US contractor Conewago Enterprises is using a paver from Volvo CE to lay a roller-compacted concrete (RCC) surface at the Liberty Trust distribution centre in Shippensburg, Pennsylvania.
This facility lies close to Interstate-81, which runs through the Appalachian Mountains from the Canada-US border to Tennessee. This 1,376km route carries heavy truck traffic and as a result, hundreds of distribution warehouses have being constructed along the route of this busy transport corridor.
Conewago Enterpris
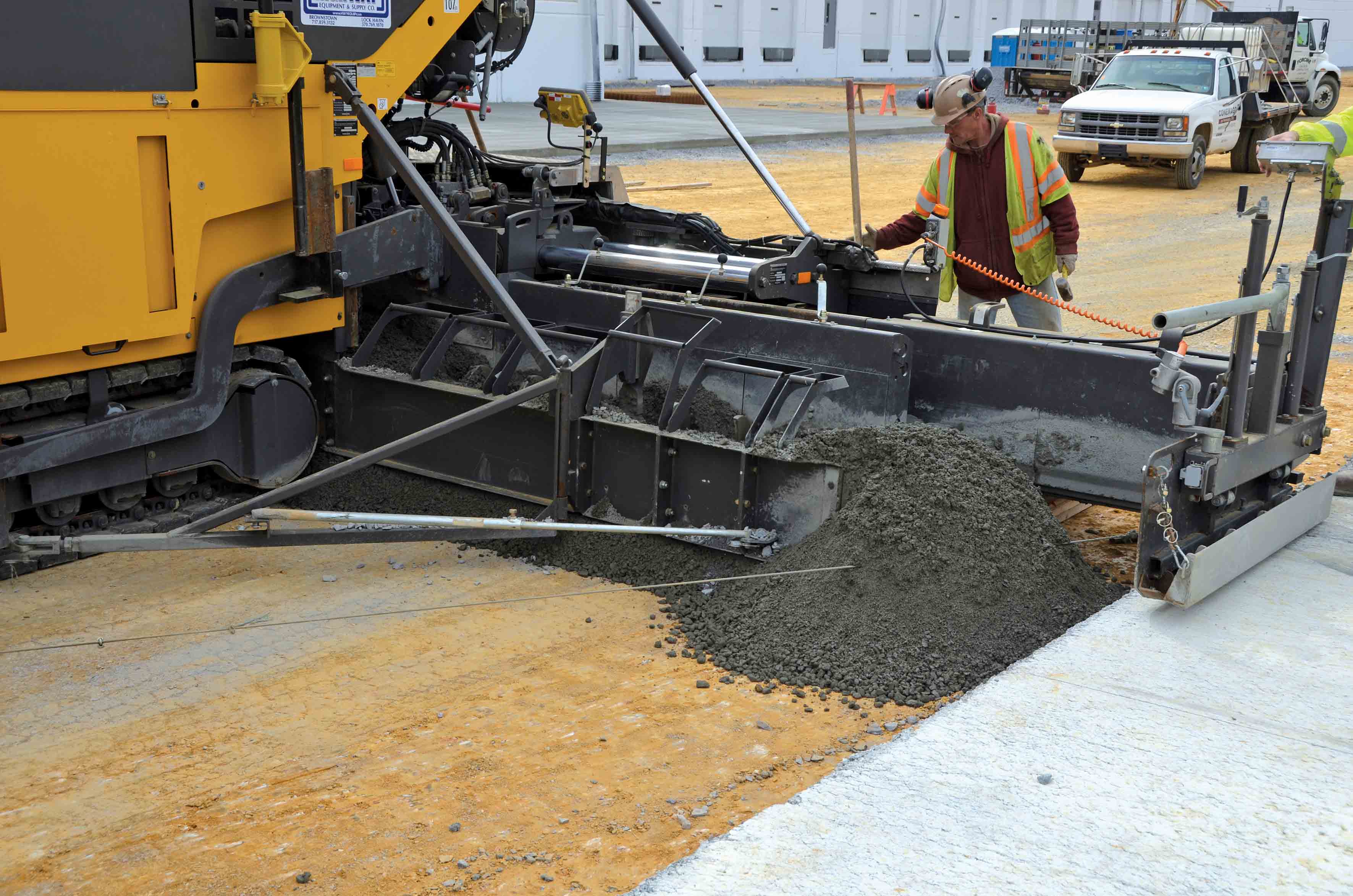
Volvo CE has supplied tamper bar-type pavers to the US for use in RCC paving
US contractor Conewago Enterprises is using a paver from 359 Volvo CE to lay a roller-compacted concrete (RCC) surface at the Liberty Trust distribution centre in Shippensburg, Pennsylvania.
This facility lies close to Interstate-81, which runs through the Appalachian Mountains from the Canada-US border to Tennessee. This 1,376km route carries heavy truck traffic and as a result, hundreds of distribution warehouses have being constructed along the route of this busy transport corridor.
Conewago Enterprises has been using modified asphalt pavers for laying RCC surfaces for some time, having first carried out trials with this technique 15 years ago. The company is now using a modified ABG7820C paver from Volvo CE as it suits the application and features a variable width screed and vibratory double tamping bar, allowing fast and efficient placement of the RCC surface.
Advantages of RCC are cost effectiveness, durability and the ability to work in poor soil conditions such as in the mid-Atlantic region. It is a combination of Portland cement, aggregate and water, which is classified as zero slump due its low water content. The RCC produces a rigid pavement, with clients seeing lifespans of more than 20 years. Because the application is similar to asphalt paving, it is applied with a conventional or high-density paver and the mix is compacted with vibratory steel or rubber-tyred rollers after placement.
Conewago initially tried laying the RCC using a standard asphalt paver working with conventional asphalt compactors. However, the results were not as good as hoped and the company then opted to use a European-style high-density pavers with dual tamper bar compaction instead.
The company opted for a Volvo ABG7820C paver, which offers a variable width screed that extends up to 9.1m. Coupled with its vibratory double tamping bar, this unit allows the firm to place material quickly while achieving compaction. The added paving width also eliminates the number of joints, which reduces long-term maintenance needs.
The quality of an RCC surface relates to its density and the industry standard is 98%. A double tamper bar type screed can deliver 90-95% compaction, reducing the rolling needed to reach the 98% target. The double tamper bar on the screed then strikes off the RCC material and gives it a smooth surface, and allows for additional compaction effort.
A known issue with RCC is its reputation for a rougher ride at speeds of 64km/h or more. But the Volvo ABG7820C is being used in conjunction with a Topcon Millimeter GPS grading control system to optimise smoothness. The pavers were supplied through Volvo Construction Equipment dealer, Highway Equipment & Supply Company, located in nearby Harrisburg.
However, there is further potential for the technique in the state as2535 Pennsylvania Department of Transportation (PennDOT) is showing strong interest. Conewago is working as part of a PennDOT pilot project to test RCC and traditional asphalt for a section of residential roadway in Adams County. While asphalt indexes are dropping in tandem with oil prices, Conewago expects demand for RCC to grow as more customers see its value.
This facility lies close to Interstate-81, which runs through the Appalachian Mountains from the Canada-US border to Tennessee. This 1,376km route carries heavy truck traffic and as a result, hundreds of distribution warehouses have being constructed along the route of this busy transport corridor.
Conewago Enterprises has been using modified asphalt pavers for laying RCC surfaces for some time, having first carried out trials with this technique 15 years ago. The company is now using a modified ABG7820C paver from Volvo CE as it suits the application and features a variable width screed and vibratory double tamping bar, allowing fast and efficient placement of the RCC surface.
Advantages of RCC are cost effectiveness, durability and the ability to work in poor soil conditions such as in the mid-Atlantic region. It is a combination of Portland cement, aggregate and water, which is classified as zero slump due its low water content. The RCC produces a rigid pavement, with clients seeing lifespans of more than 20 years. Because the application is similar to asphalt paving, it is applied with a conventional or high-density paver and the mix is compacted with vibratory steel or rubber-tyred rollers after placement.
Conewago initially tried laying the RCC using a standard asphalt paver working with conventional asphalt compactors. However, the results were not as good as hoped and the company then opted to use a European-style high-density pavers with dual tamper bar compaction instead.
The company opted for a Volvo ABG7820C paver, which offers a variable width screed that extends up to 9.1m. Coupled with its vibratory double tamping bar, this unit allows the firm to place material quickly while achieving compaction. The added paving width also eliminates the number of joints, which reduces long-term maintenance needs.
The quality of an RCC surface relates to its density and the industry standard is 98%. A double tamper bar type screed can deliver 90-95% compaction, reducing the rolling needed to reach the 98% target. The double tamper bar on the screed then strikes off the RCC material and gives it a smooth surface, and allows for additional compaction effort.
A known issue with RCC is its reputation for a rougher ride at speeds of 64km/h or more. But the Volvo ABG7820C is being used in conjunction with a Topcon Millimeter GPS grading control system to optimise smoothness. The pavers were supplied through Volvo Construction Equipment dealer, Highway Equipment & Supply Company, located in nearby Harrisburg.
However, there is further potential for the technique in the state as