The country of Qatar, located on the Persian Gulf, developed a master plan to build a new replacement airport in its capital city of Doha, the New Doha International Airport, in 2003. Its goal is to have a facility capable of handling 50 million passengers; two million tons (1.8million tonnes) of cargo, and 320,000 aircraft landings and take-offs each year by 2015. Phase one of the aggressive project is scheduled for completion early next year. The Tayseeir Contractors Company Joint Venture, including Conso
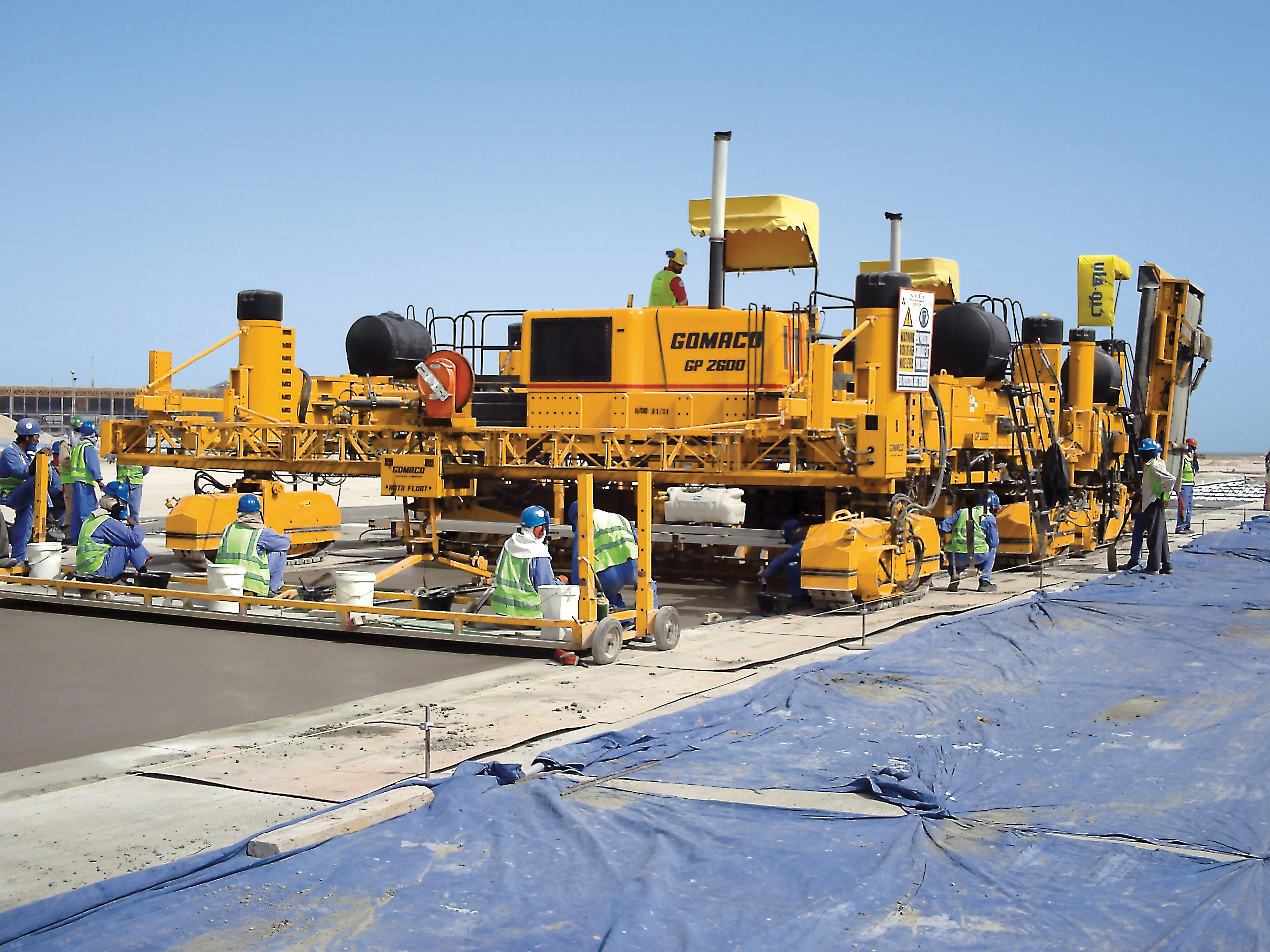
The GOMACO GP-2600 with Auto-Float paved at various widths and thicknesses
A GOMACO paving train overcame challenges on the New Doha International Airport
The country of Qatar, located on the Persian Gulf, developed a master plan to build a new replacement airport in its capital city of Doha, the New Doha International Airport, in 2003.Its goal is to have a facility capable of handling 50 million passengers; two million tons (1.8million tonnes) of cargo, and 320,000 aircraft landings and take-offs each year by 2015.
Phase one of the aggressive project is scheduled for completion early next year.
The Tayseeir Contractors Company Joint Venture, including Consolidated Contractors International Company (CCIC), is one of the many contractors on site finishing its share of the first phase. CCI¬C has been at work slipforming approximately 100,000m³ of new concrete aprons on the airport with its new
Challenges abounded on the project, including an airport design plan which did not consider slipform paving; daytime summer temperatures averaging 40ºC; a crew new to slipforming, and varying paving widths and depths, all while working around hundreds of other contractors trying to complete their portion of the project.
The challenges caused CCIC and its concrete paving manager Kevin Robinson to look at the project differently as they worked to maximise the utilisation of the GOMACO paving train.
“The project was just an obstacle course with us having to go over or around lamp post bases, fire hydrants, fuel pits, electrical pits and all the other different types of pits,” says Robinson.
“We really had to be on top of our game and keep everything carefully coordinated and planned so we could put concrete on the ground every day with the GP-2600. That was our goal, to always get concrete on the ground. We were able to achieve that goal, even if we only paved 200m³ that day.”
CCIC slipformed the new airport’s aprons on a 100mm thick asphalt base applied over a rock sub-base. The Portland Cement Concrete (PCC), without air entrainment, was produced on site by three different mobile batching plants with the capacity to produce 100-110m³ of concrete per hour. Slump averaged between 25-35mm.
Concrete was delivered to the paving site by dump trucks carrying 8m³ loads.
The trucks dumped their load onto the belt of the PS-2600 placer/spreader working in front of the GP-2600 paver or, when project logistics did not allow enough room for the PS-2600, concrete was dumped directly on the grade.
The GP-2600 paved a maximum of 6m wide on the project and up to 550mm deep. Baskets were placed on grade every 6m.
“There was a grated water trench just inside the aprons that varied in size in different areas, so we had to alter the width of the paving equipment nine different times to suit the design,” says Robinson.
“On any other project we’d be able to pave 2,000m³ per day, but this one was just so difficult. The most we ever accomplished was 856m³. It’s all due to the difficult areas of design, which would have up to 20 headers and footers per shift, as we paved around the various obstacles.”
A T/C-400 texture/cure machine followed the paver applying a burlap drag finish, transverse tine and white spray cure. Contraction joints were sawed into the new slab every 6m and expansion joints were placed every 75m.
“When we first started, the paving crew was very inexperienced, but now I would rate them as good as anyone I?know,” says Robinson. “The GP-2600 performed very well through all of it and the crew learned quickly how to work on and around the GOMACO equipment. We met all of the tolerances specified by the engineers and the paver laid the concrete as flat as you can get. I’m really proud of the concrete we produced in such challenging conditions.”
CCIC is currently finishing its portion of the concrete pavement at the New Doha International Airport.
Some hand pours and a few other details are all that is left to complete.
The GOMACO paving train and Robinson have already moved onto another project, Muscat International Airport in Muscat, Oman, where the GP-2600 is slipforming approximately 140,000m³ of stands and aprons as part of the airport’s expansion project.