Although it has been around since the 1970s, roller compacted concrete (RCC) is starting to look a whole lot more attractive, thanks to the rising price of bitumen. Now the challenge is to define specifications and tests to help ensure quality - Kristina Smith reports. At a meeting of the American Concrete Pavement Association in December 2011, there was a sea-change in the attitude towards roller compacted concrete (RCC). Up until that point, the feeling among the 400-plus members, of which half are contra
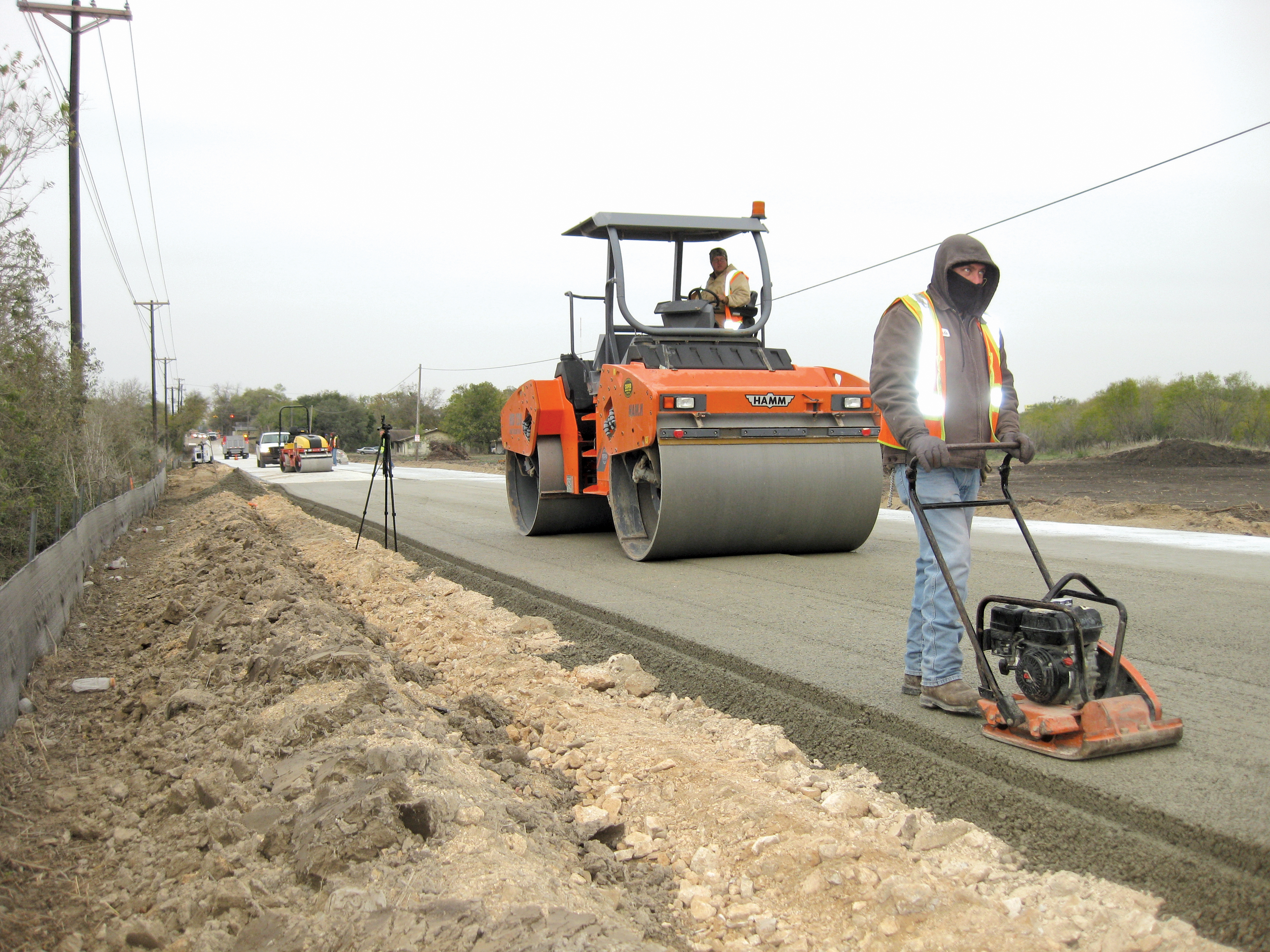
Laid in 2011, the RCC pavement in New Braunfells replaced an asphalt surface, which had been suffering due to the number of heavy trucks passing over it
Although it has been around since the 1970s, roller compacted concrete (RCC) is starting to look a whole lot more attractive, thanks to the rising price of bitumen. Now the challenge is to define specifications and tests to help ensure quality - Kristina Smith reports
At a meeting of the American Concrete Pavement Association in December 2011, there was a sea-change in the attitude towards roller compacted concrete (RCC). Up until that point, the feeling among the 400-plus members, of which half are contractors, was that RCC was of no interest to them.“Now some of the paving contractors have got involved with RCC and have seen the potential,” said ACPA president and CEO Jerry Voigt. “It’s a concrete pavement and we need to get involved and work particularly on quality issues.”
The driving force behind the increasing popularity of RCC is the rising price of oil. “The cost of asphalt pavements has gone up astronomically in the last four years,” said Martin Ashfield, national technical manager for
Based on its US experience in RCC, Cemex started 18 months ago to promote its use in other countries including the UK, Philippines, Spain, Croatia, Poland, Latvia and France.
But before some specifiers will consider RCC as an alternative to asphalt, there are a few issues to tackle. Not least the perception that RCC can be somewhat unpredictable when it comes to quality.
“If you get something slightly wrong, the quality won’t be as good,” said Ashfield. “The crucial element is water content. If it’s too wet or too dry, it’s a problem - it’s the same with asphalt and bitumen. There are concerns around quality and how accurately you can control the parameters you need to control.”
The increasing popularity of RCC and the desire to tackle issues around quality is reflected in the work which is going on around the world to produce guidance, specifications and new test methods.
In April this year, the European Ready Mixed Cement Organisation (ERMCO) published its ‘Guide to roller compacted concrete for pavements’ which includes a model specification for a RCC pavement. In the US, an ACPA task group is currently working on a specification for RCC which it plans to publish this summer.
Looking at standards, a subcommittee of
RCC as a running surface
Roller compacted concrete is a relatively dry, no-slump concrete which is laid using asphalt paving equipment. According to ERMCO, its first use dates back to the 1930s or 1940s, although its use became more widespread from the 1970s when it was used by the Canadian logging industry.Today, it’s most common use both in the US and Europe is in heavy industrial areas such as waste transfer stations and docks, although many RCC roads have also been laid in the US. In Europe, advocates are suggesting that it be used on roads with a thin asphalt layer over the top to provide skid resistance.
In the US, ACPA aims to promote the use of RCC without an asphalt overlay. “For the first time we are looking at what provisions you put in a specification for RCC as a surface exposed to traffic, as well as what provisions are needed for RCC covered by another surface layer,” said Voigt.
ACPA’s specification will call for a nuclear density test, in line with ASTM 1040 and cylindrical compressive strength tests, with the cylinders created according to ASTM C1435, using a vibrating hammer. It will also prescribe an abrasion resistance test. “The surface durability of RCC is very critical: a tipping point kind of issue,” said Voigt.
The ACPA specification will also define a ‘referee test’. “If there’s some dispute or concern about the results of the cylinder testing, the parties can go to referee provision and extract cores and test cores after the actual processing of the pavement,” explained Voigt.
ACPA’s aim with its RCC specification is not to be prescriptive. “We would like to fashion this specification as an end result specification so that the material supplier and contractor may have more latitude in bringing materials together,” said Voigt.
The use of test strips for RCC pavements at the beginning of a job will be important if latitude is to be allowed, according to ACPA. Test strips are a good way to demonstrate that the density, surface requirements and joints are meeting the required performance. Ashfield agreed this is good practice and says that it is a common requirement from the UK
ERMCO’s guide also covers testing. It says that compressive strength specimens for RCC should be made in the same way as for other hydraulically bound materials, using a vibrating hammer in accordance with EN 13286-51. And in-situ tests should be made using a nuclear density gauge to BS 19244-2, or equivalent.
The new EN 14277 Part 1 will call for tests to demonstrate compressive strength, flexural strength and the immediate bearing index, which measures how quickly you can traffic a material after it has been laid. “The rewrite of EN 14227 will be a big benefit for RCC because it will be included in the specification,” said Ashfield. “The Highways Agency will then be able to include it in their design manual.
“In the UK, we are using all our American colleagues’ information to try and convince designers and specifiers to use it. In certain situations it works, in others it doesn’t.” ACPA is currently compiling a database of 200 RCC projects from around the US, the ‘National RCC Explorer’, which will shortly be available on its website.
ASTM’s work to create the standardised method for making RCC samples in a gyratory compactor is a stepping stone to using the test machine for design, according to subcommittee member Stacy Williams, director of the Centre for Training Transportation Professionals at the University of Arkansas. “There is not a standardised method for RCC design using the gyratory compactor, but that is certainly a next step,” said Williams. “Once we all agree on the appropriate method for creating the samples in the gyratory, we can move forward with establishing a design method.”
Williams said that after several revisions over the past couple of years, the method is currently being balloted in the subcommittee and she believes that they are ‘close’ to producing the final version.
Pietro Ferrari, senior product manager at
Materials producers do already use gyrator compactors to help them design RCC mixes. “At Cemex we have used the Gyratory Compactor test to understand the difference between different RCC mixes,” said Mike Higgins, Cemex’s national technical manager for laboratories in the UK. “We use the test as a good indication of compactability and how it’s impacted for different water content and aggregate types.”