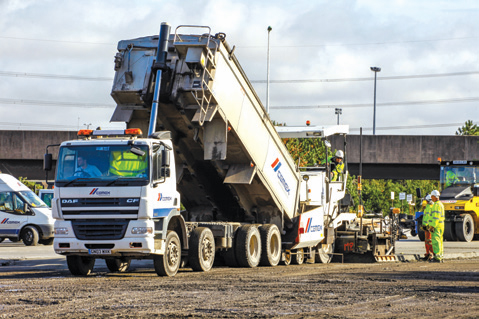
US contractor Robert Smith based in Chattanooga has long experience in the asphalt paving market but has recently added roller compacted concrete (RCC) to its paving portfolio. This heavy-duty cement mix can be poured as quickly as asphalt and the company has now developed its skills at laying large areas of RCC in just a few days for its industrial client base. Demand has grown and RCC work now accounts for over 90% of the firm’s workload, which it carries out using a Volvo CE paver.
One important job the firm had to carry out was to repave the Jack Daniels distillery site in Lynchburg, Tennessee, to deal with a major maintenance issue regarding its warehouse access roads. The asphalt roads were proving unable to cope with the weight of the heavily laden trucks carrying products to and from the warehouse. Using the Volvo CE ABG 7820 paver, the contractor was able to pave some 92m2/hour of concrete. This covered over 49,000m2 of new roads and stockyards, with a 130mm layer of the compacted concrete placed over 150mm of compacted aggregate base.
While
Demand for RCC is growing in the US, such as for sites where there are large numbers of heavy delivery vehicles. In Europe the RCC market has yet to develop, but The Concrete Centre in the UK believes that the benefits of this technique will see increasing use. The Concrete Centre is part of the
Originally developed in the 1970s, it is increasingly being viewed as an economic, long-term road surfacing material according to Minson. The RCC surfaces use cement, water and aggregates as with conventional concrete but feature drier mixes that are stiff enough to be compacted by vibratory rollers. This paving method needs no joints, dowels or steel reinforcement and needs no finishing.
Minson says that RCC combines the strength, long-term performance and minimal maintenance of conventional concrete with the ease of construction associated with asphalt paving. For roads RCC offers key advantages in that it can span localised soft subgrades, provide resistance to deformation under heavy concentrated loads and will not soften in high ambient temperatures.
Laying RCC is not complex and delivery requires large-capacity mixers to blend the material as it is transported to site and discharged into a modified asphalt paver. The machine places the materials in layers up to 250mm thick and 13m wide.
Compaction starts immediately after placement and continues until the pavement meets density requirements. Curing ensures a strong and durable pavement. Where appearance is important, joints can be saw-cut into the RCC to control crack location. If economy is more important than appearance, then the RCC can be allowed to crack naturally.
In the UK, RCC with induced cracking and binder/surface courses is increasingly being considered for truck lanes and highway widening projects, and as an alternative to fully flexible pavements.
The benefits of RCC have been underlined by research carried out at Sheffield University. There, researchers as part of the Ecolanes FP6 project have developed a RCC with recycled steel fibres from waste tyres that is 12% cheaper than conventional road construction and is 15% faster to construct. According to The Concrete Centre, RCC has significant potential as it is economical and fast to lay, has long-term performance with minimum maintenance, resists rutting and potholing and can use waste materials for its construction. In addition, at the end-of-life the material can be crushed and recycled for a new pavement.