Truly innovative is Roadtec’s Shuttle Buggy material transfer vehicle. John Irvine, President of Roadtec, explains how and why the ‘Buggy’ changed the game of asphalt paving
Road paving technology changed dramatically in the 1930s when the American inventor Harry Barber unveiled the very first asphalt paver. Barber was what we today would call a “game-changer”.
Innovations like Barber’s don’t come around often. In fact, decades can pass until another breakthrough product pushes the productivity and q
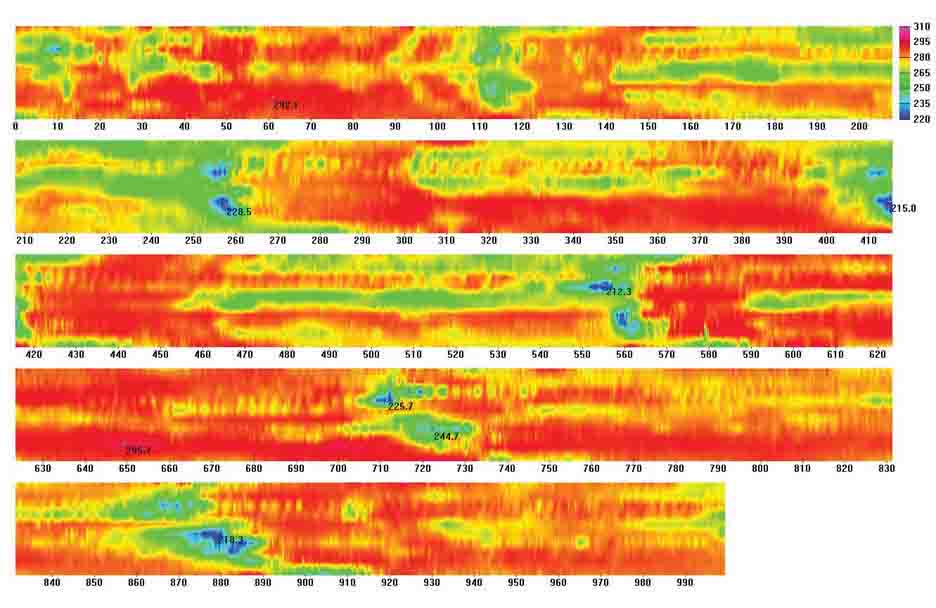
Infrared Data – 1,000ft. x 12ft. lane – Trucks dumping directly to paver. Cold spots (blue) at 130ft. intervals (truck ends)
Truly innovative is Roadtec’s Shuttle Buggy material transfer vehicle. John Irvine, President of Roadtec, explains how and why the ‘Buggy’ changed the game of asphalt paving
Road paving technology changed dramatically in the 1930s when the American inventor Harry Barber unveiled the very first asphalt paver. Barber was what we today would call a “game-changer”.
Innovations like Barber’s don’t come around often. In fact, decades can pass until another breakthrough product pushes the productivity and quality of the machines to new levels.
That was the case with Barber’s paver. His invention was a significant advance, yet subsequent years were spent mostly improving on what Barber had brought to the market.
That changed in 1989 when1252 Roadtec introduced the material transfer vehicle. The MTV “shuttled” asphalt between the haul truck and the paver – hence the name Shuttle Buggy. But was this new approach to paving simply an improvement of convenience or was it truly transformative?
The answer is the latter. MTVs proved to be such a dramatic advance that many government agencies in the US have written their use into specifications. Contractors around the world, too, see the value of these machines. They are in use virtually everywhere.
How did these MTVs change the industry and what are the benefits? And why would Harry Barber applaud their use?
A key Roadtec customer, APAC Paving, faced a difficult challenge in 1989. It had been hired to pave a test track for car manufacturer2728 Toyota in Georgetown, in the state of Kentucky. Because the track had to be extremely smooth, traditional end-dump paving methods just wouldn’t suffice.
There were the starts and stops and settling of the screed that could cause bumps. Connecting haul trucks with pavers was another trouble area. In addition, APAC wanted a way to load the paver from the side without trucks driving over the tack.
APAC needed a solution and they needed it quickly. Roadtec found one.
“The first Shuttle Buggy was built in six weeks,” said John Irvine, president of Roadtec.
“It was a prototype and developed for that Toyota test track project.”
The focus was continuous, non-contact paving and the Shuttle Buggy excelled. “Roadtec management knew they had something special,” Irvine said. In 1989, a patent was secured for the method as well as the “apparatus” – the Shuttle Buggy.
Roadtec quickly realised the process had another benefit: It remixed the material to keep temperatures consistent and reduce thermal segregation. While this had not been part of the original focus, it was a significant benefit.
The next step in the development of the Shuttle Buggy was to upgrade the design of the original auger to improve the mixing capability and keep temperatures even more consistent. A patent on that remixing process was awarded in 1991.
The key is the uniform remixing auger. The auger uses three pitches in which each becomes larger as they move toward the centre of the MTV. This is called “triple-pitch flighting”. Essential to the concept is the entry of new material into the auger area each time the pitch is increased. This creates more thorough remixing.
The original mixer had pulled material mostly from the side of the Shuttle Buggy hopper where the mix tends to be cooler. The new patented remixing process provided a more even blend. It also eliminated the cool top crust that could be tracked all the way through the process and out the back end of the paver where a trouble spot would be left behind.
“The remixing process eliminated thermal segregation,” Irvine said. It also remixed sizes, so larger rocks were blended with smaller material, such as sand.
Costs associated with thermal segregation are enormous. Contractors have a hard time reaching compaction and smoothness goals when working on mix that has cooled. Despite their best efforts, contractors end up wasting compaction passes – and the fuel, labour and machine wear that go with them. Often, those extra passes aren’t enough; the goals simply can’t be met because of the cool mix. The consequences are high in terms of penalties and missed bonuses for contractors.
Compaction density also is essential to road life. If air voids in asphalt can be kept to between 4-6%, there is little or no water penetration, so roads are not prone to damage from freeze-thaw cycles.
This is not just speculation. Roadtec and others in the industry have conducted exhaustive research that shows new pavements with increased smoothness and densities have lower average maintenance costs in the 10 years after construction. The impact on the infrastructure can’t be overstated, as money saved on maintenance can instead be used to build new roads.
Irvine said there is substantial research on the effectiveness of the Shuttle Buggy – particularly in terms of combatting thermal segregation – because the machines have been around since 1989. “It’s been a long time now,” he said. “We’ve been able to prove that, over time, roads last 20-25% longer if they’re smooth and achieve proper densification throughout the mat.”
Efficient use of haul trucks is a key benefit provided by the Shuttle Buggy. MTVs can store as much as 25tons - just under 23tonnes - in their hoppers. That means trucks can arrive, deposit their loads and return to the plant. The trucks do not have to wait for the paver to be ready to accept their mix. The mix doesn’t cool while the trucks wait either.
The cost savings are considerable. Roadtec researchers determined that a wait time of more than 15 minutes per truck is common at job sites that don’t use a Shuttle Buggy MTV.
“A very conservative cost of US$1 per minute of truck time means an extra $15 paid for each truck every time it’s delayed 15 minutes,” which can quickly add up, the research shows. “With a Shuttle Buggy MTV, trucks can be unloaded much quicker, typically in a quarter of the time. On-site mix storage and then pickup by the Buggy is another possibility. All these efficiencies can result either in the need for fewer trucks or increased production.”
In addition to these time- and money-saving capabilities, the Shuttle Buggy provides a multitude of other benefits.
The Shuttle Buggy conveyor and its side discharge also means trucks can deliver mix without driving on a milled edge or tack coat. Projects that require string lines on both sides, such as high-banked racetracks or airports, are completed much more easily.
At intersections, work is typically slow and getting trucks to the paver is often difficult. The Shuttle Buggy improves paver manoeuvrability at intersections by essentially “untethering” the pavers from trucks.
Sometimes a paver simply can’t reach a spot, making handwork necessary. A Shuttle Buggy is able to precisely dispense material to workers by lowering the discharge conveyor which can pivot from side to side.
The best technology in the world is useless if an employee finds the machine too complicated to operate or understand. A Shuttle Buggy is an intuitive, easy-to-operate machine. Also, if the machine doesn’t work, what good is the technology? MTVs certainly lead a tough life – they cycle tonnes of abrasive materials every working day.
Roadtec’s heavy-duty design keeps machines working longer while lowering maintenance and operating costs. Irvine said many recent Shuttle Buggy advances centre on extended machine life. Larger chains, taller slats, increased bearing and sprocket sizes and other adjustments all extend life.
The benefits add up for contractors. “Eventually, the Shuttle Buggy pays for itself in terms of penalties avoided, reduced trucking costs, bonuses paid for densities and elimination of thermal segregation,” Irvine said.
It uses patented technology to solve a key problem for paving contractors. It leaves behind considerably smoother and optimally compacted mats that extend the life of roads. It helps contractors reach their goals and maximise their profits.
Those are advances that Harry Barber would undoubtedly appreciate.
Astec’s really cool solution to a hot problem
In the asphalt plant world, few products have proved more innovative than1250 Astec’s Double Barrel Drum Dryer/Mixer. Key to the Double Barrel product is its ability to use high percentages of recycled asphalt pavement (RAP) without damaging the RAP bitumen.
The cost savings that result from using RAP are considerable, so there is certainly incentive to use it. However, utilising high levels of recycled materials can be difficult.
The challenge results from the bitumen that coats RAP. It can be damaged at temperatures in the presence of oxygen. Heating RAP to mix temperature (150° C) is accomplished by mixing cold wet RAP with aggregate heated to temperatures higher than 150° C.
That was the challenge Astec faced: how to reach the desired final mix temperature without damaging the bitumen on the RAP. The answer provided by Astec engineers was the Double Barrel Drum Dryer/Mixer.
The first “barrel” is a rotating counterflow drum while the second is a slightly larger fixed casing that wraps around that drum. Mixing occurs in the space between the first barrel (the drum/dryer) and the second barrel (the outer casing).
Here is a closer look at the process: virgin aggregate is heated and dried in the first drum – the first barrel. The temperature here can be very hot as it carries the entirety of the heat for the mix. Next, the heated virgin material drops through openings into space between the first and second barrel.
The hot virgin material and cold RAP mix together gently creating a protective blanket of steam so as not to damage the bitumen on the RAP as it heats up. Once the mixture of RAP and virgin material is homogenous, liquid AC is added. The core of this patented process remains the foundation of the Double Barrel system, but there have been improvements and options added since its launch in 1986.
Those options include high-RAP and extended versions. The traditional Double Barrel Drum Dryer/Mixer can use 50% RAP, while more specialised double barrel mixers can use up to 70% RAP.
It is also worth noting the improved fuel economy of the Double Barrel system. Heat that is “lost” from the first barrel (the drum/dryer) actually helps heat the second barrel, providing fuel efficiency as well.
Road paving technology changed dramatically in the 1930s when the American inventor Harry Barber unveiled the very first asphalt paver. Barber was what we today would call a “game-changer”.
Innovations like Barber’s don’t come around often. In fact, decades can pass until another breakthrough product pushes the productivity and quality of the machines to new levels.
That was the case with Barber’s paver. His invention was a significant advance, yet subsequent years were spent mostly improving on what Barber had brought to the market.
That changed in 1989 when
The answer is the latter. MTVs proved to be such a dramatic advance that many government agencies in the US have written their use into specifications. Contractors around the world, too, see the value of these machines. They are in use virtually everywhere.
How did these MTVs change the industry and what are the benefits? And why would Harry Barber applaud their use?
Birth of the ‘Buggy’
Roadtec prides itself on its entrepreneurial spirit. That was the case in 1989 and remains a company philosophy to this day. There is freedom to think creatively – and take some chances, too.A key Roadtec customer, APAC Paving, faced a difficult challenge in 1989. It had been hired to pave a test track for car manufacturer
There were the starts and stops and settling of the screed that could cause bumps. Connecting haul trucks with pavers was another trouble area. In addition, APAC wanted a way to load the paver from the side without trucks driving over the tack.
APAC needed a solution and they needed it quickly. Roadtec found one.
“The first Shuttle Buggy was built in six weeks,” said John Irvine, president of Roadtec.
“It was a prototype and developed for that Toyota test track project.”
The focus was continuous, non-contact paving and the Shuttle Buggy excelled. “Roadtec management knew they had something special,” Irvine said. In 1989, a patent was secured for the method as well as the “apparatus” – the Shuttle Buggy.
Roadtec quickly realised the process had another benefit: It remixed the material to keep temperatures consistent and reduce thermal segregation. While this had not been part of the original focus, it was a significant benefit.
The next step in the development of the Shuttle Buggy was to upgrade the design of the original auger to improve the mixing capability and keep temperatures even more consistent. A patent on that remixing process was awarded in 1991.
The key is the uniform remixing auger. The auger uses three pitches in which each becomes larger as they move toward the centre of the MTV. This is called “triple-pitch flighting”. Essential to the concept is the entry of new material into the auger area each time the pitch is increased. This creates more thorough remixing.
The original mixer had pulled material mostly from the side of the Shuttle Buggy hopper where the mix tends to be cooler. The new patented remixing process provided a more even blend. It also eliminated the cool top crust that could be tracked all the way through the process and out the back end of the paver where a trouble spot would be left behind.
“The remixing process eliminated thermal segregation,” Irvine said. It also remixed sizes, so larger rocks were blended with smaller material, such as sand.
Segregation problem
Thermal segregation has been an issue since before Harry Barber introduced the asphalt paver. It’s a significant problem with costly consequences. It weakens the structure of asphalt pavements. Virtually all paving problems – cracking, raveling, stripping and rutting – result from segregation.Costs associated with thermal segregation are enormous. Contractors have a hard time reaching compaction and smoothness goals when working on mix that has cooled. Despite their best efforts, contractors end up wasting compaction passes – and the fuel, labour and machine wear that go with them. Often, those extra passes aren’t enough; the goals simply can’t be met because of the cool mix. The consequences are high in terms of penalties and missed bonuses for contractors.
Compaction density also is essential to road life. If air voids in asphalt can be kept to between 4-6%, there is little or no water penetration, so roads are not prone to damage from freeze-thaw cycles.
This is not just speculation. Roadtec and others in the industry have conducted exhaustive research that shows new pavements with increased smoothness and densities have lower average maintenance costs in the 10 years after construction. The impact on the infrastructure can’t be overstated, as money saved on maintenance can instead be used to build new roads.
Irvine said there is substantial research on the effectiveness of the Shuttle Buggy – particularly in terms of combatting thermal segregation – because the machines have been around since 1989. “It’s been a long time now,” he said. “We’ve been able to prove that, over time, roads last 20-25% longer if they’re smooth and achieve proper densification throughout the mat.”
Fewer trucks
The MTV process improves consistency on many fronts. That consistency, in turn, adds efficiencies that provide cost savings beyond segregation improvements.Efficient use of haul trucks is a key benefit provided by the Shuttle Buggy. MTVs can store as much as 25tons - just under 23tonnes - in their hoppers. That means trucks can arrive, deposit their loads and return to the plant. The trucks do not have to wait for the paver to be ready to accept their mix. The mix doesn’t cool while the trucks wait either.
The cost savings are considerable. Roadtec researchers determined that a wait time of more than 15 minutes per truck is common at job sites that don’t use a Shuttle Buggy MTV.
“A very conservative cost of US$1 per minute of truck time means an extra $15 paid for each truck every time it’s delayed 15 minutes,” which can quickly add up, the research shows. “With a Shuttle Buggy MTV, trucks can be unloaded much quicker, typically in a quarter of the time. On-site mix storage and then pickup by the Buggy is another possibility. All these efficiencies can result either in the need for fewer trucks or increased production.”
In addition to these time- and money-saving capabilities, the Shuttle Buggy provides a multitude of other benefits.
The game is changed
The ability to avoid obstructions is one benefit, such as islands and peninsulas in parking areas. Overhead power lines, tunnels, overpasses and other obstructions can present challenges, too. In these circumstances, a typical haul truck cannot reach the paver. But with a Shuttle Buggy, the problem is solved. The truck meets the Shuttle Buggy at a convenient spot to unload, then the Buggy MTV delivers the mix to the paver.The Shuttle Buggy conveyor and its side discharge also means trucks can deliver mix without driving on a milled edge or tack coat. Projects that require string lines on both sides, such as high-banked racetracks or airports, are completed much more easily.
At intersections, work is typically slow and getting trucks to the paver is often difficult. The Shuttle Buggy improves paver manoeuvrability at intersections by essentially “untethering” the pavers from trucks.
Sometimes a paver simply can’t reach a spot, making handwork necessary. A Shuttle Buggy is able to precisely dispense material to workers by lowering the discharge conveyor which can pivot from side to side.
The best technology in the world is useless if an employee finds the machine too complicated to operate or understand. A Shuttle Buggy is an intuitive, easy-to-operate machine. Also, if the machine doesn’t work, what good is the technology? MTVs certainly lead a tough life – they cycle tonnes of abrasive materials every working day.
Roadtec’s heavy-duty design keeps machines working longer while lowering maintenance and operating costs. Irvine said many recent Shuttle Buggy advances centre on extended machine life. Larger chains, taller slats, increased bearing and sprocket sizes and other adjustments all extend life.
The benefits add up for contractors. “Eventually, the Shuttle Buggy pays for itself in terms of penalties avoided, reduced trucking costs, bonuses paid for densities and elimination of thermal segregation,” Irvine said.
Game-changer or not
Is the Shuttle Buggy a “game-changer” in the truest sense of the term? The answer is yes.It uses patented technology to solve a key problem for paving contractors. It leaves behind considerably smoother and optimally compacted mats that extend the life of roads. It helps contractors reach their goals and maximise their profits.
Those are advances that Harry Barber would undoubtedly appreciate.
Astec’s really cool solution to a hot problem
In the asphalt plant world, few products have proved more innovative than
The cost savings that result from using RAP are considerable, so there is certainly incentive to use it. However, utilising high levels of recycled materials can be difficult.
The challenge results from the bitumen that coats RAP. It can be damaged at temperatures in the presence of oxygen. Heating RAP to mix temperature (150° C) is accomplished by mixing cold wet RAP with aggregate heated to temperatures higher than 150° C.
That was the challenge Astec faced: how to reach the desired final mix temperature without damaging the bitumen on the RAP. The answer provided by Astec engineers was the Double Barrel Drum Dryer/Mixer.
The first “barrel” is a rotating counterflow drum while the second is a slightly larger fixed casing that wraps around that drum. Mixing occurs in the space between the first barrel (the drum/dryer) and the second barrel (the outer casing).
Here is a closer look at the process: virgin aggregate is heated and dried in the first drum – the first barrel. The temperature here can be very hot as it carries the entirety of the heat for the mix. Next, the heated virgin material drops through openings into space between the first and second barrel.
The hot virgin material and cold RAP mix together gently creating a protective blanket of steam so as not to damage the bitumen on the RAP as it heats up. Once the mixture of RAP and virgin material is homogenous, liquid AC is added. The core of this patented process remains the foundation of the Double Barrel system, but there have been improvements and options added since its launch in 1986.
Those options include high-RAP and extended versions. The traditional Double Barrel Drum Dryer/Mixer can use 50% RAP, while more specialised double barrel mixers can use up to 70% RAP.
It is also worth noting the improved fuel economy of the Double Barrel system. Heat that is “lost” from the first barrel (the drum/dryer) actually helps heat the second barrel, providing fuel efficiency as well.