A US contractor is upgrading rural Pennsylvania roads with the aid of a powerful new reclaimer/stabiliser
Much of the United States highway infrastructure continues to deteriorate due to lack of a comprehensive road bill and eroding investment in the nation’s roads. However, some of the country’s secondary and rural roads are being upgraded, and funding is coming from unlikely private sources. Energy companies with stakes in the Marcellus and Utica deep shale gas reserve development are working with local
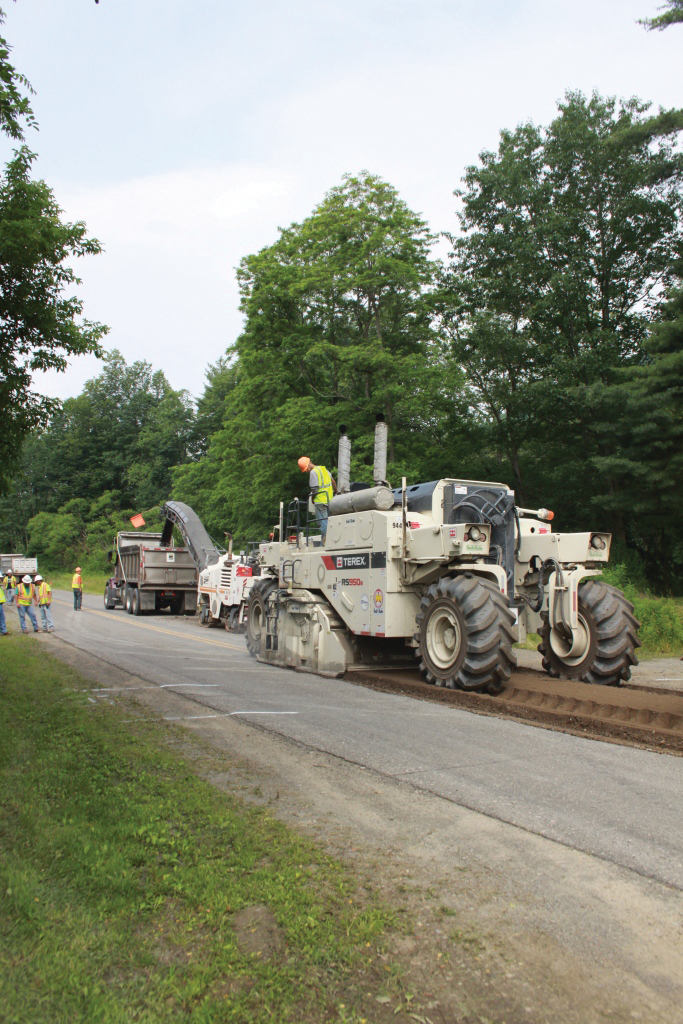
The 3m rotor of the RS950 stabiliser/reclaimer was able to reduce the number of passes the contractor carried out
A US contractor is upgrading rural Pennsylvania roads with the aid of a powerful new reclaimer/stabiliser
Much of the United States highway infrastructure continues to deteriorate due to lack of a comprehensive road bill and eroding investment in the nation’s roads. However, some of the country’s secondary and rural roads are being upgraded, and funding is coming from unlikely private sources.Energy companies with stakes in the Marcellus and Utica deep shale gas reserve development are working with local
Business is making necessary investments to help improve transportation both for its own needs, as well as for communities. Deep well hydraulic fracturing requires heavy drilling equipment and large quantitites of water, up to 21 million litres in fact, for the typical Marcellus well.
This results in hundreds of truck trips carrying fresh water to the jobsite and additional trips to remove waste water from the drilling process. Often, these sites are found where the roads are structurally deteriorating or not built to withstand heavy truck traffic.
“In Pennsylvania, hundreds of miles of county highways and rural roads are being upgraded to better withstand heavy truck traffic,” explained Scott McMaster, district manager for
One contractor charged with making these roadway improvements is Cortland, NY-based Suit-Kote Corporation. The family-owned firm serves primarily the Northeast with locations in New York and Pennsylvania and roams a market stretching from Massachusetts to Ohio for its asphalt related services. It is involved with all facets of asphalt production, paving and maintenance.
In addition to producing hot, warm and cold mixes using virgin aggregate or designs incorporating recycled asphalt,
The firm has been working for the Pennsylvania DOT for many years and has now added to its portfolio by working for energy companies to improve rural roads for heavy truck traffic. Paul Suits, vice president of Suit-Kote Corporation said, “I would describe these roads as state highways, farm-to-market and secondary roads.”
Road weight limits vary but many are rated at carrying a maximum of just 9tonnes. Historically carrying low traffic volumes, most of these roads are old and in various states of disrepair. Most average 76-254mm or more of old, oxidised asphalt with designs ranging from macadam to surface treatments to hot mix asphalt, according to Suits.
The rehabilitation process for the roads is relatively the same. Contractors use FDR to dry grind the existing asphalt road plus a portion of the subbase material. A second pass with the reclaimer/stabiliser blends portland cement and water with the pulverised material to create a stabilised base for fresh asphalt.
After a curing period of some five days, an average of 127-203mm of asphalt is paved over the stabilised base material. Even with the high truck traffic employed in the fracking process, the customer’s goal for these rehabilitated roads is a 10-year service life, according to Suit-Kote.
Suit-Kote used its FDR train in northeast Pennsylvania to rehabilitate a 3.9km portion of State Route 1007 in Bradford County. In addition to compactors and a grader, the crew used a 448kW Terex RS600 Reclaimer/Stabiliser equipped with a 2.4m cutter.
Suit-Kote used this machine for dry grinding the asphalt surface throughout the majority of the project. Asphalt depth varied, averaging 152mm throughout most of the project. However, there were pockets reaching 254mm in depth. Reclamation depths remained constant and the firm had to cut to a 381mm depth to meet the specification.
To properly reclaim the severely deteriorated road with the 2.4m cutter, Suit-Kote’s crews made three to four passes over the 6.7m wide road. Following closely behind the reclaimer/stabiliser, a padfoot roller provided preliminary compaction. This was followed by a grader, which began to establish grade for the new road surface. The grade at some points of the previous road surface was as high as 12%, and the new road specification called for a maximum final 6% grade, according to the contractor. A smooth drum roller was used for finish rolling prior to the stabilising step.
Some counties, such as Bradford County, specified an additional slot-mill step in front of the reclaimer/stabiliser. According to a Pennsylvania DOT engineer, slot milling is done so the new layer of asphalt does not add too much height to the road. Suit-Kote’s crews milled a 1.2m shoulder section on one side of SR 1007.
In addition to the RS600, crews used older RS650 and RS800 machines equipped with 3m rotors, which saved passes. While working on SR 1007, the company also took delivery of a new 730kW Terex RS950B Reclaimer/Stabiliser, and it was put to work on the project. Initially, the machine followed the 448kW machine to mix portland cement and water with the road base. Capable of stabilising with asphalt emulsions and calcium chlorides, the RS950B pushed a water tanker to add water to the cement. With its water spray system, the RS950B’s independently controlled spray nozzles helped Suit-Kote’s crew ensure the correct percentage of water was added across the entire road width.
Water system operation is controlled at the operator’s station using the machine’s colour display. This display allows the operator to set and monitor cutter depth, travel speed, steering mode, load control, and engine and fluid parameters. It also helps the operator with fault monitoring, trouble-shooting and system calibrations.
Similar to Suit-Kote’s RS600, the 730kW machine has a centre-mount rotor design. The housing is fix-mounted to the machine’s frame, and a parallelogram leg design offers up to 914mm of elevation to lower/raise the rotor into and out of the cut. Four-wheel drive helps to power the machine through difficult cuts and slippery operating conditions, such as blending cement and water with the road base.
Directly following the RS950B, crews again compacted and graded the road base to final slope and grade in preparation for the asphalt overlay. While primarily blending cement to stabilize the road base, the machine was also used to make the first dry-grind pass on occasion. After adding the 730kW machine with 3m rotor to the job, Suit-Kote was able to reclaim 3.2km of the 6.7m wide SR 1007 road each day or nearly 4,121m3.