Mention the letters MTV and most people will think you’re referring to Music Television, the firm that revolutionised the music video. But in the road construction sector the letters have another meaning: Material Transfer Vehicle.
Roadtec pioneered the MTV concept with its Shuttle Buggy, which it introduced in 1989. The concept was a novel one, providing a transition between the truck hauling the asphalt to the site and the asphalt paver. The idea of the machine was that it would provide a buffer system
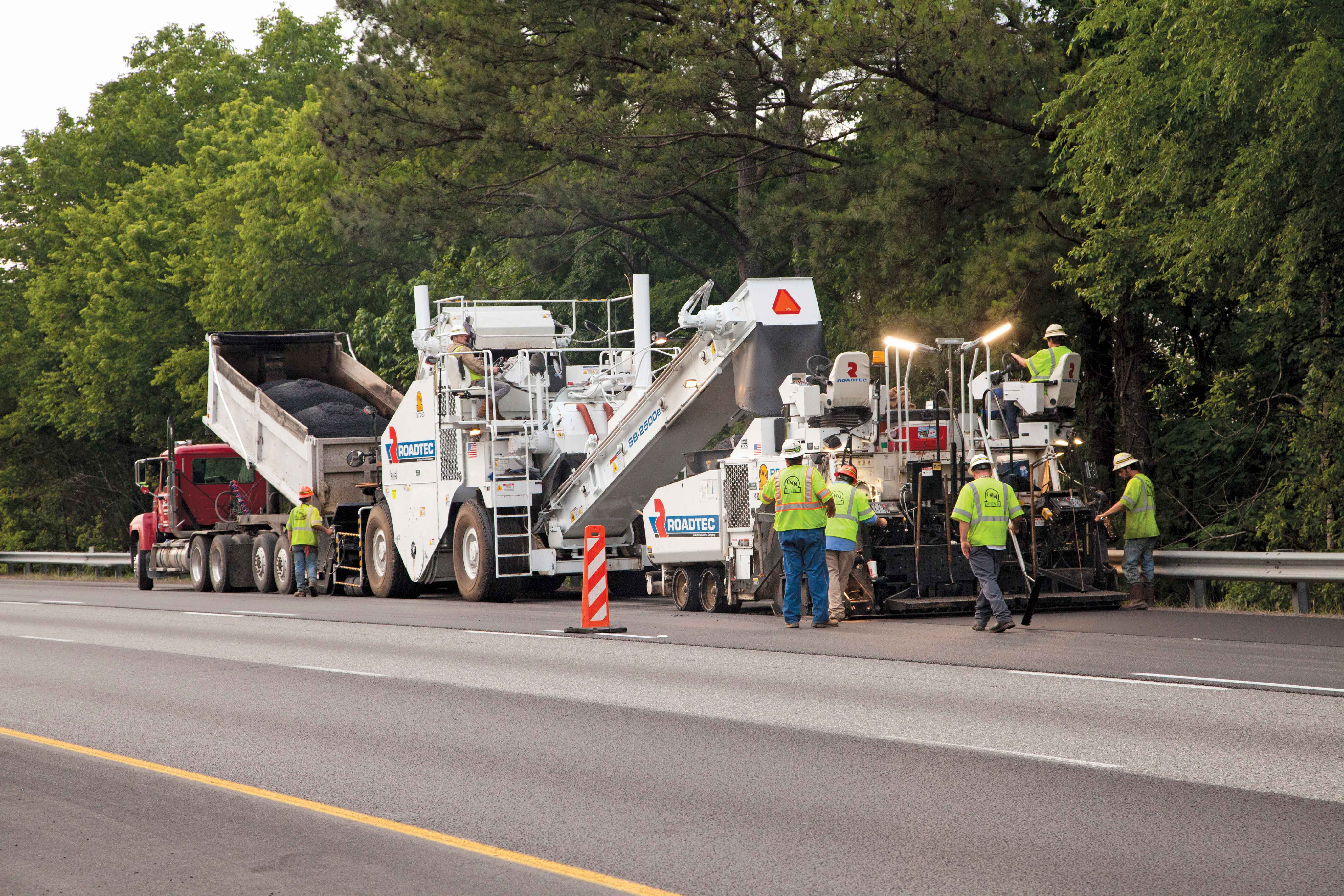
The Shuttle Buggy has been developed significantly since its original launch, with this recent model being used for paving on I-75 in Ringgold, Georgia
Mention the letters MTV and most people will think you’re referring to Music Television, the firm that revolutionised the music video. But in the road construction sector the letters have another meaning: Material Transfer Vehicle.
1252 Roadtec pioneered the MTV concept with its Shuttle Buggy, which it introduced in 1989. The concept was a novel one, providing a transition between the truck hauling the asphalt to the site and the asphalt paver. The idea of the machine was that it would provide a buffer system with extra capacity between the truck and the paver and allow a more continuous flow of material through to the screed. Because the machine was designed with a remixing capability, this also helped to prevent any material segregation within the mix, as well as ensuring a more homogenous mat temperature behind the screed.
There has been some discussion as to whether too much remixing could increase oxidation of the asphalt. However, roads that have been constructed with the use of a Shuttle Buggy as part of the paving train have performed better in terms of ageing than those built using trucks tipping directly into the pavers.
Providing a more continuous flow of material to the paver and improving the mat homogeneity are important points as these reduce the potential for cold spots in the mat that can be hard to compact and result in early failure. On some roads paved without an MTV, it is even possible to detect where the end of each truck load has passed through the screed. This can result in a cold spot that does not compact correctly leaving a ‘truck bump’ that a driver will feel as the vehicle passes over the top.
Using an MTV allows the supply trucks to fully unload and return to the asphalt plant, which also helps with logistics and overall efficiency. Contractors typically employ MTVs as part of the paving train on larger paving jobs for dual carriageways or highways or well as airport runways, where continuity and high paving quality are required.
Since that time, the Shuttle Buggy has become an enormous success for Roadtec, now selling in large numbers right across the globe, and even being written into the specifications for high-speed highway construction in some markets. The machine has also been upgraded numerous times, benefiting from advances in diesel technology as well as materials, with longer lasting wear materials, while its remixing capability has also been improved.
However, given the success of the Shuttle Buggy and its popularity with contractors, other manufacturers soon took note. Rival firms quickly realised the potential for an MTV in optimising paving quality, developing their own designs as a result. These too have since gone through several generations of improvements, offering greater throughput and capacity and also benefiting from the latest advances in engine technology. Customers now have a wider range of MTVs to choose from than ever before.
But not all MTVs are the same. In fact, many of the models on the market have been developed from different concepts and to meet slightly different needs.
The recently introduced172 BOMAG and 206 Dynapac machines for example are more compact units and resemble pavers that have had their screeds removed and bigger hoppers fitted instead.
7985 Atlas Copco Dynapac’s MF2500CS uses a lot of paver components in its construction and is said to offer high throughput on its compact chassis. The company says that its compact MTV should be easier to transport than its rivals while still provide high materials throughput. Equipped with a high performance conveying system, the firm claims that the machine can empty a full truck load in less than 35 seconds. The 2.55m wide feeder is said to be cost-effective to transport, while operating costs are low, and reliability and serviceability high.
Equipped as standard with a short conveyor, the Dynapac MF2500CS mobile feeder can also be fitted with an optional Swingapp. This allows the machine to be used for offset feeding application, feeding two pavers side by side, feeding one paver from a different lane or for filling medians. This offset conveyor can swing 55° to both sides and can be fitted to any Dynapac MF2500CS model. It features a quick-mount device that boosts versatility and the company claims the unit can be fitted or removed in 45 minutes.
The machine is driven by a196 Cummins diesel rated at 170kW and which has a thermostatic fan control that provides efficient cooling as well as sophisticated hydraulics to help optimise fuel efficiency.
BOMAG is offering its BMF 2500 feeder in three different versions, although they are all said to feature high output and compact design. These models can each handle a 27tonne truck-load of material in just 35 seconds, while the 2.55m width of BOMAG’s BMF 2500 is the same as the rival161 Atlas Copco Dynapac MF2500CS and both are narrow enough for transport without a special permit.
The conveyor belt on the Bomag BMF 2500 feeder has a width of 1.2m and is said to allow optimum material flow with minimal segregation. In addition, the rubber belt is mounted on metal struts. The BMF 2500 has a large material hopper with individually controllable wings for quick discharge and slewing bumper rollers to safely dock the supply truck. The BMF 2500 S base model can be upgraded with a slewable offset belt, allowing lateral feeding to supply two pavers. However, the BMF 2500 S Offset offers the slewable offset conveyor belt as standard. And the BMF 2500 M has a longer, height-adjustable conveyor belt and is designed to feed extra capacity paver hoppers with higher sides.
As mentioned earlier, Roadtec’s Shuttle Buggy has been upgraded numerous times in the years since its initial launch with the firm now offering the SB-2500e/ex model. A key feature of the machine is its patented, triple-pitch auger, mounted at the bottom of the hopper. This remixes materials right across the width of the hopper, preventing material segregation by size. The auger also breaks up any colder lumps and allows for an even temperature gradient, ensuring homogeneity. A slat conveyor runs from the bottom of the hopper and feeds the discharge conveyor. The machine’s front hopper has a steep slope and a vibrating bottom plate, which are designed to prevent material build-up. Heavy-duty, swivelling support casters under the hopper are said to assure smooth movement. Operators can adjust the hopper position from either of two separate control boxes. They can also adjust the position of the push roller for different truck designs. An optional windrow pickup head is available.
Recent versions of the Shuttle Buggy have benefited from improvements in materials technology, with longer lasting wear materials now used for the auger and many internal components. The auger diameter has also been increased in size for the more recent versions to boost its remixing capability. The conveyors also have longer lasting components and are wider, allowing greater materials handling capability.
The machine can unload a truck at a rate of up to 907tonnes/hour and then deliver the asphalt to the paver behind at 544tonnes/hour. The SB-2500e is powered by a 224kW Cummins QSL 9 diesel that meets the latest emissions requirements. It has a two-speed hydrostatic drive for operation and travel, offering continuously variable speeds. The machine runs on high flotation tyres and is controlled by a steering wheel that guides the front wheels of the all-wheel drive machines.
Designed to optimise throughput, the MT 3000-2i from1194 Vögele is now available with an Offset PowerFeeder version. This highly productive material transfer vehicle helps ensure homogeneity and quality in high output paving operations such as for highways. Its large hopper and innovative conveying system are key features that allow a 35tonne storage capacity and high throughput, with a grating system in the receiving hopper to break up any congealed chunks of material. Its maximum conveying capacity is 1,200tonnes/hour, allowing the machine to handle the full load from a 25tonne capacity asphalt delivery truck in just 60 seconds.
With its 55° right- and left-hand offset capability, the machine offers high versatility and increases the range of applications for the contractor. The maximum distance from the outside edge of the material feeder to the centre of the discharge point is 3.5m. The machine is equipped with the firm’s well proven ErgoPlus operating system, as well as an automatic distance control and an anti-collision package.
The firm says that the maximum distance from the outside edge of the material feeder to the centre of the discharge point is 3.5m, while the conveyor can be raised by up to 23° from the horizontal to a discharge height of 3.9m. This allows the machine to feed pavers working in echelon from the side, or for backfilling trenches or filling median strips between safety barriers on dual carriageway or highway projects. The machine can also be used for paving shoulders and other hard-to-reach areas. Further increasing the versatility, the conveying concept can also base course material, recycled materials and even topsoil.
The machine has a trough-shaped conveyor belt that centres material during transfer as well as tensioning cylinders that guide the belt and ensure alignment and an automatic system to adjust belt tension. An option is the conical augers to mix the material in the receiving hopper, helping to minimise segregation and also ensure a more homogenous temperature across the mat. Diesel heating with non-contact infrared panels ensures the temperature of the conveyor belt is optimised.
Power comes from a201 Deutz diesel rated at 160kW and which meets Tier 4 Final emissions requirements and weighing close to 26tonnes, the machine is said to be easy to transport. The machine has been designed particularly for customers in the US and Australia that require high throughput but could also suit duties with contractors elsewhere in the world working on large highway projects that require the offset capability.
Of the rival machines, Weiler’s E2850 MTV is also a wheel-mounted and is powered by a178 Caterpillar C9 diesel rated at 224kW. Weighing nearly 34tonnes the machine features four-wheel and optional rear wheel steering as well as a three-speed hydrostatic drive system with variable speeds. It has an asphalt capacity of 22.5tonnes, although the customer can install a hopper insert to boost capacity by 5tonnes. It has hydraulically-operated clean-out doors on the dump hopper, storage hopper and rear conveyor to make the clean out process easier. The machine has high torque, direct drive motors with loop flush cooling system on its two conveyors and elevator, helping to reduce heat build-up during operation. The machine is also equipped with a fumes extraction system that is designed to be folded away when the machine passes underneath an overhead obstruction. The Weiler 2850 is sold and serviced through the Caterpillar dealer network for North America.
There has been some discussion as to whether too much remixing could increase oxidation of the asphalt. However, roads that have been constructed with the use of a Shuttle Buggy as part of the paving train have performed better in terms of ageing than those built using trucks tipping directly into the pavers.
Providing a more continuous flow of material to the paver and improving the mat homogeneity are important points as these reduce the potential for cold spots in the mat that can be hard to compact and result in early failure. On some roads paved without an MTV, it is even possible to detect where the end of each truck load has passed through the screed. This can result in a cold spot that does not compact correctly leaving a ‘truck bump’ that a driver will feel as the vehicle passes over the top.
Using an MTV allows the supply trucks to fully unload and return to the asphalt plant, which also helps with logistics and overall efficiency. Contractors typically employ MTVs as part of the paving train on larger paving jobs for dual carriageways or highways or well as airport runways, where continuity and high paving quality are required.
Since that time, the Shuttle Buggy has become an enormous success for Roadtec, now selling in large numbers right across the globe, and even being written into the specifications for high-speed highway construction in some markets. The machine has also been upgraded numerous times, benefiting from advances in diesel technology as well as materials, with longer lasting wear materials, while its remixing capability has also been improved.
However, given the success of the Shuttle Buggy and its popularity with contractors, other manufacturers soon took note. Rival firms quickly realised the potential for an MTV in optimising paving quality, developing their own designs as a result. These too have since gone through several generations of improvements, offering greater throughput and capacity and also benefiting from the latest advances in engine technology. Customers now have a wider range of MTVs to choose from than ever before.
But not all MTVs are the same. In fact, many of the models on the market have been developed from different concepts and to meet slightly different needs.
The recently introduced
Equipped as standard with a short conveyor, the Dynapac MF2500CS mobile feeder can also be fitted with an optional Swingapp. This allows the machine to be used for offset feeding application, feeding two pavers side by side, feeding one paver from a different lane or for filling medians. This offset conveyor can swing 55° to both sides and can be fitted to any Dynapac MF2500CS model. It features a quick-mount device that boosts versatility and the company claims the unit can be fitted or removed in 45 minutes.
The machine is driven by a
BOMAG is offering its BMF 2500 feeder in three different versions, although they are all said to feature high output and compact design. These models can each handle a 27tonne truck-load of material in just 35 seconds, while the 2.55m width of BOMAG’s BMF 2500 is the same as the rival
The conveyor belt on the Bomag BMF 2500 feeder has a width of 1.2m and is said to allow optimum material flow with minimal segregation. In addition, the rubber belt is mounted on metal struts. The BMF 2500 has a large material hopper with individually controllable wings for quick discharge and slewing bumper rollers to safely dock the supply truck. The BMF 2500 S base model can be upgraded with a slewable offset belt, allowing lateral feeding to supply two pavers. However, the BMF 2500 S Offset offers the slewable offset conveyor belt as standard. And the BMF 2500 M has a longer, height-adjustable conveyor belt and is designed to feed extra capacity paver hoppers with higher sides.
As mentioned earlier, Roadtec’s Shuttle Buggy has been upgraded numerous times in the years since its initial launch with the firm now offering the SB-2500e/ex model. A key feature of the machine is its patented, triple-pitch auger, mounted at the bottom of the hopper. This remixes materials right across the width of the hopper, preventing material segregation by size. The auger also breaks up any colder lumps and allows for an even temperature gradient, ensuring homogeneity. A slat conveyor runs from the bottom of the hopper and feeds the discharge conveyor. The machine’s front hopper has a steep slope and a vibrating bottom plate, which are designed to prevent material build-up. Heavy-duty, swivelling support casters under the hopper are said to assure smooth movement. Operators can adjust the hopper position from either of two separate control boxes. They can also adjust the position of the push roller for different truck designs. An optional windrow pickup head is available.
Recent versions of the Shuttle Buggy have benefited from improvements in materials technology, with longer lasting wear materials now used for the auger and many internal components. The auger diameter has also been increased in size for the more recent versions to boost its remixing capability. The conveyors also have longer lasting components and are wider, allowing greater materials handling capability.
The machine can unload a truck at a rate of up to 907tonnes/hour and then deliver the asphalt to the paver behind at 544tonnes/hour. The SB-2500e is powered by a 224kW Cummins QSL 9 diesel that meets the latest emissions requirements. It has a two-speed hydrostatic drive for operation and travel, offering continuously variable speeds. The machine runs on high flotation tyres and is controlled by a steering wheel that guides the front wheels of the all-wheel drive machines.
Designed to optimise throughput, the MT 3000-2i from
With its 55° right- and left-hand offset capability, the machine offers high versatility and increases the range of applications for the contractor. The maximum distance from the outside edge of the material feeder to the centre of the discharge point is 3.5m. The machine is equipped with the firm’s well proven ErgoPlus operating system, as well as an automatic distance control and an anti-collision package.
The firm says that the maximum distance from the outside edge of the material feeder to the centre of the discharge point is 3.5m, while the conveyor can be raised by up to 23° from the horizontal to a discharge height of 3.9m. This allows the machine to feed pavers working in echelon from the side, or for backfilling trenches or filling median strips between safety barriers on dual carriageway or highway projects. The machine can also be used for paving shoulders and other hard-to-reach areas. Further increasing the versatility, the conveying concept can also base course material, recycled materials and even topsoil.
The machine has a trough-shaped conveyor belt that centres material during transfer as well as tensioning cylinders that guide the belt and ensure alignment and an automatic system to adjust belt tension. An option is the conical augers to mix the material in the receiving hopper, helping to minimise segregation and also ensure a more homogenous temperature across the mat. Diesel heating with non-contact infrared panels ensures the temperature of the conveyor belt is optimised.
Power comes from a
Of the rival machines, Weiler’s E2850 MTV is also a wheel-mounted and is powered by a