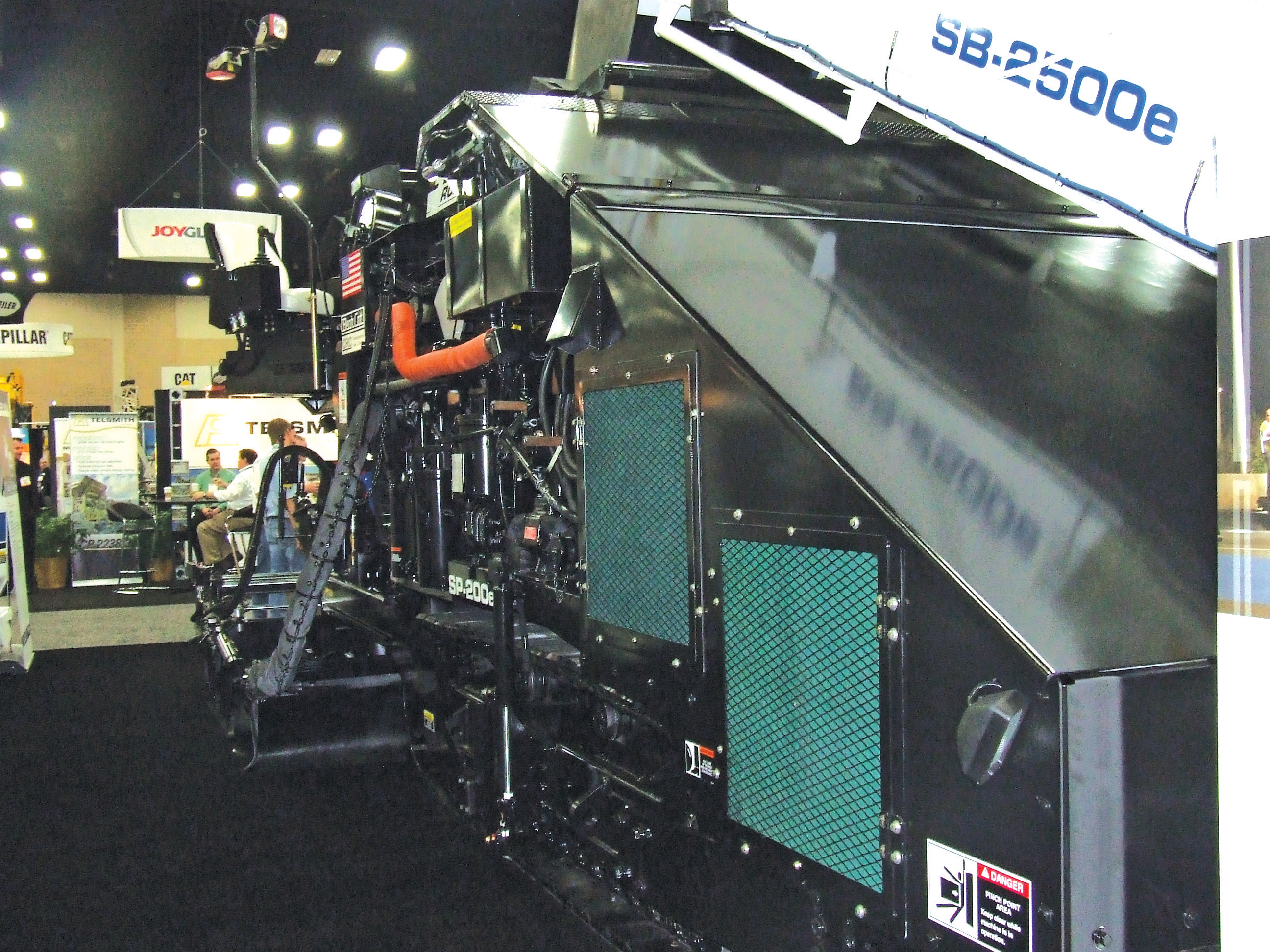
New developments are coming to market for US style, high production pavers while material transfer vehicles are also evolving – Mike Woof reports
Paving machines vary considerably in North America compared with those units used elsewhere. On a worldwide basis, pavers with tamper bar screeds are popular having been developed in Europe and also favoured by Japanese and Chinese firms. But in the US the length of highways to be constructed resulted in a focus on high production pavers, which still continues today. North America and Latin America are key markets for these machines, with Australia being one of the few territories to employ both European and US-style paving equipment.At the World of Asphalt event in San Antonio, Texas, several manufacturers rolled out new pavers aimed at the North American and Latin American markets. These included small pavers and also new highway class machines. Another development comes with the introduction of improved material transfer vehicles. Although these were developed in the US initially to meet the demand of the high production North American paving operations, they are attracting customers on a global basis too and customers also have a wider choice of machines than in the past. For large paving projects in particular, global customers have recognised the benefits these machines offer in terms of more homogenous mixing, reduced material segregation, better temperature gradients and more continuous material flow both into and through the paver.
Of note for the market in US pavers and also material feeders is the fact that the Cedarapids brand machines formerly owned by
Somewhat smaller in size is the new CP100 paver from
The machine is fitted with Carlson’s own EZ-RZ-10 rear mount screed and the CP100 replaces a previous small paver developed by the company. Travers said, “We’ve gone the extra distance and put in a lot of extra steel.”
He continued that the machine has been heavily-built, sharing some components too from the larger pavers built by sister company
The machine meets Tier 4 Interim emissions standards and is powered by a
Operation is fully automated by steering, distance and feeding sensors and the optional steering device automatically guides the feeder, so the operator can concentrate on the truck emptying process for productivity. Maintenance costs for the MF2500CS are said to be low, while its low weight of less than 20tonnes and narrow 2.55m width help cut transport costs.
Also aimed at smaller projects is
Weighing in at 9.1tonnes the machine features a 9tonne capacity hopper, with power from a 75kW
In addition, LeeBoy is now offering its proven 8515 paver with the same heavy-duty Legend electric screed as an option, as well as a conventional electric screed.
Roadtec is keen to maintain its position in the materials transfer sector with the latest upgrade to its highly successful Shuttle Buggy. The company took on board comments from the contractors about the remixing performance, reliability and productivity that has led the firm to increase the life of critical wear components in the machine, to reduce maintenance downtime and increase uptime.
Roadtec president Jeff Richmond said, “We included a lot of improvements to wear parts. We believe we’ve increased the life of these parts by up to 50%.”
Although the new Shuttle Buggy looks the same as the previous model, it is slightly heavier due to a beefed-up structure but the new engine is more fuel-efficient. “We’ve been pleasantly surprised by the fuel-efficiency of the new Tier 4 Interim engine,” Richmond said.
In operation the Shuttle Buggy and the paver work together, with the former following the latter automatically, a paver train technology that was developed to meet the needs of the European market. “The Buggy operator doesn’t need to worry about keeping up with the paver.”
The SP-200e spray paver is also available for use with the Shuttle Buggy that features a 7,949litre capacity on-board, product storage system. This is a 3m class machine with a gravity feed hopper and an extendable spraybar with proven rate control technology from Bearcat. Internationally the Shuttle Buggy is proving popular and Richmond said, “We have six or seven Shuttle Buggies working in Germany now, and it’s difficult to sell a US paving product to Germany.”
The sophisticated Guardian telematics system from Roadtec is also being fitted to the Shuttle Buggy and allows full diagnosis of performance back at the factory. Richmond said, “We can look at all that in real-time. There are a lot of functions we can repair over the internet, or we can identify component failures for an operator and put a new part in the air for delivery next day.”
Customer service has been a strong focus for the firm and he said, “Every machine is now covered by a three year warranty and if an operator wants to repair a machine himself, we will pay the cost.”
The key behind this is to make sure that operating cost is a known quantity for the customer. The new RP190e is the first Cummins-powered, 3m class paver Roadtec has built, with good all-round visibility due to its low deck design and efficient fumes extraction. An anti-segregation feed system is fitted as standard to improve paving quality, with abrasion resistant components to increase working life.
The Guardian system is also being fitted to this machine to monitor electrics, hydraulics, engine, auger speed and flow gate height for example. Richmond said, “If a customer has problems with surface quality, we can look at the slope control and reset it over the internet in real-time. We know the customer gets a bonus for quality.”
The Guardian package is effectively a PC on the machine that will provide an alert if something goes wrong with the piece of equipment. “We can do analysis of production data and we’re trying to help them to be more efficient.”
Roadtec is launching a 2.5m tamper bar screed developed by the firm’s operation in Germany. This screed has been designed as a heavy-duty unit and for US customers, this will allow it to be used for RCC applications. Worldwide however it will be sold on the new German-built Roadtec asphalt pavers.
One of the more sophisticated competitors to Roadtec’s Shuttle Buggy is a very different machine in concept.
One of the biggest launches at World of Asphalt was for
The wheeled version is the P7170 and the tracked model is the P7110 and the paver is of note as this is the first large road machine to have been developed at the facility since this business was acquired from Ingersoll Rand by Volvo Construction Equipment. In all it features around 200-250 upgrades over the machine being replaced and is intended to compete in the 3.05m wide screed class, with a maximum paving width of 7.9m.
An array of screeds with front and rear-mounted extensions is available to suit various customer needs. Quick-coupling makes the extensions easy to add or remove, while four standard ultrasonic sensors automatically regulate the proper delivery and flow of material to match the paver’s speed and ensure smooth and consistent paving.
Power comes from a Volvo D8 235 diesel rated at 175kW and which meets Tier 4 Interim legislation. The spokesperson said, “We took some of our legacy design from the Blaw Knox. It has a smooth propel drive and we’ve added more power to this model while it has the same fuel consumption.”
The design has been tested extensively, with 250,000tonnes of material having been put through the pre-production machines in working applications. Once this tough trial period was over, the test machines were taken apart to see what had worn. The spokesperson said, “We’re very careful in Volvo how we design machines for high altitude and high temperature operations. We have 2,000 hours on three pre-production machines.”
Paving efficiency is said to be maximised as the hopper works in conjunction with independently controlled conveyors and augers to provide a consistent material flow to the screed. Synchronised folding, hydraulic front hopper wings deliver material to the conveyor system, which the firm claims minimises material segregation.
Hydrostatic drives for the independently controlled conveyors and augers ensure material is moved evenly to both sides of the screed. Each conveyor has a reverse feature which helps control material and assist in clean-up. Proportional auger speed control and hydraulic auger height adjustments optimise the head of material in the auger channel. The company claims the new 7000 series will outperform competing units with features such as a 90.5m/min maximum paving speed and the spokesperson said, “This is one of the most productive pavers out there.”
Slurry option
The fibres help the mechanical performance of the mix and help increase life and the company saw market demand for this technology grow. As a result the company now builds a feeder system for the fibres that can be fitted to its Macropaver and Hogue said, “We make a cutter for it. The fibres are cut into the final mix slurry.”Designed to be easy to operate from either side of the deck even in night working conditions, the controls on the dual consoles are all back-lit. A low deck height allows good all-round visibility for the operator while the firm has also paid close attention to service needs by keeping maintenance points at comfortable working height from the ground. A fume extraction system is fitted that is said to removes fumes at 83% efficiency without obstructing the operator’s view into the auger channel. Fumes exit through the integral exhaust stack.
The 34tonne Weiler E2850 is driven by a Cat C9 diesel rated at 224kW and the machine has four-wheel steering as well as a three-speed hydrostatic drive. It has a 22.5tonne capacity and the user can fit a hopper insert that boosts capacity by 5tonnes. The Weiler material transfer vehicle is now supported in the US by all 52 Caterpillar distributors and Weiler units are also being sold in Russia, Mongolia and Australia through the Caterpillar network. Bill Hood of Weiler said, “A Mongolian customer has ordered a 2850 and it’s the first transfer vehicle in the country.”