The Fort Lauderdale-Hollywood International Airport in Broward County, Florida, was suffering departure delays on every single flight. The existing 9R-27L runway was too short at 1615m in length, affecting capacity at the airport. To deal with the issue, the Broward County Board of County Commissioners created a plan to extend the southern runway to 2438m to accommodate larger commercial aircraft.
The project was not simple however and could not be achieved by tearing out the
existing runway and buil
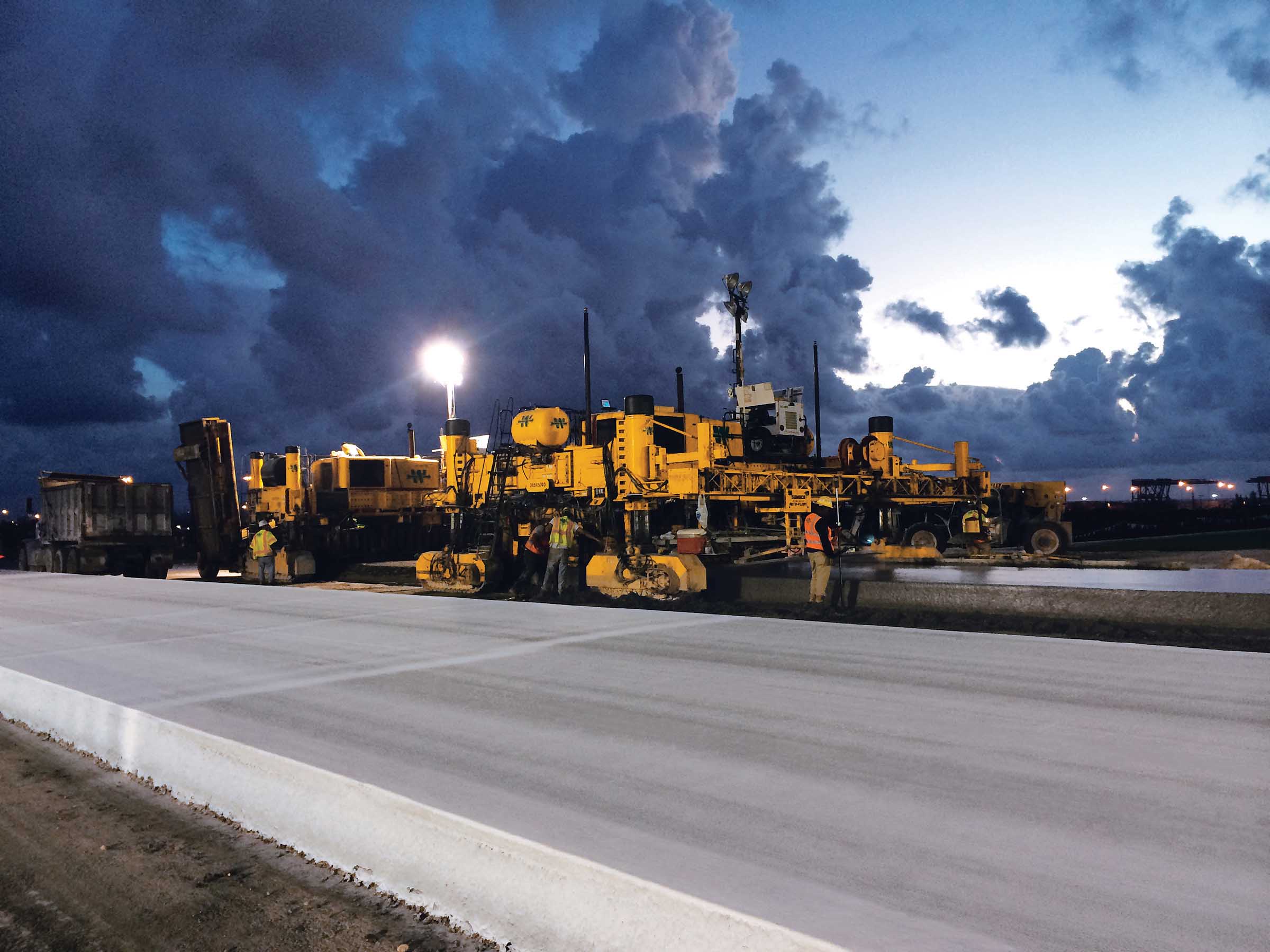
The airport paving job was carried out despite challenging weather conditions, with stringless technology playing a key role in optimising efficiency
The Fort Lauderdale-Hollywood International Airport in Broward County, Florida, was suffering departure delays on every single flight. The existing 9R-27L runway was too short at 1615m in length, affecting capacity at the airport. To deal with the issue, the Broward County Board of County Commissioners created a plan to extend the southern runway to 2438m to accommodate larger commercial aircraft.
The project was not simple however and could not be achieved by tearing out the
existing runway and building a new one in its place. To create enough area for the longer runway, a new 18.3m-high man-made embankment had to be built. In addition, to the west of the new embankment, concrete bridge structures had to be built to support the runway extension and adjacent taxiway as it crossed over US Highway 1 and the Florida East Coast Railroad line.
4760 Archer Western Construction, based in Tampa, Florida, won the bid for the grade work, sub-base preparation, and concrete slipforming of the airport’s new runway and taxiway. Due to delays on the project, the firm had to carry out its portion of the work while the other major contractors finished the embankment and bridge structures.
The paver selected for the project was a218 GOMACO four-track GHP-2800 with Leica Geosystems 3D machine guidance. The GHP-2800’s jobsite mobility, along with it being a stringless project, would allow the firm to pave when and where needed amidst the crowded project site.
For the sub-base, the firm used a GOMACO 9500 placer. On the concrete paving it used a PS-2600 placer/spreader with a GHP-2800 paver setup at 15.7m wide, followed by a T/C-600 texture/cure machine. The firm ran stringless with a Leica Geosystems setup. Then, for its hand pours, used the 9500 and RTP-500 placers.
As grade work was completed, sub-base could be placed. Archer Western used the GOMACO 9500 to place the 152mm thick cement-treated base (CTB). Originally, the plan was to pave the new 2438m-long concrete runway in 610m sections. Project phasing did not allow for that so paving runs were shortened to 457m in 10-hour shifts.
The concrete for the project was mixed on site in the company’s portable batch plant. Requirements called for a standard P-501concrete, 650 flex airfield mix. The concrete had fly ash added and used manufactured sand instead of natural sand, while slump averaged 19mm.
The trucks unloaded onto the large conveyor belt mounted on the left side of the GOMACO PS-2600 placer/spreader. Dowel baskets were placed every 6.1m while the dowels were placed on 457mm centres.
The GOMACO four-track GHP-2800 slipformed the new runway in 5.7m-wide by 419mm-thick paving passes with a standard crown down the middle. At that width and thickness, each 305mm of new runway lane required nearly 0.8m3 of concrete.
The paver was equipped with a Leica Geosystems 3D guidance system, eliminating stringline from the site. Since most of Archer Western’s paving is done at night to accommodate the subtropical heat of southern Florida, the 3D system eliminated the risk of crew members tripping over a stringline.
To make work easier, the firm said it learned to do a dry run at the beginning of each shift, backing up the paver 18m or so prior to the concrete coming into place to make sure the machine was at the right elevation.
The weather also proved challenging as rain showers would hit every night and the Archer Western crew had to be ready to cover the fresh concrete quickly.
Slipforming the runway was divided into eight paving lanes. Smoothness specifications using the two-tenths blanking band and edge slump requirements had to be met on all areas of the new concrete pavement. The firm was allowed a 4.9m straightedge and the cut-off for payment was 110mm/km but the company kept well within tolerance at around 32mm/km.
A GOMACO T/C-600 texture/cure followed the paver applying a burlap drag finish and a white spray cure. Transverse joints were saw cut into the new runway every 6.1m.
With the project complete, the new runway’s designation changed from 9R-27L to 10R-28L and the Fort Lauderdale-Hollywood International Airport is operating more efficiently with fewer delays.
The project was not simple however and could not be achieved by tearing out the
existing runway and building a new one in its place. To create enough area for the longer runway, a new 18.3m-high man-made embankment had to be built. In addition, to the west of the new embankment, concrete bridge structures had to be built to support the runway extension and adjacent taxiway as it crossed over US Highway 1 and the Florida East Coast Railroad line.
The paver selected for the project was a
For the sub-base, the firm used a GOMACO 9500 placer. On the concrete paving it used a PS-2600 placer/spreader with a GHP-2800 paver setup at 15.7m wide, followed by a T/C-600 texture/cure machine. The firm ran stringless with a Leica Geosystems setup. Then, for its hand pours, used the 9500 and RTP-500 placers.
As grade work was completed, sub-base could be placed. Archer Western used the GOMACO 9500 to place the 152mm thick cement-treated base (CTB). Originally, the plan was to pave the new 2438m-long concrete runway in 610m sections. Project phasing did not allow for that so paving runs were shortened to 457m in 10-hour shifts.
The concrete for the project was mixed on site in the company’s portable batch plant. Requirements called for a standard P-501concrete, 650 flex airfield mix. The concrete had fly ash added and used manufactured sand instead of natural sand, while slump averaged 19mm.
The trucks unloaded onto the large conveyor belt mounted on the left side of the GOMACO PS-2600 placer/spreader. Dowel baskets were placed every 6.1m while the dowels were placed on 457mm centres.
The GOMACO four-track GHP-2800 slipformed the new runway in 5.7m-wide by 419mm-thick paving passes with a standard crown down the middle. At that width and thickness, each 305mm of new runway lane required nearly 0.8m3 of concrete.
The paver was equipped with a Leica Geosystems 3D guidance system, eliminating stringline from the site. Since most of Archer Western’s paving is done at night to accommodate the subtropical heat of southern Florida, the 3D system eliminated the risk of crew members tripping over a stringline.
To make work easier, the firm said it learned to do a dry run at the beginning of each shift, backing up the paver 18m or so prior to the concrete coming into place to make sure the machine was at the right elevation.
The weather also proved challenging as rain showers would hit every night and the Archer Western crew had to be ready to cover the fresh concrete quickly.
Slipforming the runway was divided into eight paving lanes. Smoothness specifications using the two-tenths blanking band and edge slump requirements had to be met on all areas of the new concrete pavement. The firm was allowed a 4.9m straightedge and the cut-off for payment was 110mm/km but the company kept well within tolerance at around 32mm/km.
A GOMACO T/C-600 texture/cure followed the paver applying a burlap drag finish and a white spray cure. Transverse joints were saw cut into the new runway every 6.1m.
With the project complete, the new runway’s designation changed from 9R-27L to 10R-28L and the Fort Lauderdale-Hollywood International Airport is operating more efficiently with fewer delays.