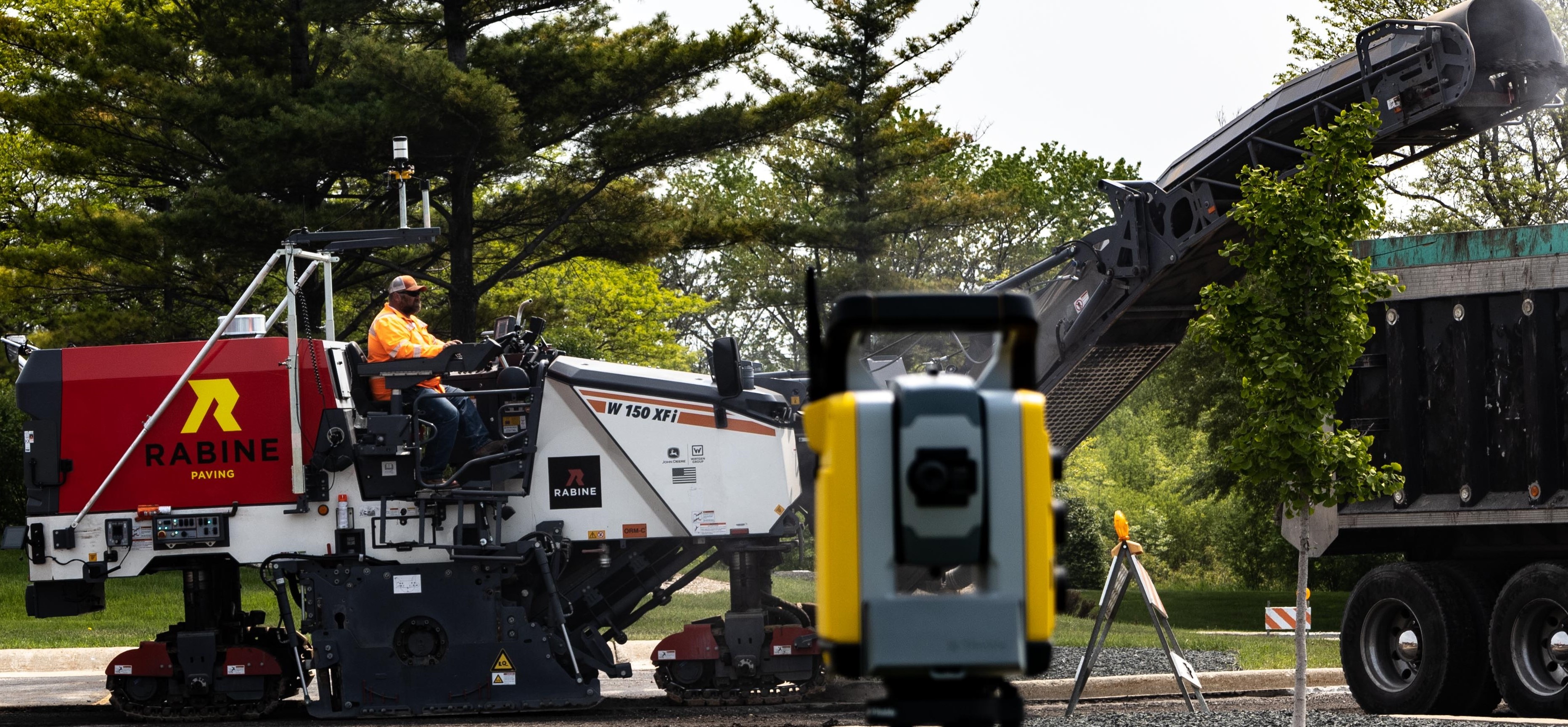
The specialist US contractor Rabine Paving is taking a lead in the milling market by being an early adopter of the latest Trimble Roadworks Paving Control Platform for Mills and Cold Planers. This sophisticated technology is being used along with the Trimble SPS930 Universal Total Station and Trimble Business Center Software to deliver improved efficiency and quality profiles even on complex surfaces, ADA slopes, drainage.
“When it comes to pavement restoration, surface smoothness, drainage and ADA adaptations are the primary challenge,” said Kyle Miller, director of operations at Rabine. “We have great operators who are able to adjust to these complexities and deliver optimal results—but we’re always looking to give them every advantage. That’s where technology comes into play.”
In early 2023, Rabine became a beta tester for the new Trimble Roadworks Paving Control Platform for Mills and Cold Planers. For milling, a 3D design is displayed to the machine operator showing areas that are on, above or below ideal grade, comparing the actual drum position and slope with the digital design. The platform guides the milling drum to cut the defined depth and slope without needing string lines or manual adjustments.
“It’s really the next level and an opportunity for us to improve our efficiency, field safety and precision,” said Miller. “It’s also a key component of our efforts to attract new operators to our industry.”
The contractor has been running 3D concrete screeds for several years, though its milling remained 2D. When Miller joined the company in January 2023, he looked to 3D for paving applications. He explained, “I came from the civil and earthworks industry where 3D machine control is well established. I wondered if there was a place for 3D in milling workflows.”
A skilled milling operator can see the changes of slope and contours necessary for drainage and ADA requirements in a parking lot, Miller said and continued, “If a third-party inspector finds any deviation outside the specs, we have to rework, which is costly. I believed that the same advantages we’ve had with the screeds could be realised with a more automated milling solution.”
He talked to the local Trimble Heavy Civil Construction dealer, SITECH Midway, about using 3D. This opened the door to beta testing the newest Trimble milling solution. The Roadworks Paving Control Platform for mills and cold planers was installed on a Rabine paver and was on a jobsite in May 2023.
The first project that Rabine put the new 3D mill solution to work on was a mill job at an office building/distribution centre in Wisconsin. “This project proved to be a perfect demonstration of the 3D milling capabilities,” said Miller. “It’s a small employee parking lot, but with complex slopes and a roundabout. The software automatically adjusted to slopes and roundabout radius at a fairly quick speed.”
The 3D milling workflow is straightforward, according to Miller. The crew sets up control, shoots the edges, curves and basins and then uploads it to Trimble Business Center to create 3D milling plans and quality and production reports.
“The technology automatically calculates the surface so we’re able to accurately read the profile ahead of time,” said Miller. “It takes the operator's guesswork out of the equation. Instead of the operator having to gauge mill depth based on experience, the Roadworks solution mills to the design profile within the designated precision. It allows our crews to optimise material quantities that are milled on a site.”
Rabine’s relationship with SITECH Midway was important as the dealer had a team from the contractor at its office to learn the basics of total station operation and 3D machine control. “Not only did they introduce us to the key functionality of the platform, but they help us in other ways, such as building profiles, walking the job sites and working with the operators to answer questions or troubleshoot,” said Miller. “Our jobsite is safer because we can reduce ground support near the mill machine pinch points. This technology allows us to address drainage or ADA slopes with greater accuracy, speed, and operational ease, and reduce material quantities so we’re more sustainable.”
“Technology allows us to be more competitive because of our increased production,” said Miller. “Even more important is our ability to bring new or less experienced operators up to speed quicker. We also believe it’s going to attract new talent to our team.”
Another advantage of the 3D milling system will be the detailed as-built conditions data. Looking forward, Miller added, “If we’ve milled a particular site in the past, we can provide value to our clients because we already have the surface file that we can reference.”
“The value of the solution goes beyond the mill,” Miller said. “I can see us using this system for subgrade or finished grade as a way to guarantee yield and improve quality. Overall, we are certain that this investment is going to pay off.”