A specially adapted Wirtgen SP25i concrete slipformer has been used on the M6 motorway near Cannock in the UK. The machine worked together with a Wirtgen ISF25i (independent side feeder) in order to pave a concrete slab under difficult conditions.
With an overall length of 373km, the M6 is the longest and one of the most heavily congested motorways in the UK. The M6 connects the M1 motorway near Rugby with Carlisle near the Scottish border. But due to the steadily growing volume of traffic, the Highways
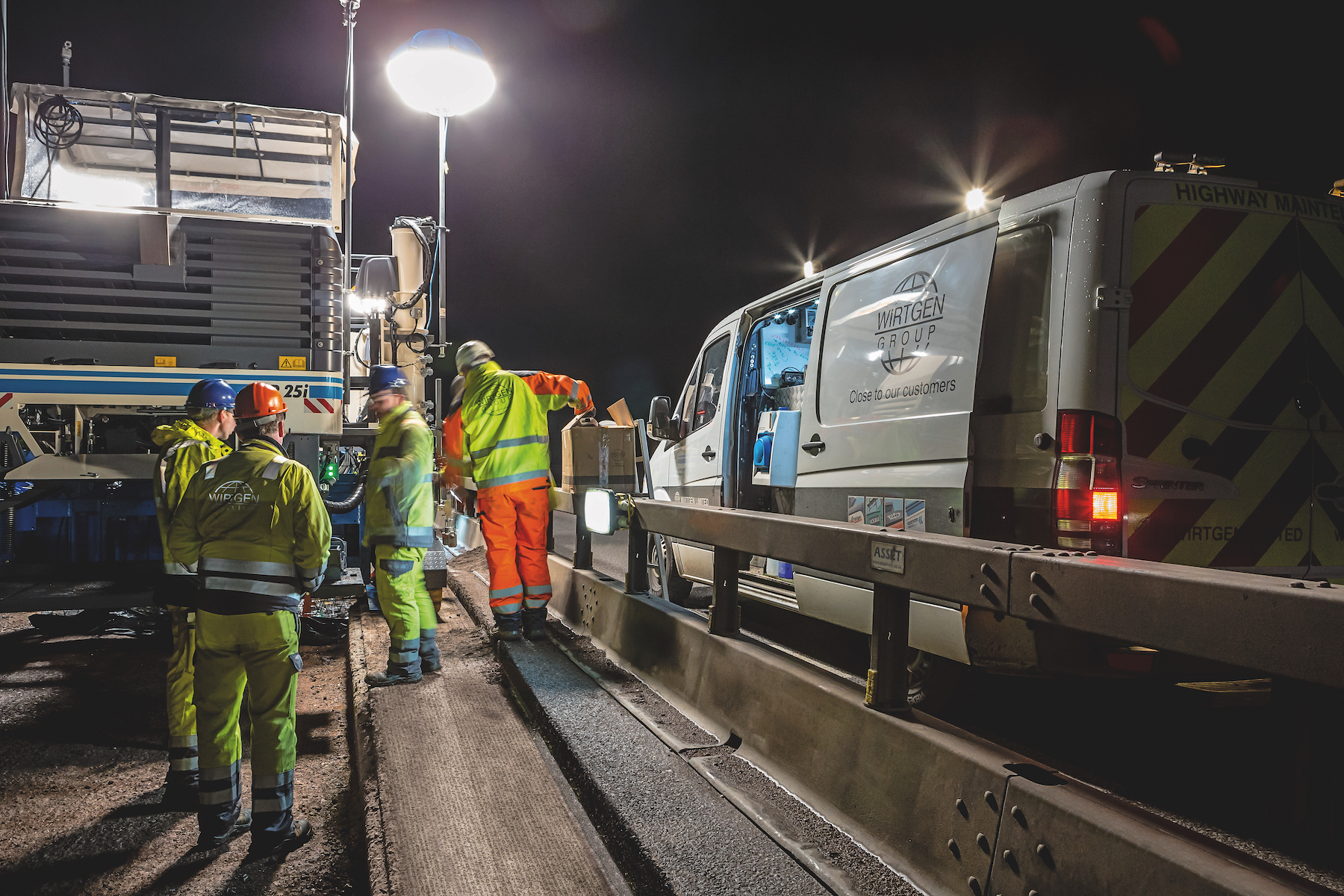
The work had to be carried out within a tight timeframe to minimise disruption
A specially adapted 2395 Wirtgen SP25i concrete slipformer has been used on the M6 motorway near Cannock in the UK. The machine worked together with a Wirtgen ISF25i (independent side feeder) in order to pave a concrete slab under difficult conditions.
With an overall length of 373km, the M6 is the longest and one of the most heavily congested motorways in the UK. The M6 connects the M1 motorway near Rugby with Carlisle near the Scottish border. But due to the steadily growing volume of traffic, the2309 Highways Agency decided that the service lane was to be upgraded for use as an additional lane between junctions 10a and 13 near Cannock, 25km north of Birmingham. The primary task of the contractor 2435 Carillion and specialist sub-contractor Extrudakerb was to replace the existing reinforced concrete slab with asphalt surfacing on the service lane in order to bring the new traffic lane onto a level with the adjacent pavement and create a homogeneous concrete pavement.
This project is the first of its kind in the UK. Work can only be carried out at selected times and in confined conditions. Following an intensive planning phase, project manager Mark Gladwell decided on a sophisticated timetable and logistics schedule. During the day, temporary steel barriers separated the service lane to be converted from the main traffic stream on the adjacent traffic lane. At night, when traffic was lighter, lane 1 and part of lane 2 were closed to traffic to provide an access route for the construction vehicles.
It was decided to use a Wirtgen SP25i together with a Wirtgen ISF25i which had been developed on the basis of the SP25i in order to meet the project's special requirements. Gladwell continued, "Using the ISF25i as an independent side feeder with pivotable conveyor was the only option available to assure the safety of the operator and of the workers on this confined job site while at the same time minimising the nuisance to passing traffic."
The project encompassed 16km of new roadway, around 3m wide and 300mm deep. Around 14,000m³ of C50 class concrete was delivered to the site just-in-time by7406 Lafarge Tarmac from the mixing plant in Walsall using specially modified 8m³ concrete mixer trucks. These trucks are equipped with GPS and an automatic system, which monitors and adjusts concrete consistency to ensure that exactly the required quality is delivered at the right moment.
On arrival at the job site, the concrete was transferred over the top of the temporary steel barrier into the hopper of the ISF25i and from there to the slab paving kit of the slipform paver through two synchronised conveyors. The time frame available for working was never more than six hours and it was important to maximise productivity so that the construction work could proceed efficiently. Around 32m³ of concrete was paved/hour, making around 200m³ for each six-hour shift. The work was undertaken in 12 consecutive shifts followed by two rest days. All the other materials needed for the project including around 300tonnes of reinforcement, 25,000 tie bars and 3,000 dowels, dowel bars and curing material, had to be delivered during the night, within the same time frame.
The compact SP25i paver is a versatile machine and benefits from the Wirtgen Auto Pilot Field Rover control system, which does away with the need for stinglines and helps optimise performance.
If the concrete profile is to be slipformed on an existing roadway edging, the user can calculate the optimum virtual stringline on site in a matter of minutes. For the first time, the customary stringline can indeed be replaced in practice. This advantage proved useful for the construction project on the M6 motorway. "Another decisive advantage of the Auto Pilot Field Rover was that we did not have to install stringlines, as the Highways Agency had prohibited the use of posts drilled into the ground for attaching the stringlines. Such posts could have damaged underground cables," said site manager Dom Egan, Extrudakerb.
With an overall length of 373km, the M6 is the longest and one of the most heavily congested motorways in the UK. The M6 connects the M1 motorway near Rugby with Carlisle near the Scottish border. But due to the steadily growing volume of traffic, the
This project is the first of its kind in the UK. Work can only be carried out at selected times and in confined conditions. Following an intensive planning phase, project manager Mark Gladwell decided on a sophisticated timetable and logistics schedule. During the day, temporary steel barriers separated the service lane to be converted from the main traffic stream on the adjacent traffic lane. At night, when traffic was lighter, lane 1 and part of lane 2 were closed to traffic to provide an access route for the construction vehicles.
It was decided to use a Wirtgen SP25i together with a Wirtgen ISF25i which had been developed on the basis of the SP25i in order to meet the project's special requirements. Gladwell continued, "Using the ISF25i as an independent side feeder with pivotable conveyor was the only option available to assure the safety of the operator and of the workers on this confined job site while at the same time minimising the nuisance to passing traffic."
The project encompassed 16km of new roadway, around 3m wide and 300mm deep. Around 14,000m³ of C50 class concrete was delivered to the site just-in-time by
On arrival at the job site, the concrete was transferred over the top of the temporary steel barrier into the hopper of the ISF25i and from there to the slab paving kit of the slipform paver through two synchronised conveyors. The time frame available for working was never more than six hours and it was important to maximise productivity so that the construction work could proceed efficiently. Around 32m³ of concrete was paved/hour, making around 200m³ for each six-hour shift. The work was undertaken in 12 consecutive shifts followed by two rest days. All the other materials needed for the project including around 300tonnes of reinforcement, 25,000 tie bars and 3,000 dowels, dowel bars and curing material, had to be delivered during the night, within the same time frame.
The compact SP25i paver is a versatile machine and benefits from the Wirtgen Auto Pilot Field Rover control system, which does away with the need for stinglines and helps optimise performance.
If the concrete profile is to be slipformed on an existing roadway edging, the user can calculate the optimum virtual stringline on site in a matter of minutes. For the first time, the customary stringline can indeed be replaced in practice. This advantage proved useful for the construction project on the M6 motorway. "Another decisive advantage of the Auto Pilot Field Rover was that we did not have to install stringlines, as the Highways Agency had prohibited the use of posts drilled into the ground for attaching the stringlines. Such posts could have damaged underground cables," said site manager Dom Egan, Extrudakerb.