Manufacturers are making advances in stabiliser/reclaimers and milling machines - Mike Woof reports. The market for milling equipment is a competitive one, with a range of companies from around the globe now offering machines for this segment: BOMAG, Caterpillar, Dynapac, Roadtec, Volvo CE and Wirtgen. In recent years a number of Chinese firms have entered this segment and determining the number of machines these companies manufacture is difficult, although most of their units are sold in China. But interna
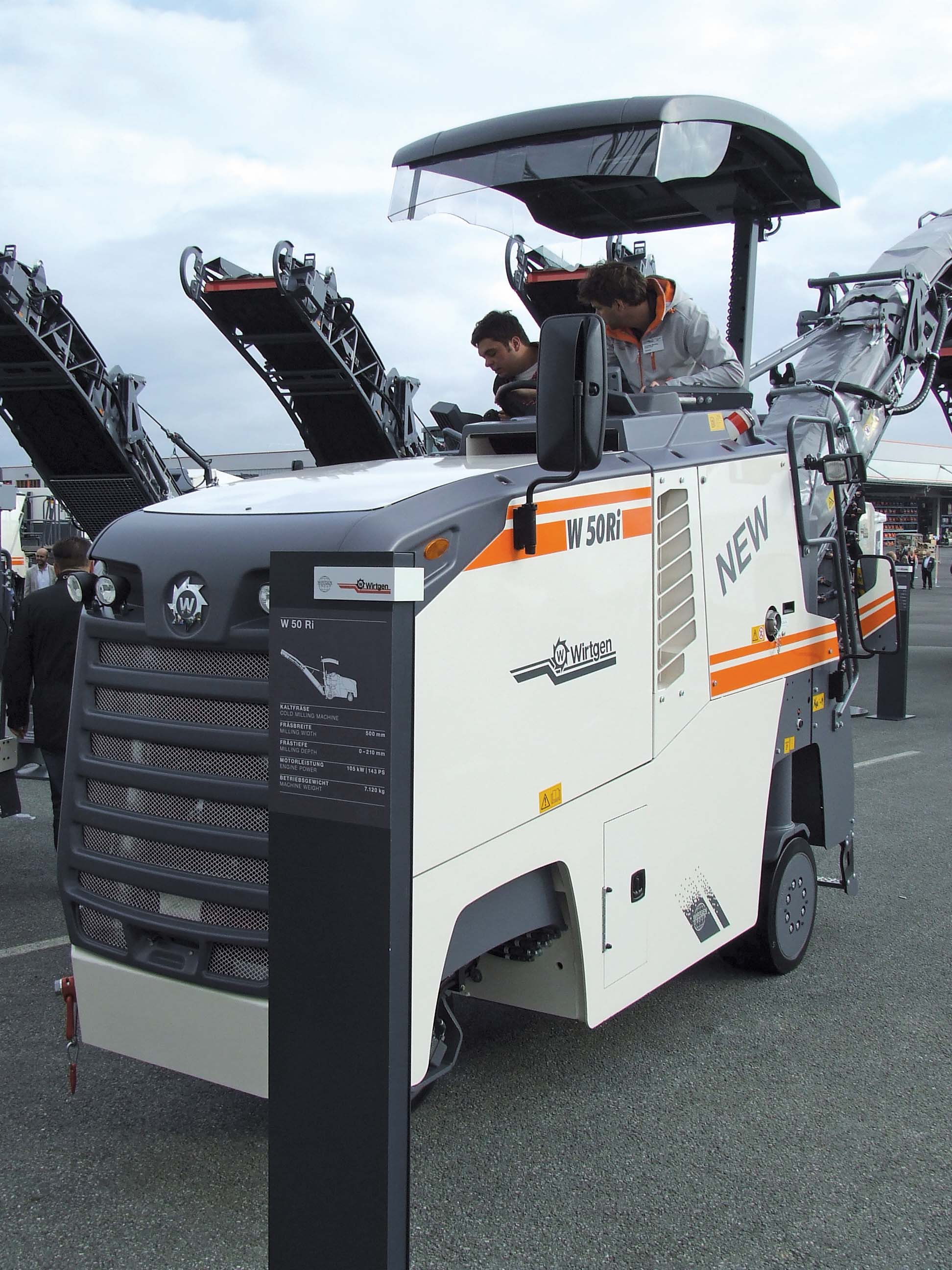
The new W 50 Ri from Wirtgen is the firm’s versatile 0.5m milling machine
RSSManufacturers are making advances in stabiliser/reclaimers and milling machines - Mike Woof reports
The market for milling equipment is a competitive one, with a range of companies from around the globe now offering machines for this segment:172 BOMAG, 178 Caterpillar, 206 Dynapac, 1252 Roadtec, 359 Volvo CE and 2395 Wirtgen. In recent years a number of Chinese firms have entered this segment and determining the number of machines these companies manufacture is difficult, although most of their units are sold in China. But internationally at least, Wirtgen remains market leader.
BOMAG is keen to develop its share of the milling machine sector, having introduced first a 500mm machine followed more recently by a 1m class machine. The latest introduction from the firm is a 2m class machine, the BM2000/75, which tips the scales at 36tonnes and is powered by an emissions compliant diesel delivering 560kW.
Developed at the firm’s Boppard facility, the machine can be used for milling widths of 2m, and in some instance 2.2m. This suits it to jobs on major highways as well as airport runway construction, where productivity and low dust emissions are crucial to minimising the impact on air traffic. The machine is offered with the firm’s Powerdrum, standard drum and fine milling drum options and can be configured to handle an array of different tasks. Drum speed and travel speed can be adjusted to suit the needs of the application and the conditions, so as to optimise operation. The design of the drum and positioning of the tool holders and cutting tools is said to further optimise operation by delivering maximum cutting efficiency to the surface being cut. The firm claims that its BMS 15 exchange holder system ensures the tools provide optimum cutting efficiency as well as low wear and long life. Worn tools can also be replaced quickly by tapping them out from behind, reducing downtime and boosting overall output.
An integrated dust extraction system is said to ensure dust emissions are minimised, while the system is also maintenance-free. Other features include long tracks that help maximise stability and traction, comfortable and adjustable seating and a vibration-damped operator platform. In addition the machine is said to be easy to maintain, with good access to service points while it also has a hydraulically folding conveyor belt, for ease of transport.
Wirtgen continues to develop its product range as the firm is keen to maintain its strong position having faced renewed competition from its rivals, particularly in the segment for small milling machines. As a result Wirtgen is now offering a new generation of small milling machines, as well as a new levelling system and new milling drums for small milling machines.
Better performance and ease of operation are two of the key benefits claimed for the new compact planers. For the hotly contested 500mm width milling machine class, Wirtgen is now offering the W 50 Ri and W 60 Ri models. Also new to the market from Wirtgen are the 1m class W 100 CFi, as well as the 1.2m class W 120 CFi and 1.3m class W 130 CFi.
The W 50 Ri weighs in at 7.1tonnes, with power from an emissions compliant diesel delivering 105kW. The machine is said to be economical to run due to fuel-saving features, as well as being efficient and productive and able to cut to depths of 210mm. Versatile and productive, the wheel-mounted machine has been designed for use in small road repair jobs and can operate in tight working areas.
Wirtgen’s new compact W 50 Ri and W 60 Ri mills now share the same standardised operating and control concept. This is said to offer a range of automatic functions that make operation easier and speed up work being carried out. The design also means that operators can move from one model to another and find the same type of controls, making them easier to drive.
Other novel features include intuitive operation due to easier driving and more precise steering, as well as versatility when carrying out milling and loading functions. This more straightforward operation allows work to be carried out more quickly, as well as more precisely. An important tool is the new LEVEL PRO PLUS levelling system, which is said to ensure operations are carried out more precisely. Meanwhile the firm’s new HT08 milling drums for planers in the 500mm class are also said to offer more productive cutting and longer working life.
The company’s LEVEL PRO PLUS levelling system is now integrated into the machine management system, making it easier to achieve fine milling results, with a colour display for the operator that can be read even in bright sunlight.
In addition the new drum design from Wirtgen for the 500mm class is said to extend wear life by up to 75%, compared with earlier generation types.
The W 100 CFi, W 120 CFi and W 130 CFi are front loading models that are designed for versatility and high productivity. The W 100 CFi delivers high output and a spokesperson for the firm said, “It’s the most powerful machine in its class and milling output has been increased by 15%.”
Power comes from a Tier 4 Final/Stage IV compliant diesel rated at 261kW and which is also economical on fuel, while it features a narrow chassis that is said to help optimise visibility. The operator platform can also be moved hydraulically 200mm to the side to provide a better view of the milling drum and the front right-hand crawler. Meanwhile a CCTV system provides visibility of the left-hand milled edge and material discharge.
As with the smaller machines, the LEVEL PRO PLUS system ensures optimum milling quality. The operator benefits from a high visibility, colour screen that displays all relevant working parameters. The machine is said to be easy to operate and manoeuvre in tight spaces as well, due to a mechanism that allows the right-hand rear track to be swivelled.
The machine also has a large conveyor offering a slewing angle of 60° to the left or right, which is of use when working on curves or in constricted areas. The firm also says that for more precise loading, the machine operator can slew the conveyor at two different speeds.
And the firm is also extending the capabilities of its reclaimer/stabilisers, as the proven WR 240/WR 240i and WR 250 machines are now available with an optional integrated S-Pack spreader module. This feature is important for the segment as the spreader pack means that binding agent can be spread without generating a dust cloud behind the machine. Fitting this extra system to the machines helps boost their capabilities, while helping improve cost-efficiency for contractors.
The machines are used in a wide variety of applications, including the construction of highways, roads in residential areas and to stabilise areas for industrial estates. The units can help improve difficult terrain, with the new features helping reduce emissions while improving safety. When fitted with the S-Pack, the WR machine can spread the binding agent directly in front of the milling and mixing rotor. This mixes the binding agent into the soil efficiently, while the closed drum housing and the double curtain of rubber matting prevents the formation of dust clouds and also ensures effective spreading inside the milled portion. This feature means that binding agent can be spread even on windy days, without risk of the material subsequently being blown or washed away on days when the weather is poor.
The feature also boosts safety as it allows materials such as cement or lime to be spread safely and precisely and processed without emissions. This is important for areas such as industrial estates, near airports or on highways, where materials drifting could pose risks for traffic.
These powerful reclaimer/stabilisers are generally used on rough ground to improve soils with insufficient bearing capacity. The integrated spreader module broadens their abilities, reducing the numbers of machines needed onsite and also transport costs. The machines feature sophisticated sensors and metering systems to ensure the quantities of binding agents are closely controlled. A two-part transverse auger is continuously supplied with binding agent by a conveyor and this ensures that the material is uniformly applied over the 2.4m working width. In addition, spreading width can be incrementally adjusted to 1.6m and 0.8m. Depending on the application concerned, the spreader can deliver between 1.5 and 40 kg/m².
The level in the 5.5m3 capacity binding agent tank is monitored by sensors and indicated on the control display, while the spreading quantity is calibrated through the display as the bulk density of the binding agent is entered.
Meanwhile2490 XCMG is aiming its new XM1003S milling machine at the 1m market, although this is restricted to emergent territories for the moment. The machine offers a milling depth of 300mm, while proportion-controlled hydrostatic drive to all four wheels is said to provide good traction. The machine has one speed range for moving between jobsites and three speed ranges for working applications. The combination of the modulated hydrostatic drive and the steering system with its maximum front axle steering angle of 70° is said to allow good manoeuvrability on tight working sites. Other features include a welded frame that combines counterweight, fuel tank and operator station for a compact overall design. Adjustment of steering wheel and seat are offered and are said to make the machine comfortable to use while the LCD operating panel is designed to make the machine easy to use. RSS
The market for milling equipment is a competitive one, with a range of companies from around the globe now offering machines for this segment:
BOMAG is keen to develop its share of the milling machine sector, having introduced first a 500mm machine followed more recently by a 1m class machine. The latest introduction from the firm is a 2m class machine, the BM2000/75, which tips the scales at 36tonnes and is powered by an emissions compliant diesel delivering 560kW.
Developed at the firm’s Boppard facility, the machine can be used for milling widths of 2m, and in some instance 2.2m. This suits it to jobs on major highways as well as airport runway construction, where productivity and low dust emissions are crucial to minimising the impact on air traffic. The machine is offered with the firm’s Powerdrum, standard drum and fine milling drum options and can be configured to handle an array of different tasks. Drum speed and travel speed can be adjusted to suit the needs of the application and the conditions, so as to optimise operation. The design of the drum and positioning of the tool holders and cutting tools is said to further optimise operation by delivering maximum cutting efficiency to the surface being cut. The firm claims that its BMS 15 exchange holder system ensures the tools provide optimum cutting efficiency as well as low wear and long life. Worn tools can also be replaced quickly by tapping them out from behind, reducing downtime and boosting overall output.
An integrated dust extraction system is said to ensure dust emissions are minimised, while the system is also maintenance-free. Other features include long tracks that help maximise stability and traction, comfortable and adjustable seating and a vibration-damped operator platform. In addition the machine is said to be easy to maintain, with good access to service points while it also has a hydraulically folding conveyor belt, for ease of transport.
Wirtgen continues to develop its product range as the firm is keen to maintain its strong position having faced renewed competition from its rivals, particularly in the segment for small milling machines. As a result Wirtgen is now offering a new generation of small milling machines, as well as a new levelling system and new milling drums for small milling machines.
Better performance and ease of operation are two of the key benefits claimed for the new compact planers. For the hotly contested 500mm width milling machine class, Wirtgen is now offering the W 50 Ri and W 60 Ri models. Also new to the market from Wirtgen are the 1m class W 100 CFi, as well as the 1.2m class W 120 CFi and 1.3m class W 130 CFi.
The W 50 Ri weighs in at 7.1tonnes, with power from an emissions compliant diesel delivering 105kW. The machine is said to be economical to run due to fuel-saving features, as well as being efficient and productive and able to cut to depths of 210mm. Versatile and productive, the wheel-mounted machine has been designed for use in small road repair jobs and can operate in tight working areas.
Wirtgen’s new compact W 50 Ri and W 60 Ri mills now share the same standardised operating and control concept. This is said to offer a range of automatic functions that make operation easier and speed up work being carried out. The design also means that operators can move from one model to another and find the same type of controls, making them easier to drive.
Other novel features include intuitive operation due to easier driving and more precise steering, as well as versatility when carrying out milling and loading functions. This more straightforward operation allows work to be carried out more quickly, as well as more precisely. An important tool is the new LEVEL PRO PLUS levelling system, which is said to ensure operations are carried out more precisely. Meanwhile the firm’s new HT08 milling drums for planers in the 500mm class are also said to offer more productive cutting and longer working life.
The company’s LEVEL PRO PLUS levelling system is now integrated into the machine management system, making it easier to achieve fine milling results, with a colour display for the operator that can be read even in bright sunlight.
In addition the new drum design from Wirtgen for the 500mm class is said to extend wear life by up to 75%, compared with earlier generation types.
The W 100 CFi, W 120 CFi and W 130 CFi are front loading models that are designed for versatility and high productivity. The W 100 CFi delivers high output and a spokesperson for the firm said, “It’s the most powerful machine in its class and milling output has been increased by 15%.”
Power comes from a Tier 4 Final/Stage IV compliant diesel rated at 261kW and which is also economical on fuel, while it features a narrow chassis that is said to help optimise visibility. The operator platform can also be moved hydraulically 200mm to the side to provide a better view of the milling drum and the front right-hand crawler. Meanwhile a CCTV system provides visibility of the left-hand milled edge and material discharge.
As with the smaller machines, the LEVEL PRO PLUS system ensures optimum milling quality. The operator benefits from a high visibility, colour screen that displays all relevant working parameters. The machine is said to be easy to operate and manoeuvre in tight spaces as well, due to a mechanism that allows the right-hand rear track to be swivelled.
The machine also has a large conveyor offering a slewing angle of 60° to the left or right, which is of use when working on curves or in constricted areas. The firm also says that for more precise loading, the machine operator can slew the conveyor at two different speeds.
And the firm is also extending the capabilities of its reclaimer/stabilisers, as the proven WR 240/WR 240i and WR 250 machines are now available with an optional integrated S-Pack spreader module. This feature is important for the segment as the spreader pack means that binding agent can be spread without generating a dust cloud behind the machine. Fitting this extra system to the machines helps boost their capabilities, while helping improve cost-efficiency for contractors.
The machines are used in a wide variety of applications, including the construction of highways, roads in residential areas and to stabilise areas for industrial estates. The units can help improve difficult terrain, with the new features helping reduce emissions while improving safety. When fitted with the S-Pack, the WR machine can spread the binding agent directly in front of the milling and mixing rotor. This mixes the binding agent into the soil efficiently, while the closed drum housing and the double curtain of rubber matting prevents the formation of dust clouds and also ensures effective spreading inside the milled portion. This feature means that binding agent can be spread even on windy days, without risk of the material subsequently being blown or washed away on days when the weather is poor.
The feature also boosts safety as it allows materials such as cement or lime to be spread safely and precisely and processed without emissions. This is important for areas such as industrial estates, near airports or on highways, where materials drifting could pose risks for traffic.
These powerful reclaimer/stabilisers are generally used on rough ground to improve soils with insufficient bearing capacity. The integrated spreader module broadens their abilities, reducing the numbers of machines needed onsite and also transport costs. The machines feature sophisticated sensors and metering systems to ensure the quantities of binding agents are closely controlled. A two-part transverse auger is continuously supplied with binding agent by a conveyor and this ensures that the material is uniformly applied over the 2.4m working width. In addition, spreading width can be incrementally adjusted to 1.6m and 0.8m. Depending on the application concerned, the spreader can deliver between 1.5 and 40 kg/m².
The level in the 5.5m3 capacity binding agent tank is monitored by sensors and indicated on the control display, while the spreading quantity is calibrated through the display as the bulk density of the binding agent is entered.
Meanwhile