Internationally, airports are being upgraded and expanded to increase capacity and safety – Mike Woof writes. All around the world, airports are being expanded and upgraded, both to cope with massive increases in passenger numbers and also to handle larger aircraft. Runways have to be rebuilt with stronger structures and surfaces to handle greater air traffic volumes as well as increased loads from larger aeroplanes. Building airport runways, however, poses many challenges for construction crews. Paving qua
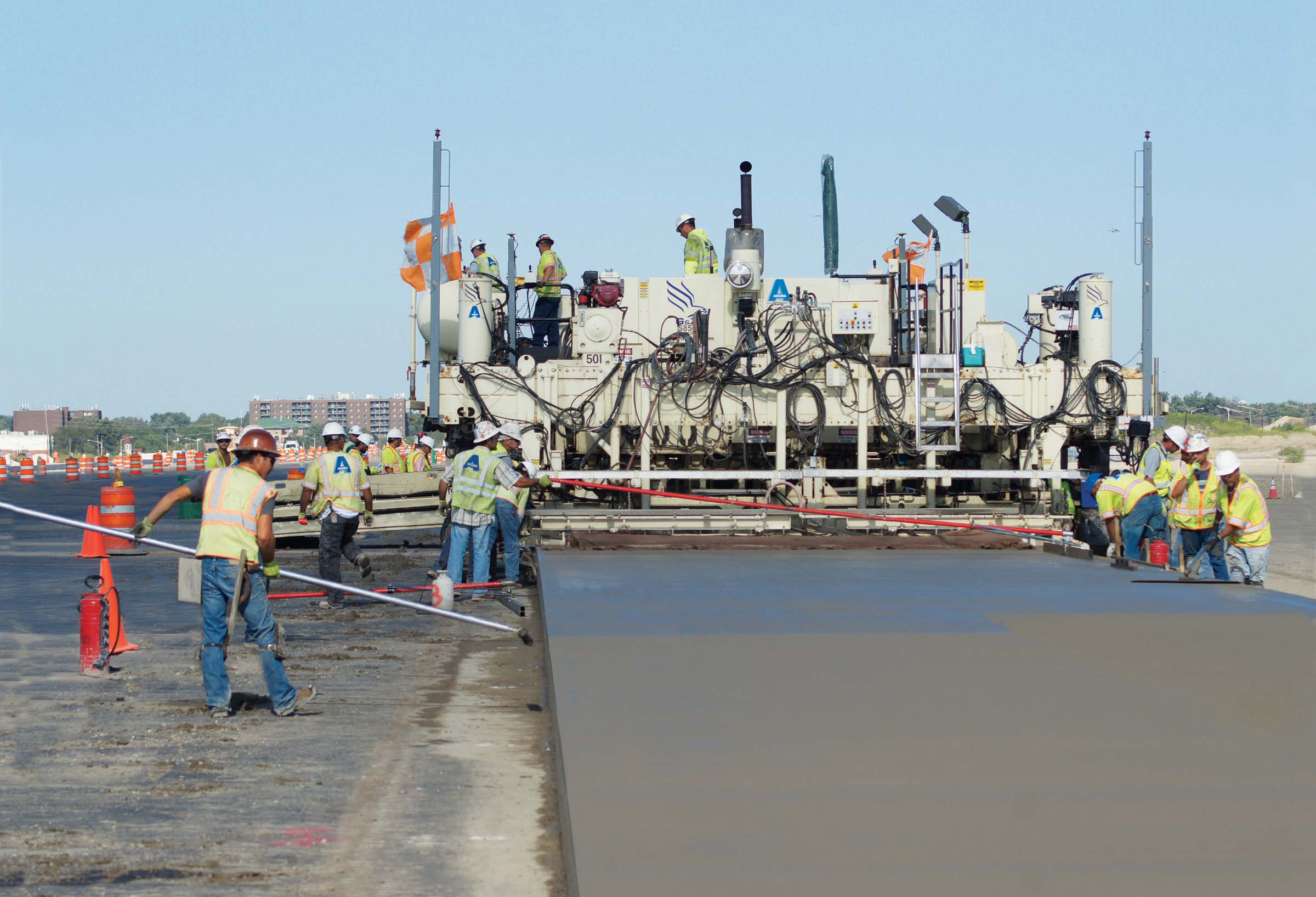
The high-quality, low-slump concrete has itself been a challenge to work with
Internationally, airports are being upgraded and expanded to increase capacity and safety – Mike Woof writes
All around the world, airports are being expanded and upgraded, both to cope with massive increases in passenger numbers and also to handle larger aircraft. Runways have to be rebuilt with stronger structures and surfaces to handle greater air traffic volumes as well as increased loads from larger aeroplanes. Building airport runways, however, poses many challenges for construction crews. Paving quality has to be extremely high so as to maximise safety, while time schedules can be very strict, with only short possession time available and tough penalties for late working.
The Chicago Department of Aviation is managing one of the largest construction projects in the country at O’Hare, one of the world’s busiest airports. The O’Hare Modernisation Program (OMP) promises to upgrade the airport’s outdated layout into modern parallel runways to reduce flight delays in all weather conditions.
When the project is complete, O’Hare will have eight runways, including six east-west parallel runways and two crosswinds runways. A partnership between Turner Construction, Acura, and Lindahl Brothers is completing runway and taxiways work, a south air traffic control tower and several other enabling projects. The bulk of the concrete paving is being completed by Acura.
The firm is an experienced concrete paving contractor but this is its first airport job. The specifications are tighter and the concrete mix is more challenging than the crews are used to. Additionally, this job requires the use of a dowel bar inserter and stringless paving job, both of which the firm is using for the first time.
The firm is confident it can complete the work efficiently as it has an experienced crew and is using a machine in which it has confidence, a225 Guntert & Zimmerman S850 paver with a compact dowel bar inserter (CDBI) system. But the project is demanding and the team is using new technology on an airport project with very strict 2423 Federal Aviation Administration (FAA) specifications. The crew must meet 2.54mm line precision tolerance and 1.27mm grade tolerance from theoretical zero.
The CDBI system is helping achieve high productivity as it eliminates the time and expense of placing dowel baskets in front of the paver. It can be quickly fitted on to the rear of the paver and accurately inserts the epoxy-coated dowel bars along the transverse contraction joint.
Dowel bars are inserted at 457mm centres every 6.1m of paving. The dowels have to be precisely inserted into the concrete vertically and horizontally according to the firm, saving time and materials.
The firm is also the first in Illinois to use stringless paving and the dowel bar inserter at the same time but has managed this successfully on its first attempt. The company has also managed to meet the stringent requirements of a high-profile airport paving project. It has installed about 40,000 dowels using the CDBI and started at 97% passing during the first couple of pours. After that, it has achieved nearly 100%, even with the very strict specifications and acceptance criteria, maintaining quality, while delivering the final product within the necessary timeframe.
Acura equipped its Guntert & Zimmerman PS1200 placer spreader and S850 slipform paver with Guntert & Zimmerman’s NoLine Stringless Paving Preparation Kit. The set-up uses GPS technology from Leica Geosystems for grade and elevation control. This connects directly into the paving equipment’s controls, and the kit provides telescopic mounts for two total station prisms.
According to Acura president, Nico DiGioia, “The accuracy of Guntert & Zimmerman’s hydraulic system and compatibility with the Total Station System is delivering some phenomenal results for grade and line control.” The S850 paver is averaging 0.127mm deviation from theoretical zero for line and grade. This is important as any panels that do not meet the specification must be removed and replaced.
Stringless paving is also increasing paving production by saving time and money on surveying, stake driving and string set-up. It is allowing the contractor to be more efficient and to save time on the job.
Paving work began in July 2014, and Acura had to complete 70% of the paving by May 2015 to meet the contract’s end-date of October 2015. The runway and parallel high-speed taxiway are each 2,286m long, while the four taxiways connecting these two parallel structures measure 152m long. This is the equivalent of more than 5.1km of paving.
The special FAA P-501 spec concrete is produced by a 459m3/hour double-drum concrete plant, located at a far edge of the project site. Even though it’s a short route for the 15 haul trucks, the mix is still a challenge. Carlos Lopez, project manager for Acura said, “The P-501 spec concrete with Type F fly ash loses 1% air per minute for the first 30 minutes, and it loses 0.5in (12.7mm) slump every 15 minutes for the first 45 minutes.”
Acura must meet a 12.7–38.1mm slump with this design and achieve the 5-7% air void content. “We start with a higher air content at the plant and pave the concrete at the lower end of the slump limit,” explained DiGioia. Lopez added, “The paver is heavy duty and powerful, which allows us to pave at the low end of the slump at the specified depth.”
Trucks discharge concrete on to 1.625m wide, roll-in/roll-out conveyor of the PS1200. The placer spreader is equipped with a342 Topcon system to control its steering and offers heavy-duty tractor frame construction and 2.1m telescoping ability, so crews can quickly adjust to the job’s 5.5-6.1m paving widths. Its rapid belt relocation system for the conveyor allows concrete to be loaded from either the left or right side of the machine.
Following closely behind the placer spreader, the Guntert & Zimmerman S850 provides final form and consolidation to the concrete. Acura equipped its paver with Guntert & Zimmerman’s patented TeleEnds Telescopic Paving Kit End Sections to help shorten the time to make paving width adjustments, so crews could meet the 6,116m3/week placement goal during the peak paving season. These hydraulically adjustable segments give Acura’s crews a total of 1.8m quick-width-change capabilities.
TeleEnds allow workers to make width changes without a crane, using only 1-2 people. Spacers – in 26.2- 304.8-mm segments with shim spacers for smaller width adjustments – come in front, bottom (pan) and back sections, so one person can easily install them.
Beyond saving time and providing accuracy while surveying, stringless paving with the S850 saves time and increases production while paving. “We don’t have the string on either side of the paver to impede the paving process,” commented Lopez. “It makes it much easier and faster for concrete trucks to deliver their loads.”
With efficiencies gained through the use of the latest stringless and dowel bar inserter technologies available, Acura was able to complete the work well within schedule. The firm paved 114,683m3 of concrete in all, while achieving quality results.
All around the world, airports are being expanded and upgraded, both to cope with massive increases in passenger numbers and also to handle larger aircraft. Runways have to be rebuilt with stronger structures and surfaces to handle greater air traffic volumes as well as increased loads from larger aeroplanes. Building airport runways, however, poses many challenges for construction crews. Paving quality has to be extremely high so as to maximise safety, while time schedules can be very strict, with only short possession time available and tough penalties for late working.
The Chicago Department of Aviation is managing one of the largest construction projects in the country at O’Hare, one of the world’s busiest airports. The O’Hare Modernisation Program (OMP) promises to upgrade the airport’s outdated layout into modern parallel runways to reduce flight delays in all weather conditions.
When the project is complete, O’Hare will have eight runways, including six east-west parallel runways and two crosswinds runways. A partnership between Turner Construction, Acura, and Lindahl Brothers is completing runway and taxiways work, a south air traffic control tower and several other enabling projects. The bulk of the concrete paving is being completed by Acura.
The firm is an experienced concrete paving contractor but this is its first airport job. The specifications are tighter and the concrete mix is more challenging than the crews are used to. Additionally, this job requires the use of a dowel bar inserter and stringless paving job, both of which the firm is using for the first time.
The firm is confident it can complete the work efficiently as it has an experienced crew and is using a machine in which it has confidence, a
The CDBI system is helping achieve high productivity as it eliminates the time and expense of placing dowel baskets in front of the paver. It can be quickly fitted on to the rear of the paver and accurately inserts the epoxy-coated dowel bars along the transverse contraction joint.
Dowel bars are inserted at 457mm centres every 6.1m of paving. The dowels have to be precisely inserted into the concrete vertically and horizontally according to the firm, saving time and materials.
The firm is also the first in Illinois to use stringless paving and the dowel bar inserter at the same time but has managed this successfully on its first attempt. The company has also managed to meet the stringent requirements of a high-profile airport paving project. It has installed about 40,000 dowels using the CDBI and started at 97% passing during the first couple of pours. After that, it has achieved nearly 100%, even with the very strict specifications and acceptance criteria, maintaining quality, while delivering the final product within the necessary timeframe.
Acura equipped its Guntert & Zimmerman PS1200 placer spreader and S850 slipform paver with Guntert & Zimmerman’s NoLine Stringless Paving Preparation Kit. The set-up uses GPS technology from Leica Geosystems for grade and elevation control. This connects directly into the paving equipment’s controls, and the kit provides telescopic mounts for two total station prisms.
According to Acura president, Nico DiGioia, “The accuracy of Guntert & Zimmerman’s hydraulic system and compatibility with the Total Station System is delivering some phenomenal results for grade and line control.” The S850 paver is averaging 0.127mm deviation from theoretical zero for line and grade. This is important as any panels that do not meet the specification must be removed and replaced.
Stringless paving is also increasing paving production by saving time and money on surveying, stake driving and string set-up. It is allowing the contractor to be more efficient and to save time on the job.
Paving work began in July 2014, and Acura had to complete 70% of the paving by May 2015 to meet the contract’s end-date of October 2015. The runway and parallel high-speed taxiway are each 2,286m long, while the four taxiways connecting these two parallel structures measure 152m long. This is the equivalent of more than 5.1km of paving.
The special FAA P-501 spec concrete is produced by a 459m3/hour double-drum concrete plant, located at a far edge of the project site. Even though it’s a short route for the 15 haul trucks, the mix is still a challenge. Carlos Lopez, project manager for Acura said, “The P-501 spec concrete with Type F fly ash loses 1% air per minute for the first 30 minutes, and it loses 0.5in (12.7mm) slump every 15 minutes for the first 45 minutes.”
Acura must meet a 12.7–38.1mm slump with this design and achieve the 5-7% air void content. “We start with a higher air content at the plant and pave the concrete at the lower end of the slump limit,” explained DiGioia. Lopez added, “The paver is heavy duty and powerful, which allows us to pave at the low end of the slump at the specified depth.”
Trucks discharge concrete on to 1.625m wide, roll-in/roll-out conveyor of the PS1200. The placer spreader is equipped with a
Following closely behind the placer spreader, the Guntert & Zimmerman S850 provides final form and consolidation to the concrete. Acura equipped its paver with Guntert & Zimmerman’s patented TeleEnds Telescopic Paving Kit End Sections to help shorten the time to make paving width adjustments, so crews could meet the 6,116m3/week placement goal during the peak paving season. These hydraulically adjustable segments give Acura’s crews a total of 1.8m quick-width-change capabilities.
TeleEnds allow workers to make width changes without a crane, using only 1-2 people. Spacers – in 26.2- 304.8-mm segments with shim spacers for smaller width adjustments – come in front, bottom (pan) and back sections, so one person can easily install them.
Beyond saving time and providing accuracy while surveying, stringless paving with the S850 saves time and increases production while paving. “We don’t have the string on either side of the paver to impede the paving process,” commented Lopez. “It makes it much easier and faster for concrete trucks to deliver their loads.”
With efficiencies gained through the use of the latest stringless and dowel bar inserter technologies available, Acura was able to complete the work well within schedule. The firm paved 114,683m3 of concrete in all, while achieving quality results.