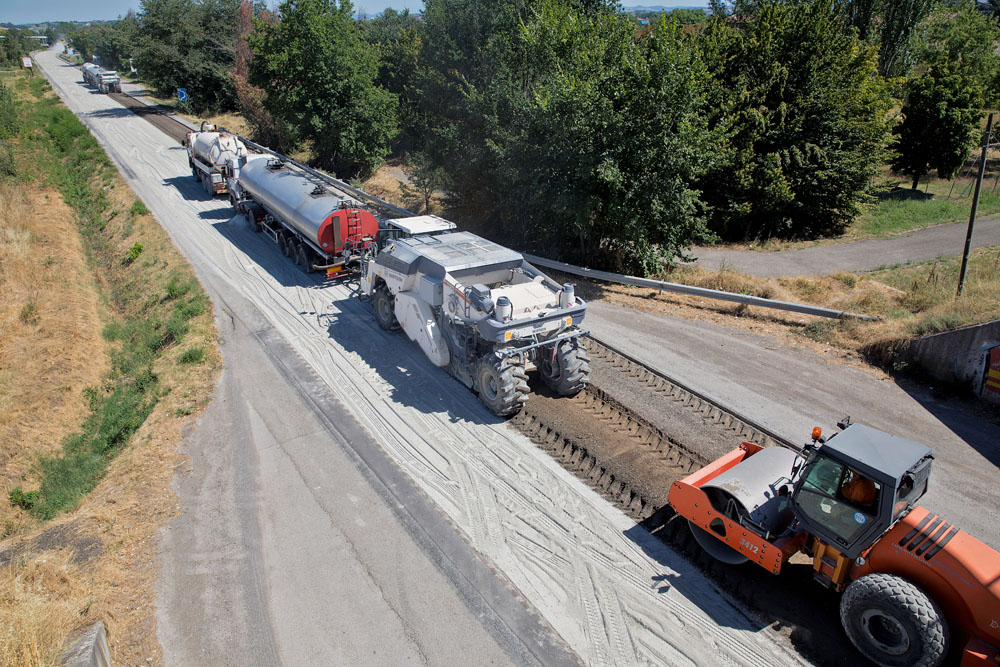
The pressure to conserve materials in road construction means that resource-saving technologies are more in demand than ever before.
Roads subjected to continuous and heavy traffic often show signs of damage that extend down to the road base. To eliminate this damage, the entire road needs structural rehabilitation. Full reuse of the milled material as well as its cost-effective treatment make cold recycling with foamed bitumen efficient and economical.
Foamed bitumen is produced by injecting small quantities of water and air into hot bitumen under high pressure. The water evaporates and makes the bitumen foam up to 15-20 times its original volume. The foam is then injected into a mixer through injection nozzles and mixed into cold and moist construction materials. The quality of the foamed bitumen is primarily described in terms of the parameters ‘expansion ratio’ and ‘half-life’. The greater the expansion ratio and half-life, the more easily the foamed bitumen can be processed.
Cold recycling with foamed bitumen is attracting increasing interest in road construction for asphalt road rehabilitation. It allows the paving of flexible and durable base layers, providing a suitable foundation for the final, thinner asphalt surfacing. New technology is used to produce foamed bitumen from normal bitumen which has been heated to approximately 175°C. With the in-situ method, a precisely dosed quantity of binding agent is added to mineral aggregate inside the Wirtgen 2200 CR or 3800 CR cold recycler or the soil stabilisers of the WR series, using microprocessor-controlled injection systems.
The cold recycling process has proven its worth around the world. In practical use, there are two different methods: an in-situ approach using wheeled or tracked Wirtgen cold recyclers, and the in-plant method using the Wirtgen KMA 200i, a mobile cold recycling mixing plant. The methods allow a large number of materials to be recycled such as milled asphalt, crushed asphalt or new material. The application range for foamed bitumen is varied, and it can also withstand very high traffic loads.
The Ayrton Senna Highway in Sao Paulo is used by more than 250,000 vehicles every day, 15% of them trucks. During the rehabilitation project in 2011, milled material from the asphalt pavement was recycled with foamed bitumen in a Wirtgen cold recycling mixing plant and repaved in two layers by a road paver.
In Greece, the cold recycling projects carried out with foamed bitumen back in 2003/2004 on the motorways between Iliki, Korinthos and Athens have been demonstrating their strength for more than 10 years. These have been carrying traffic volumes of 40,000 vehicles/day including a 25% share of heavy vehicles.
To achieve such results, extensive preliminary tests must be conducted on the entire pavement structure, while the mix produced with foamed bitumen must pass a rigorous mix design test.