Concrete is a versatile construction product, but it must be tested to make sure that it is fit for purpose
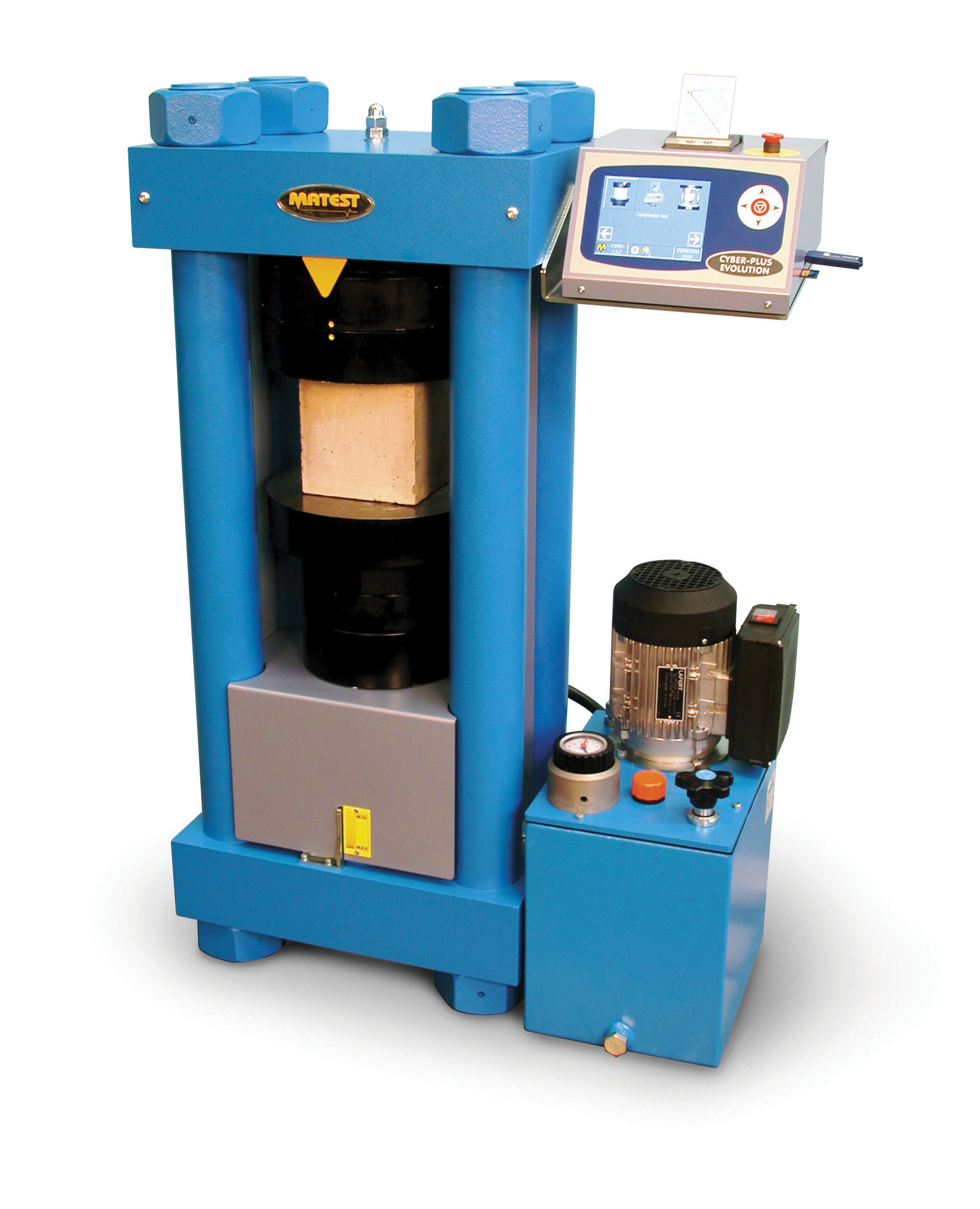
Matest recently renewed and improved its whole range of compression and flexural machines including the Cyber-Plus Evolution
Concrete is a versatile construction product, but it must be tested to make sure that it is fit for purpose
For control purposes, concrete is normally required to be tested under uniaxial compression, indirect tension and flexure. In view of the importance of concrete cube, cylinder and core testing within the construction industry, compression testing machines have been the subject of more rigorous standardised performance testing.The most recent European EN 12390-4 is essentially a performance specification which allows each manufacturer to design a testing machine using its own expertise and ideas provided that it complies with geometrical and mechanical requirements for parts.
"On the other hand concrete reveals loading rate sensitivity which may considerably affect the compressive test results," says Italian testing equipment manufacturer
"As rate of loading increases, the compressive strength of concrete increases according to a principle called strain-rate effect. The international standards (for example, EN 12390-3, ASTM C39) specify that during the test the loading rate must be constant within a small allowable range. This firm specification helps ensure consistency within and among laboratories." The majority of the hydraulic compression testing machines for concrete now in service are manually-operated, says Controls. The operator is required to manually adjust a valve to achieve a loading rate within the specification.
"Unfortunately, these adjustments can be inaccurate: the manual flow control reacts badly to small speed variations during a test which ideally should be corrected instantaneously.
"To cover the weakness of the loading rate verification, manually operated machines are now being offered with digital indicators that calculate and report the average loading rate and can generate load versus time diagrams to verify that the test was performed according to requirements of the standards.
"These systems however do not eliminate the possibility that an operator could perform tests at rates exceeding limits set by the standards. There is evidently a need for an automatic concrete testing system that can control loading rate."
Some years ago Controls decided to produce a dual stage pump with variable flow which provides three fundamental characteristics: accuracy of load control, productivity and energy saving.
Its new range of PILOT 4 compression machines include ES (Energy Saving) technology, which was introduced some ten years ago on the well-known AUTOMAX 5 series. Now, it has been substantially improved and employed in the new PILOT 4 series, which Controls claims guarantees high productivity, up to 30 samples per hour and low energy consumption with savings up to 30% compared with traditional manually-operated machines.
The hydraulic unit is driven by an efficient dual stage volumetric pump driven by a dc motor with the variable speed controlled by a high resolution closed-circuit microprocessor.
"This solution allows on the one hand the limitation of costly waiting times between tests thanks to the raid approach stage (up to 40mm/min), and on the other hand to control drop by drop the oil flow so as to use only that necessary to perform the test.
"Cold oil and a pump that does not heat up avoids the need of a cooling fan while perfect mechanical coupling ensures near silent operation at the high pressures required," says Controls.
On the electronics side a big step forward has been made with a new control board which reads and converts the load on a scale with more than 131,000 points for each channel. A second test frame can be controlled by fitting a pressure transducer or load cell to the second channel and a distribution block to the hydraulic circuit. The operator interface is by a touch screen with icons for easy and immediate use.
"Rigidity is the characteristic of the robust welded frame certified for stability to EN 12390-4: a solid cross head distributes the absorbed forces to four welded columns, symmetrical and equal distance from the load axis.
The load, free from unwanted "moments," is transmitted to the sample via a self-locking ball seat with an oil bath which is characterised by its high hardness and non-deformability. The load test chamber is large enough to house rectangular load platens for block testing, and the compression machine can be furnished with a wide range of optional accessories allowing tests on cement samples, indirect tensile tests on cubes, cylinders and pavers.
"As each laboratory attempts to create a distinctive product, the need to improve quality and productivity by means of reducing testing times and data entry is assuming importance.
"Employing testing systems that automatically perform the tests according to specifications, calculate results and seamlessly communicate with other computers and programs running on their corporate network, ensure consistency within and among laboratories and lead straight to success," says Controls.
Innovative machine
With the introduction of building materials promising ever higher performance, leading to ever more ambitious and complex projects for infrastructures, possessing a solid scientific background makes a remarkable difference, saysThe company has been consulted by leading companies and has come up with solutions that have "subsequently proved useful for the whole industry," citing as an example an Italian project where it developed a compression testing machine for concrete whose innovative design involved two distinctive measurement scales, the lesser one covering 10% of the larger one.
This consisted of a hydraulic ram having two concentric stems, one working from inside the other but completely autonomous so that, in practice, two machines are available in one, the more powerful machine for specimens of standard strength and the more sensitive for testing cores taken from tunnel linings.
"A single frame and a single power unit proved an advantageous solution cost-wise and meant that no sacrifices were necessary in terms of performance when compared with the classic, two-machine solution. It is a bit like having a truck which, when needed, becomes a scooter," says Tecnotest.
According to the company that project was well in advance of its time, and only today, after many years, the dual ram machine is largely recognised as "a highly practical and technologically advanced solution." Tecnotest produced a graph illustrating the problems it had to face and solve before coming up with its solution. It shows the theoretical curves that delineate the possible errors in response made by the two generic devices with a discrimination of ± 0.1% of respective full scales. If a precision higher than 1% is required, the object described by the red curves can be used from 10-100% of its potentiality. The green curves show the effect using the second device, which has the same characteristics but with a scale limited to 10% of that of the former.
Combining the two objects stretches the field of use to the lower limit of 1%, so the required precision is respected at all times.
In order to effectively obtain two measurement scales in a hydraulic press, apart from the sensitivity of the dynamometers, fine tuning of the device regulating fluid pressure should also be considered: with only one ram, the lower the strength required by the system, the higher the percentage error in response.
"By way of comparison, it is like increasing the size a photo: beyond a certain limit the grains of a film inevitably become more evident and details are lost," says Tecnotest.
"Using two rams of differing sizes working at the same pressure, different forces are obviously obtained, but with the same number of elementary regulation units.
"In the case in hand, the small piston develops a maximum force equal to about 10% of that of the large one so hydraulic discrimination is ten times sharper.
"This characteristic enables the compression testing machine to be used also for tests where low loads are foreseen without any risk of causing jolts in the ramp generated during upward movement.
"As far as accuracy of measurement is concerned, the argument is quite similar since each piston has its own dedicated dynamometer."
Renewed range
In another move,These have been developed by its R&D department to offer a "new generation of testing machines for semi-automatic (C109N) and fully automatic (C104N) compression, flexural, and splitting tensile tests on concrete specimens.
"All new compression machines, having a capacity from 1,300-5,000kN, are conceived for professionals and produced with the latest technologies to offer user-friendly systems and advanced functions," says Matest.
"Testing concrete specimens using a new model allows the operator to easily control all the test phases (such as system configuration, parameters setting and calibration) and to get reliable and repeatable results."
The C109N and C104N control units are supplied with compression and flexural frames, and work as a common PC on Windows Embedded Operating System, offering all the functions available on a PC for the management and visualisation of data, pictures and graphics.
The new models have full colour touch screen displays with icons and internet and intranet connections for remote technical assistance: once the machine has been connected to the internet, Matest technicians can check the unit and provide the customer with professional assistance. All test data can be saved on external memories through 2 USB ports and 1 SD card slot.
"The production of concrete testing machines has been a Matest core business for about 25 years, and more than 10,000 frames are used worldwide to carry out tests on cubes, cylinder and blocks. All the machines are manufactured in accordance to the most important international standards," says Matest.