Modern technology is making testing more efficient and reliable, increasing productivity and reducing costs, as Patrick Smith reports A few years ago, visual inspection of an 18-year-old bridge by ARRB in Australia identified considerable cracking in the precast, prestressed deck planks as well as in the cast in situ deck overlay. Laboratory examination indicated that the deck planks and the deck overlay were suffering from a strong case of alkali-aggregate reaction (AAR). Testing of concrete cores drilled
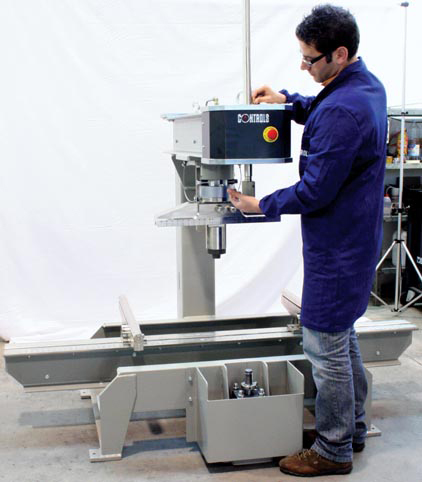
Controls' Frame Model 50-C1601/FR fitted with lower long bearers and upper pad for flexure test on kerbs to EN 1338
Modern technology is making testing more efficient and reliable, increasing productivity and reducing costs, as Patrick Smith reports
A few years ago, visual inspection of an 18-year-old bridge by ARRB in Australia identified considerable cracking in the precast, prestressed deck planks as well as in the cast in situ deck overlay.Laboratory examination indicated that the deck planks and the deck overlay were suffering from a strong case of alkali-aggregate reaction (AAR). Testing of concrete cores drilled from the planks indicated that the concrete component had lost around 30-50% of its compressive strength and elastic modulus.
Many similar bridges have exhibited the same problem. For the bridge in question, the deck was replaced after 14 years, and the affected planks stored on site. Assessment of the mechanical properties and load capacity of the planks was essential for sound decision making regarding rehabilitation of the other affected bridges.
Full scale testing of three planks was undertaken in collaboration with Monash University, to examine the overall effects of the AAR-cracking.
Durability properties of the concrete were determined from residual strength and expansion properties of concrete, petrographic examination, scanning electron microscopy (SEM) and energy dispersive X-ray (EDX) analysis. Residual alkali content, cement content, compressive and splitting tensile strength, elastic modulus, residual expansion and maximum expansion potential were also determined. Coarse aggregate was separated for testing, as well as accelerated testing of the planks expansion.
A strength assessment was conducted to determine a load rating for the planks. This assessment included ultimate strength, ductility and deflection.
The SEM/EDX and petrographic examination identified two reaction mechanisms in the planks, being AAR and delayed ettringite formation (DEF). The latter occurs at high curing temperatures. The severity of the AAR in some of the planks was evident from the extent of the reaction products seen in the concrete.
Planks which exhibited worse cracking contained large amounts of both AAR and DEF, indicating that they were cured at temperatures higher than the other planks and greater than 75°C. However, despite the degree of reaction and cracking, the ultimate strength of the planks appeared to be good and in the range of 580-610 kN, close to the design value. This indicated that the ultimate strength is governed by the performance of the prestressing tendons and their bond with the concrete. This bond did not appear to have deteriorated in the planks. However, the residual expansion of the concrete was still very high, despite the extensive reaction, indicating further deterioration would occur in the future.
Therefore, long term durability of the planks is in doubt, with further expansion and cracking expected, which may also affect the bond strength of the prestressing tendons.
Expert advice on material selection can avoid the problem. Also, the temperature of curing of the prestressed planks should be controlled below 75°C. ARRB is aware of AAR related concrete cracking on bridges within eight years of their construction, despite design lives of 100 years.
Dr Ahmad Shayan (%$Linker:
His team at ARRB also advises on the corrosion of steel in reinforced concrete, and pile integrity testing, as well as other concrete related services. This particular project provided a practical demonstration of the value of AAR research to road agencies.
Flexure Frame
Such testing is vital to the integrity of structures including bridges and highways, and the Italian
The C-shaped open structure allows easy front loading and once the specimen is in testing position the structure is closed by a vertical hydraulically-controlled rod.
"The closed structure grants higher rigidity to the system with respect to the most common static C-shaped frame," says Controls.
"Due to this important feature and to the capacity of 300 kN, this frame is ideal either for conventional flexural tests or for more sophisticated determinations such as deformability tests and ductility index."
A high precision strain gauge load cell assures high accuracy to the test results, and the frame can be fitted with various accessories to perform a flexural tests on standard concrete beams to EN 12390-5; on paving flagstones to EN 1339; on kerbs to EN1340; an energy absorption test on sprayed concrete to UNI 10834 (access. 50-C1601/6); flexural toughness of fibre reinforced concrete to
The frame can be connected to various Controls' consoles such as the Semiautomatic; new Automax 5 automatic; Sercomp 7 servohydraulic automatic; MCC 8 servohydraulic automatic, and Advantest 9 servohydraulic automatic control console.
Controls' new Automax 5 automatic compression testers is said to represent a more sophisticated and advanced evolution of compression testers, and features a complete automatic test cycle with closed-loop digital feedback.
The hydraulic group includes an efficiency dual stage pump: centrifugal low pressure high delivery stage for fast approach and radial multi-piston high pressure stage for test execution.
It has been optimised to prevent any overheating effect even under intensive use and severe working conditions, and the hydraulic group can be fitted with a distribution block for connection and non-simultaneous control of a compatible second frame (for example flexural frame or compression frame).
The control unit is located above the hydraulic unit and controls the functioning of the whole equipment: once the specimen parameters have been introduced, it is sufficient to press the start button to complete the test. The system automatically applies the correct load rate conforming to the information introduced via the control touch screen panel.
The load rate value is continuously monitored and automatically controlled and can be printed in the test report when connected to PC or to a compatible USB inkjet printer.
The wide memory of the control unit means that thousands of tests complete of load-time graphics can be memorised.
Concrete for tunnels
Concrete is used in a diverse range of tunnelling projects, due to its combination of versatility and strength. However, this flexibility also makes thorough and accurate testing crucial to avoid potentially disastrous failures.
Modern technology is now making testing more efficient and reliable, increasing productivity and reducing costs, says ELE International, which offers a range of testing equipment.
Concrete's flexibility can, however, create problems as the raw materials of cement, aggregate and water to make concrete are difficult to regulate, and the methods used for mixing can result in finished products that potentially have widely varying properties.
"The implications for inadequate quality control are considerable. There is the obvious threat to the safety of workers and users if tunnel components fail and lead to a collapse, and there are possible commercial and legal implications, with the potential costs of court action, compensation and repairs. Less immediately damaging, but just as serious, is the threat of premature deterioration due to incorrect formulation or inconsistencies in mixing," says ELE.
"Sample testing of concrete is an essential part of all construction projects, and tunnelling is no exception.
"Fresh concrete should be regularly tested to assess the suitability of the mix to the specific application, and to ensure that the concrete used is of a consistent standard throughout the duration of each contract."
"Three standard test methods are available for fresh concrete at different levels of workability.
"The slump test measures the consistency of freshly mixed concrete; the flow table test is used where high workability mixes are specified (slump of 180mm plus), and the Vebe consistometer test is generally used with particularly stiff mixes."
Hardened concrete should also be tested in the laboratory and on site to ensure that the component parts have the correct properties, and that concrete already in use has retained its desired properties.
Compressive testing can help engineers assess the strength of concrete, its performance under actual loading, and if any deterioration has occurred, for example from chemical action, weathering, fatigue or excessive loading.
A range of testing machines is available to accommodate different sized samples, designed for different frequencies of use, and with varying levels of data handling.
"For high throughput testing, on site and in the laboratory, advanced microprocessor-controlled units such as ELE's ADR Auto range can be used to meet current EN standards and provide fast, accurate and detailed results recording and analysis."
International standards
The company says its line includes the servo-controlled machines which allows the operator to carry out different kind of tests automatically (concrete compression and flexure test; mortar compression and flexure tests; splitting tensile test of cylinder, cubes, and elastic modulus on concrete and rock specimens).
The machines are connected to the C104 Servotronic Unit, which by means of a valve, provides fully automatic tests in all its phases of acquisition, visualisation, data processing, including the setting of the pace rate and the software for the printing out of the results on a certificate.
This automatic system can be supplied with UTM2 (Universal Testing Machine) software that allows the machine to be managed through a PC, and includes licences for compression, flexure, tensile splitting tests and elastic modulus.
The company says its testing machines allow the user to select and combine compression and flexural groups to satisfy specific requirements.
Among its range of flexural frames, Matest has developed the C091 open side frame that enables the operator to position the specimen easily between the rollers.