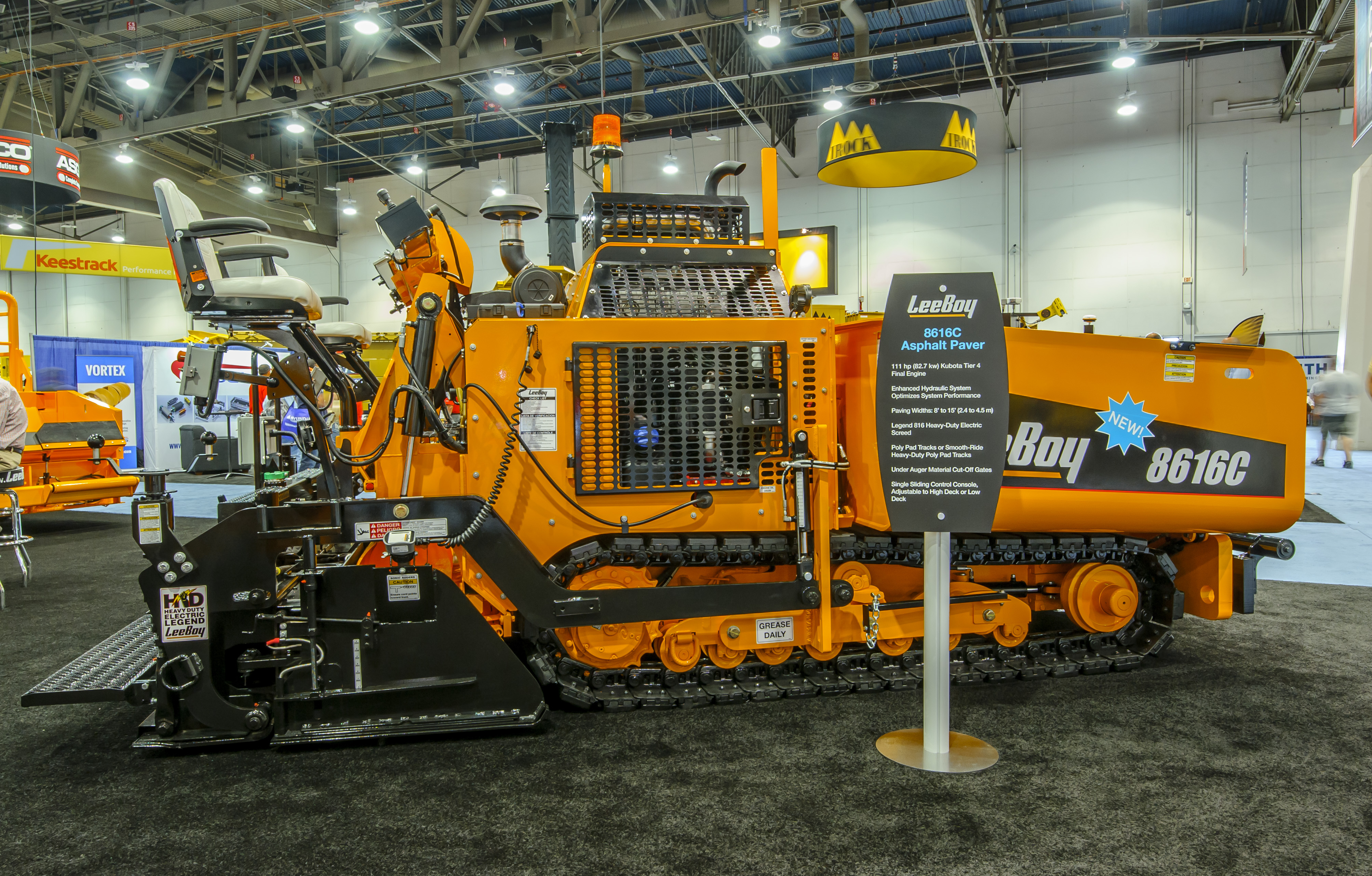
Developments are being seen in both European and North American asphalt paving machines. The latest equipment will help boost productivity and quality for asphalt paving work, while many of the new machines also offer increased versatility. Innovations in telematics meanwhile are helping to ensure that new generation asphalt pavers also offer easier maintenance, lower running costs and greater uptime.
Designed for European paving needs, the
Fast screed heating allows the machines to be ready for work in just 20 minutes, while an auto-fill feature that optimises material levels within the auger chamber as well as the central auger drive is designed to optimise material flow to the screed.
High paving performance is an important advantage and the machines have grade and slope controls integrated into the pavers. The 2D system is standard although there is an option to upgrade this to 3D capability.
An important feature is the integrated fumes control package, which removes fumes from the auger and directs these upwards, away from the operator and the paving crew. The system also reduces heat and makes the working area more comfortable, of particular importance for paving operations carried out in hot countries. Also integrated are the generators, which have enough additional power for lighting or other equipment.
Other improvements include Tier 4 Final engines that are powerful and responsive, with lower fuel consumption helped by an eco-mode system and improved hydraulics.
The FleetLink management package is also offered and purchasers of new machines receive a three-year subscription when they buy a new model. The Dynapac units can also communicate with the BPO optimisation package developed by
The same revised control layout is fitted to the 8520E paver, with power from a 107kW Kubota diesel. The machine has a wide conveyor system that allows a steady material flow in tight paving conditions and is equipped with a heavy-duty Legend 815 screed offering paving widths from 2.4-4.5m.
The 6150 meanwhile is an upgrade of a former Blaw Knox design, with a Legend screed, added cut-offs and the same new controls as on the other machines in the line-up, as well as power from a 55kW Kubota diesel and the firm’s narrow hopper conveyor.
Power comes from a 130kW diesel and this machine offers a turning radius of 762mm, allowing use in congested sites and space-restricted urban areas. It has a shipping width of 3.2m, making it easier to transport between sites.
As with other Roadtec pavers and MTVs, the new RP-170e has the firm’s FXS fume extraction system, featuring two fans. Fumes are then exhausted at the front of the engine cover while the air flow over the hopper also cools the platform. The firm says that the side-mounted layout of the cooling system with its large radiators meanwhile optimises engine cooling and is augmented by hydraulic fans that work on-demand.
The wheeled Super 1700-3i and Super 1703-3i can cover a wide range of road construction applications. When combined with the Vögele front-mounted extending screed and hydraulic bolt-on extensions they provide a maximum paving width of up to 5.95m. A 129kW
The material handling system of these pavers is designed for high output, with separate hydraulic drives on the conveyor and the auger, delivering paving rates of up to 700 tonnes/hour. The material handling system also helps to reduce segregation due to the novel design of receiving hopper, ascending conveyors and hydraulic augers.
The Super 2000-3i and Super 2003-3i come with the latest version of Vögele’s ErgoPlus 3 operating system. The highway class pavers can be combined with a VF600 screed with front-mounted extensions, or the VR600 and AB600 rear-mounted screeds with extensions. The AB600 is equipped with both a vibrating system and a tamper.
Both models are powered by six-cylinder Cummins diesels rated at 186kW, offering low fuel consumption and low-noise operation. Large coolers, revised air routing and variable-speed fan ensure temperatures stay low and allow the machines to operate in hot climates. The machines have 15tonne capacity hoppers and can handle up to 1,400 tonnes/hour of material.
Several screed options are available, featuring different equipment with compacting systems. The pavers can be combined with the VF 600, the VR 600 and the AB 600 extending screeds. Maximum paving width with bolt-on extensions is 7.3m for the wheeled machine and 8.6m for the tracked model when using the VR 600 screed. When using the AB 600 screed, maximum paving width is 8.5m for the tracked model and 7.5m for the wheeled model. The latter screed is said to deliver higher compaction and is suited for placing cold RAP for roadbase and polymer modified asphalt.