US-based P&S Paving has boosted output from its asphalt facility in Daytona, Florida with the purchase of a new plant from Astec Industries.
The firm supplies a wide range of customers ranging from small urban works up to large highway projects for the Florida Department of Transportation. As a result the company needed a modern, versatile and productive plant capable of delivering an array of mixes and quantities, including high quality materials.
Tim Phillips, president of P&S Paving said, “We want
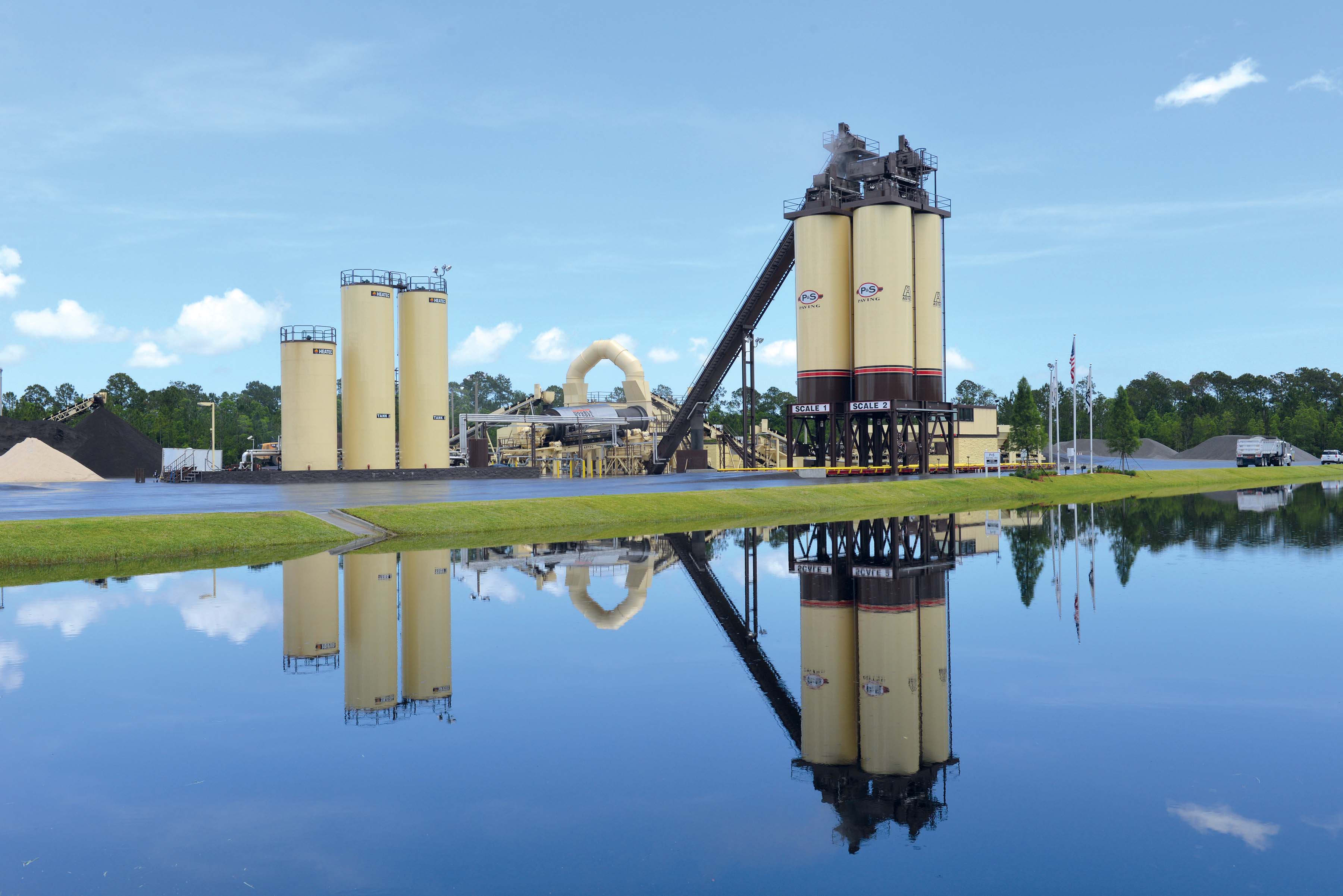
The plant was custom-built to the needs of P&S Paving
US-based P&S Paving has boosted output from its asphalt facility in Daytona, Florida with the purchase of a new plant from Astec Industries.
The firm supplies a wide range of customers ranging from small urban works up to large highway projects for the2697 Florida Department of Transportation. As a result the company needed a modern, versatile and productive plant capable of delivering an array of mixes and quantities, including high quality materials.
Tim Phillips, president of P&S Paving said, “We wanted to test the mix; know what we have in the silo before it’s delivered to the roadway. Of course the technology has changed dramatically within the last 15 years and we wanted to take advantage of what’s out there.”
The new equipment at the facility includes1250 Astec’s novel Double Barrel XHR system. The Double Barrel XHR is said to offer low operating costs while being able to use stockpiles of reclaimed asphalt pavement. The ASTEC Double Barrel XHR drum can produce high-quality mix with a high RAP content; up to 65% RAP at 5% moisture.
The high recycled asphalt pavement (RAP) capability of the Double Barrel XHR was an important feature for P&S Paving. Through a combination of features, the Double Barrel XHR is able to achieve a quality mix with a high RAP content and benefits from two well proven mixing technologies. It has an outer chamber on the drum and an external mixer. The V-Pack Stack Temperature Control System is said to maintain as low an exhaust temperature as possible when running a high RAP/low virgin mix. This is important as less virgin material in the drying portion of the drum could result in high exhaust temperatures. In order to combat the high temperatures encountered when running high RAP content, the last half of the Double Barrel XHR drum is made from stainless steel, including the combustion flights.
The outer mixing chamber on the dryer gently mixes recycle with dry hot aggregate maximising heat and binder transfer between RAP, aggregate and selected admixtures in a rarefied oxygen atmosphere. The external mixer vigorously mixes virgin liquid as well as other admixtures. The ASTEC warm mix system is fitted as standard on all XHR mixers.
The ASTEC V-Pack Stack Temperature Control System uses v-flights and a drum variable frequency drive (VFD) to help produce different types of mixes, while controlling stack temperature without the added cost and time of flight changes. ASTEC v-flights shower along the edge of the notch as well as the tip. A wider veil increases the effectiveness of the veil by exposing more material to hot gases.
Meeting the needs of FDOT requires P&S Paving to remain on the ready with a high reserve of asphalt, which can sometimes be difficult in Florida’s often erratic weather. The firm now has 1,088tonnes of storage, allowing it to store asphalt for up to four to five days, according to Phillips. “Florida summers are notorious for rainfalls that can last for spurts of two or three days at a time, so the extra storage capacity was a definite plus for us.”
P&S Paving currently provides about 362,873tonnes/year out of this one facility, and Astec was keen to ensure its customer had enough capacity to meet that goal comfortably.
Phillips was also pleased that the new Daytona plant was ready-made to incorporate the latest in operations and control systems to better assist preventive maintenance. “After 20 years of operations,” Phillips observed, “we know where the high-maintenance areas in a plant are, so it was important that we made them very accessible. We also placed 16 cameras throughout this plant.”
“With eyes right there in the control house, it means that a couple of ground personnel are now free for something else,” he explained. “In fact, the first time the plant fired up, we were able to use one of the cameras to identify where a belt was tracking off a recycle conveyor. This is something that a normal operator can’t see inside the plant. With that catch, the cameras paid for themselves within the first five minutes of operation.”
The firm supplies a wide range of customers ranging from small urban works up to large highway projects for the
Tim Phillips, president of P&S Paving said, “We wanted to test the mix; know what we have in the silo before it’s delivered to the roadway. Of course the technology has changed dramatically within the last 15 years and we wanted to take advantage of what’s out there.”
The new equipment at the facility includes
The high recycled asphalt pavement (RAP) capability of the Double Barrel XHR was an important feature for P&S Paving. Through a combination of features, the Double Barrel XHR is able to achieve a quality mix with a high RAP content and benefits from two well proven mixing technologies. It has an outer chamber on the drum and an external mixer. The V-Pack Stack Temperature Control System is said to maintain as low an exhaust temperature as possible when running a high RAP/low virgin mix. This is important as less virgin material in the drying portion of the drum could result in high exhaust temperatures. In order to combat the high temperatures encountered when running high RAP content, the last half of the Double Barrel XHR drum is made from stainless steel, including the combustion flights.
The outer mixing chamber on the dryer gently mixes recycle with dry hot aggregate maximising heat and binder transfer between RAP, aggregate and selected admixtures in a rarefied oxygen atmosphere. The external mixer vigorously mixes virgin liquid as well as other admixtures. The ASTEC warm mix system is fitted as standard on all XHR mixers.
The ASTEC V-Pack Stack Temperature Control System uses v-flights and a drum variable frequency drive (VFD) to help produce different types of mixes, while controlling stack temperature without the added cost and time of flight changes. ASTEC v-flights shower along the edge of the notch as well as the tip. A wider veil increases the effectiveness of the veil by exposing more material to hot gases.
Meeting the needs of FDOT requires P&S Paving to remain on the ready with a high reserve of asphalt, which can sometimes be difficult in Florida’s often erratic weather. The firm now has 1,088tonnes of storage, allowing it to store asphalt for up to four to five days, according to Phillips. “Florida summers are notorious for rainfalls that can last for spurts of two or three days at a time, so the extra storage capacity was a definite plus for us.”
P&S Paving currently provides about 362,873tonnes/year out of this one facility, and Astec was keen to ensure its customer had enough capacity to meet that goal comfortably.
Phillips was also pleased that the new Daytona plant was ready-made to incorporate the latest in operations and control systems to better assist preventive maintenance. “After 20 years of operations,” Phillips observed, “we know where the high-maintenance areas in a plant are, so it was important that we made them very accessible. We also placed 16 cameras throughout this plant.”
“With eyes right there in the control house, it means that a couple of ground personnel are now free for something else,” he explained. “In fact, the first time the plant fired up, we were able to use one of the cameras to identify where a belt was tracking off a recycle conveyor. This is something that a normal operator can’t see inside the plant. With that catch, the cameras paid for themselves within the first five minutes of operation.”