Foamed bitumen is a versatile and cost-effective tool in recycling roads - Mike Woof reports Wirtgen hopes to capitalise on the growing demand for materials recycling and its range of solutions for this sector has expanded considerably in recent times. The firm has been taking advantage of further developments in foamed bitumen technology to offer an array of cost-effective road repair solutions. The range allows this material to be used in array of cold recycling applications and Wirtgen also offers labora
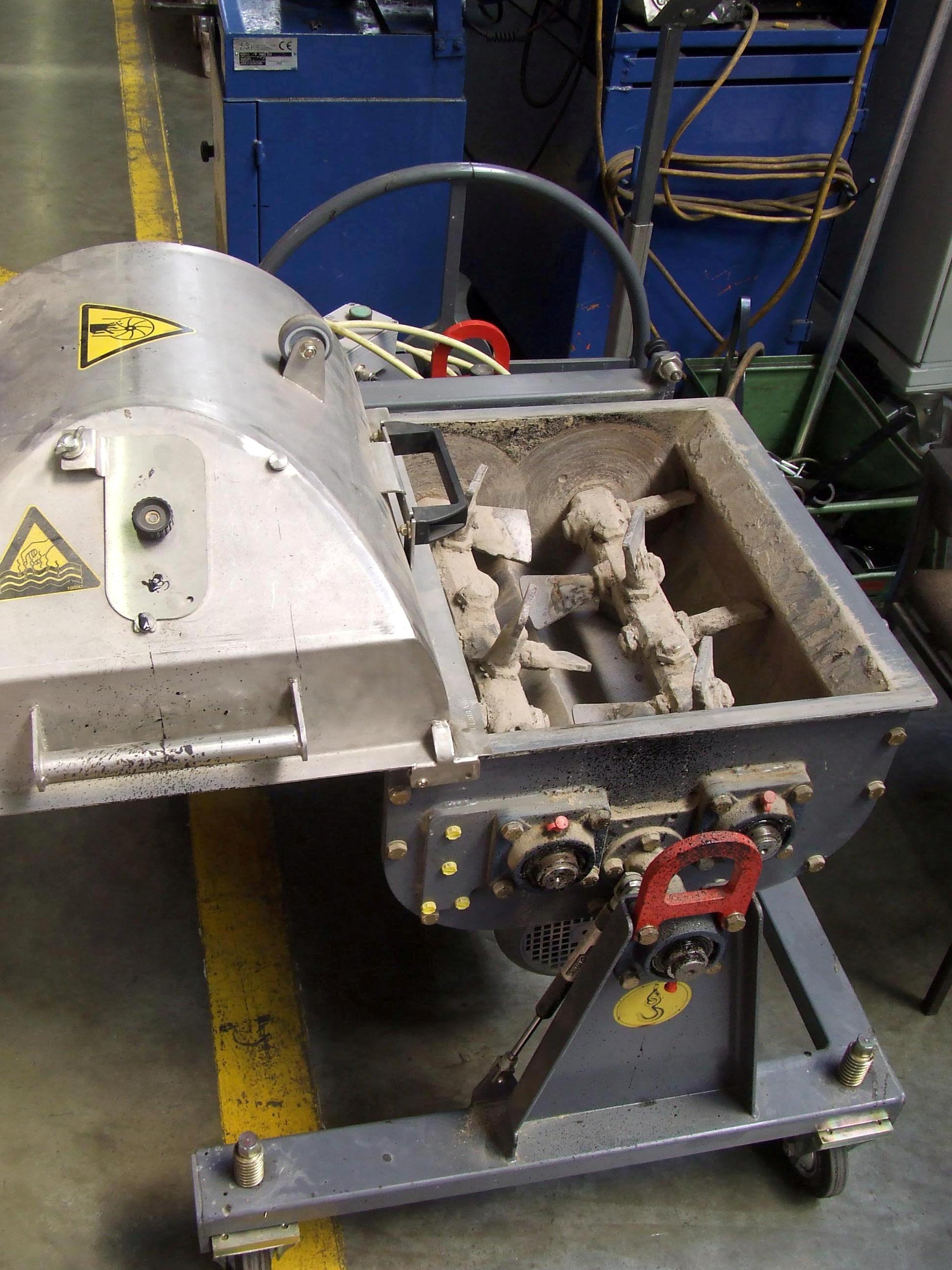
The WLM30 mill can be directly attached to the WLB10S foamed bitumen lab plant to produce test specimens
Foamed bitumen is a versatile and cost-effective tool in recycling roads - Mike Woof reports
Foamed bitumen is effective in cold recycling duties while also cutting costs and has a huge potential in the highway construction sector that has yet to be fully exploited. An innovative binding agent, foamed bitumen offers several benefits according to Martin Diekmann, a specialist in recycling technologies at Wirtgen. The technology scores points on a number of levels as it is economical and cuts cost, as well as being environmentally friendly.
The foamed bitumen can be used in a stabilisation process, by hooking up a supply tanker to a road stabiliser, which mixes that material with the cuttings from the road surface leaving a base that can then be compacted. A new surface can then be laid on top of this stabilised base using a paver in the conventional manner.
Using foamed bitumen is also highly suited to resurfacing applications and in this process the bitumen bubbles over the stone and only remains at the contact points between the pieces of aggregate. The distribution of the materials in the mix means that asphalt courses made using foamed bitumen technology will have a bitumen content of just 2%, compared with 5% for a conventional mix.
Because a mix made with foamed bitumen can be quite flexible, there is a significant reduction in failures caused by cracks propagating upwards from the base of the road structure. Diekmann said that simply milling off the top layer and adding a new thin wearing course will be sufficient for repairs. As a result, using foamed bitumen in road recycling not only provides financial savings when the work is carried out, it provides a substantial future reduction in repair costs.
The massive WR4200 is Wirtgen's top-of-the-range recycling solution, a machine combining milling, mixing and paving technologies. Features of the WR4200 include the twin shaft pugmill as well as a variable milling drum, a fixed milling drum, spreading auger and a paving screed (a Vögele MB500). The firm's 2200CR is a slightly more compact recycling solution that is based on the W2200 milling machine and does not feature the pugmill or the second planning drum, although it is fitted with a
Wirtgen reckons it makes the most sophisticated spraybar systems on the market and these units are also self-cleaning to minimise maintenance. According to Diekmann, some rival machines have fixed spraybars that require the machines to be kept at a constant speed while operating, while the microprocessors in the Wirtgen machines will adjust the various flow rates and levels accordingly.
Because it is a cold process the material does not need to be compacted immediately, which is of benefit in scheduling. Diekmann added, "For compaction you need optimum water content."
Wirtgen's KMA220 recycling plant has added another capability as this mobile machine can carry out the same material recycling and mixing processes at a specific location that the firm's WR models carry out on-site. The KMA220 can be used to mix cement and foamed bitumen. If the cement is left out of the mix, the material can also be stockpiled for use several months later and a crust will form on the surface that holds in the moisture content.
Wirtgen has developed its improved WLB10S laboratory-scale plant to meet demands from contractors for a unit that can be used to optimise foamed bitumen grades for each application. Diekmann said, "You can do test samples and find out the optimum bitumen content for the material."
The potential for machines like the WR4200 is particularly good for the Chinese market as using this type of equipment would allow the highway authorities to repair long stretches of damaged or worn roads comparatively quickly.