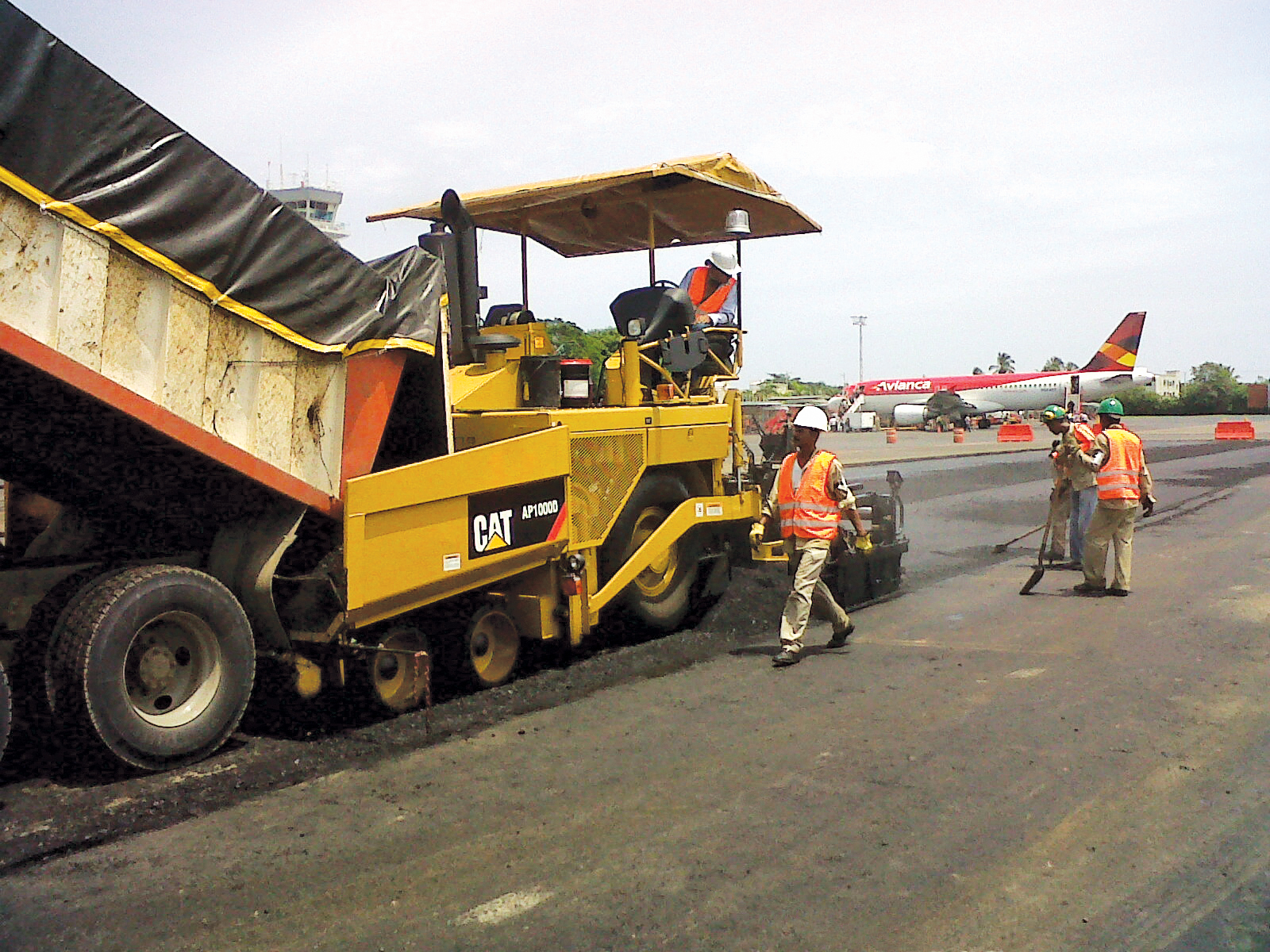
Cartagena, Colombia’s coastal city attracts large numbers of visitors, generating heavy traffic through the Rafael Nuñez International Airport. However the surface of the runway had suffered from heavy wear, r esulting in bumpy landings and this was in need of repair. In addition, engineers wanted to create a graded, ramped approach to aid with both take-offs and landings.
However, the volume of air traffic using the airport meant that construction work had to take place in a tight timeframe, between midnight and 5am only. The ramp work was a key element to the project at Rafael Nuñez International Airport but created its own challenges. The ramp had to be built higher than the rest of the existing runway and also required an extremely dense hot mix better able to handle the impact of the landing aircraft."The planes are bringing a lot of weight and force to that specific area, and the airport engineers wanted it reinforced," said Oscar Polo, civil engineer with Pavimentos Universale SA, the firm handling the work. "The mix has more fines to prevent damage to the plane tyres as they land. That material is expensive, so the planner didn't want to use it on the entire runway."
Plans called for milling the landing/takeoff ramp, then building it up with base material, and finally placing new asphalt. The rest of the runway also was paved, but not milled. The entire runway is 3200m long, of which 250m is considered part of the ramp. Pavimentos Universal milled at a depth of 140mm for the 250m and also used recycled materials for the ramp. Paving was carried out with a
Because of the warm, humid weather in Cartagena, Polo was able to have the mix delivered hours in advance. "It takes the mix a long time to cool," he said. "We usually have most of the trucks lined up before we start paving."
Many trucks arrived at the jobsite before midnight, so the firm knew there would be no transport problems before starting with each night's paving. The calculations for the amount of mix had to be precise. "The Cat Paver is very exact in the amount of mix it uses," he said. "The paver's consistency helped us calculate the proper amount."
The average of fines in the mix was 2-4 mm. To place the mix on the ramp portion, the paver worked across the width of the runway, in 40m increments. "That is what the specifications called for," Polo said. "Because of the fine materials, the consensus was that it made more sense to pave in shorter increments, and then reach compaction goals. With that level of fines, there can only be a few passes with the roller before the danger of damaging the mix becomes very real."
Paving over the width, and not length, of the ramp also meant less chance for wasting material during compaction. The material had to cool to at least 130°C before rolling and there were joints to consider too. Pavimentos Universal placed a mat at a width of about 8m; then left the adjacent 8m unpaved. Each night it placed five lifts of 40m. After completing the first three lifts, and leaving two of five stretches unpaved, the paver returned and filled in the missing lifts. "This allows the asphalt to cool enough so that we can work on it, and compact the joints, while also making sure we don't damage the fine material by working it too early and too extensively," Polo said
Handling compaction was a Cat CB534D which made two passes without vibration, and one pass with vibration. A Cat CB434D followed, making several static passes. Meanwhile a Cat PS150C pneumatic compactor was used between the CB534D and CB434D if more compaction was needed.
The mix on the main runway included larger aggregate, and cooled faster. As it had done during the ramp paving, Pavimentos Universale worked every 8-9m when handling the main portion of the runway.
Doha improvement
Upgrade works have been carried out at Doha International Airport (DIA) by Clearspan Technology Middle East (CTME). The company has expanded its operations by moving into the market for slipform paving concrete construction, in addition to its work with stressed hangar construction technology. As a part of its airport construction division, CTME acquired a G&Z S850 concrete slipform paver and has carried out two fast track projects for Qatar Airways at DIA, where flight traffic is increasing. Based on CMTE’s past project performance with Qatar Airways, it was awarded a six bay and a two bay apron expansion contracts. “The schedules were so tight that without our G&Z machinery the program would not have been possible.”
The projects were worth a total of US$7 million. The 500x138m six bay apron was the first project to be tackled while the 132x66m two bay area was the second to be completed. CMTE paved the aprons in alternating lanes and finished with fill-in lanes. As the project needed to be completed quickly, there was little room for error. With the success on the apron expansion projects, CTME is planning to bid similar projects in Qatar, where infrastructure expansion is planned as Qatar becomes a prominent destination in the Middle East Region.