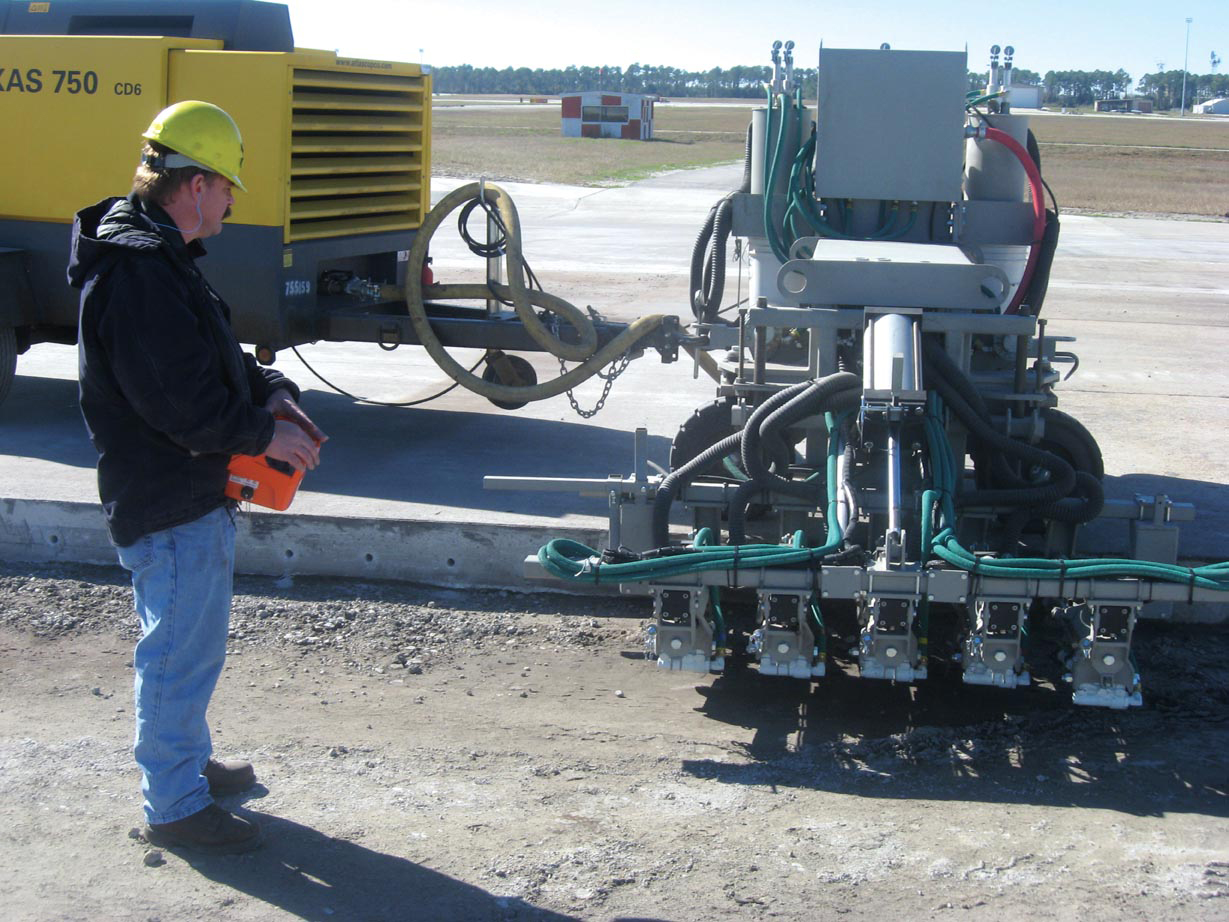
Innovations in materials technology, as well as machines, could provide a major boost to the concrete paving sector - Mike Woof reports
Development of new material technologies for the concrete paving sector continues apace and the latest innovations could provide the biggest boost for this market in many years. High performance cementitious material (HPCM) is an innovative concept that has been developed and tested for road surfacing applications as part of a project in which the UK's Transport Research Laboratory (The initial mix-design developed was improved during the project and evolved through the selection of constituents, mix-design and laboratory application processes and assessment of behaviour. This was assessed for critical properties such as: skid resistance; binder function; protection of lower pavement layers; cracking behaviour; and bond between the cementitious and the bituminous substrate. The results showed that the thickness of the fibre-reinforced mortar layer needed to be minimised to control costs. At the same time, it needed to be thick enough to allow for good penetration of the chippings in the fresh mortar.
Testing showed that HPCM has great strength and integrity and there is a high probability that wearing courses of the material will be practically maintenance-free during a likely service life of 30 years, even on roads with heavy traffic volumes.
Production of HPCM uses existing know-how and equipment although laying the material and inserting the chippings will require some modification to existing machines. Further testing in the field is also needed to achieve the best balance between mixing/handling/placing and the performance of the hardened material. However HPCM has the potential to offer high skid resistance, comfort, durability and moderate noise emissions.
In the metal
This development could be of major importance for concrete highway construction techniques, which are often used when highways are expected to cope with heavy traffic loads. The technology offers a potential solution that will ensure the surface can meet macro-texture requirements for low road noise and driver comfort, at the same time as providing good skid resistance even after 10-20 years of heavy traffic. According to TRL, this system could replace the use of current flexible surfacing solutions for semi-rigid pavements, but without requiring such frequent maintenance and extending time between repaving.
In the metal
The machines used to slipform concrete are a vital part of the market and their continuous development allows this market to remain highly competitive. At the smaller end of the concrete slipformer market, versatility is an important feature. These more compact machines can be expected to carry out an array of concrete paving and concrete barrier forming tasks, as well as other duties.
One of the best-accepted multiple role slipformers on the market is
This latest feature broadens the range of capabilities for the successful Commander III, which is already well-accepted in the market for duties such as lane additions, shoulders and variable-width paving when using its V2 mold. By fitting the IDBI unit GOMACO says that the Commander III can now be used to insert transverse joint dowel bars in pavements up to 4.88m wide.
The inserter system is an independently-powered unit that fits onto the Commander III and is driven by a
Highly productive, the bar insertion system is said to be rugged in construction, independent, self-contained and self-powered. The unit is attached directly to the paver and has adjustable-height bar extractors that allow contractors to change the set-up quickly to suit different bar sizes. The IDBI attachment is fitted with hydraulic outriggers for use when attaching the unit to the paver as well as for loading and unloading the unit for transport. GOMACO says that the IDBI attachment will also be offered on some other pavers in the future.
Meanwhile Miller Formless is improving its three model range of slipformers with the latest version of its M-8100 model. Designed to handle an array of applications including kerb, kerb and gutter and barrier wall slipforming, the M-8100 is powered by a four cylinder, 6.8 litre John Deere diesel rated at 129kW and which meets Tier III/Stage IIIA noise and emission regulations. Modifications and upgrades for this latest model include increased weight, thicker skins on the paving pan sections and increased power from the diesel.
For paving applications the M-8100 can lay concrete in strips up to 4.88m wide and as standard it features four tracks, giving it stability when paving lane additions, shoulder, residential streets and expressway ramps. Four track steering allows the machine to turn in confined spaces while the machine is said to retain the durability and reliability of previous models, which help ensure longevity. .
The range also includes the M-1000and M-8800 slipformers. Although Miller Formless is based in the US, the firm has been supported in Western Europe by Paris-based dealer Sti for over 30 years selling machines. The company also has a dealer in the UK and a dealer selling machines in the Asian, Australian and South American markets.
And
The system is fitted to the left rear of the machine and is powered with the machine's auger conveyor circuit, which provides
direction and speed control. Meanwhile the driveway knife circuit controls the plunge function up and down.
The auger for the post-hole digger works inside a cylinder and moves dirt upward onto a hinged chute, catching the material before it hits the ground. The chute device means that the material is dumped out of the way of the slipforming work and eliminates the need for manual removal of the soil. The unit can bore a hole in a matter of seconds and no excavated material falls back into the hole, leaving it clean for the slipform application. A stop rod is available to ensure hole depths are consistent and the standard auger has a diameter of 305mm although other sizes are available if required.
Using the system is straightforward as the trimmer runs as normal and allows the operator to drill the holes in a single pass. Once the holes have been bored, the machine can then slipform the foundation, filling the holes with concrete as it passes over them. The machine's vibrators consolidate and strengthen the concrete so that no voids are left in the concrete inside the pier holes. Once the mold has passed over each hole, a crew member inserts a tube into the pier. A steel post is then inserted into each tube, and the wire rope barrier can be strung between the posts.
Bar insertion system
Remote operation allows an operator to stand in the grade and out of jobsite traffic and commuter traffic if the drilling is along an open lane. Using a pointer the operator can align the drill unit for the next set of holes. According to Minnich, the alignment system allows the operator to move on down the slab and Bar insertion system continue drilling. The firm says that the operator is in a better location to position the drill and keep an eye on the hammers themselves. In addition, the operator has a better view of the individual drills and can make adjustments if there is any hang up. Each remote is programmed with its own radio ID code and each receiver is programmed only to respond to the remote with that code, so radio interference is not an issue. However, if the contractor is operating in an area where radio transmissions are not allowed, a cord can be attached between the remote and the receiver and it will work without broadcasting signals.
German concrete paving
CONTRACTOR
The paving work is taking place in two working shifts of 12 hours each and up to 700m of concrete pavement can be laid/shift. The machine is paving an 11.5m wide carriageway with a 210mm bottom concrete layer and a 60mm thick surface concrete layer. Washed concrete with a low noise surface texture is used for the 14km and dowel bars and tie bars are being inserted into the concrete automatically.
The SP1500L is a lightweight slipformer and for this job is being used in a paving train to install a twolayer concrete slab. The train comprises two machines that can move independently of one another and this feature ensures quick and easy transport, requiring relatively little disassembly, which has come in useful on this project as there are three bridges along the 14km route. A self-propelled, track-mounted TCM1600 texture curing machine follows behind the slipform paver train and this unit is equipped with an automatic spraying and sweeping system.
RSS