Guntert & Zimmerman equipment is being used to create a new hard-wearing asphalt surface on a key Interstate highway in the US state of Kansas as Mike Woof reports A busy Interstate highway in the US is now benefiting from a new, long-lasting surface. The road, Interstate 70 in Western Kansas, was in need of resurfacing. The full-depth asphalt roadway, up to 508mm thick in certain sections, had reached the end of its working life.
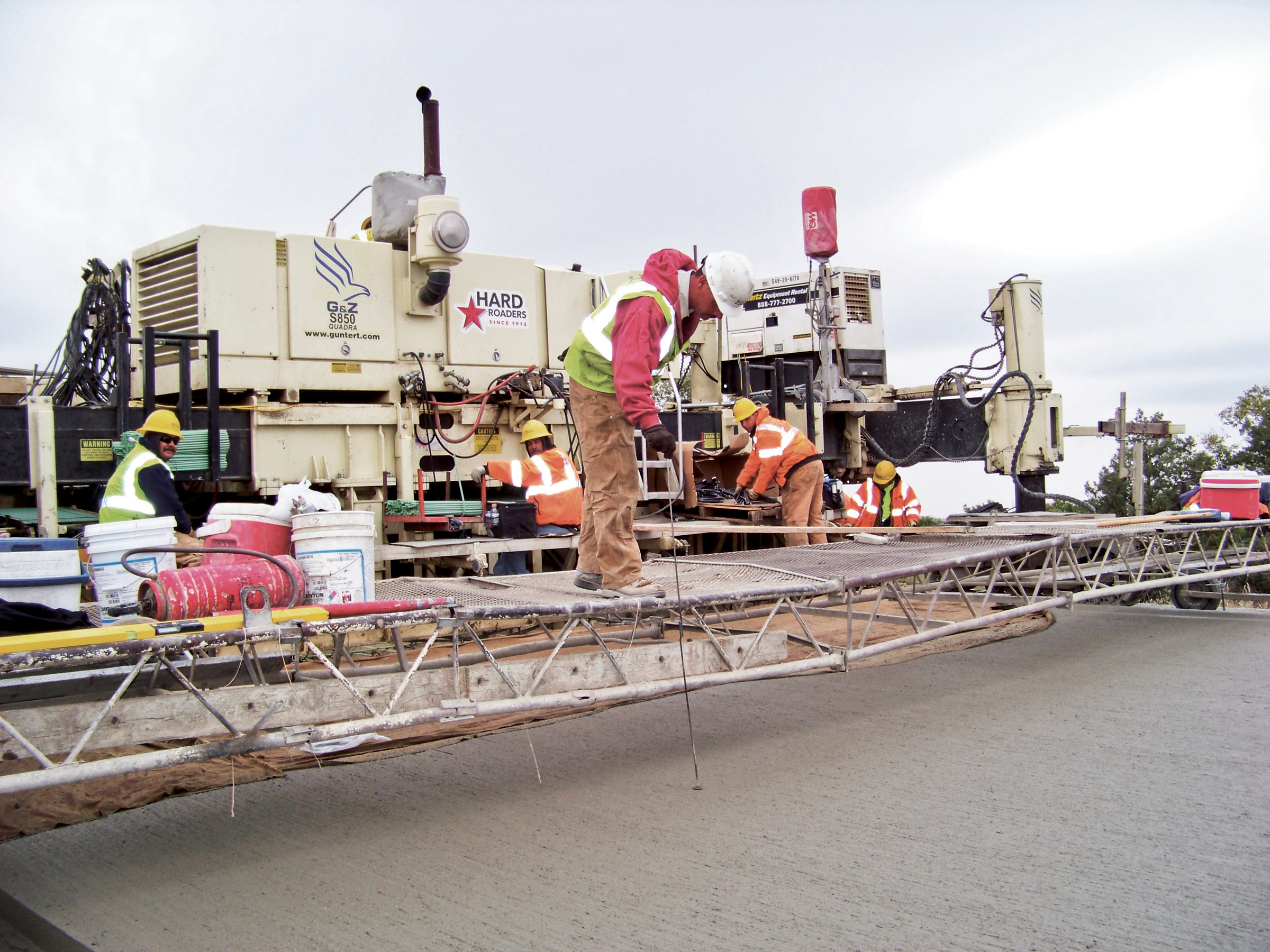
Using concrete Koss has been able to provide a hard-wearing, long lasting surface on key connections in Kansas
Guntert & Zimmerman equipment is being used to create a new hard-wearing asphalt surface on a key Interstate highway in the US state of Kansas as Mike Woof reports
A busy Interstate highway in the US is now benefiting from a new, long-lasting surface. The road, Interstate 70 in Western Kansas, was in need of resurfacing. The full-depth asphalt roadway, up to 508mm thick in certain sections, had reached the end of its working life.Resurfacing work had lasted just five to seven years and a longer term solution was required, according to Andrew Gisi, a geotechnical engineer with the Kansas DOT. The state opted for a 152mm bonded concrete overlay, some 121 million m2 of it in all. During 2011
Including shoulders, the two projects totalled 606,000m2 and the resurfacing cost some $20.1 million. The Kansas DOT is continuing with the I-70 upgrade and by the end of 2012, Koss will have milled and paved two more similar projects on I-70 for a total of 607,772m2 at a cost of $21.9 million.
The contractor has achieved good performance for its surface smoothness, winning incentives for every job it carried out in Kansas in 2011. The company also won an award from the Missouri-Kansas Chapter of the American Concrete Pavement Association (ACPA) for a 1372m section on which the contractor hit just 137mm of deviation.
Kansas DOT used Colorado’s pavement design criteria and system in designing its 152mm overlay on asphalt. With this technique, the overlay is sawn into panels that are 1.83m square and surfaces of this type have so far provided Colorado with 10-12 years of wear life on routes carrying heavy traffic, and remain in service.
Gisi says that Kansas expects to get 20 years from this overlay, possibly with some panel replacement at mid-life. He said, “The road really needed reconstruction, but we couldn’t afford that.”
Meanwhile Koss explained that the firm achieves good smoothness numbers on all of its contracts and added that it is easier to achieve low smoothness numbers on the thinner 152mm pavement, because the paver is not pushing a big head of material. “You can push the small head of mud and you are not extruding a lot of concrete either,” said Robert Kennedy, quality control manager for Koss.
Kennedy explained that the firm used dual stringlines. “We pay a lot of attention to the stringlines to make sure they are set up right and that our concrete batch plant is right. Then when we are confident that all of those things are set up, you have to be consistent,” he said. “The plant has to give you consistent slump on the concrete in every single batch after batch. And you have to have consistent delivery so that the paver never stops. Everything has to be in unison, working together.”
On a good day, Kennedy said Koss paved 1.6km a day, working 9.14m wide. “We averaged about 1505m2 per hour, or maybe a little better,” he said. Two belt placers spread concrete in front of the paver, and that helped boost production. That way, Koss could dump two trucks at once. Each project last year had its own batch plant, and typically 15 trucks hauled concrete to the site.
For nearly 3.2km of pavement last year, Koss paved with a stringless automated control system from
Koss used three robotic total stations, and set two of them 76m in front of the paver. One robotic total station was set behind. When the paver advanced close to the two forward stations, a technician would leapfrog the rear total station to a point up ahead.
Kennedy said one advantage to the milling and concrete overlay process was that Koss could correct roadway slopes and transitions into and out of curves. With so many asphalt treatments over 40 years, the slopes had gone awry. “We could go in there and pave back to the exact slope and correct all of those geometric issues,” Kennedy said.