Several of the key asphalt paver manufacturers are rolling out new models that deliver increased performance and capabilities - Mike Woof writes
The pace of development in the asphalt paving equipment sector is high, with a wide array of new machines coming to market. All of the major manufacturers are introducing new models for 2017, while there are also key business developments that are ongoing.
One of the most notable business moves in the road machinery sector is the agreement between the Fayat G
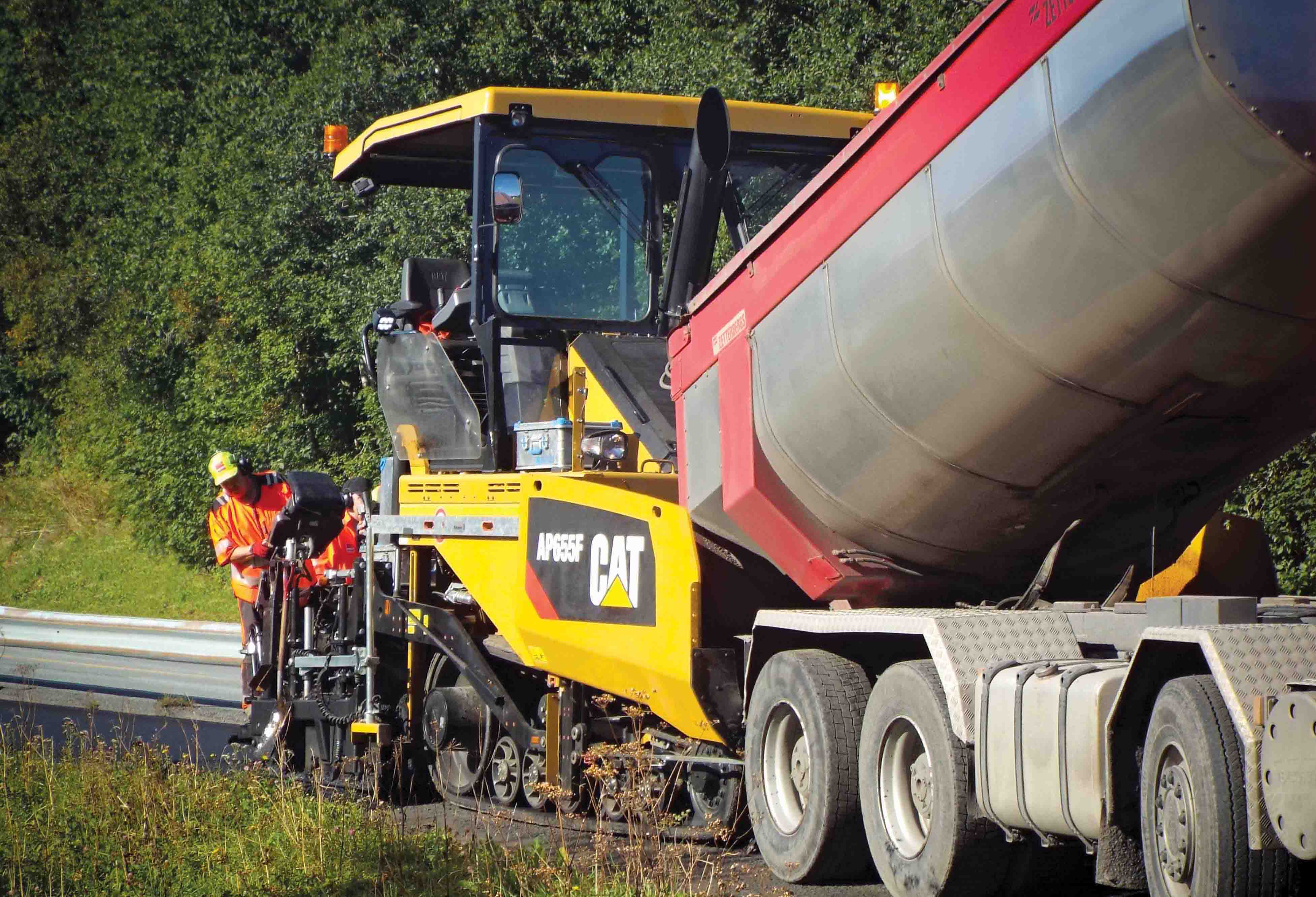
Caterpillar has versions of its F Series pavers suitable for European and US markets
Several of the key asphalt paver manufacturers are rolling out new models that deliver increased performance and capabilities - Mike Woof writes
The pace of development in the asphalt paving equipment sector is high, with a wide array of new machines coming to market. All of the major manufacturers are introducing new models for 2017, while there are also key business developments that are ongoing.
One of the most notable business moves in the road machinery sector is the agreement between the2779 Fayat Group in France and 161 Atlas Copco in Sweden. This will see the 206 Dynapac road machinery brand becoming part of the Fayat Group, which already owns the 172 BOMAG range of road machines. The deal is still subject to approval by the relevant authorities but will see the BOMAG and Dynapac brands, equipment ranges and distribution networks being retained. Further ahead there may be an integration of products but this has yet to be determined.
New models are coming for both the BOMAG and Dynapac ranges in the next few months, which will be available through the separate distribution networks. BOMAG’s latest addition is coming in the shape of a new compact asphalt paver, the BF232C.
This tracked machine will offer a maximum throughput of 200tonnes/hour. The paver will fit into the range below the mid-sized BF300, itself smaller than the mid-sized BF600 and BF700 and highway class BF800 and BF900. It will offer a maximum paving width of 4m and will benefit from the Magmalife screed heating technology seen on other units in the range, along with the firm’s proven compaction and quick coupling systems. The heating system allows the screed to reach an operating temperature of 120°C within 20 minutes. The cast aluminium heating elements are said to ensure efficient heat distribution and be well protected against damage, offering a long working life of 5,000 hours or more.
178 Caterpillar has been developing its tracked and wheeled paver range, with the introduction of its F-Series models, offering increased performance and versatility. The firm offers F Series pavers for both US and European market needs, with a range of screed types available that are suited to local requirements.
The Tier 4 Final engines are said to be powerful and responsive, as well as offering low fuel consumption, further reduced by efficient hydraulics and an eco-mode system, while engine maintenance is said to be easy.
Grade and slope controls have been integrated into the pavers, with a 2D system as standard but the option to upgrade to a 3D system if required. The touch-screen grade control units are integrated into the machines, so these do not have to be removed at the end of a shift to prevent theft.
According to Caterpillar, its F Series machines offer fast screed heating, with the machines being ready to work in 20 minutes (and even 15 minutes in some instances). The machines have an auto-fill feature that maintains material levels within the auger chamber, which is said to ensure an optimum flow of material to the screed. The central auger drive meanwhile is also designed to optimise material flow into the screed An important feature is the integrated fumes control package, which removes fumes from the auger area and vents these upwards, away from the operator and paving crew. The fumes control system also moves the heat away from the operator and paving crew and makes the working area more comfortable, which is of particular importance when the machines are operating in hot climates.
The integrated generators are important features of the F Series models, with sufficient power to run lighting and other systems, allowing operation at night. This is particularly important for the highway class pavers, which may be used for night possession work on highways or aircraft runways for example.
A notable feature of the tracked pavers from the firm is the undercarriage design. While Caterpillar was not the first firm to fit its pavers with rubber tracks, it developed the concept and made it more reliable. This in turn has led to a wide acceptance of the system, which offers the mobility of a wheeled paver combined with the stability of a tracked machine.
Dynapac has invested heavily in developing the range. Product manager Catharina Krindberg said, “The biggest thing was the introduction of the City pavers and they are being distributed worldwide now. The previous design had some years on the counter.”
She said that considerable development has gone into improving and modernising these models and as an example, the pavers now have similar operator panels to the compactors. She said, “We have upgraded the platform and added a USB capability. The new software allows us to display information in a more modern way.”
The firm is seeing its new machines being used too, with one paver having been used at the Hong Kong airport, featuring a 6m screed width extended to 9m using four 0.75m extensions, two on either side.
The firm has developed new technology and of the key developments has been the truck assist system, which is said to boost efficiency, as this measures the distance between the truck and the hopper. “It’s mounted on the hopper as that’s where the driver wants to look. We get a lot of requests to retrofit the system.”
And while the system is integrated onto the latest generation machines, it can also be fitted to older machines with a manual setting. The FleetLink management system is also fitted, with customers for new machines getting a three-year subscription when they buy a new unit. The Dynapac units can also communicate with the BPO optimisation package developed by8820 Volz Consulting. Krindberg said “It’s an open system you can use with any technology, whether it’s from Volz or 2122 Trimble for example, because these all use common standards.”
In addition the firm has also updated its material feeder, which is based on a paver platform and now offers a larger swing angle. The material feeder has also been an example of an early partnership between BOMAG and Dynapac that predates Fayat’s move to buy the business. And Dynapac has been supplying a BOMAG badged version of its material feeder to BOMAG for some time.
LeeBoy is introducing a Tier 4 Final version of its 8616 paver, which shares a number of features with the 8500 series. The 8616C offers screed widths from 2.44-4.6m and has improved performance over the 8616B being replaced, with better visibility of the screed. Some features such as choice of a high deck or low deck variants, have been retained. The 8500 models such as the 8510D are all now offered in Tier 4 Final variants for use in North America as well as Australia. These pavers are also offered in Tier 3 variants however, for sale into lesser regulated markets such as Latin America. The firm is also offering its PF-1510B, an updated version of an earlier model.
1252 Roadtec’s latest RP-170e paver is a rubber tyred model aimed at the 2.5m highway class and features dual operator stations that swing out hydraulically over the side for better visibility. The machine features a 1.905m wheelbase, which the firm claims is designed to offer manoeuvrability without sacrificing traction. The hopper is 3.175m wide and offers a capacity of 10.4tonnes and the machine can be fitted with various electrically-heated, vibratory screed options to match customer needs. Roadtec offers the EZ-IV and EZ-V front mount screeds from sister firm Carlson. The machine can also be fitted with Roadtec’s S-8 standard wedge-lock screed or the Eagle 8 rear extendable screed.
This is the smallest machine in the Roadtec paver line and has been designed to offer better manoeuvrability, ride quality and traction. Two large rear drive tyres are steered by two tandem bogie assemblies. Dry disc brakes, hydraulic braking, and a parking brake are designed to provide precise control.
It has a turning radius of 762mm, is powered by a 130kW diesel and is aimed at use in congested sites and space-restricted urban areas with its manoeuvrability allowing it to operate in tight spots around barriers and drains. It has a shipping width of 3.2m and is designed for quick and easy transport between job locations.
The RP-170e is equipped with the firm’s novel anti-segregation design, which now includes larger 406mm-diameter augers. The auger assembly can be raised, lowered, or tilted, further helping to minimise segregation in certain mixes, as well as aiding loading and unloading and laying HMA Superpave mixtures. Standard sonic feed sensors control each side of the feed system. The machine also offers a clear field of view for the operator, with ergonomic controls.
As with all Roadtec pavers and MTVs, the Roadtec RP-170e paver features the FXS fume extraction system for the operator area. The FXS system uses two fans to draw fumes and exhaust through vents at the front of the engine hood. This large quantity of air moving over the hopper is designed to keep the platform fume-free and cooler. The cooling package on the Roadtec RP-170e paver is side-mounted to receive the cleanest and coolest air, with cooling further optimised by hydraulic fans and large radiators.
1194 Vögele is widening its offering for the asphalt paving sector, with several new units. The firm says that the tracked SUPER 1700-3i and wheeled SUPER 1703-3i pavers are highly versatile machines. These can be used for a wide range of applications and are said to be highly manoeuvrable as well as being easy to transport.
Pavers in the 2.44m class are road construction machines that are designed to achieve high performance in confined conditions and on highway job sites. The machines feature a material handling system designed to reduce thermal and mechanical segregation due to the novel design of receiving hopper, ascending conveyors and hydraulic augers.
The new pavers offer hydraulic extension from 2.44-4.75m and can be fitted with extensions to allow a maximum paving width of 5.95m. The machines have 13tonne capacity hoppers, with high-powered, separate hydraulic drives on the conveyor and auger to deliver an optimum head of mix in front of the screed and offer a maximum throughput of 700tonnes/hour. Power comes from a four-cylinder196 Cummins diesel rated at 129kW, while high traction is claimed and customers for the SUPER 1703-3i wheeled paver have a choice of 6x4 or 6x6 drive.
The SUPER 2000-3i and SUPER 2003- 3i pavers are designed for use on highway projects. The tracked SUPER 2000-3i and the wheeled SUPER 2003-3i pavers are designed for use in highway construction and largescale applications.
Both pavers come with the latest version of the VÖGELE operating system, the ErgoPlus 3. Both models are powered by six-cylinder Cummins diesels rated at 186kW, offering low fuel consumption and low-noise operation. Large coolers, revised air routing and a variable-speed fan keep temperatures within the optimum range for the machines in hot climates.
The SUPER 2000-3i and the SUPER 2003-3i feature materials hoppers holding 15 tonnes and allow laydown rates of up to 1,400 tonnes/hour.
Several screed options are available, featuring different equipment with compacting systems. The pavers can be combined with the VF 600, the VR 600 and the AB 600 extending screeds. Maximum paving width with bolt-on extensions is 7.3m for the wheeled machine and 8.6m for the tracked model when using the VR 600 screed.
When using the AB 600 screed, maximum paving width is 8.5m for the tracked model and 7.5m for the wheeled model. The latter screed is said to deliver higher compaction and is suited for placing cold RAP for roadbase and polymer modified asphalt.
The pace of development in the asphalt paving equipment sector is high, with a wide array of new machines coming to market. All of the major manufacturers are introducing new models for 2017, while there are also key business developments that are ongoing.
One of the most notable business moves in the road machinery sector is the agreement between the
New models are coming for both the BOMAG and Dynapac ranges in the next few months, which will be available through the separate distribution networks. BOMAG’s latest addition is coming in the shape of a new compact asphalt paver, the BF232C.
This tracked machine will offer a maximum throughput of 200tonnes/hour. The paver will fit into the range below the mid-sized BF300, itself smaller than the mid-sized BF600 and BF700 and highway class BF800 and BF900. It will offer a maximum paving width of 4m and will benefit from the Magmalife screed heating technology seen on other units in the range, along with the firm’s proven compaction and quick coupling systems. The heating system allows the screed to reach an operating temperature of 120°C within 20 minutes. The cast aluminium heating elements are said to ensure efficient heat distribution and be well protected against damage, offering a long working life of 5,000 hours or more.
The Tier 4 Final engines are said to be powerful and responsive, as well as offering low fuel consumption, further reduced by efficient hydraulics and an eco-mode system, while engine maintenance is said to be easy.
Grade and slope controls have been integrated into the pavers, with a 2D system as standard but the option to upgrade to a 3D system if required. The touch-screen grade control units are integrated into the machines, so these do not have to be removed at the end of a shift to prevent theft.
According to Caterpillar, its F Series machines offer fast screed heating, with the machines being ready to work in 20 minutes (and even 15 minutes in some instances). The machines have an auto-fill feature that maintains material levels within the auger chamber, which is said to ensure an optimum flow of material to the screed. The central auger drive meanwhile is also designed to optimise material flow into the screed An important feature is the integrated fumes control package, which removes fumes from the auger area and vents these upwards, away from the operator and paving crew. The fumes control system also moves the heat away from the operator and paving crew and makes the working area more comfortable, which is of particular importance when the machines are operating in hot climates.
The integrated generators are important features of the F Series models, with sufficient power to run lighting and other systems, allowing operation at night. This is particularly important for the highway class pavers, which may be used for night possession work on highways or aircraft runways for example.
A notable feature of the tracked pavers from the firm is the undercarriage design. While Caterpillar was not the first firm to fit its pavers with rubber tracks, it developed the concept and made it more reliable. This in turn has led to a wide acceptance of the system, which offers the mobility of a wheeled paver combined with the stability of a tracked machine.
Dynapac has invested heavily in developing the range. Product manager Catharina Krindberg said, “The biggest thing was the introduction of the City pavers and they are being distributed worldwide now. The previous design had some years on the counter.”
She said that considerable development has gone into improving and modernising these models and as an example, the pavers now have similar operator panels to the compactors. She said, “We have upgraded the platform and added a USB capability. The new software allows us to display information in a more modern way.”
The firm is seeing its new machines being used too, with one paver having been used at the Hong Kong airport, featuring a 6m screed width extended to 9m using four 0.75m extensions, two on either side.
The firm has developed new technology and of the key developments has been the truck assist system, which is said to boost efficiency, as this measures the distance between the truck and the hopper. “It’s mounted on the hopper as that’s where the driver wants to look. We get a lot of requests to retrofit the system.”
And while the system is integrated onto the latest generation machines, it can also be fitted to older machines with a manual setting. The FleetLink management system is also fitted, with customers for new machines getting a three-year subscription when they buy a new unit. The Dynapac units can also communicate with the BPO optimisation package developed by
In addition the firm has also updated its material feeder, which is based on a paver platform and now offers a larger swing angle. The material feeder has also been an example of an early partnership between BOMAG and Dynapac that predates Fayat’s move to buy the business. And Dynapac has been supplying a BOMAG badged version of its material feeder to BOMAG for some time.
LeeBoy is introducing a Tier 4 Final version of its 8616 paver, which shares a number of features with the 8500 series. The 8616C offers screed widths from 2.44-4.6m and has improved performance over the 8616B being replaced, with better visibility of the screed. Some features such as choice of a high deck or low deck variants, have been retained. The 8500 models such as the 8510D are all now offered in Tier 4 Final variants for use in North America as well as Australia. These pavers are also offered in Tier 3 variants however, for sale into lesser regulated markets such as Latin America. The firm is also offering its PF-1510B, an updated version of an earlier model.
This is the smallest machine in the Roadtec paver line and has been designed to offer better manoeuvrability, ride quality and traction. Two large rear drive tyres are steered by two tandem bogie assemblies. Dry disc brakes, hydraulic braking, and a parking brake are designed to provide precise control.
It has a turning radius of 762mm, is powered by a 130kW diesel and is aimed at use in congested sites and space-restricted urban areas with its manoeuvrability allowing it to operate in tight spots around barriers and drains. It has a shipping width of 3.2m and is designed for quick and easy transport between job locations.
The RP-170e is equipped with the firm’s novel anti-segregation design, which now includes larger 406mm-diameter augers. The auger assembly can be raised, lowered, or tilted, further helping to minimise segregation in certain mixes, as well as aiding loading and unloading and laying HMA Superpave mixtures. Standard sonic feed sensors control each side of the feed system. The machine also offers a clear field of view for the operator, with ergonomic controls.
As with all Roadtec pavers and MTVs, the Roadtec RP-170e paver features the FXS fume extraction system for the operator area. The FXS system uses two fans to draw fumes and exhaust through vents at the front of the engine hood. This large quantity of air moving over the hopper is designed to keep the platform fume-free and cooler. The cooling package on the Roadtec RP-170e paver is side-mounted to receive the cleanest and coolest air, with cooling further optimised by hydraulic fans and large radiators.
Pavers in the 2.44m class are road construction machines that are designed to achieve high performance in confined conditions and on highway job sites. The machines feature a material handling system designed to reduce thermal and mechanical segregation due to the novel design of receiving hopper, ascending conveyors and hydraulic augers.
The new pavers offer hydraulic extension from 2.44-4.75m and can be fitted with extensions to allow a maximum paving width of 5.95m. The machines have 13tonne capacity hoppers, with high-powered, separate hydraulic drives on the conveyor and auger to deliver an optimum head of mix in front of the screed and offer a maximum throughput of 700tonnes/hour. Power comes from a four-cylinder
The SUPER 2000-3i and SUPER 2003- 3i pavers are designed for use on highway projects. The tracked SUPER 2000-3i and the wheeled SUPER 2003-3i pavers are designed for use in highway construction and largescale applications.
Both pavers come with the latest version of the VÖGELE operating system, the ErgoPlus 3. Both models are powered by six-cylinder Cummins diesels rated at 186kW, offering low fuel consumption and low-noise operation. Large coolers, revised air routing and a variable-speed fan keep temperatures within the optimum range for the machines in hot climates.
The SUPER 2000-3i and the SUPER 2003-3i feature materials hoppers holding 15 tonnes and allow laydown rates of up to 1,400 tonnes/hour.
Several screed options are available, featuring different equipment with compacting systems. The pavers can be combined with the VF 600, the VR 600 and the AB 600 extending screeds. Maximum paving width with bolt-on extensions is 7.3m for the wheeled machine and 8.6m for the tracked model when using the VR 600 screed.
When using the AB 600 screed, maximum paving width is 8.5m for the tracked model and 7.5m for the wheeled model. The latter screed is said to deliver higher compaction and is suited for placing cold RAP for roadbase and polymer modified asphalt.