An authority replaces container wharf pavement damaged by forklift loads in world's first commercial use of high-performance asphalt base course. By Paul Fournier
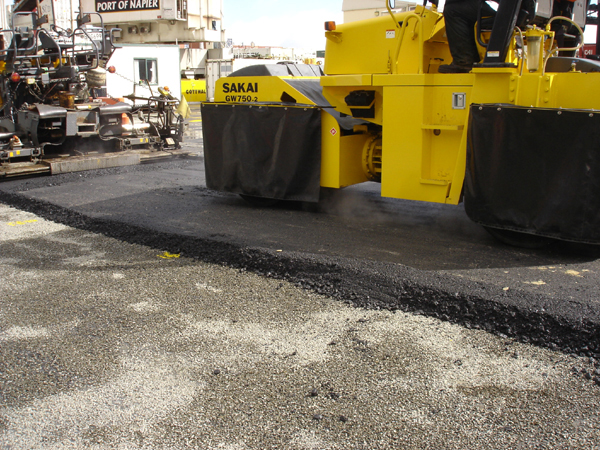
As mix cooled rapidly in the raw weather, the crew operated the Sakai pneumatic-roller in vibratory mode to expedite compaction
An authority replaces container wharf pavement damaged by forklift loads in world's first commercial use of high-performance asphalt base course. By Paul Fournier
New Zealand's Port of Napier recently replaced a heavily deformed section of pavement in its Container Terminal with high-performance asphalt mix incorporating technology never before used in a base course.Higgins Contractors of Napier removed the deformed pavement from a section of H8-K1 and re-paved the area using Highly Modified Asphalt (HiMA) technology developed by
Such pavement qualities are essential at the section near the edge of Kirkpatrick Wharf where forklifts loading and unloading shipping containers have imposed extraordinary repeated loads that caused premature pavement failure. Built in 2001 and 2002 as an access road, the pavement was never designed to accommodate forklift front-axle loads of 110tonnes.
Adding to the problem is the increasing number of container throughputs at the port, which have approximately doubled over the past ten years according to Clarke Curtis, senior engineering technician for the Port of Napier.
Within a few years, pavement damage from this activity produced ruts up to 85mm deep with deformation in the base course alone exceeding 40mm. Furthermore, ruts were causing forklifts to shake, requiring the Port of Napier to spend more money on maintaining them. Port officials decided to have the pavement reconstructed, but they wanted a pavement that could stand up to high forklift axle loads over a design life of 20 years.
At a meeting with Higgins Group, port officials approved the use of HiMA for the H8-K1 project.
Sean Bearsley, product development manager for Higgins Laboratory, said the trial could have major ramifications for pavements subjected to heavy loads or pavements with asphalt layer thickness limitations.
Robert Patience, Higgins group technical manager, designed the pavement structure and executed the H8-K1 project, removing the deformed section and re-paving it with HiMA technology in the base course and standard SBS-modified mix for the surface layer. This new pavement structure utilised 750mm of 4.5% Portland cement stabilised 0/40 crushed aggregate sub-base; 100mm of SP28 high modulus base course made using Kraton D0243 modified bitumen 40/50; and a 50mm SP14 surface course made using 5% SBS modified 80/100 bitumen. The base course was a continuous well-graded mix using six single-sized crushed coarse greywacke aggregate and one fine aggregate comprised of crusher fines or dust. No natural sand was used.
The content of the 40/50 penetration grade bitumen for the base course was formulated to be 4.3% of the mix mass, with Kraton D0243 modified polymer comprising 7.5% of the bitumen. Until the development of low-viscosity Kraton D0243, such an elevated polymer content would not have been practical.
While adding polymer to bitumen provides desirable benefits, generally as polymer content in bitumen binder exceeds 3% the binder viscosity increases, making asphalt mix gradually more difficult to produce in the plant and increasingly unworkable at the job site.
However, through changes in polymer design, Kraton D0243 polymer content can be raised well beyond 6%, even in harder bitumens. At the selected 7.5%, no adjustments were needed at the plant or in the field for the H8-K1 project.
On the day that Higgins paved H8-K1, the weather was damp and chilly, with ambient temperatures hovering about 8°C and winds of approximately 30km/hour. Since Higgins' asphalt plant is located just 6km from the job site, there was no discernible drop in mix temperature as delivery trucks deposited the 160°C asphalt directly into the hopper of Higgins' Vögele paver.
According to Higgins' Patience and Bearsley, mixing, paving and compaction went smoothly. They indicated that the asphalt mix team observed an unusually clean operation and not much difference in handling the high-performance base course mix in comparison to asphalt employing standard SBS modified bitumen. However, they observed that as the mix cooled rather quickly due to raw weather hand work became more difficult. Compaction was accomplished by two
A few months later, an opportunity arose for Higgins Group to pave another, larger, area of pavement covering an area of approximately 2,700m² at Loading Zone 1. The same type of mix was placed here as at H8-K1. Bearsley said the proof of performance of the two re-paved sections would be simple: the absence of pavement wheel path deformations over time.
This article is reprinted with permission from Roads magazine.