One thing is clear in the concrete slipforming sector. This comparatively niche market for equipment is rapidly becoming a good deal more competitive as key manufacturers jostle for position.
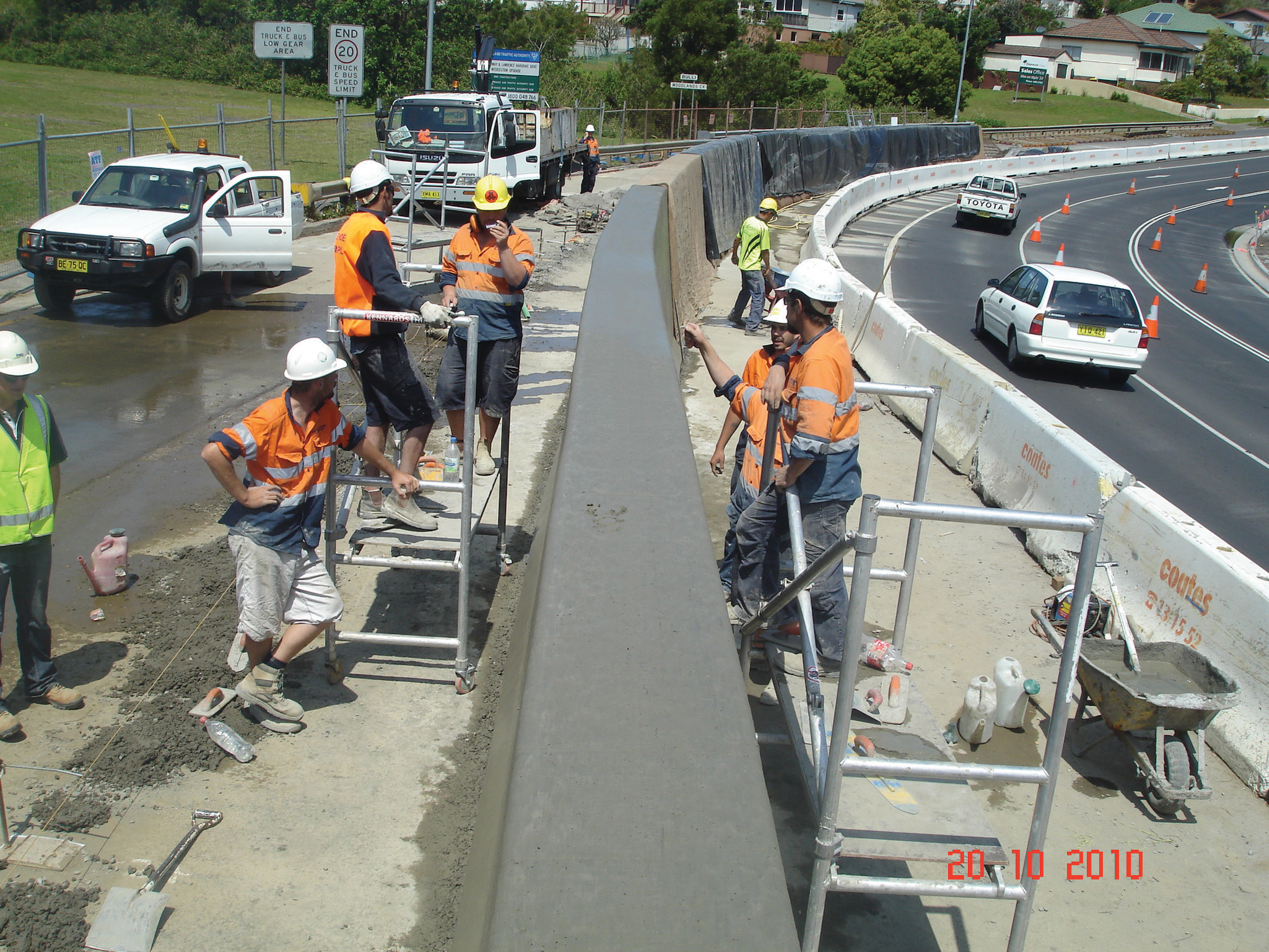
A special mold was required to slipform the 2m high barrier that was manufactured by Power Cubers for the work
Competition is gearing up in the concrete paving market, Mike Woof reports
One thing is clear in the concrete slipforming sector. This comparatively niche market for equipment is rapidly becoming a good deal more competitive as key manufacturers jostle for position. This is particularly apparent at the smaller end of this segment, for compact slipforming machines where an array of new models is coming to market.In addition, the demand for high precision 3D control solutions continues to develop, with manufacturers embracing this technology. In this respect,
Go for concrete GOMACO has developed several new machines, including the ultra-compact 4400 which is designed specifically for use in barrier work and in the European market. The 4400 features a new frame design that maximises its versatility and the machine can be used for both right-side and left-side slipforming. The control console can be slid from one side of the machine to the other, allowing the operator a high degree of visibility of the paving operation in all applications. The machine features GOMACO's proven G+ control system, which is said to be simple to use, as well as featuring an array of language options.
The new 4400 offers symmetric steering and minimal set-up changes, which allows it to switch profiles from one side to the other and also has the new barrier hook-and-go mold mounting system. This allows an operator to locate barrier molds up to 1m high on either side of the machine, while an option allows a larger barrier. The GOMACO?barrier mold is designed to allow effective vibration and consolidation of material and features the firm's trailing stainless steel configuration to maximise finish quality.
The machine is fitted with the new 4400 series auger with its pitch and speed suited for transporting low slump concrete. The 406mm?diameter auger has polyurethane, bolt-on blade liners for extended wear and protection. Its four-way hydraulic positioning capability allows the auger to be placed for concrete receiving and delivery to the mold on either side of the machine.
The 4400 is powered by a
Also new from the firm is the GP-2400, a half-width concrete paver capable of slipforming widths up to 7.3m. The GP-2400 is designed to work in tight-radii applications, as well as being user-friendly, manoeuvrable, easy to transport and quick to set up. The machine was developed following a request from a contractor for a machine capable of slipforming a tight radius. The new paver is equipped with 3m series two tracks that are capable of turning tighter than conventional length tracks on a paver. The tracks also allow for a minimum machine transport width of 3m, making the machine considerably easier to move from site to site. As with the 4400, the GP-2400 is equipped with the G+ control system that has self-diagnostics for grade and steering.
The paver is equipped with the firm's 3100 series open-front mold and a telescoping frame for versatility, allowing paving widths from 3-5m, with the standard telescoping frame and paving widths up to 7.3m with frame inserts, while 16 vibrator circuits are standard.
Power comes from a 129.5kW C6.6
Californian option Guntert & Zimmerman has long been a major player in the concrete slipforming market, but its focus in recent years has been on the larger end of the sector, specialising in the biggest machines for use in applications such as canal construction. However the company's new compact S600 increases its level of competition with its rivals.
Company president Ron Guntert explained, "With the success of the S850 in the US market, these same customers came to us and asked us for a smaller paver." He said that the S850 has developed a reputation for achieving good smoothness and was keen for the S600 to offer a similar performance in this respect. "The main criteria was to offer the widest range possible in paving widths and we had to figure out a way to do that. We patented a system with hydraulic clamping that slows fast widening and has no need of support. We also have a turnbuckle solution, with a mounting bracket independent from the frame." Guntert & Zimmerman has also been investing in its internal operations and manufacturing capabilities. Marketing manager David Lipari said, "We've been focusing on customers." He continued, "We've spent a lot of time in the last year building jigs to speed up production and we've introduced a scheduling system to improve efficiency. It streamlines the process for the assembly shop." The improved production flow will be of benefit to the firm, which anticipates strong demand for the new compact machine now offered. There has also been strong commercial interest in the new telescopic ends developed by the firm, announced at the same time as the new S600 slipform paver. Existing customers have placed enquiries for the telescopic units as these can be retro-fitted to boost versatility of earlier machines as the paving kit the company fits features a universal design, according to Lipari. He added that customers in Omaha, Nebraska and Salt Lake City in Utah have purchased telescopic ends for their machines as these units allow for fast width changes. Lipari added that Guntert & Zimmerman system for fitting a compact dowel bar inserter (DBI) on its existing S850 paver is also now offered as an option for the new S600.
According to the firm, early orders for the S600 show that the machine will have strong market appeal. The first of the new S600 models was supplied to a customer in Pittsburgh, with the second being delivered to a customer in Belgium, the third to a contract in Texas being handled by
Guntert & Zimmerman's design goals for the S600 were to make it the most productive and manoeuvrable multi-purpose, slipform paver on the market. Versatility is crucial for this class of machine and the company also wanted the unit to be highly adaptable, allowing users to specify different features and change the set-up quickly so as to suit a wide array of applications. The machine is competing in the market against some well-proven and highly successful machines from the competition, so Guntert & Zimmerman is aware of the challenge this presents.
Lipari said, "This is designed to do shoulders and barrier walls and can also pave widths out to 9m. At the same time, it's also able to achieve very strict smoothness tolerances." He added, "For existing customers, we wanted the machine to use the same features as our current machines."
The S600 can be used to carry out narrow profile paving applications, as well as being able to pave maximum widths of 9m and according to the firm the unit also has the deepest tractor frame of any machine in the compact class. Lipari said, "This is a machine that fits in between a single and a dual lane paver."
Another feature of the tractor is that its design allows the paving kit to be located anywhere along the paving frame. The proven paving kit fitted as standard to the S600 is the same unit as used on the larger S850 and this can feature an optional crown system that allows a 3% profile if required. Meanwhile the machine offers 457mm of vertical adjustment and includes a guillotine system for the start/end of paving work. The machine is also said to allow more flexibility on where to locate the paving kit in relation to track position and the paving slab. Lipari said, "Offset paving is another feature we have available."
A novel option for the tractor, which has a base weight of around 25tonnes, is an overlap between the swing bolsters and the tractor frame that does away with the need to reposition the turnbuckles, allowing for fast width changes. Joystick controls are said to make the machine easy to use and the control panel can be moved to suit the operator. The machine has other important features and options too. The jacking columns offer an adjustment range of 1.07m and this means standard barriers can be slipformed in a single lift. The machine runs using a CANbus system for its electronics and also features a new software platform that was developed in-house. The machine continuously monitors operating parameters and should problems such as clogging arise, an alarm sounds. A transducer system ensures that the machine will keep tracking in a straight line automatically when in paving mode, while the fuel tank has been located so that it does not block the operator's view. Lipari said, "We fit a lot into a small space and we've automated a lot of functions." Even the walkway retracts with the machine and there is no need for a bolt-on walkway as with some competing machines. Lipari said, "We maintained visibility under the walkway at narrow width so the operator can see the liquefaction."
An array of options are available including tie bar inserter, telescopic ends, DBI, smart 90° swing legs, anti-torsion control, electric poker vibrators and final finisher. Narrow profile, four roller tracks are fitted as standard that feature a planetary gearbox and a two speed drive, although wider undercarriage units can be specified for machines fitted with the DBI system or for the broader paving duties. The track design allows paving work to be carried out to within 76mm of the barrier. A 149kW Cummins diesel is fitted as standard, although the customer can also select the more powerful 194kW engine option, should the machine be specified for DBI work. To fit this size of engine on the model presented a design challenge according to Guntert. But operating noise and emissions are low due to the use of the latest Cummins diesels and the machine features low ambient working temperatures, further reduced by a hydraulically driven cooling fan. Guntert added, "This S600 paving kit is one of the quietest in the industry."
Meanwhile the company is also looking ahead in terms of technology and is keen to develop its experience in using 3D paving control technology. Guntert said, "We were a bit late into this market but we've come a long way and we're convinced stringless technology is here to stay. We had our first Leica Geosystems 3D trial in Iowa and the smoothness results we got were world class."
German technology German firm
The larger SP25 can be used in inset mode to pave concrete slabs with widths from 1-3.5m and paving thicknesses of up to 400mm, both on surface and in tunnel construction. In offset mode, the SP25 can slipform safety barriers of up to 2m in height, as well as kerbs, gutters, shoulders and concrete slabs or bicycle paths of up to 2.5m in width.
Australian barrier boosts safety
A special 2m high concrete barrier is helping boost safety at an accident black spot in Australia. The drive down Bulli Pass into Bulli, near Sydney in New South Wales can be a treacherous one and concerned with the risk of trucks losing control at the bottom of this winding road, the local authorities decided to build a barrier wall to contain traffic. Knowing the threat posed by runaway trucks, the Road & Traffic Authority designed a massive wall, 2m tall and anchored to a 1x1m concrete footer resting on 8m deep piles spaced on 2m centers. Fearing that out of control trucks could entering the jobsite, the R&TA decided to close the road to truck traffic while installation took place. Though the wall was designed to cover only a short distance, prime contractor
The contractor used its
For the standard slipform paver models, concrete feed is supplied through a belt conveyor although customers have the additional choice of an optional folding belt conveyor or auger conveyor. The feed systems offer an array of hydraulic adjustment options in terms of incline and slewing angles and can also be moved transversally and longitudinally.
Because compact slipform pavers may be required to handle different profiles in a single working shift, Wirtgen says it has designed the SP15 and SP25 to be able to change set up quickly. This is achieved with the optional quick-change mold mounting system. Operation of the hydraulic quick-change mold mounting system is said to be simple, with the operator lowering the machine and driving up to the mold to slide mounting hooks into guides. Hydraulic clamps then secure the mold.
Both of the new machines are available with a trimmer that is fitted with cutting tools arranged in a helical pattern, to prepare the base, ensuring uniform profile paving. The trimmer offers height and slope adjustment and can be telescoped horizontally using its hydraulic cylinders. The unit has a working depth of up to 150mm and offers a standard width of 600 mm but can be extended in increments to a maximum width of 1.6m.
To reduce fuel consumption as well as noise and emissions, the machines feature an eco mode that automatically adjusts engine output to match demand. The SP15 is powered by a four cylinder diesel rated at 92kW, while the larger SP25 has a six cylinder diesel rated at 118kW and both machines meet the latest emissions regulations. The machines have high traction drive motors in their crawler tracks allowing paving and travel speeds of 15m/min and 35m/min respectively, an increase over the models being replaced.
The machines feature accurate paving controls and the standard levelling system includes a slope sensor, two level sensors and two steering sensors, with a 3D kit available as an option.
A 3D interface allows all commercial 3D systems to be used and the SP25 also offers optional level and steering sensors for use when driving through narrow radii. In addition, the versatile modular design of the firm's levelling technology allows versatility as this means the pavers can be operated using conventional stringlines as well as advanced 3D controls.