Part of an iconic US bridge has been given a new lease of life, as Mike Woof reports The western section of the historic Oakland Bay Bridge in the US state of California has recently benefited from a series of improvements to strengthen its structural integrity and also upgrade the running surface. Contractor OC Jones & Sons of Berkeley CA, paved large portions of the bridge, taking on two different projects as part of the work. First was placement of the specialised epoxy on the self-anchored suspension (S
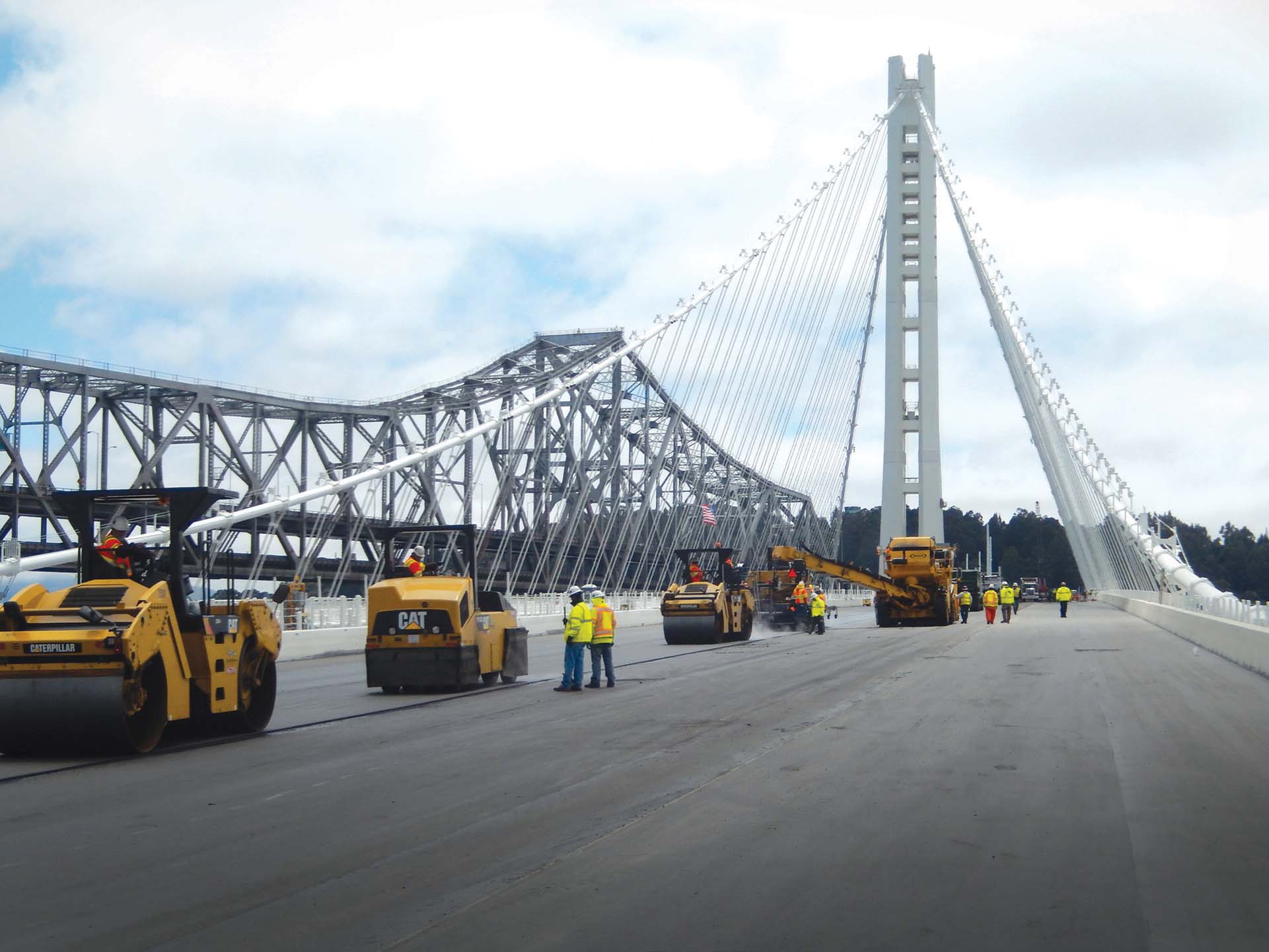
Compaction and rolling patterns were closely monitored given the challenging material
Part of an iconic US bridge has been given a new lease of life, as Mike Woof reports
The western section of the historic Oakland Bay Bridge in the US State of California has recently benefited from a series of improvements to strengthen its structural integrity and also upgrade the running surface. Contractor7707 OC Jones & Sons of Berkeley CA, paved large portions of the bridge, taking on two different projects as part of the work.
First was placement of the specialised epoxy on the self-anchored suspension (SAS) portion of the new bridge. The second project was the new transitional paving on the Oakland touchdown side of the new bridge, stretching some 1,289m from beyond the toll plaza to the new approach area. The2451 California Department of Transportation (Caltrans) wanted a new surface on the approach, and also corrections to grade and slope.
Carrying some 280,000 vehicles/day, the bridge has a heavy traffic loading and the new running surface had to be sufficiently robust to cope with the application. Two 25mm lifts of epoxy asphalt concrete (EAC) were placed on the eastbound and westbound lanes of the Bay Bridge’s new SAS Span, with the material being selected due to its durability, skid resistance and light weight. The material used was unusual, and presented some challenges not normally seen with conventional asphalt concrete, according to Kelly Kolander, president and CEO of the contractor.
The EAC is essentially a 9mm mix that uses a two-part epoxy. One part is blended with AR 4000 paving oil and this is combined with a special dry aggregate and a separate epoxy resin, and mixed in a pug mill. The resultant EAC is then placed atop a two-part epoxy bond coat. That bond coat was applied to both the steel bridge deck and the first lift of EAC. The bond coat needed to be applied at a high application rate, using both a robotic device and spray wands. The epoxy products, as well as the technical support, were provided by Chemco Systems of Redwood City, CA.
“The EAC is significantly different from conventional AC in that once the material is produced from the batch plant, a chemical reaction begins as it is hauled to the project site,” project manager Bill Jensen said. “Due to this chemical reaction and extremely tight time and temperature requirements, consistency in travel time for the haul trucks and in the production of the material at the plant were crucial.”
To ensure efficient transport, OC Jones secured a haul route to the site with the help of the Californian Highway Patrol and Caltrans, to minimise delays from traffic disruptions. Once the material arrived, it was again tested before it could be placed through the paver. The window for mix placement was tight and closely monitored by testing personnel to ensure project specifications were met. The material then was approved for placement on the bridge deck.
The process had another complication as trucks and other machines were not allowed to travel on the paving lane after the bond coat had been applied, so the material had to be loaded from the side. As a result, OC Jones used a Weiler E1250A transfer vehicle on the job as the machine has a conveyor for offset paving, allowing the trucks and the Weiler machine to stay off the paving base and the bond coat.
As the E1250A does not have storage capacity, this helped keep its weight down, an important factor for bridge works. The material was discharged into a2294 CAT AP1055E paver, which used non-contact averaging skis to ensure better ride quality.
Compaction and rolling patterns were closely monitored and achieved with Cat CB54 rollers and Cat PS150C rubber-tyred rollers.
The compactors typically made three complete passes, with movement up and back counting as a single pass.
Another important aspect of the project was the need to clean out the transfer vehicle and paver after every pass, typically 670m in length. Unlike conventional AC, the EAC material is not thermoplastic, and cannot be reheated. Once the chemical reaction occurs, the mix remains hard and this required removing any built-up material in the paver’s auger chamber as well as inside the transfer vehicle to prevent cured EAC from falling onto the finished mat, according to OC Jones’ area manager Kevin Goddard. The bridge was shut down over one holiday weekend as the paving crews reconstructed the approach area on the Oakland touchdown side. That portion of the project did not require the placement of EAC. Instead, the crews worked with conventional AC mix, as well as an open-graded asphalt cement, placing some 17,200 tonnes of material over an area of 93million m2. That project also had challenges and planers had to remove mix over much of the area before repaving could begin. So large was the required milling volume that up to seven machines worked continuously for 36hours. The levelling was particularly extensive in some areas. The eastbound direction required a large profile correction and required removing asphalt at depths up to 0.9m. “Complicated cross-slope corrections, levelling and new construction to tie into the new bridge structure from the existing toll plaza area proved challenging, given the tight time constraints,” said area manager Jim Gallagher.
“There was an incredible amount of coordination between the AC plants, grinders, trucking, traffic control and access points,” Jensen said. “Over half of the material placed was required to correct cross-slope to aid drainage, establish a new roadway profile, and level uneven pavement, which is all very time-consuming.”
Additionally, the westbound portion goes from five lanes to 20 lanes at the toll plaza, then back down to five lanes. This made the joints and lane lines a major challenge but the machines handled the variable widths well. Equipment used included Cat AP1055E and 655D asphalt pavers, Cat CB64, CB54 and PS 150C rollers, as well as the Weiler E1250A transfer vehicle.
The western section of the historic Oakland Bay Bridge in the US State of California has recently benefited from a series of improvements to strengthen its structural integrity and also upgrade the running surface. Contractor
First was placement of the specialised epoxy on the self-anchored suspension (SAS) portion of the new bridge. The second project was the new transitional paving on the Oakland touchdown side of the new bridge, stretching some 1,289m from beyond the toll plaza to the new approach area. The
Carrying some 280,000 vehicles/day, the bridge has a heavy traffic loading and the new running surface had to be sufficiently robust to cope with the application. Two 25mm lifts of epoxy asphalt concrete (EAC) were placed on the eastbound and westbound lanes of the Bay Bridge’s new SAS Span, with the material being selected due to its durability, skid resistance and light weight. The material used was unusual, and presented some challenges not normally seen with conventional asphalt concrete, according to Kelly Kolander, president and CEO of the contractor.
The EAC is essentially a 9mm mix that uses a two-part epoxy. One part is blended with AR 4000 paving oil and this is combined with a special dry aggregate and a separate epoxy resin, and mixed in a pug mill. The resultant EAC is then placed atop a two-part epoxy bond coat. That bond coat was applied to both the steel bridge deck and the first lift of EAC. The bond coat needed to be applied at a high application rate, using both a robotic device and spray wands. The epoxy products, as well as the technical support, were provided by Chemco Systems of Redwood City, CA.
“The EAC is significantly different from conventional AC in that once the material is produced from the batch plant, a chemical reaction begins as it is hauled to the project site,” project manager Bill Jensen said. “Due to this chemical reaction and extremely tight time and temperature requirements, consistency in travel time for the haul trucks and in the production of the material at the plant were crucial.”
To ensure efficient transport, OC Jones secured a haul route to the site with the help of the Californian Highway Patrol and Caltrans, to minimise delays from traffic disruptions. Once the material arrived, it was again tested before it could be placed through the paver. The window for mix placement was tight and closely monitored by testing personnel to ensure project specifications were met. The material then was approved for placement on the bridge deck.
The process had another complication as trucks and other machines were not allowed to travel on the paving lane after the bond coat had been applied, so the material had to be loaded from the side. As a result, OC Jones used a Weiler E1250A transfer vehicle on the job as the machine has a conveyor for offset paving, allowing the trucks and the Weiler machine to stay off the paving base and the bond coat.
As the E1250A does not have storage capacity, this helped keep its weight down, an important factor for bridge works. The material was discharged into a
Compaction and rolling patterns were closely monitored and achieved with Cat CB54 rollers and Cat PS150C rubber-tyred rollers.
The compactors typically made three complete passes, with movement up and back counting as a single pass.
Another important aspect of the project was the need to clean out the transfer vehicle and paver after every pass, typically 670m in length. Unlike conventional AC, the EAC material is not thermoplastic, and cannot be reheated. Once the chemical reaction occurs, the mix remains hard and this required removing any built-up material in the paver’s auger chamber as well as inside the transfer vehicle to prevent cured EAC from falling onto the finished mat, according to OC Jones’ area manager Kevin Goddard. The bridge was shut down over one holiday weekend as the paving crews reconstructed the approach area on the Oakland touchdown side. That portion of the project did not require the placement of EAC. Instead, the crews worked with conventional AC mix, as well as an open-graded asphalt cement, placing some 17,200 tonnes of material over an area of 93million m2. That project also had challenges and planers had to remove mix over much of the area before repaving could begin. So large was the required milling volume that up to seven machines worked continuously for 36hours. The levelling was particularly extensive in some areas. The eastbound direction required a large profile correction and required removing asphalt at depths up to 0.9m. “Complicated cross-slope corrections, levelling and new construction to tie into the new bridge structure from the existing toll plaza area proved challenging, given the tight time constraints,” said area manager Jim Gallagher.
“There was an incredible amount of coordination between the AC plants, grinders, trucking, traffic control and access points,” Jensen said. “Over half of the material placed was required to correct cross-slope to aid drainage, establish a new roadway profile, and level uneven pavement, which is all very time-consuming.”
Additionally, the westbound portion goes from five lanes to 20 lanes at the toll plaza, then back down to five lanes. This made the joints and lane lines a major challenge but the machines handled the variable widths well. Equipment used included Cat AP1055E and 655D asphalt pavers, Cat CB64, CB54 and PS 150C rollers, as well as the Weiler E1250A transfer vehicle.