India’s new Formula 1 motor racing circuit, with its tight construction tolerances, demands considerable driving skill. More than 500 million people worldwide watched the first Formula 1 motor race in India's history. The drivers were thrilled by the new asphalt circuit with its numerous bends and the peripheral area around the new race track at Greater Noida near the capital New Delhi, which were built by machinery from German company Vögele (a member of the Wirtgen Group). Working with four Super 1800-
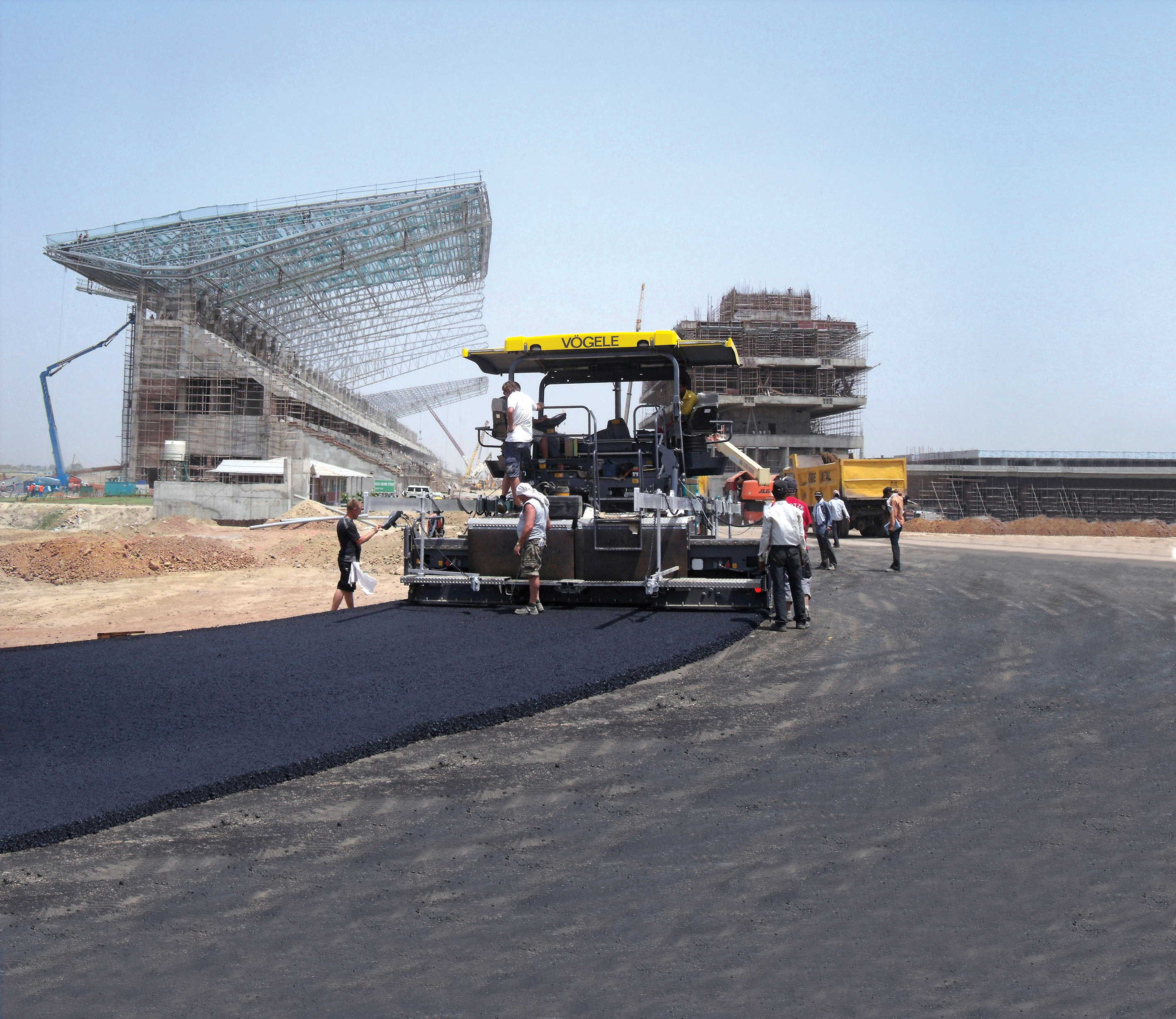
Working with four Super 1800-2 pavers, the Vögele team helped construct the Buddh International Circuit.
India’s new Formula 1 motor racing circuit, with its tight construction tolerances, demands considerable driving skill.
More than 500 million people worldwide watched the first Formula 1 motor race in India's history.
The drivers were thrilled by the new asphalt circuit with its numerous bends and the peripheral area around the new race track at Greater Noida near the capital New Delhi, which were built by machinery from German company1194 Vögele (a member of the 364 Wirtgen Group).
Working with four Super 1800-2 pavers, the Vögele team helped construct the Buddh International Circuit.
“To build a perfectly level asphalt pavement for the drivers as they battle for milliseconds, contractor Oriental Structure Engineers from New Delhi used the Vögele pavers for the crushed-stone base followed by three layers of asphaltic concrete. A Big MultiPlex Ski was used to ensure perfect grade and slope control,” says Vögele.
A demanding 5.1km circuit with 16 bends, a road varying between 18m-25m in width, super-elevations up to 12% and gradients up to 10%, distinguishes this newcomer to the Formula 1 racing calendar, and demands considerable driving skill, offering optimum conditions for breathtaking overtaking manoeuvres.
Oriental’s experts opted for technology from Vögele in order to deliver top-quality paving results despite these demanding requirements. Aided by the powerful pavers, they built a two-layer crushed-stone base and paved roughly 325,000tonnes of asphalt for the circuit and its peripheral areas in the course of the project.
“The requirements made on the asphalt layers were extremely high in terms of both material quality and paving accuracy. The permissible tolerances for binder content, grain mix and also evenness were far lower than those of German motorways,” says Vögele.
Particularly stringent demands were made on the surface course. The planning engineers had reduced by half the permitted deviation of the granular material from the ideal aggregate grading curve, compared with the tolerances allowed under German regulations. Aggregate with high resistance to polishing was used for the surface course.
“This mix guarantees a road surface with uniform texture depth and perfect tyre grip. All aggregate for the asphalt package was hauled to the mixing plants from specially selected quarries, some of which were several hundred kilometres away. The binder, too, was modified in line with the climatic conditions prevailing in northern India to ensure an outstanding mechanical and temperature stability at all times.
“Overall, the planning engineers' various measures allowed the achievement of an extremely uniform pavement structure whose properties will endure for many years, despite changing climatic conditions.”
Paving extended over a period of roughly 14 months during which the work had to be interrupted temporarily, mainly on account of the monsoon rain, but also due to technical requirements associated with the project as a whole.
“In retrospect, however, the figures are still impressive: all-in-all, the Vögele pavers built both the road-base and the two or three-layer asphalt pavement according to the highest technical standards over a total area of 750,000m².”
Quality was the most important aspect, particularly when it came to paving the asphalt for the race track. For this reason, numerous sample mixes were prepared and laid on test areas before the paving work began.
The formula, mixing plant parameters and materials were perfectly matched by the team of German and Indian operators and laboratory technicians. Access roads and tangents covering several thousand square metres were built in this way.
“Such sample mixes are essential for optimizing the quality of the asphalt surface course. All the various constituent parts of the asphalt, the mixing plant parameters and precision adjustment of the pavers can only be perfectly matched with one another on the basis of such tests,” explains asphalt specialist Dr Rainer Hart. He developed the concept for the race track asphalt and supervised the asphalt work from selection of the aggregate in the quarry to paving and compaction.
On a racing circuit, the base and binder courses are very much thinner than on normal roads. This is due to the lower pressure acting on the asphalt package. Non-skid properties and evenness are far more important here, and this is why the paving teams paid more and more attention to the pavement’s evenness as they worked their way up to the top of the asphalt package.
A Big MultiPlex Ski was fitted on each side of the Super 1800-2 pavers when placing all three layers, a move that paid off, particularly when a maximum permissible tolerance of 3mm per 4m has been specified. “The evenness achieved by Vögele is outstanding, thanks to the Big MultiPlex Ski. To the greatest possible extent, the surface unevenness was less than 1mm over a distance of 4m,” says Dr Hart, who has supervised the paving work on Formula 1 circuits in the past.
The Big MultiPlex Ski uses the proven Vögele technology of the sonic grade sensor. Three multi-cell sonic sensors are mounted on a beam with a maximum length of 13m. They simultaneously scan a reference at several widely spaced points. NIVELTRONIC Plus, the Vögele system for automated grade and slope control, calculates a virtual reference from these picked-up values. The Big MultiPlex Ski is capable of detecting and levelling out long irregularities in the surface, such as undulations, over a maximum distance of 13m.
It consequently operates with greater precision than a single cell grade sensor, and is controlled as usual via the screed operator’s console. Variability is also assured: the individual sensors of the Big MultiPlex Ski can be moved along the beam to optimally adapt to any job site.
“Even at temperatures of more than 40°C the pavers continued to operate faultlessly,” reports service technician Ralf Peter.
“With their profound know-how and skilled eye, the service technicians from Wirtgen India and Vögele gave us optimum support when fine-tuning the pavers,” says Pankaj Gautam, Oriental’s overall project manager.
And the result of the first race on 30 October, 2011 saw the German Formula 1 world champion Sebastian Vettel win, setting the first course record with a lap time of 1.27 minutes.
More than 500 million people worldwide watched the first Formula 1 motor race in India's history.
The drivers were thrilled by the new asphalt circuit with its numerous bends and the peripheral area around the new race track at Greater Noida near the capital New Delhi, which were built by machinery from German company
Working with four Super 1800-2 pavers, the Vögele team helped construct the Buddh International Circuit.
“To build a perfectly level asphalt pavement for the drivers as they battle for milliseconds, contractor Oriental Structure Engineers from New Delhi used the Vögele pavers for the crushed-stone base followed by three layers of asphaltic concrete. A Big MultiPlex Ski was used to ensure perfect grade and slope control,” says Vögele.
A demanding 5.1km circuit with 16 bends, a road varying between 18m-25m in width, super-elevations up to 12% and gradients up to 10%, distinguishes this newcomer to the Formula 1 racing calendar, and demands considerable driving skill, offering optimum conditions for breathtaking overtaking manoeuvres.
Oriental’s experts opted for technology from Vögele in order to deliver top-quality paving results despite these demanding requirements. Aided by the powerful pavers, they built a two-layer crushed-stone base and paved roughly 325,000tonnes of asphalt for the circuit and its peripheral areas in the course of the project.
“The requirements made on the asphalt layers were extremely high in terms of both material quality and paving accuracy. The permissible tolerances for binder content, grain mix and also evenness were far lower than those of German motorways,” says Vögele.
Particularly stringent demands were made on the surface course. The planning engineers had reduced by half the permitted deviation of the granular material from the ideal aggregate grading curve, compared with the tolerances allowed under German regulations. Aggregate with high resistance to polishing was used for the surface course.
“This mix guarantees a road surface with uniform texture depth and perfect tyre grip. All aggregate for the asphalt package was hauled to the mixing plants from specially selected quarries, some of which were several hundred kilometres away. The binder, too, was modified in line with the climatic conditions prevailing in northern India to ensure an outstanding mechanical and temperature stability at all times.
“Overall, the planning engineers' various measures allowed the achievement of an extremely uniform pavement structure whose properties will endure for many years, despite changing climatic conditions.”
Paving extended over a period of roughly 14 months during which the work had to be interrupted temporarily, mainly on account of the monsoon rain, but also due to technical requirements associated with the project as a whole.
“In retrospect, however, the figures are still impressive: all-in-all, the Vögele pavers built both the road-base and the two or three-layer asphalt pavement according to the highest technical standards over a total area of 750,000m².”
Quality was the most important aspect, particularly when it came to paving the asphalt for the race track. For this reason, numerous sample mixes were prepared and laid on test areas before the paving work began.
The formula, mixing plant parameters and materials were perfectly matched by the team of German and Indian operators and laboratory technicians. Access roads and tangents covering several thousand square metres were built in this way.
“Such sample mixes are essential for optimizing the quality of the asphalt surface course. All the various constituent parts of the asphalt, the mixing plant parameters and precision adjustment of the pavers can only be perfectly matched with one another on the basis of such tests,” explains asphalt specialist Dr Rainer Hart. He developed the concept for the race track asphalt and supervised the asphalt work from selection of the aggregate in the quarry to paving and compaction.
On a racing circuit, the base and binder courses are very much thinner than on normal roads. This is due to the lower pressure acting on the asphalt package. Non-skid properties and evenness are far more important here, and this is why the paving teams paid more and more attention to the pavement’s evenness as they worked their way up to the top of the asphalt package.
A Big MultiPlex Ski was fitted on each side of the Super 1800-2 pavers when placing all three layers, a move that paid off, particularly when a maximum permissible tolerance of 3mm per 4m has been specified. “The evenness achieved by Vögele is outstanding, thanks to the Big MultiPlex Ski. To the greatest possible extent, the surface unevenness was less than 1mm over a distance of 4m,” says Dr Hart, who has supervised the paving work on Formula 1 circuits in the past.
The Big MultiPlex Ski uses the proven Vögele technology of the sonic grade sensor. Three multi-cell sonic sensors are mounted on a beam with a maximum length of 13m. They simultaneously scan a reference at several widely spaced points. NIVELTRONIC Plus, the Vögele system for automated grade and slope control, calculates a virtual reference from these picked-up values. The Big MultiPlex Ski is capable of detecting and levelling out long irregularities in the surface, such as undulations, over a maximum distance of 13m.
It consequently operates with greater precision than a single cell grade sensor, and is controlled as usual via the screed operator’s console. Variability is also assured: the individual sensors of the Big MultiPlex Ski can be moved along the beam to optimally adapt to any job site.
“Even at temperatures of more than 40°C the pavers continued to operate faultlessly,” reports service technician Ralf Peter.
“With their profound know-how and skilled eye, the service technicians from Wirtgen India and Vögele gave us optimum support when fine-tuning the pavers,” says Pankaj Gautam, Oriental’s overall project manager.
And the result of the first race on 30 October, 2011 saw the German Formula 1 world champion Sebastian Vettel win, setting the first course record with a lap time of 1.27 minutes.