increased road noise and damage to cars caused by debris.
Contractors and binder producers will now have the opportunity to elevate polymer concentrations to enhance performance
without sacrificing workability and compatibility features, says Kraton Polymers, whose new polymer is "ideally suited for high performance asphalt road applications."
Porous asphalt is used on roadways globally, and Japan has applied highly modified porous asphalt binders for over 20 years. Based on the advances in Asia and Europe, Kraton Polymers says it has been able to formulate a binder that exceeds the Japanese specifications for porous asphalt binders while retaining the workability and compatibility expectations of European road contractors.
The cooperation between KWS Infra, Latexfalt and Kraton Polymers contributed to the successful trial application of the new porous asphalt binder to a stretch of highway leading to the Eindhoven ring road in the Netherlands. This consisted of a 25mm top layer (approximately 10,000m²) of porous asphalt applied alongside an equal sized section of standard SBS (styrene-butadiene-styrene) modified bitumen.
The application was a success, despite the low temperatures, which are less desirable for applying asphalt, and the three parties are confident the results confirm the excellent performance capabilities of highly modified binders and will continue to monitor the trial site, says Kraton Polymers."