Concrete paving is being carried out on a key section of Interstate 20, close to the US city of Colombia in South Carolina Contractor Zachry Construction has had success using its Guntert & Zimmerman concrete slipformer for an Interstate paving project in South Carolina. The firm has been using the machine on the US$64 million project to resurface a section of Interstate 20, close to the city of Columbia.
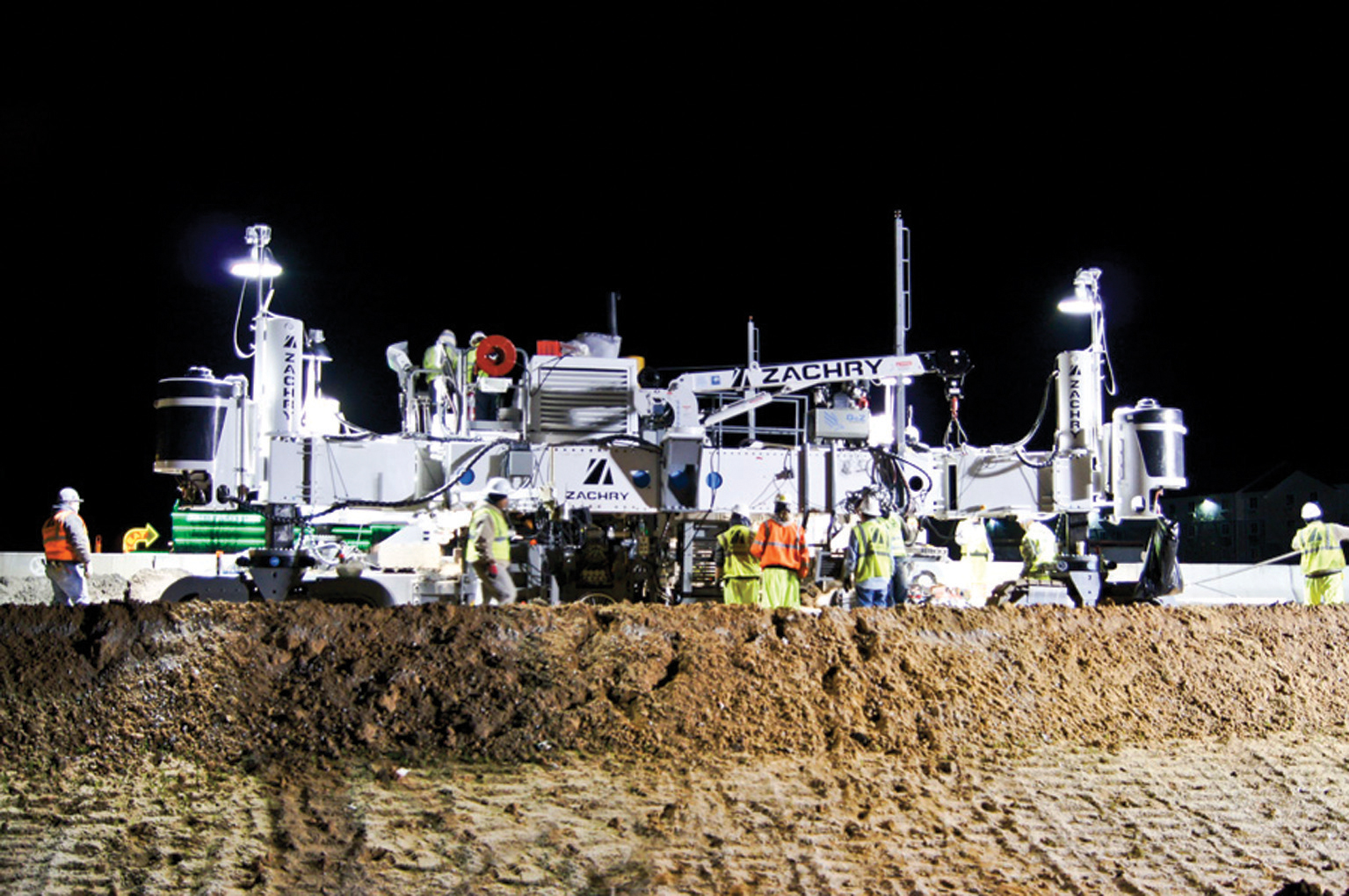
Contractor Zachry Construction has been using its G&Z paver on a contract in South Carolina
Concrete paving is being carried out on a key section of Interstate 20, close to the US city of Colombia in South Carolina
Contractor Zachry Construction has had success using ITS225 Guntert & Zimmerman concrete slipformer for an Interstate paving project in South Carolina. The firm has been using the machine on the US$64 million project to resurface a section of Interstate 20, close to the city of Columbia.
Zachry carried out the work with ITS new S-850SL-CDBI by paving sections of 305mm-thick concrete on Interstate 20 at 5.5m wide. Production in early May was running between 157 and 275m3 of concrete/hour, or between 1,067 and 1,219m/ day, according to project manager Curtis Schwartz.
Due to new development on the east side of Columbia, the South Carolina Department of Transportation has opted to widen Interstate 20 from two lanes to three on a 9.6km stretch near Interstate 77. Zachry will first pave an inside lane and shoulder in a 5.5m wide slab on each side of the four-lane divided highway. Then in a multi-staged process, the contractor will remove the existing eastbound and west-bound lanes and pave two new lanes at 7.3M wide on each side.
The new paver was equipped with a G&Z dowel bar inserter (DBI) and a265 Leica PaveSmart 3D stringless machine control system for the project. The DBI played a major role in Zachry’s decision to buy the new paver, said Zachry’s equipment manager. Originally the firm planned to pave the I-20 project at 10.4m wide but decided to buy the Guntert & Zimmerman machine because of ITS versatility and as it could be used at desired widths with a dowel bar inserter.
The new dowel bar inserter has proven accurate and X-Ray tests Confirm that these are being placed at the right depth. The joints are spaced 4.6m apart for the I-20 job and the G&Z equipment has placed the dowel bars where required, according to Mark Fancella, Zachry’s paving superintendent on the project.
Fancella has used competing units but said he has been impressed by the G&Z’s side forms and their ability to move in and out, as well as the swing legs which can be tucked in to allow the machine to pave right alongside a median barrier.
The swing legs allow an operator to steer the tracks at a 90° angle and move the paver straight sideways.
Or for loading the paver for transport, the legs can be swung around to the side and the machine steered at 90° to crawl it directly onto the trailer. Another reason Zachry bought the Guntert & Zimmerman paver is for the telescoping ends on the machine. They make it easier to change widths, especially if the DBI is not on the machine.
Using the machine has been something of a learning curve as this has been the contractor’s first job on the East Coast and it had to hire a new team. In addition, this is Zachry’s first concrete paver with a stringless machine control system, although it only took about a week for crews to learn the new Leica system. The dowel bar inserter also allows trucks to dump concrete directly in front of the 850SL CDBI paver. Zachry has used three robotic total stations with the Leica PaveSmart 3D system, with two active at any time to control steering and grade on the paver. The Leica system regulates the steering, grade, draft and crossfall of the paver with no need to retrofit complex hydraulics.
The PaveSmart 3D package guides the paver in relation to a digital 3D model of the highway, running on the paver’s onboard computer.
The paver is equipped with two prisms, mounted above the machine, as tracking targets for the two active stations. When setting up the robotic total stations, a technician back-sights each of them to five known control points.
That fixes the location of the total stations relative to the digital model. The two total stations then follow the movement of the two prisms on the paver and communicate to the machine computer the paver’s precise location via radio link. The machine’s computer calculates the differences between the paver’s actual location and the digital terrain model and the system then instructs the G&Z paver to regulate the mold’s steering and grade automatically.
Fancella said that the system works best to set up the total stations 76m in front of the paver. As the machine passes the next total station in front of it, the crew moves the rear station around in front, leapfrogging the total stations down the highway so that the paver can move continuously. Even in traditional stringline paving, stopping the paver is highly undesirable for mainline paving, as it can introduce a bump in the surface which will count against the ride bonus the contractor is striving to achieve.
It is necessary to use an accurate digital model and to calibrate the paver correctly in order for the stringless control system to work properly, according to Fancella. He said that paving without a stringline offers benefits. “You can back trucks in directly in front of the paver without worrying about a stringline. When you use a stringline, it’s like you’re trapped inside of a room. But with the stringless control system, the paver is out in the open.”
Contractor Zachry Construction has had success using ITS
Zachry carried out the work with ITS new S-850SL-CDBI by paving sections of 305mm-thick concrete on Interstate 20 at 5.5m wide. Production in early May was running between 157 and 275m3 of concrete/hour, or between 1,067 and 1,219m/ day, according to project manager Curtis Schwartz.
Due to new development on the east side of Columbia, the South Carolina Department of Transportation has opted to widen Interstate 20 from two lanes to three on a 9.6km stretch near Interstate 77. Zachry will first pave an inside lane and shoulder in a 5.5m wide slab on each side of the four-lane divided highway. Then in a multi-staged process, the contractor will remove the existing eastbound and west-bound lanes and pave two new lanes at 7.3M wide on each side.
The new paver was equipped with a G&Z dowel bar inserter (DBI) and a
The new dowel bar inserter has proven accurate and X-Ray tests Confirm that these are being placed at the right depth. The joints are spaced 4.6m apart for the I-20 job and the G&Z equipment has placed the dowel bars where required, according to Mark Fancella, Zachry’s paving superintendent on the project.
Fancella has used competing units but said he has been impressed by the G&Z’s side forms and their ability to move in and out, as well as the swing legs which can be tucked in to allow the machine to pave right alongside a median barrier.
The swing legs allow an operator to steer the tracks at a 90° angle and move the paver straight sideways.
Or for loading the paver for transport, the legs can be swung around to the side and the machine steered at 90° to crawl it directly onto the trailer. Another reason Zachry bought the Guntert & Zimmerman paver is for the telescoping ends on the machine. They make it easier to change widths, especially if the DBI is not on the machine.
Using the machine has been something of a learning curve as this has been the contractor’s first job on the East Coast and it had to hire a new team. In addition, this is Zachry’s first concrete paver with a stringless machine control system, although it only took about a week for crews to learn the new Leica system. The dowel bar inserter also allows trucks to dump concrete directly in front of the 850SL CDBI paver. Zachry has used three robotic total stations with the Leica PaveSmart 3D system, with two active at any time to control steering and grade on the paver. The Leica system regulates the steering, grade, draft and crossfall of the paver with no need to retrofit complex hydraulics.
The PaveSmart 3D package guides the paver in relation to a digital 3D model of the highway, running on the paver’s onboard computer.
The paver is equipped with two prisms, mounted above the machine, as tracking targets for the two active stations. When setting up the robotic total stations, a technician back-sights each of them to five known control points.
That fixes the location of the total stations relative to the digital model. The two total stations then follow the movement of the two prisms on the paver and communicate to the machine computer the paver’s precise location via radio link. The machine’s computer calculates the differences between the paver’s actual location and the digital terrain model and the system then instructs the G&Z paver to regulate the mold’s steering and grade automatically.
Fancella said that the system works best to set up the total stations 76m in front of the paver. As the machine passes the next total station in front of it, the crew moves the rear station around in front, leapfrogging the total stations down the highway so that the paver can move continuously. Even in traditional stringline paving, stopping the paver is highly undesirable for mainline paving, as it can introduce a bump in the surface which will count against the ride bonus the contractor is striving to achieve.
It is necessary to use an accurate digital model and to calibrate the paver correctly in order for the stringless control system to work properly, according to Fancella. He said that paving without a stringline offers benefits. “You can back trucks in directly in front of the paver without worrying about a stringline. When you use a stringline, it’s like you’re trapped inside of a room. But with the stringless control system, the paver is out in the open.”