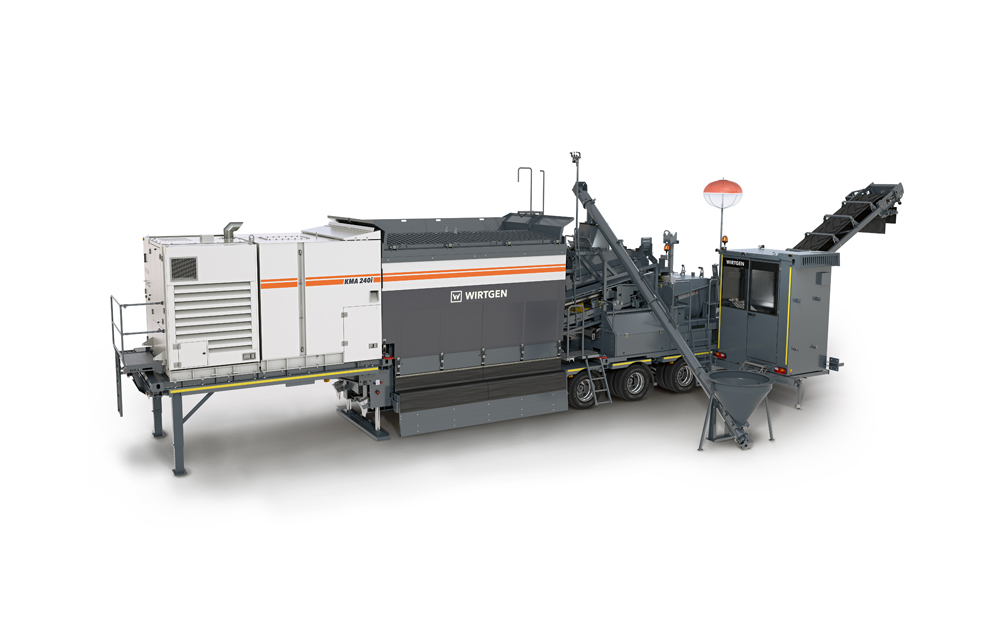
The KMA 240(i) is a mobile, cold recycling mixing plant that is capable of processing 240tonnes of material from a variety of construction materials/hour. Using this latest version of the KMA, users can recycle construction materials into road construction in the form of high-quality mix. The unit also delivers a quality product and the firm claims that roads built using its output offer high bearing capacity, resistance to deformation, and long service life.
The KMA 240(i) cold recycling mixing plant produces mix/cold mix that can be paved immediately and is suited to producing different types of bound base layers. In addition to cement-treated base layers (CTB) and roller-compacted concrete (RCC), the machine can also be used to produce bituminous bound base layers (with emulsion or foamed bitumen). The different mixes/cold mixes can be used for a wide range of applications, including highway construction, road and path construction, and the construction of parking lots or industrial areas.
The cold recycling mixing plant is mounted on a flatbed semitrailer and has its own engine unit. This mobile design allows the system to be moved to different locations and set up rapidly. In its new model, Wirtgen has combined the advantages of the earlier KMA 220(i) with improved mixing performance and an innovative cement metering system with automatic self-calibration using static weighing.
Power comes from an economical, low emissions, six-cylinder diesel located inside a noise-insulated housing. The machine can produce a full 20tonne truckload of mix every five minutes. As a result, sections of a cement-treated or bituminous bound base layer with a working width of 4m and a paving thickness of 150mm can be completed over a length of 1400m/day.
The KMA 240(i) can process a large variety of non-cohesive base materials, which wheeled loaders feed to the hopper via vibrating grids. It can produce mixes/cold mixes from a wide variety of new granular mixtures or various milled materials and binding agents. Asphalt milled material, all other non-cohesive materials reclaimed from old road surfaces, and materials from RC processing can all be used to build new road surfaces. The ability to reuse the material results in high CO2 and energy savings with minimal construction costs and project periods.
Silos or tank trucks supply the cold recycling mixing plant with binding agents, such as hot bitumen, bitumen emulsion, and cement. The metering of the input materials and binding agents, the ratio of which is determined in advance by preliminary tests in the road construction laboratory, is monitored by a proven microprocessor control system. The KMA 240(i) can load the new, homogeneous mix directly onto trucks or deposit it continuously on a stockpile. Loading or depositing can be carried out by the discharge conveyor that can swing 55° to either side.
The KMA mobile cold recycling mixing plant can be located in the immediate vicinity of the site, saving time and truck capacity and making it possible to achieve up to 70% fewer CO2 emissions through cold processing, a 90% reduction in transport volumes, and up to 40% lower construction costs, while high-quality building materials can be reused entirely.