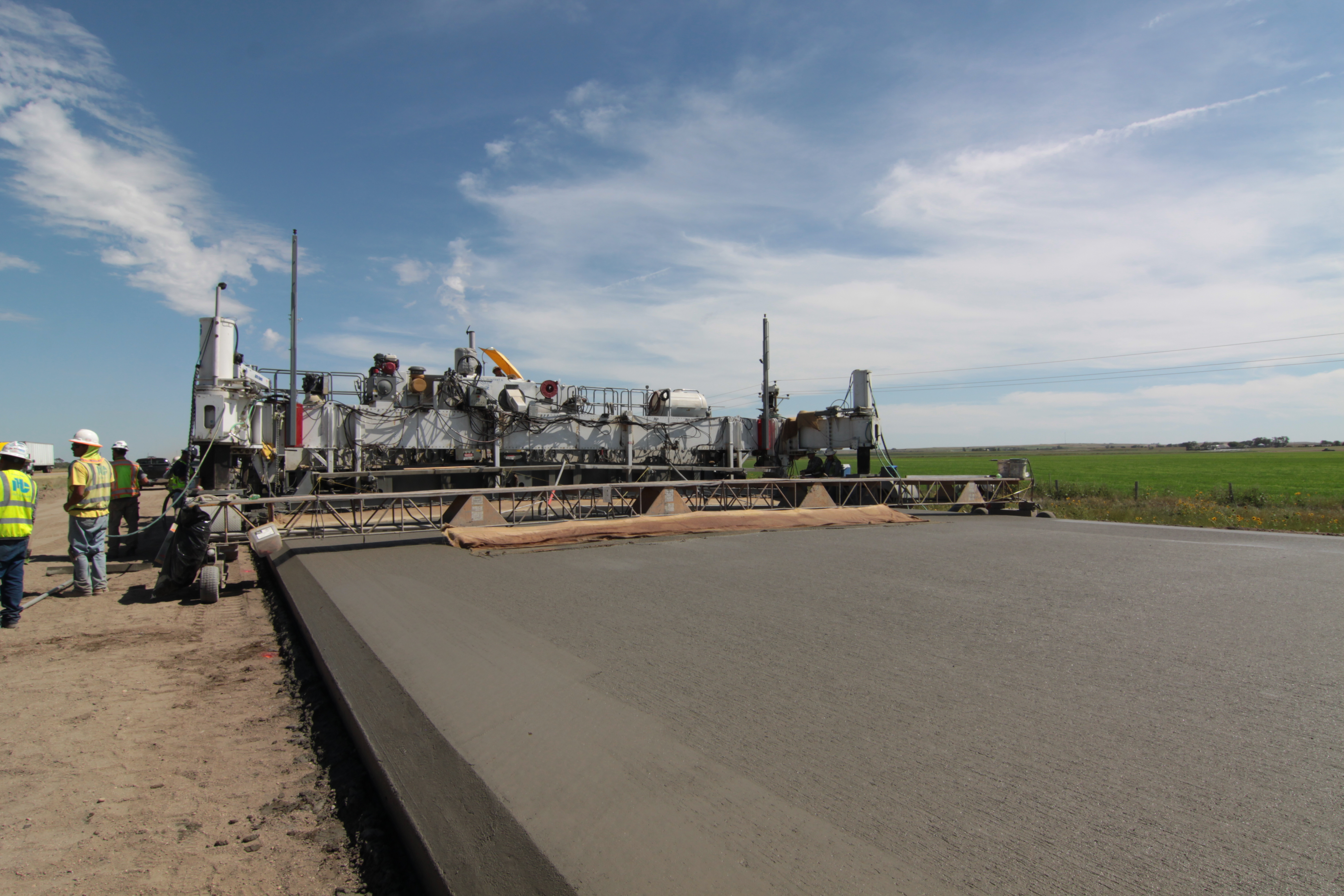
Much-needed work on a busy section of Interstate 80 has been carried out in Nebraska to improve the road surface. This is one of the most important highways in the US, providing a link that stretches right across the country between the east and west coasts. This busy highway carries a high percentage of heavy truck traffic as it is a vital transport route. However this constant flow of large trucks had taken its toll on the road surface, not helped by harsh winter conditions that had added to the heavy wear and tear and resulted in further deterioration. The worsening condition of the road surface of a key stretch became of increasing concern to the state authorities in Nebraska. As a result, Nebraska Department of Roads (NDOR) decided that this section of highway had to be upgraded and awarded a contract to improve a 15.5km stretch of the historic route, between Brule and Big Springs in the west of the state. Although not large in terms of cost, improving this section of highway was vital to allowing heavy
truck transport from Nebraska to the neighbouring state of Wyoming to the west. The contract for the highway upgrade was awarded to a specialist firm, Interstate Highway Construction (IHC), with the work being handled by the company’s west division, based in Colorado. The project was carried out during the 2015 and 2016 paving seasons and involved the removal and reconstruction of both the eastbound and westbound lanes of Interstate 80.
For IHC the project presented a challenge. While the geology and topography of the area are not complex, the firm knew it had to deliver the work within the tight time constraints given as the unpredictable weather meant that the paving period could be shorter than desired. The highway is prone to closures in winter when the weather reaches its extremes, while the state also experiences severe thunderstorms and tornadoes. The hot summer weather in the area is well-suited to road construction but as the paving window can be restricted, productivity was a crucial focus for the work to be carried out as required.
At the same time, surface quality was also key and IHC was keen to provide a highway running surface with a very smooth finish as the firm knew it could win back bonuses if this could be achieved. Smooth road surfaces are much preferred as they are safer and less prone to early wear in the areas around bumps. A road with a smooth surface is less tiring to drive along and reduces wear and tear on vehicles too, important points from the client’s perspective.
IHC opted to use an S1500 concrete paver from
The use of the stringless machine control technology on the paver was crucial as it allowed the necessary cross-slope and elevation to be achieved, while delivering the all-important smoothness results. Dispensing with the stringline reduced setting-up time for the survey crew, as well as opening up access to the paving lane. Doing without the stringline also eliminated the risk of accidental breakages, as these are vulnerable to damage from personnel or equipment, which can cause delays or surface issues.
The use of the CDBI system meanwhile meant that there was no need to locate baskets in front of the paver. This provided another saving as it eliminated the need for the use of a placer, as well as saving additional time on the job. In addition, the removal of the stringline and the baskets made it easier for IHC in terms of logistics as the firm was able to increase the efficiency of the concrete delivery process by truck, directly to the paver.
IHC has used concrete pavers from Guntert & Zimmerman for many years and has a great deal of experience in this type of specialist work. However the firm required an S1500 for this job due to the width of the paving work being carried out. The machine features a double-telecopic frame that can extend by 3.6m on either side of its 5.4m centre frame module. This allows the S1500 to be able to handle paving widths from 5.4-12.8m, easily sufficient for the 12.2m required for this specific project. Moreover, the S1500 can be adapted to handle even larger paving widths of as much as 16m, with the use of optional bolt-in sections.
The machine has a paving kit with a deep section, latticework frame design. According to the manufacturer, this provides both stiffness and rigidity for paving work, which helped the contractor to deliver the tough smoothness requirements from client NDOR for the work. The design of the paving kit also allows as many as three crown points over the paving width. For this project IHC had to provide two crown points in the slab and Pablo Erazo, paving foreman for IHC explained, “We have a double crown throughout the (12.2m) width, 2% at the centre travel lanes and 4% at the shoulder.”
The use of the CDBI was able to automatically position the dowels at a preset depth in the concrete slab. This eliminated the need for the assembly and placement of thousands of baskets along the 15.5km-long by 12.2m-wide stretch of highway.
With IHC’s S1500 paver set up to pave the 12.2m width, the crew was able to deliver a slab with a1.2m inside shoulder and twin 3.6m wide travel lanes. According to Clark, being able to pave the entire width in a single pass eliminated the need to key in a longitudinal joint, while also improving quality by eliminating failure points. He added that this approached also saved time, around 10 days from the paving schedule.
The use of stringless paving technology can be integrated into Guntert & Zimmerman’s pavers such as the S1500 using its NoLine: Stringless Paving Preparation Kit. This system allows contractors to connect stringless systems directly into the paver’s controls. Meanwhile, telescopic mounts on the paver can be used to mount two Leica prisms. The proven machine control package was crucial to the work and Adam Hall, west division surveyor for IHC, said that the system provided four survey points, meaning that it took less than a day to configure the set-up for the job.
The modular CDBI module meanwhile was mounted to the rear of the S1500’s frame and without the need of a separate diesel power pack to drive it. The contractor had previously paved maximum widths of 11.5m using a CDBI system but found the equipment suited the project, placing the dowels at 305mm centres. In all, 25 dowels were inserted at every 5m contraction joint in the slab.
IHC planned for 20 days of mainline paving work to be able to resurface the eastbound and westbound lanes. The firm also estimated that 20 days would be needed for paving the various gaps, ramps and crossovers.
To optimise material supply as well as the paving process, IHC sited its concrete mixing plant roughly at the centre of the site. This helped to reduce material delivery times to the paver and ensured that the mix was fed continuously to the machine using a fleet of end-dump trucks. The plant was set to produce a mix that met the Nebraska 47-B grade, containing 70% sand and 30% of aggregates with a maximum size of 19mm. The plant delivered 343m3/hour, providing a mix with 6.5-9% of air entrainment. The paving crew set a production target of 50 truckloads of concrete placed in front of the S1500 paver/hour, around 500 trucks/day, allowing it to pave a distance of 800m/day.
In total, the paving project delivered close to 380,576m2 of concrete pavement, featuring dowels. The travel lanes were paved at 330mm deep, while the shoulders tapered off to a depth of 254mm, although IHC said that the weight of the paving kit on the paver can allow it to pave thicknesses up to 457mm, when set-up correctly. The spreader plow helped to distribute the mix across the entire front of the paver, while also eliminating the need for side-mounted gearboxes.
The stringless system the contractor utilised had four survey points and with two survey guns pointed toward the receivers at the top of the paver. IHC explained that this allowed the firm to triangulate points to get elevation and position. The contractor surveyed every 91m, while also utilising secondary guns to deliver the necessary quality control and quality assurance checks.
Using an accurate elevation control over the paver helped deliver the necessary smoothness, as well as to ensure correct and accurate dowel bar positioning to the centre of the slab. The specification required the dowels to be placed at depths of 152-178mm depth from the surface of the slab. The quality control system utilised an MIT scan to ensure that the dowels were placed correctly.
Construction work on Interstate 80 commenced in 1956, with sections being amongst the first interstate stretches to be built in the US. This followed immediately after the passing of the Federal Aid Highway Act of 1956 under the leadership of then president Dwight D Eisenhower. The stretch of Interstate 80 through Nebraska was finished in 1974, although the highway took until 1986 to be completed.
It is worth noting that the route of Interstate 80 long predates the construction of the US interstate network. Eisenhower was inspired to begin the development of the Interstate system due to his previous experience crossing the US as part of the 1919 Army Convoy, which travelled along the original Lincoln Highway that Interstate 80 now follows. As a young army officer at the time, Eisenhower experienced at first-hand the dirt roads that delayed the convoy’s journey along the Lincoln Highway, the first continuous stretch of road to cross the US. When he was later elected president, Eisenhower vowed to invest in road construction to boost transport for both strategic and economic reasons, helping develop the country’s economy. In the western states, Interstate 80 roughly follows the route of the historic California Trail through much of Nevada and California. It also follows the historic Oregon Trail through Wyoming and Nebraska, as well as the Great Platte Highway. Along other sections it follows the route o
f the Victory Highway, State Route 1, and US 40. In addition, the highway has further importance for US transport history as it follows the route of the First Transcontinental Railroad, as well as the US postal flights of the 1920s and 1930s.
Interstate 80 is an important road link for the US, closely following the route of the original Lincoln Highway. The route runs right across the US, from a junction with Interstate 101 in San Francisco in California in the west all the way to Teaneck in New Jersey, in the east and on the outskirts of New York City.
The highway measures just over 4,666km in all and is second only to Interstate 90 in length. Historically important, Interstate 80 has played a key role in the development of the US.
From west to east, the highway runs through the states of California, Nevada, Utah, Wyoming, Nebraska, Iowa, Illinois, Indiana, Ohio, Pennsylvania and New Jersey. It also connects a number of important cities in addition to San Francisco and New York City, including Oakland and Sacramento in California, Salt Lake City in Utah, Omaha in Nebraska, Des Moines in Iowa, and Toledo in Ohio.
In addition it runs within 16km of Chicago in Illinois and Cleveland in Ohio. The highway passes through a wide range of terrain, including a stretch crossing the famous Bonneville Salt Flats in Utah, reaching a maximum elevation of 2,630m in Wyoming and crossing the Continental Divide, also in Wyoming. In addition it passes through the Red Desert, the Wasatch Mountains and the Rocky Mountains.
The 116km section of Interstate 80 in Nebraska between exit 318 close to Grand Springs and the city of Lincoln is the straightest in the US, deviating by only a few metres along this stretch.