Dan Gilkes reports on a Belgian highway upgrade When the Ministry of Public Works in the Belgian State of Flanders decided to reconstruct and resurface 19km of the N49 Antwerp-Knokke Expressway, continuously reinforced concrete paving (CRCP) with an exposed aggregate surface was the natural material choice. Indeed exposed aggregate, with its high grip and low noise benefits, has been the first option for all motorway surfacing work in Belgium since the 1980s. However, the €15.65 million contract is not a li
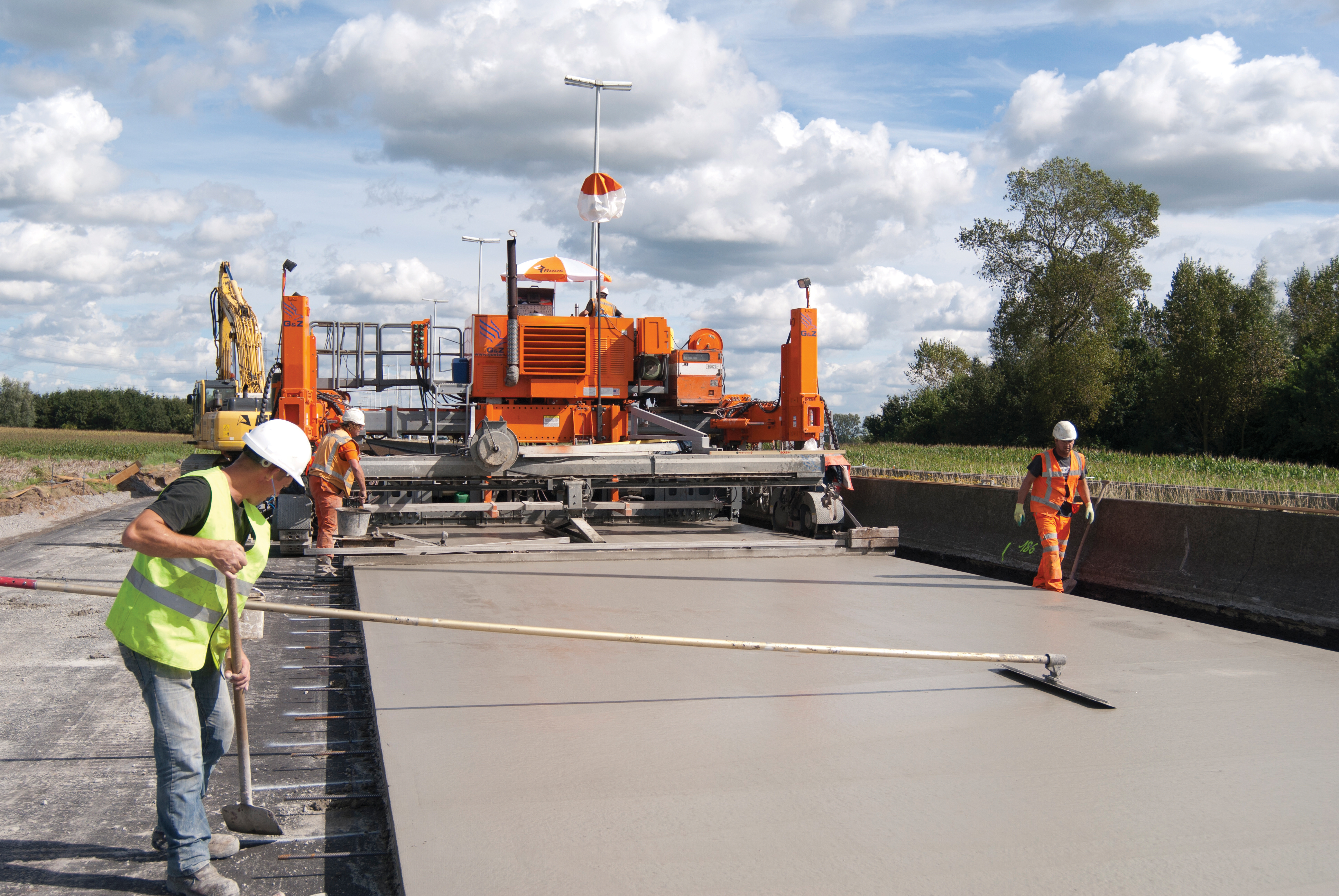
The Roos team produce an incredibly smooth finish , working at a rate of around 1km per day in two shifts.
Dan Gilkes reports on a Belgian highway upgrade
When the Ministry of Public Works in the Belgian State of Flanders decided to reconstruct and resurface 19km of the N49 Antwerp-Knokke Expressway, continuously reinforced concrete paving (CRCP) with an exposed aggregate surface was the natural material choice. Indeed exposed aggregate, with its high grip and low noise benefits, has been the first option for all motorway surfacing work in Belgium since the 1980s.However, the €15.65 million contract is not a like-for-like reconstruction project. Main contractor, Belgian firm Aswebo, has had to mill off 23cm of asphalt paving before commencing reconstruction. A 5cm layer of asphalt ABT-B course was then laid, above the previous foundation course and beneath the new CRCP, to prevent water ingress into the foundation layers.
The CRCP is being laid in a 23cm deep layer in three widths along the two-lane highway. Aswebo has called upon sub-contractor Roos Group to install the initial 6m wide pavement, which includes the outside faster lane of the road, with tie bars inserted into the side of the concrete to connect to a 4.75m wide lane and hard shoulder with a drainage gully that will be laid later.
A 1m connecting strip of concrete will also be laid between the 6m wide lane and the existing concrete step barrier in the centre of the highway.
Roos Group is using a Guntert & Zimmerman S600 paver to lay the 6m wide pavement, while Aswebo will employ its own paving machinery for the 4.75m and 1m width sections. The job is being carried out in five separate contract phases, with a total of 230,000m2 of new concrete paving to be laid.
The first phase includes 7.3km of continuous roadway on the eastbound carriageway, while the second phase is for just 2km of pavement. However there is a distance of 25km between these two phases.
Phase three includes the construction of 4km of concrete step barrier, with the fourth phase providing the westbound carriageway of the 7.3km phase one section.
The final phase includes the remaining 2km of westbound road.
The distances involved, particularly for delivery of concrete from the batching plant which can take up to an hour, did lead to some early concerns with concrete temperature, particularly in heavy weekend traffic.
However, having tuned the specification of the concrete, Aswebo is now moving ahead rapidly with the work.
By the end of the first week of concreting Roos was achieving an average production of 1km per day, over two 11-hour shifts.
Which is good news for all concerned, as the Antwerp-Knokke Expressway is a particularly busy stretch of highway.
Linking the city of Antwerp with the Belgian coast, the N49 carries a heavy traffic load of commercial vehicles heading to the port of Zeebrugge throughout the week, but also provides a direct route for those in the city to reach the beaches at the weekend and in the summer holiday period.
The G&Z S600 has been in the Roos Group fleet for two years now, and was in fact the manufacturer’s second model of this type to be produced. G&Z has sold more several of the S600 pavers to date.
A multi-purpose slipform paver, the S600 has a modular tractor frame that allows it to work on city streets, secondary roads and highways, as well as paving contracts at airports.
The machine can also handle barrier walls, off-set paving and zero or minimum distance paving, making it a versatile addition to the Roos fleet.
The company runs seven slipform pavers in total, but the Expressway project is a major contract for the firm.
“We have a lot of kerb and gutter work at the moment but this is certainly a substantial contract for us,” said managing director Peter Roos.
The double telescopic frame of the S600 permits a nominal working range of 2.44m to 6.71m with a dowel bar inserter fitted. However with bolt-on extensions, the machine can handle paving widths of up to 9m without the dowel bar inserter.
The Roos machine is equipped with an optional Final Finisher device, which uses a magnesium surface finishing ski that floats on the concrete surface.
The longitudinal ski oscillates fore and aft while travelling transversely back and forth across the slab. Roos then manually floats the concrete surface to achieve a smooth finish.
As soon as the CRCP roadway is formed, Roos sprays a chemical, sugar-based compound on the concrete and covers it with plastic sheeting, allowing the concrete to cure.
This plastic sheet is removed the following day and a powered sweeping brush is employed to sweep away the top layer of fines, revealing the exposed aggregate set in the finished concrete surface.
Belgian road specifications stipulate that the maximum width of a single stretch of concrete road should be no more than 5m wide.
Due to this fact, Aswebo is running a longitudinal cut, to a depth of one third of the concrete roadway, in the centre of the 6m wide lane.
In addition, the company is trying a new technique to prevent further damage of the pavement while in use.
Aswebo is using a process called induced cracking, which involves cutting 40cm slots in the outer edge of the pavement, to a depth of 6cm, every 1.2m along the route.It is hoped that this will prevent additional cracking of the main concrete carriageway under heavy traffic as the roadway ages.
Belgium has a number of heavily loaded highways, though not always with its own traffic, as the country provides a major through route for trucks in particular travelling from other parts of continental Europe to the ports on the coast.
In the State of Flanders alone there is expected to be more than 140km of highway repair and replacement work this year, which is keeping local contractors busy.
“We have three projects like this one to complete,” said Aswebo’s site manager and recycling director Steven Last.
“Two have to be completed this year and then we will start another one in the new year.”