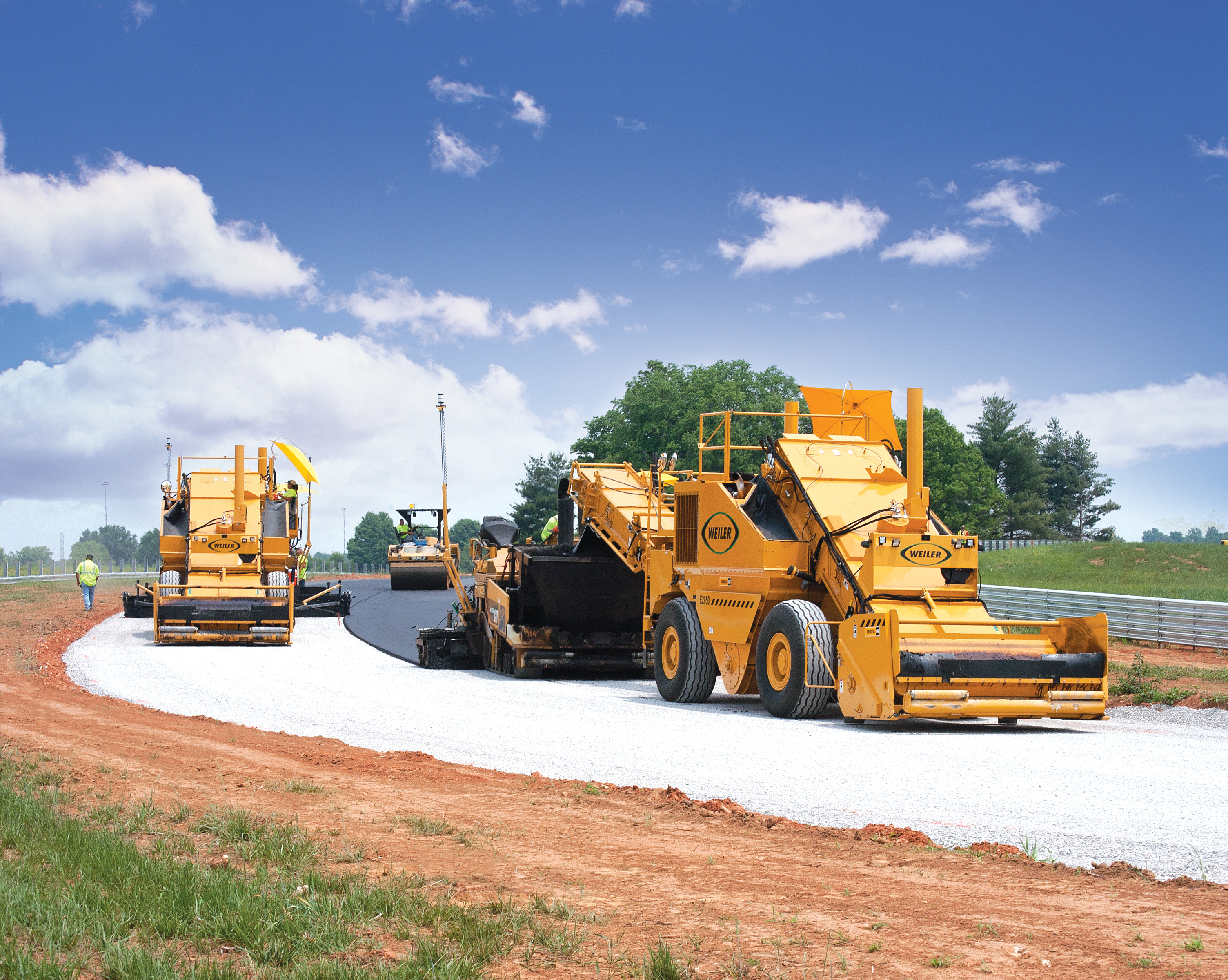
Saving construction costs and meeting tight tolerances, sophisticated technology has helped deliver a quality racetrack surface within tight time constraints. The National Corvette Museum (NCM) in Bowling Green, Kentucky, lies close to Interstate 65 and now features a brand new racetrack, constructed with the assistance of the latest machine control technologies.
The recently built NCM Motorsports Park includes a 5.15km road course, which was constructed to precise tolerances. To deliver the track surface, sophisticated new technology was used during earthmoving and then later with the road construction operations.
“During rough grading, the dozers installed with
The technology was so deeply embedded that, when museum officials visited the job site a few days before work began, they were unclear as to the layout of the track as there were no stakes to show the course.
The NCM Motorsports Park will serve many purposes. It is a test track for Corvette cars, with the Corvette museum and a General Motors factory both lying close at hand. It also will be used for various types of driver training, while car clubs can also rent the track.
A race circuit project requires smoothness, and the NCM park was no exception, with specifications prohibiting deviations of more than 3mm around the track. Another specification required evenness of the longitudinal joint in the centre of the course surface.
“There could not be a cold longitudinal joint,” said Chris Higgins, engineering manager at Scotty’s. That meant two pavers worked in tandem, and the joint was compacted while still hot. “It’s really like there isn’t a joint,” he added.
Also required on the job were material transfer vehicles (MTVs); in this case Weiler E2850s. The MTVs were used to deliver a constant flow of hot mix and allow the pavers to work continuously at a consistent speed.
Another technique to optimise smoothness was the use of non-stop paving of the track during placement of the surface lift. “The final day of surfacing on the track consisted of 13 hours of nonstop paving with pavers side by side to eliminate the joint in the track,” said Kenny Reynolds, paving manager at Scotty’s. “The transfer machines and pavers were fuelled while they were all moving to eliminate the crew from stopping.”
A tight timeframe also proved to be a challenge. Wet weather delayed the start of the project, so technology helped make up for lost time. “It needed to be done by mid-July of this year, and we didn’t start until mid-summer of last year,” Higgins said, adding that the combination of a large earthmoving requirement and poor weather made for a tight schedule.
The track is a road course, not an oval. Most corners were sloped at 1.5-2.5%, primarily for drainage and not banking. While time was a factor, smoothness and precision were also of major importance.
“Smoothness is key out here,” said Mike Law, vice president of materials for Scotty’s. “It needs to be one of the smoothest jobs we’ve ever done. Racing at speeds of 180mph—well, it better be smooth.”
Time pressures were a part of the job, leading to the start of work before all plans were finalised. “The museum wanted to start, but the track wasn’t fully designed, so we did somewhat of a phased construction,” Higgins said.
Scotty’s crews input the job information into Trimble’s Business Center – HCE software that transforms a design into a 3D site plan. Crews started moving bulk materials in areas they knew would be close to grade, even if final plans were not yet available.
“We used a great deal of machine control,” Higgins said. “With the way the design changes came in, we were constantly modifying the site during the project.”
The software easily handled revisions to the site plan, which was updated on each machine by way of wireless signals. The changes could be made without a word of communication between Scotty’s central office, the on-site foremen and machine operators. “Those kinds of changes would not have been feasible with staking,” Higgins said. “We had about 15 pieces of automated equipment in here at one time. We would just make the changes on the site plan and they would be incorporated into all machines.” The machine operators would then work to the updated design.
The project slowed during the depths of winter, though that downtime had been planned and actually improved the quality of the track, said Mitch Wright, general manager of the NCM Motorsports Park. “We had most of the rough grading done by mid to late November,” Wright said. “That allowed the ground to settle, which over the long run will pay huge dividends. It also helped us find areas that held water. We provided some additional drainage without having to impact the subgrade.”
The GPS and total station controlled the scrapers and dozers and made even the rough grading work considerably more precise; a solid start needed to help reach the more precise tolerances later on. After rough grading, dense-grade aggregate was laid down to a depth of 220mm using pavers for precise depth and elevation control.
Next came a 64-22 asphalt base course that was compacted to 51mm. “It’s a standard Superpave mix that we use on many jobs,” said Law.
The mix for the next two lifts, each 38mm, was a very stiff 82-22 and anything but routine. “We’re topping this off with probably the most premium mix we’ve ever used,” Law said. “The museum worried about tyre wear.” Scotty’s consulted with aggregate experts to help find the perfect stone to provide grip and skid resistance.
The liquid asphalt was also innovative. “It’s very highly polymerised,” Law said. “Once we lay this down, it’s going to stay in place for a long, long time.” Scotty’s developed all the mixes and polymers in its technology centre.
Cat AP1055D and AP1055E Asphalt Pavers laid down the mix, working side-by-side to leave a hot-on-hot longitudinal joint. The two Weiler E2850s that transferred the mix to the pavers also provided remixing for temperature uniformity and elimination of segregation.
The track width was typically 11m. The lead paver worked at a width of 5m. The second paver worked closely behind the first paver at a width of 6m. Average paving speed was about 4.5m/minute, based on hourly tonnage, paving depth and paving widths. The relatively low paving speed allowed the pavers to move continuously and not out-run the trucking. That pace also allowed the compactors to match the pavers’ production. “The pavers are doing just fine working at those widths,” Law said. “The auger is spreading material out. We’ve put extended screeds on there and it’s compacting equally all the way across.”
Because Scotty’s technology team was used to working with Trimble’s Business Centre – HCE software, making the step to 3D paving was accomplished easily on site.
The models automatically generate uncompacted surface designs for the 3D paving system. As the final step in executing the construction of the racecourse, the designs guide the paver to make adjustments automatically that place slightly more material above low areas and slightly less material in high areas.
The 3D paving system links with the Cat Paver’s conventional 2D grade control package. The design file is stored in the control box installed on the screed. The technology team installed a mast with a prism (target) on top on the right side of the screed. There is also a slope sensor on the bottom of the mast.
Trimble Universal Total Stations, located strategically around the site, tracked the prisms as the pavers moved around the racecourse. The Universal Total Station sends a constant stream of signals with precise measurements to the prism on the screed. The prism relays those measurements to the controller where they are compared to the master design file calculations.
If elevation corrections are needed, the commands are sent through the conventional 2D grade control system—to the right tow point in this instance. The left side of the screed is under slope control, using the calibrated slope sensor.
As the pavers move forward, the prism is picked up by the next Trimble Universal Total Station on the jobsite to ensure constant 3D connections. In all, 10 total stations were used on the Scotty’s site to ensure the paver could do a single long run.
One of the most impressive benefits of the 3D paving system was its ability to use slope control on the joint match side of the trailing paver screed and have consistent height match. This accomplishment underscores the speed, accuracy and inter-connectivity of the Trimble system.
“The biggest benefit of 3D paving is it precisely and accurately achieves the design the designer wanted,” Higgins said.
Four Cat CB64 rollers handled breakdown, intermediate and finish phases of compaction. For the breakdown phase, two compactors were set in high amplitude and low frequency. Each roller made four vibratory passes behind its designated paver to achieve 92-93% density.
Because the second paver worked a width of 6m, the pattern for the second CB64 would require more passes. The quality control technician had the first CB64 drop back and make two passes along the longitudinal joint on the wider side to equalise the patterns and allow both rollers to stay tight to the pavers ahead of the tender zone.
The other two CB64s were set in high frequency and low amplitude for the intermediate phase. They made two vibratory passes behind the tender zone, starting the pattern when the mat was around 80°C. They dropped back occasionally and made long static passes around 60°C for the finish phase. Final density ranged from 94-95%.
Higgins said the technology, at all steps of the process, enabled enormous productivity gains. “We never would have finished on time without it,” he said.
The technology also delivered significant cost savings, Scotty said. “On this job, we talk about 3D and GPS, it probably saved us US$250,000 just on engineering,” he said. “When we save money, that enables us to be cheaper and to win bids, and it really helps our company prosper.”
Monty Boyd, president and chief executive officer of
The job called for Scotty's Contracting to pave a 5km total loop track, which can be reconfigured into separate 1.6km and 3.2km loops. Because they are Le Mans-style tracks, the elevation changes are frequent and cover about 9.1m from top to bottom, and they must be smooth and consistent regardless of which configuration the cars are driving.
The team at Scotty's saved between $150,000-$200,000 in staking and survey costs using grade control and 3D paving technology. In total, the firm laid 60,000tonnes of asphalt and 85,000tonnes of base stone, finishing the project a full 20 days ahead of schedule.