Atlas Copco’s Dynapac brand is launching new models aimed at the asphalt paving market - Mike Woof reports Atlas Copco’s Dynapac brand looks set to boost its worldwide presence in the road construction market, with new asphalt paving products forming a major segment of the firm’s improved portfolio.
The launch of new pavers and an improved material feeder comes at a busy time for the Dynapac brand. When Dynapac was first acquired by Atlas Copco the business was left separate initially, however it has now
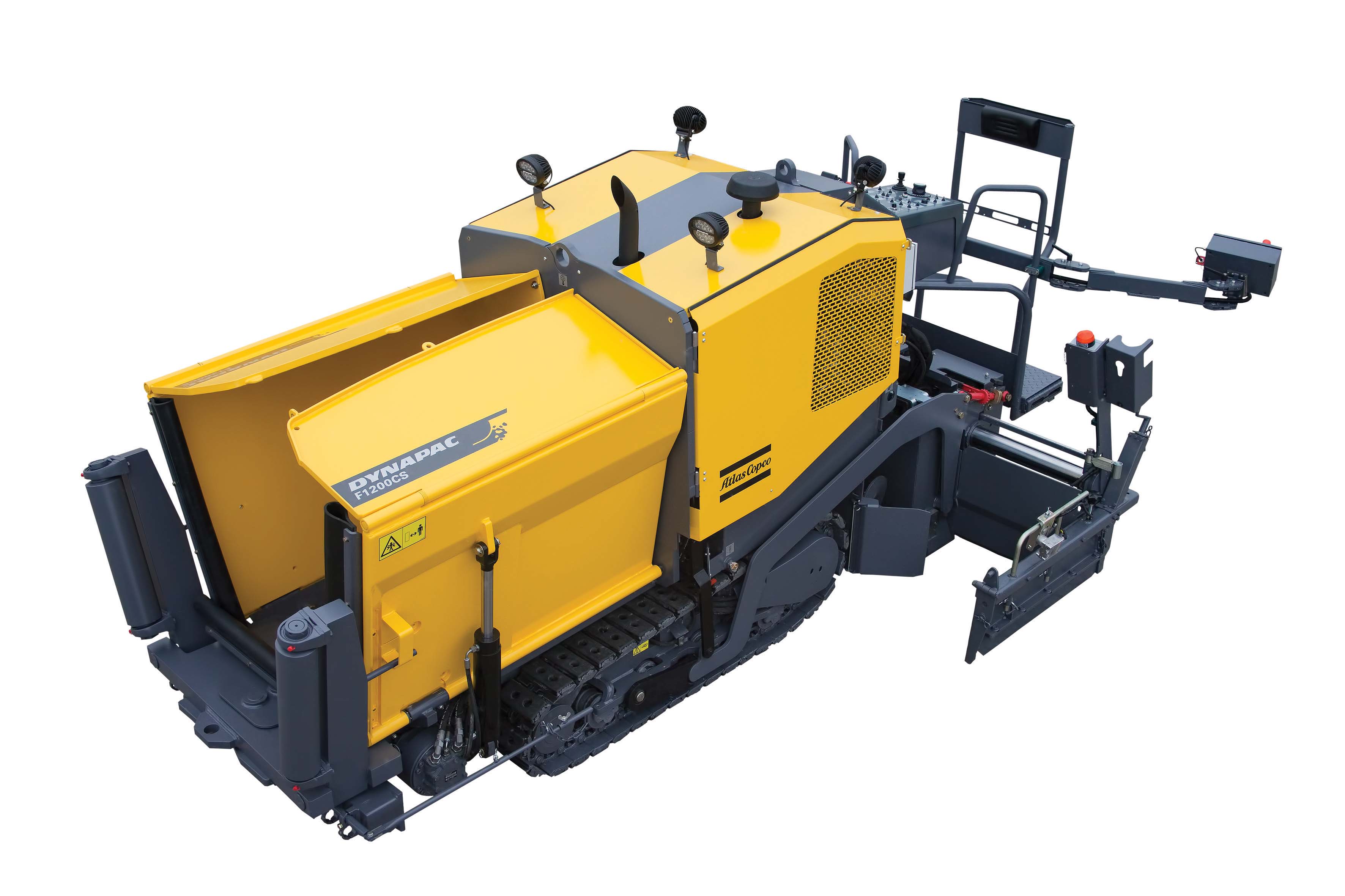
The F1200CS is a compact paver for small road repairs
Atlas Copco’s Dynapac brand is launching new models aimed at the asphalt paving market - Mike Woof reports
161 Atlas Copco’s 206 Dynapac brand looks set to boost its worldwide presence in the road construction market, with new asphalt paving products forming a major segment of the firm’s improved portfolio.
The launch of new pavers and an improved material feeder comes at a busy time for the Dynapac brand.
When Dynapac was first acquired by Atlas Copco the business was left separate initially, however it has now been fully incorporated into the firm’s new construction equipment division.
Peter Lauwers is president of Atlas Copco Road Construction Equipment and he explained that the company is expanding its presence worldwide, with products being developed for local markets. The company has manufacturing operations in Brazil, China and India and these are developing machines for use in those territories.
One of the key technical issues the firm is facing is the tough emissions requirements, which vary from area to area.
For the asphalt paving market the firm is introducing new pavers for the European market as well as for North American customer, and an improved version of its material feeder. The smallest of the new European pavers is the compact F1200CS, which is designed for patching repairs and small jobs. Abhijit Som is product manager for large pavers at the firm and said, “You could use it to pave a trench. It’s a low height machine so you can pave in an underground car park for example. We can offer a simple vibration screed or a tamper bar screed.”
With the screed retracted the machine is just 1.2m wide and less 2m high while it is 4.5m long, allowing operation in small working areas. This compact machine can be used to pave thicknesses of up to 250mm and widths from 0.8-3.1m, using its 5tonne capacity hopper to deliver up to 300tonnes/hour. Gas and electric heating options are offered, in addition to the choice of vibration or tamper bar type screeds. The screeds have a temperature control unit, ensuring that no energy is wasted and the screed is always at its optimum temperature. Power comes from a Deutz diesel that meets Tier 4 Final/Stage IIIB emissions requirements and delivers 54kW. The machine is more stable and offers faster transport between job sites than the model it replaces, while it is said to be more comfortable to operate due to a new layout for the crawler rollers and an improved centre of gravity.
The firm’s larger wheeled pavers can handle paving widths from 2.5-9m and are offered with gas or electric screed heating options. These are Tier 4 Interim compliant and Som said, “We will be able to offer them with Tier 4 Final engines early next year.”
The new SD2500WS wheeled paver can be fitted with the firm’s V5100TV Vario screed and is powered by a QSB-6.7 Cummins that meets Stage IIIB/Tier4 Interim requirements. The novel VarioSpeed system is an optional drive concept that provides the required engine speed for the working situation, and can save up to 15% on fuel costs. The firm also has a new drive system that hydraulically optimises traction at the front wheels, taking into account the load on the hopper. And combined with the electronically controlled rear wheel drive, the novel AddTraxxion system is said to ensure optimum traction.
New hydraulics increase drivetrain efficiency, giving high traction force for more precise paving. The four tube screed support layout has been patented and is said to provide a precise mat application.
The machines feature an automatic drive system that prevents the wheels from spinning out, particularly when turning with a load in the screed. “They’ve got a very good turning radius.”
The machines have been designed to ensure paving quality and Som said, “We have the largest conveyor tunnels on the market to minimise segregation and we have large augers. Our focus will be on enhancing productivity for our customers. The machines pave faster, wider, thicker and also use less energy and have longer service intervals, reducing the cost of ownership. If you use less fuel, you produce less CO2 and we’re already using some Tier 4 Final engines in the range.”
Also new is the Dynapac SD2550CS paver, a machine said to offer high paving capacity and a low cost/tonne. Together, the Dynapac SD2550CS paver and the Dynapac MF2500CS material feeder make a great paving team, meeting the needs of contractors, communities and rental companies around the world. The new screed system and the latest version of the sophisticated Pave Manager 2.0 control system are said to contribute to mat quality. The upgraded Pave Manager 2.0 operating system, with colour display, offers an improved operator interface as well as additional features. The Dynapac SD2550CS is suitable for highway paving up to 14m, with a theoretical production capacity of 1,100tonnes/hour.
The 15tonne capacity hopper provides the smooth material flow required while paving wide sections. The paver is also available with a larger hopper and, when used together with the new Dynapac MF2500CS material feeder, the paving performance can be 30% higher. A number of screeds are suitable for the Dynapac SD2550CS paver: the Dynapac V5100/6000 TVE (tamper vibration) screeds, V5100/6000TVH (high compaction) screeds as well as the Dynapac R300TVE rigid screed.
The MF2500 material feeder is able to empty a 27tonne truck in just 35 seconds, providing a throughput of 4,000tonnes/hour. This capacity can help maximise the potential of paving machines and Som said, “Pavers can pave at twice the rate they do today on most jobs. The problem is the material delivery.”
Material feeders are also important for quality and Som said, “We did a study and it showed that paving stops cause problems. These cold areas are the first to fail.”
The machine has been built on a 2.55m wide platform that is compact for its capacity and to lower ownership costs for customers with existing Dynapac equipment, it uses many paver components. The materials feeder has been designed to be versatile and easy to transport and Som said, “It’s available with a swing conveyor and this means our materials feeder can supply two pavers. The machine is smaller and more compact than previous feeders that require special transport and you can put it on a normal truck.”
Power for the MF2500CS comes from a Stage IIIB/Tier4 Interim196 Cummins QSB6.7 diesel rated at 170kW, while the machine’s hydraulic drive system features thermostatic fan control for efficient cooling and efficient hydraulics to ensure fuel efficiency.
Customers can choose either the standard short conveyor or the swingable conveyor mounted behind the short belt. This additional unit can be attached and removed quickly as required and no modification of the standard feeder is required for this extra tool. The main advantage of attaching the swingable conveyor is that it enables the machine to feed two pavers. However, it can also be used, for example, for bicycle lanes and road shoulders.
The material feeder can be used for large highway jobs and suits both European and US style machines. For the US market the firm has the new F800T 2.44m class paver with power from a Cummins QSB6.7 diesel rated at 127kW and which meets the latest Tier 4 Final emissions requirements. All the hydraulic components are oversized and many of the same units are used as in the firm’s larger F1000 paver to ensure reliability and longevity, as well as cutting spares holding costs for fleet customers.
The machine runs on a high performance undercarriage system, which is said to be capable of pushing trucks even when the hopper is fully loaded. The machine is available with the proven Carlson EZ08-15 front mounted electrical screed. Power for the screed’s electrical heating is provided by a tractor-mounted, hydraulically-driven generator that is oversized and provides 34kV, with plenty of capacity for powering additional equipment.
The launch of new pavers and an improved material feeder comes at a busy time for the Dynapac brand.
When Dynapac was first acquired by Atlas Copco the business was left separate initially, however it has now been fully incorporated into the firm’s new construction equipment division.
Peter Lauwers is president of Atlas Copco Road Construction Equipment and he explained that the company is expanding its presence worldwide, with products being developed for local markets. The company has manufacturing operations in Brazil, China and India and these are developing machines for use in those territories.
One of the key technical issues the firm is facing is the tough emissions requirements, which vary from area to area.
For the asphalt paving market the firm is introducing new pavers for the European market as well as for North American customer, and an improved version of its material feeder. The smallest of the new European pavers is the compact F1200CS, which is designed for patching repairs and small jobs. Abhijit Som is product manager for large pavers at the firm and said, “You could use it to pave a trench. It’s a low height machine so you can pave in an underground car park for example. We can offer a simple vibration screed or a tamper bar screed.”
With the screed retracted the machine is just 1.2m wide and less 2m high while it is 4.5m long, allowing operation in small working areas. This compact machine can be used to pave thicknesses of up to 250mm and widths from 0.8-3.1m, using its 5tonne capacity hopper to deliver up to 300tonnes/hour. Gas and electric heating options are offered, in addition to the choice of vibration or tamper bar type screeds. The screeds have a temperature control unit, ensuring that no energy is wasted and the screed is always at its optimum temperature. Power comes from a Deutz diesel that meets Tier 4 Final/Stage IIIB emissions requirements and delivers 54kW. The machine is more stable and offers faster transport between job sites than the model it replaces, while it is said to be more comfortable to operate due to a new layout for the crawler rollers and an improved centre of gravity.
The firm’s larger wheeled pavers can handle paving widths from 2.5-9m and are offered with gas or electric screed heating options. These are Tier 4 Interim compliant and Som said, “We will be able to offer them with Tier 4 Final engines early next year.”
The new SD2500WS wheeled paver can be fitted with the firm’s V5100TV Vario screed and is powered by a QSB-6.7 Cummins that meets Stage IIIB/Tier4 Interim requirements. The novel VarioSpeed system is an optional drive concept that provides the required engine speed for the working situation, and can save up to 15% on fuel costs. The firm also has a new drive system that hydraulically optimises traction at the front wheels, taking into account the load on the hopper. And combined with the electronically controlled rear wheel drive, the novel AddTraxxion system is said to ensure optimum traction.
New hydraulics increase drivetrain efficiency, giving high traction force for more precise paving. The four tube screed support layout has been patented and is said to provide a precise mat application.
The machines feature an automatic drive system that prevents the wheels from spinning out, particularly when turning with a load in the screed. “They’ve got a very good turning radius.”
The machines have been designed to ensure paving quality and Som said, “We have the largest conveyor tunnels on the market to minimise segregation and we have large augers. Our focus will be on enhancing productivity for our customers. The machines pave faster, wider, thicker and also use less energy and have longer service intervals, reducing the cost of ownership. If you use less fuel, you produce less CO2 and we’re already using some Tier 4 Final engines in the range.”
Also new is the Dynapac SD2550CS paver, a machine said to offer high paving capacity and a low cost/tonne. Together, the Dynapac SD2550CS paver and the Dynapac MF2500CS material feeder make a great paving team, meeting the needs of contractors, communities and rental companies around the world. The new screed system and the latest version of the sophisticated Pave Manager 2.0 control system are said to contribute to mat quality. The upgraded Pave Manager 2.0 operating system, with colour display, offers an improved operator interface as well as additional features. The Dynapac SD2550CS is suitable for highway paving up to 14m, with a theoretical production capacity of 1,100tonnes/hour.
The 15tonne capacity hopper provides the smooth material flow required while paving wide sections. The paver is also available with a larger hopper and, when used together with the new Dynapac MF2500CS material feeder, the paving performance can be 30% higher. A number of screeds are suitable for the Dynapac SD2550CS paver: the Dynapac V5100/6000 TVE (tamper vibration) screeds, V5100/6000TVH (high compaction) screeds as well as the Dynapac R300TVE rigid screed.
The MF2500 material feeder is able to empty a 27tonne truck in just 35 seconds, providing a throughput of 4,000tonnes/hour. This capacity can help maximise the potential of paving machines and Som said, “Pavers can pave at twice the rate they do today on most jobs. The problem is the material delivery.”
Material feeders are also important for quality and Som said, “We did a study and it showed that paving stops cause problems. These cold areas are the first to fail.”
The machine has been built on a 2.55m wide platform that is compact for its capacity and to lower ownership costs for customers with existing Dynapac equipment, it uses many paver components. The materials feeder has been designed to be versatile and easy to transport and Som said, “It’s available with a swing conveyor and this means our materials feeder can supply two pavers. The machine is smaller and more compact than previous feeders that require special transport and you can put it on a normal truck.”
Power for the MF2500CS comes from a Stage IIIB/Tier4 Interim
Customers can choose either the standard short conveyor or the swingable conveyor mounted behind the short belt. This additional unit can be attached and removed quickly as required and no modification of the standard feeder is required for this extra tool. The main advantage of attaching the swingable conveyor is that it enables the machine to feed two pavers. However, it can also be used, for example, for bicycle lanes and road shoulders.
The material feeder can be used for large highway jobs and suits both European and US style machines. For the US market the firm has the new F800T 2.44m class paver with power from a Cummins QSB6.7 diesel rated at 127kW and which meets the latest Tier 4 Final emissions requirements. All the hydraulic components are oversized and many of the same units are used as in the firm’s larger F1000 paver to ensure reliability and longevity, as well as cutting spares holding costs for fleet customers.
The machine runs on a high performance undercarriage system, which is said to be capable of pushing trucks even when the hopper is fully loaded. The machine is available with the proven Carlson EZ08-15 front mounted electrical screed. Power for the screed’s electrical heating is provided by a tractor-mounted, hydraulically-driven generator that is oversized and provides 34kV, with plenty of capacity for powering additional equipment.