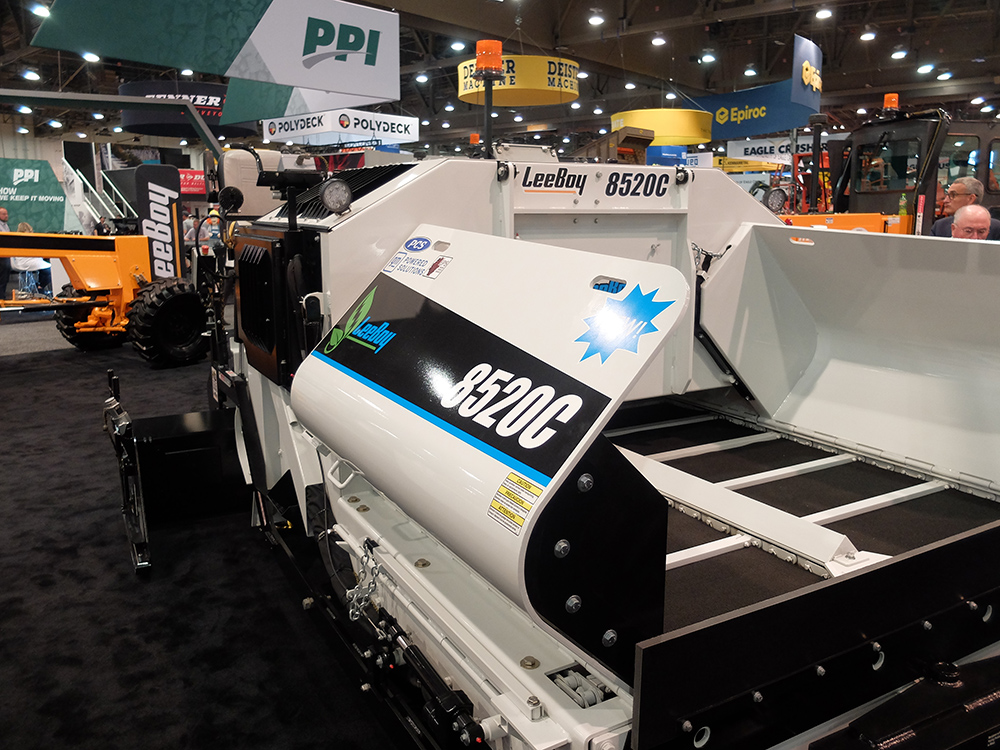
Several asphalt pavers are now under development that use electric drive instead of diesel power, with the potential to reduce localised emissions. A number of asphalt paver firms are working on prototypes at present, with trial sections of road having already been paved in some areas, such as in the Netherlands.
For use in urban areas, electric asphalt pavers offer the benefits of reduced noise and exhaust emissions. With regulations becoming particularly tough in Europe and California for example, the paver firms are looking ahead to offer solutions to contractors who will face restrictions on the use of diesel machines. In addition, these new machines would offer advantages for contracting firms carrying out underground car park works or for paving road tunnels.
For tunnelling projects, providing sufficient ventilation is expensive and using zero emissions equipment will reduce costs significantly. Contractors working on projects such as the upcoming Silvertown Tunnel project in London will be required to use zero emissions machines for construction of the cross passages as well as fitting out work, and electric asphalt pavers would fit requirements for the road surfacing portion of the project.
Although battery life means that electric pavers would work best for small road works and not suit long highway jobs requiring continuous operation, this could still be achieved in underground applications. With electric power available in tunnel projects for other equipment, an electric paver could operate from a cable. It would only need to run on the battery when the cable would be moved from one power point to the next as the machine advances. As with other electric construction machines, the cost of the battery will be a key factor in the purchase price of any production model but will be offset by much low running and maintenance costs over the paver’s working life.
One of the most recent electric pavers to be unveiled is the prototype model being worked on by LeeBoy in the US, shown at the CONEXPO-CON/AGG exhibition in March 2023. The electric 8520C is powered by a 150kW drive and features a 48kWh battery pack, while charging can be from 120V or 240V supplies, depending on what is available. The machine is equipped with the firm’s proven vibratory Legend HD screed and can pave widths of up to 4.6m, as with the conventional 8520 paver model. Many of the electric components are proven units from the automotive sector and supplied by GM, while PCS provided the powertrain integrator. The automotive components suit this duty and do not have to be specially ruggedised as the paver application features comparatively smooth and continuous operation with fewer shock loads than for other construction machine types.
LeeBoy stresses that the electric paver is a prototype that is still in development. Chris Brown is senior product manager at the firm and said, “We’re not ready to put out prices or sell it yet.”
He said that the machine offers the same paving performance as the conventional diesel model. The machine is now commencing full testing, which will also provide useful information on how long the battery will last in a working application.
However, Dynapac’s SD1800We city-class paver is now available commercially and was shown at the bauma construction machinery exhibition in October 2022. The first units are already being supplied to customers in Europe. The SD1800We features a tamper bar type screed and has the same paving specifications as the comparable SD1880W diesel machine, with both offering paving widths from 1.8-4.7m and laying up to 350tonnes/hour. The SD1800W e is built in collaboration with SUNCAR HK. SUNCAR, a leader in the electrification of construction machines based in Switzerland.
Dynapac says that its electric drive comes with an efficient three-phase permanent magnet synchronous motor (PMSM) that provides 55kW to the hydraulics for the screed and undercarriage. Depending on the type of job, application, and intensity of the work cycle, the SD1800We offers up to four hours of rugged performance with one charge. Charging is through a CE-compliant Type 2 plug for 400V, 6-32A, 1.4-22kW AC and through a wall box or a charging station. Depending on battery condition, charging takes around 3 hours to go from 5% to 80% @ 400V 22kW (AC) and 40 min to go from 5% to 80% @ 80kW (DC). Although charging while working is not possible, a user can pre-heat the screed with the charger (with Type 2 AC or CCS2 DC) while waiting for material to arrive.
Also shown at the bauma 2022 exhibition were the diminutive MINI 500e and 502e pavers from Vögele and these are also being made available in certain markets, rather than being prototypes under development. The tracked MINI 500e and wheeled MINI 502e pavers have battery electric drive, although more conventional diesel versions are also offered. The machines are aimed at use in small-scale construction projects that include constructing cycle and pedestrian paths, paving between railroad tracks as well as repair work in small inner-city sites. Compact pavers generally work for short periods only and suit the use of battery power, although charging times for the MINI 500e and MINI 502e are said to be short.
These machines have standard screed working widths of 0.8m and can be enlarged up to 1.35m hydraulically. The minimum paving width can be reduced down to 0.25m, while the width can be built up to a maximum of 1.8m using bolt-on extensions. The new Vögele MINI series has been developed in partnership with CM,, an Italian company that will also build the machines for Vögele.
Diesel power
More conventional diesel powered asphalt pavers are still being introduced to the market though. From Astec come improved versions of the proven RP-175 and RP-195 highway-class asphalt pavers for North American customers. Both machines now benefit from the installation of Cummins diesels that are Tier 4 Final/Stage V emissions compliant, with power ratings of 130kW for the B4.5 in the RP-175 and 172kW for the QSB6.7 in the RP-195. The engine covers have also been redesigned for both machines, providing better visibility for the operator and improving working safety.
Both machines have Carlson EZIV screeds offering paving widths from 2.43-4.72m for the RP-175 and 3.04-5.94m for the RP-195. Maximum paving width using bolt-on sections is 7.32m for the RP-175 and 9.14m for the RP-195.
The RP-175 weighs in at around 14.7tonnes while the larger RP-195 weighs 17.8tonnes. Both machines benefit from redesigned tracks with oscillating track frames for better traction and stability. Other improvements include better cooling systems and a relocated generator for the RP-195.
From Caterpillar comes a range of new asphalt paver variants for the 14-16tonne class. These include the AP400, AP455 Mobil-trac, AP455 Steel Track, AP500, AP555 Mobil-trac, and AP555 Steel Track asphalt pavers. The new models for the asphalt paving market from Cat also include the SE47 VT and SE50 VT tamper bar screeds.
The SE47 VT standard paving range is 2.4-4.7m with a maximum width of 6m using extensions, while the SE50 VT standard paving range is 2.55-5m with a maximum width of 7.64m. The SE47 VT screed and SE50 VT are tamper bar models for the international market. Meanwhile, the SE47 V and SE50 V screeds are vibration only units aimed at customers in North America and Latin America.
The machines also benefit from the firm’s PaveStart system, which retains the screed settings used for a job and allows the machine to be restarted with the same settings after a break in working. An improved feature is an integrated generator delivering 25kW and which powers the 240V AC heating system. The improved screed heating system offers a fast heating up time, having the machine ready for use in just 20-25 minutes according to the firm.
Compact and manoeuvrable, the machines are said to be easy to transport. With lengths of less than 5.6m and widths of 2.55m, these 14-16tonne class machines can be transported on a variety of trailer types without special permits.
The front-loading angle of 17° and high bumper clearance simplify loading without the need for additional blocking materials. These models combine a low truck entry height with smaller 355mm diameter augers that efficiently move material through the auger chamber at both narrow and wide paving widths.
The rubber tracks are offered with a four-year warranty and have a four-bogie system with self-tensioning accumulators and centre guide blocks. This design helps prevent slippage and reduces wear, while the oscillating bogie wheels help deliver smooth transitions when exiting the cut over transverse joints of mill and fill applications.
The AP455 and AP555 steel track models provide many of the same features with lower travel speeds and have an auto-tensioning system to ensure tractive performance while minimising wear.
For contractors that prefer a simple wheel undercarriage design, the AP400 can be equipped with a front-wheel assist option, while the AP500 can be equipped with front-wheel assist or the all-wheel drive option for increased performance on soft base materials or when pushing heavy loads.
The AP400 and AP455 pavers are equipped with a Cat C3.6 engine, while the AP500 and AP555 use the Cat C4.4 engine. The engines are available in configurations that meet Tier 4 Final, EU Stage V, and ECE R96 Stage IIIA emission standards, equivalent to Tier 3 and Stage IIIA.
Designed for the North American market, the new D17 C commercial paver from Dynapac suits use in medium to large parking lots and county roads, says the company. It comes with a standard paving width of 2.5-4.7m, while optional bolt-on extensions allow the unit to pave up to nearly 5.5m in width.
Key improvements over the earlier FC1700 C include a fail-safe heat management system for increased efficiency and reliability. The newly designed proportional auger conveyor system controls the material flow to the screed. Dynapac’s D17 C is paired with the VF0816 front extension screed, which weighs over 2tonnes and is the heaviest in its class, boosting paving quality. Screed heating is powered by a newly designed, three-phase 16kW generator that increases efficiency and reduces heat-up time. And the heating system includes multi-zone monitoring, allowing even temperatures across the width of the screed.
Bolted-on conveyor floor plates, segmented auger flights and screed plates mean that the wear parts can be replaced and rebuilt several times. The quad auger system includes screed-mounted augers on both main and extension sections. This allows a smooth material feed whatever the pavement width. The independent conveyor system, along with reversible conveyor, allows for ease of operation while paving and eliminates spillage when transporting the paver. The proportional feed system offers precise control of the material in front the screed. Operators can also personalise material pile-height settings according to job requirements.
Aimed at utilities works, Dynapac’s F1250CS compact paver now benefits from the option of the RC360 remote control unit, which is said to offer additional versatility. The compact Dynapac F1250CS suits use where paving is required with widths of 0.5-3.5m. Using the remote unit, an operator can control the paver from a point that offers the lowest asphalt fumes while providing maximum visibility. Should the operator be more than 10m from the paver, the machine stops automatically for safety. The paver also stops automatically when the remote is tilted higher than a 45° angle. The remote comes with a case and charging devices with a mechanical connector for external supply.
Meanwhile, the F1250CS’s V2400 screed is available with gas and electric heating, offering the same quality and performance as its larger stablemates and has an extension box allowing greater widths. The Dynapac F1250CS can pave below zero for refurbishment work, as the paver can drive out of the milling cut and allow the screed to pave a smooth finish.
Multiple adjustments such as for angle of attack and the deep bottom plates allow high pre-compaction and a smooth surface, even with thick layers. The quick coupling eases setup and operation.
The F1250C comes with a 54kW Deutz engine in either Tier 3/Stage III or Tier 4/Stage V versions to local emissions requirements.
LeeBoy is offering a new addition to its conventional asphalt paver range also. The new 8508 paver is a compact, low maintenance machine with a narrow conveyor aimed at repair works in the North American market. It shares many features with the existing 8616, but is around 300mm shorter to allow it to operate in tighter sites. Power comes from a Tier 4 Final compliant Kubota diesel delivering 125kW, while the machine features oscillating bogies for the undercarriage, allowing smoother operation. The machine can be fitted with the HD or HD Pro screeds offering paving widths of 4.6m or 4.72m.
And German firm Vögele says that its SUPER 1703-3i Universal Class paver is being offered with the VF 500 screed to meet the needs of the North American market. The VF 500 front-mounted screed offers paving widths from 2.44m up to 4.72m using hydraulic extension and a maximum 5.94m using bolt-on extensions.
The wheeled paver benefits from compact dimensions and Pivot Steer braking, allowing good manoeuvrability. High paving speeds can be achieved, along with laydown rates of up to 695tonnes/hour. The firm says that its Universal Class paver suits duties in large commercial applications.
The paver and screed are equipped with the user-friendly ErgoPlus 3 operating system. It makes controlling the machine, including the Niveltronic Plus system for automated grade and slope control, easy and convenient. The Vögele EcoPlus low-emissions package cuts fuel consumption by up to 25%, depending on the application and workload, and reduces noise. When equipped with Vögele RoadScan, the non-contacting temperature measurement system, checking and documenting the paving temperature is easy. Temperature monitoring across the entire surface makes quality measurable.
The firm is also offering two improved asphalt pavers aimed at the highway class for European customers. The new SUPER 1900-5(i) and SUPER 2100-5(i) Highway Class pavers are the first models in the firm’s new Dash 5 generation and are equipped with the latest-generation AB 500 and AB 600 Extending Screeds. The firm says that these new pavers benefit from the latest technology so as to meet the increasing need for digitalisation in construction.
User requirements have been a key focus during the development of these machines according to the firm. For the paving crew, this allows simple machine handling, maximum operating convenience and safety on the job site.
Reduced setup times, improved logistics and greater machine availability are said to deliver and ensure fuel economy and reduce material wastage, helping address increasing fuel and materials costs. New automation and control technology provides operator assistance and has been optimised to prevent errors and to increase efficiency and paving quality according to Vögele.
Reducing the noise emissions and fuel consumption of Dash 5 pavers while maintaining the same performance helps meet sustainability targets for contractors, while also lowering fuel costs and CO2 emissions.
And Chinese firm XCMG is introducing its RP705 asphalt paver into the European and North American markets. The firm says that the machine offers reliability and productivity with a throughput of 600tonnes/hour, suiting it for urban road repairs. The machine is said to be easy to operate and has its screed options, tracks and its feeder system modified to suit the needs of customers in developed markets.