A pavement recycling contractor in eastern New York State in the US is using an innovative and versatile Wirtgen machine to carry out very different road rehabilitation tasks. This unit is being used to lay foamed bitumen-recycling pavements as well as carrying out cold-milling.
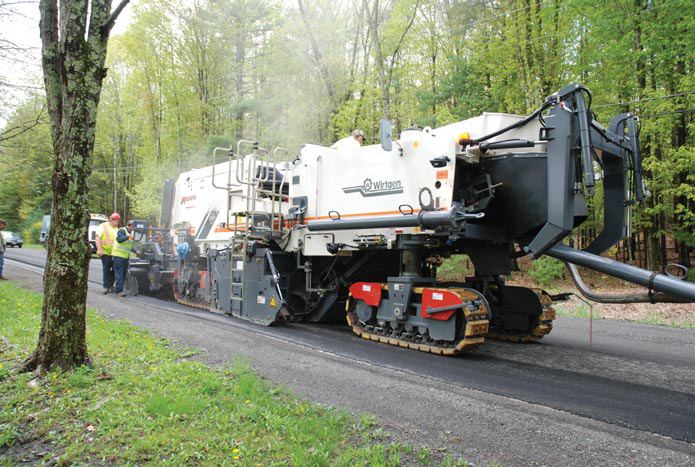
Using the Wirtgen 2200CR allows contractors to use foamed bitumen-recycling and cold-in-place techniques to a depth of 102mm
A pavement recycling contractor in eastern New York State in the US is using an innovative and versatile 2395 Wirtgen machine to carry out very different road rehabilitation tasks. This unit is being used to lay foamed bitumen-recycling pavements as well as carrying out cold-milling.
Specialist contractor Reclamation, of Kingston, NY, acquired the machine in May and put it to work carrying out foamed asphalt-recycling on Zena Road for Ulster County, NY, within the environmentally sensitive Catskill State Park in the Catskill Mountains north of New York City. The contractor then mounted a conveyor on the machine and began using it to cold-mill pavements.
"We're recycling the road in-place to a 102mm depth," said Chris Suttmeier, technical services manager for Reclamation. "We do the full-blown design, including gradation, density, and optimum moisture and asphalt content."
"It's a very 'green' process," said David Sheeley, commissioner of public works, Ulster County, NY. "We don't have to haul a lot of material. Foaming the base adds structural stability and does away with the problem of having to do a lot of work on driveways afterwards. Foamed asphalt recycling is beneficial in a lot of ways."
Foamed asphalt allows a stable cold mix that can be overlaid with a thin wearing course and can permit traffic almost immediately. Tremendous savings in extraction and hauling costs can be achieved because the reclaimed asphalt pavement (RAP) used in this technology contains aggregates that have already been acquired, permitted, shot, loaded, crushed, screened, stockpiled, reloaded and hauled.
The machine, a 2200CR from Wirtgen Group, was foam-recycling the pavement surface cold in-place to a depth of 102mm, with a mix of containing 2% PG 64-22 performance-graded liquid asphalt, with 1.5% water added to assist compaction. Pre-construction material tests indicated that addition of cement or lime fines would not be required. The recycled base was topped with a 63mm friction course of asphalt over its 3km length for a total of 23,411m2 of pavement.
The Wirtgen 2200CR recycled the road in-place at just over 10.4m/minute. To ensure proper gradation the 2200CR is fitted with a gradation beam mounted directly in front of the cutter. The beam is held under pressure on the pavement, holding down the loose alligator-cracked pavement and is said to allow the cutting action to achieve gradation. Once a positive recycled lane is established, the 2200CR's screed can run from sonic sensors to ensure the correct pavement crossfall.
Three rollers were used to compact the freshly foamed surface, which was accommodating local traffic. They included the 2.1m wide HD130HV double-drum steel vibratory roller, and HD110K hybrid roller, combining a 1.7m wide vibratory steel drum at one end, with four pneumatic tyres at the other.
Compaction of the foamed base provided a roadway over which local traffic could move almost immediately, as no curing was required. A full lane of alternating one-way traffic always was available with the foamed asphalt option, which could accommodate even heavy trucks on the rural road, so no disruptions of traffic or road closures were necessary. As there is a local asphalt plant on this road, it carries a lot of heavy truck traffic and had deteriorated over the past five years to the point where it had become very hard to maintain.
The benefit of this technology is that it helps tackle the underlying problems for a road and unlike conventional techniques, can provide a solid base with no risk of crack propagation through to the surface. Meanwhile the process also helps reduce haulage and materials needed for a project, cutting costs.
In addition to the foamed bitumen and cold recycling work, the new 2200CR also can stabilise bases with asphalt emulsion. "The machine is versatile in that it can straight-mill as well," Suttmeier said.
"The 2200CR gives us the opportunity to move into some other disciplines," said Mike Haggerty, marketing director for Reclamation. "We are impressed with the machine as it does cold in-place recycling, milling, stabilisation and laydown with the screed. Recycling trains with other machines are longer with more components; here we have an oil tanker and the water is contained within the 2200CR."
Specialist contractor Reclamation, of Kingston, NY, acquired the machine in May and put it to work carrying out foamed asphalt-recycling on Zena Road for Ulster County, NY, within the environmentally sensitive Catskill State Park in the Catskill Mountains north of New York City. The contractor then mounted a conveyor on the machine and began using it to cold-mill pavements.
"We're recycling the road in-place to a 102mm depth," said Chris Suttmeier, technical services manager for Reclamation. "We do the full-blown design, including gradation, density, and optimum moisture and asphalt content."
"It's a very 'green' process," said David Sheeley, commissioner of public works, Ulster County, NY. "We don't have to haul a lot of material. Foaming the base adds structural stability and does away with the problem of having to do a lot of work on driveways afterwards. Foamed asphalt recycling is beneficial in a lot of ways."
Foamed asphalt allows a stable cold mix that can be overlaid with a thin wearing course and can permit traffic almost immediately. Tremendous savings in extraction and hauling costs can be achieved because the reclaimed asphalt pavement (RAP) used in this technology contains aggregates that have already been acquired, permitted, shot, loaded, crushed, screened, stockpiled, reloaded and hauled.
The machine, a 2200CR from Wirtgen Group, was foam-recycling the pavement surface cold in-place to a depth of 102mm, with a mix of containing 2% PG 64-22 performance-graded liquid asphalt, with 1.5% water added to assist compaction. Pre-construction material tests indicated that addition of cement or lime fines would not be required. The recycled base was topped with a 63mm friction course of asphalt over its 3km length for a total of 23,411m2 of pavement.
The Wirtgen 2200CR recycled the road in-place at just over 10.4m/minute. To ensure proper gradation the 2200CR is fitted with a gradation beam mounted directly in front of the cutter. The beam is held under pressure on the pavement, holding down the loose alligator-cracked pavement and is said to allow the cutting action to achieve gradation. Once a positive recycled lane is established, the 2200CR's screed can run from sonic sensors to ensure the correct pavement crossfall.
Three rollers were used to compact the freshly foamed surface, which was accommodating local traffic. They included the 2.1m wide HD130HV double-drum steel vibratory roller, and HD110K hybrid roller, combining a 1.7m wide vibratory steel drum at one end, with four pneumatic tyres at the other.
Compaction of the foamed base provided a roadway over which local traffic could move almost immediately, as no curing was required. A full lane of alternating one-way traffic always was available with the foamed asphalt option, which could accommodate even heavy trucks on the rural road, so no disruptions of traffic or road closures were necessary. As there is a local asphalt plant on this road, it carries a lot of heavy truck traffic and had deteriorated over the past five years to the point where it had become very hard to maintain.
The benefit of this technology is that it helps tackle the underlying problems for a road and unlike conventional techniques, can provide a solid base with no risk of crack propagation through to the surface. Meanwhile the process also helps reduce haulage and materials needed for a project, cutting costs.
In addition to the foamed bitumen and cold recycling work, the new 2200CR also can stabilise bases with asphalt emulsion. "The machine is versatile in that it can straight-mill as well," Suttmeier said.
"The 2200CR gives us the opportunity to move into some other disciplines," said Mike Haggerty, marketing director for Reclamation. "We are impressed with the machine as it does cold in-place recycling, milling, stabilisation and laydown with the screed. Recycling trains with other machines are longer with more components; here we have an oil tanker and the water is contained within the 2200CR."