The historic city of Raleigh in North Carolina is one of the few cities in the US that was planned and built specifically to serve as a state capital and its population and traffic volume have grown enormously in recent years An indicator of Raleigh's growth has been the need for an expanded roadway system to serve Wake County. As early as the 1970s there were plans for a Western Wake Expressway. This developed into a 112km, interstate-grade beltway, known as the Raleigh Outer Loop, which will encompass Ral
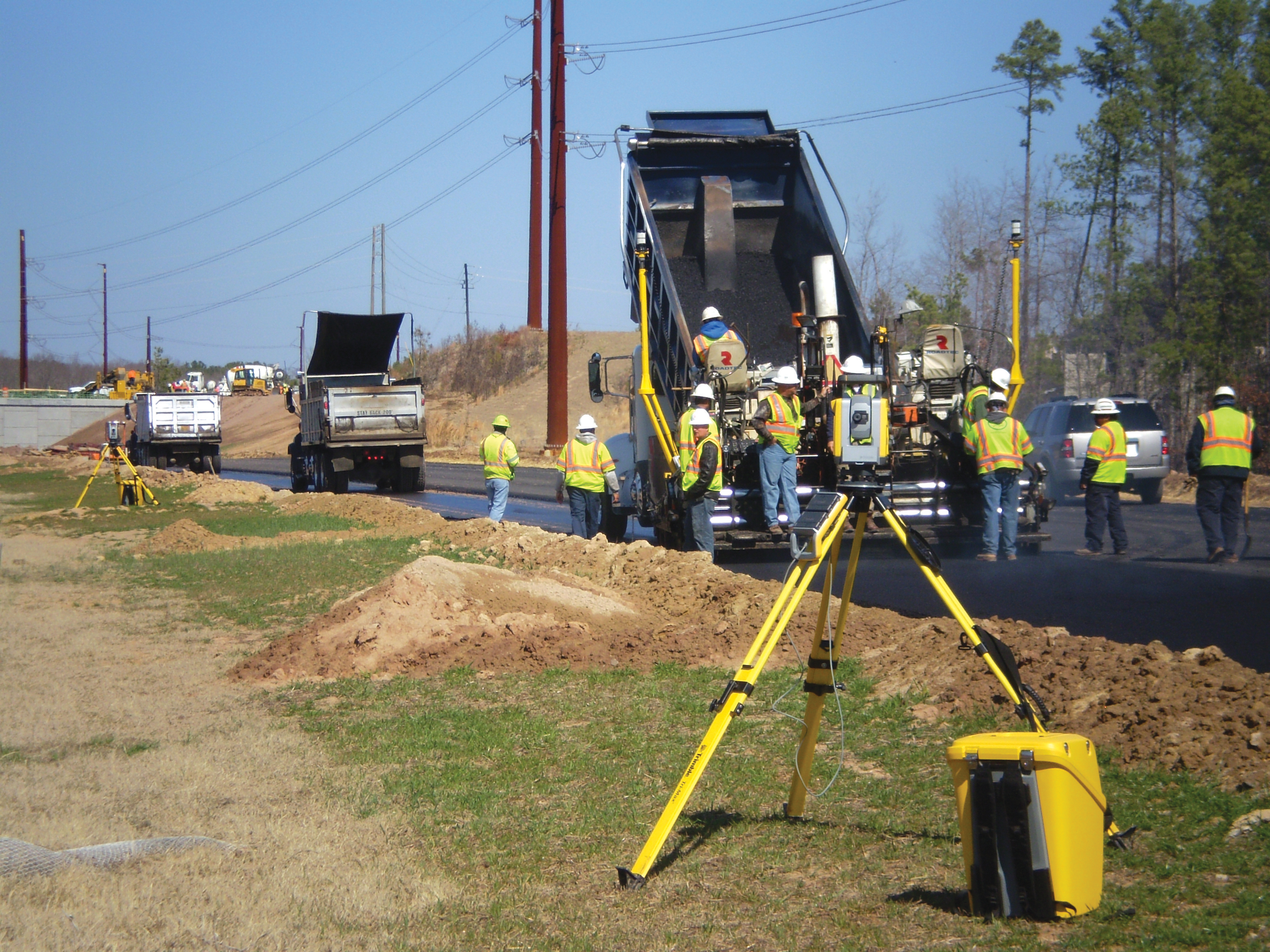
The machine control system was guided by robotic total stations placed at the roadside
The historic city of Raleigh in North Carolina is one of the few cities in the US that was planned and built specifically to serve as a state capital and its population and traffic volume have grown enormously in recent years
An indicator of Raleigh's growth has been the need for an expanded roadway system to serve Wake County. As early as the 1970s there were plans for a Western Wake Expressway. This developed into a 112km, interstate-grade beltway, known as the Raleigh Outer Loop, which will encompass Raleigh and the towns of Apex, Cary, Garner, and Morrisville. To complete it, there will be three other segments in addition to the Western Wake Expressway.“We worked on a stretch of the Western Wake Expressway running from Cary and looping south to Apex,” said Ryan Graham, project engineer for The
The US$30 million, 22.5km project for Lane Construction forms part of NCDOT’s $460 million contract for completing the western segment of the Raleigh Outer Loop. The Western Wake Expressway is brand new construction and will be a toll road when completed. The prime contractor is Raleigh-Durham Roadbuilders, which is a joint venture between
Lane’s portion of the project started at the beginning of 2011. Lane used a 12-worker paving crew, a surveyor, a project engineer, and a superintendent dedicated to the project.
“We understood that the quality of the finished road surface was dependent upon the quality of the subgrade,” Graham said. “That’s why our asphalt paving quality was critical.”
Lane Construction was required to produce top-shelf asphalt paving and to coordinate with the other contractors on the project. The key to the contractor’s productivity and accuracy on this job has been its use of sophisticated machine control systems, with the latest equipment from
Graham said, “We used the Trimble PCS900 3D paving control system on our paver, supported by four Trimble SPS930 universal total stations.”
Lane used a
“The contract called for the placement of 200,000tonnes of asphalt, so we wanted to minimise waste and ensure accuracy across the three-lane highway,” Graham said.
The company had to pave two 3.65m wide lanes and a 4.26m wide lane, and all the on-ramps and off-ramps and acceleration lanes as well. As the expressway widens out to four lanes temporarily in sections, the total width also expanded from 11.6m to13.7m wide.
The Trimble PCS900 paving system was a 3D automatic screed control package for use in a stakeless environment and helped boost smoothness as the machine automatically implemented the design.
“The Trimble technology helped us since our tolerances were very tight,” said Graham.
He explained that if the firm was over 3mm too high it would have to go back and mill or if it was 6mm too low it would have to pay for the extra material on top. Our milling and concrete costs would have been substantial without the Trimble systems, just because the road was that complex.”
Lane Construction builds its own digital 3D models, such as the one the Roadtec paver equipped with the Trimble system relies on. “Our company works on $1 billion worth of work annually so we have 10 model builders on staff,” said Joe Grenier, GPS manager for Lane Construction.
He explained that the firm invested the time to analyse the existing conditions every 7.6m and compared that to the theoretical finish grade, and then added in the compaction factor of the asphalt. Grenier said, “We created what we call an ‘uncompacted model’ to ensure we could hit within that tolerance.”
Grenier said that learning the uncompacted model procedure and getting it ironed out was probably one of the biggest challenges the company faced at first. A second challenge was mastering the Trimble system for pavers, although it did have some in-house experience to draw upon. “We’re very familiar with building models and running machine control systems on earth movers, so taking advantage of that technology for asphalt paving was a natural extension, but still new to us,” Grenier said.
“But once we figured it out,” Graham added, “the tangible benefits were apparent. By far the biggest benefit was to not have to go back and mill stretches of completed asphalt paving. With the tight tolerances on this project and with all of its complexities, it would be expected to have the expense of a milling crew out there all of the time—but we didn’t. With the success we’ve seen on this project, we bought a Trimble PCS900 for a paver we have working in South Carolina and we’re looking at two additional systems.”
Grenier continued, “The big reason why the paving control system was so valuable is that concrete is so expensive. We saved a lot of money on milling and concrete material. If we were too low with the asphalt surface, then we would need to fill that with the more expensive concrete.”
Anthony Todd, assistant corporate survey manager, for Lane Construction said, “We achieved more accurate results using the Trimble technology. Higher accuracy means better quality.”
Trimble dealer, SITECH Mid-Atlantic was also helpful, providing extensive back up for the contractor. Meanwhile the team involved in the work believes that the road will offer better smoothness for drivers, lower maintenance requirements and greater overall working life. “When people drive on it, they probably don’t realise all the work that went into what’s under that concrete, because they’re just seeing the concrete surface,” Graham said. “But that’s fine, all of us who worked on it know.”