Wirtgen's new 120F milling machine has been developed from the 100F launched late last year. The two machines use the same basic chassis but the 120F is a more powerful mill that can handle wider cuts of up to 1.2m. Jeff Wylie is product manager for Wirtgen's milling machines in the US and explained that the machine comes with several new features. Power comes from a Cummins QSC diesel and this engine is rubber-mounted, to reduce vibration and noise. A variable speed cooling fan is fitted that senses engine
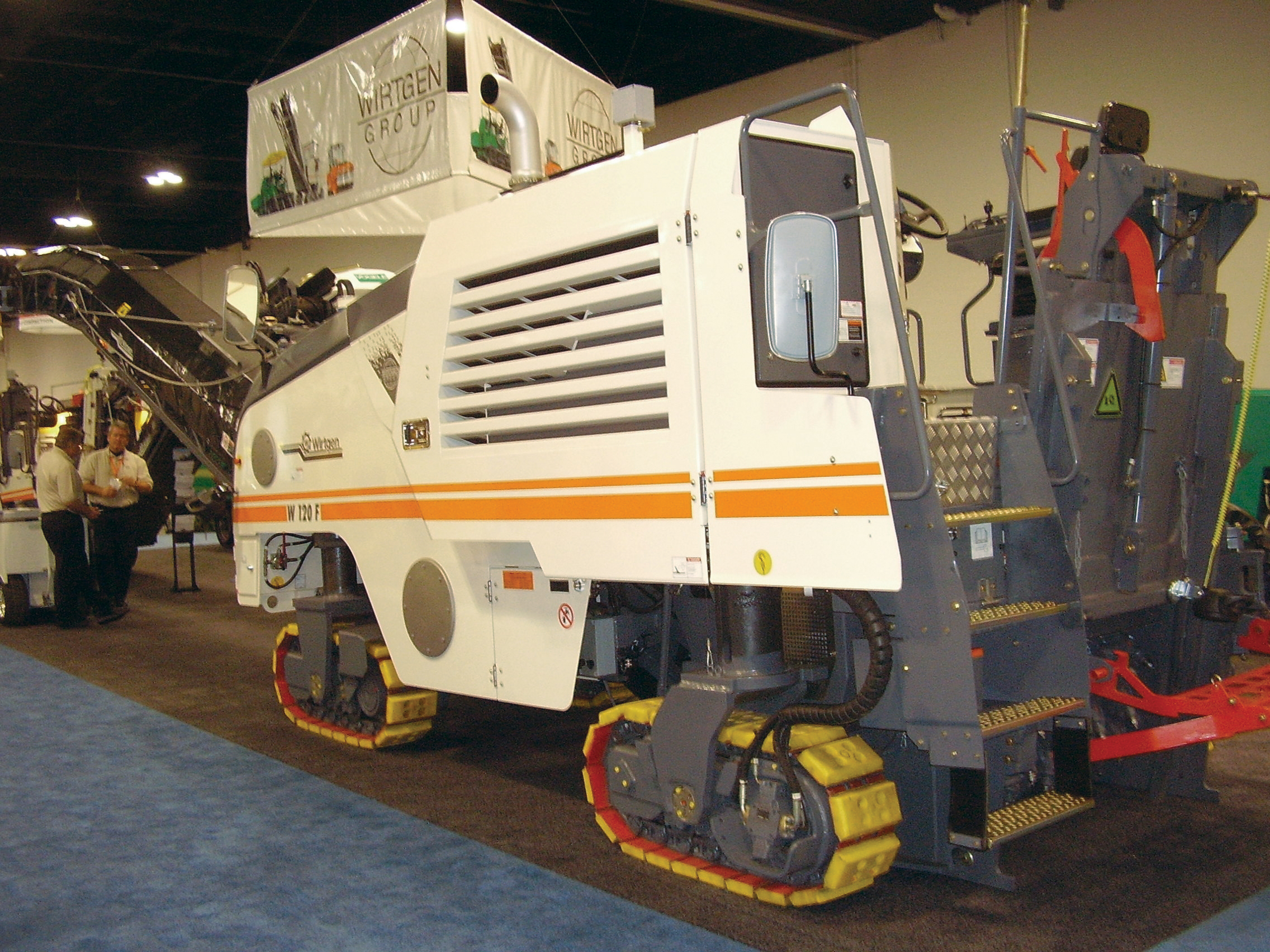
The new Wirtgen 120F offers more power and productivity than the model it replaces
Wirtgen's new 120F milling machine has been developed from the 100F launched late last year.
The two machines use the same basic chassis but the 120F is a more powerful mill that can handle wider cuts of up to 1.2m. Jeff Wylie is product manager forThe machine is able to back up with the cutter running and Wylie said that this is an important development that will boost output. He added, "It's a first for Wirtgen."
The machine features a walk¬through operator station with the controls mounted on the left hand side. A sideshift feature on the seat allows better visibility of the cutting process, while the computer display comes with both US standard and metric units. Wire rope controls are standard for the machine, although other sensor systems can be used too.
Wylie reckons the machine will be around 20% more productive than Wirtgen's previous model in this class. Several features will increase output and reduce maintenance time. Fuel and water capacity has been increased, while the track tensioners are hydraulic and operate automatically. The position of the drum has been moved slightly in comparison with the earlier model and Wylie explained that this will provide a better flow through of material into the conveyor, which also comes with an automatic boost system. In addition, a folding conveyor is offered as an option for customers wanting to minimise transport dimensions.