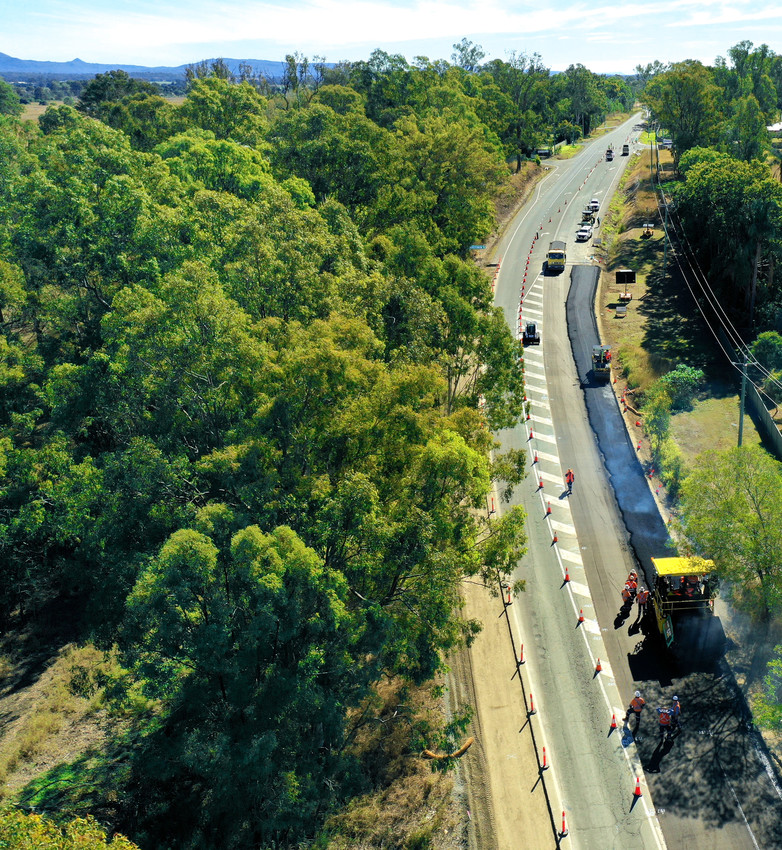
Contractors can now count carbon for every road surfacing and maintenance activity, thanks to a tech start-up called Asphalt-IQ. Its Carbon-IQ app, which operates on a smart phone, can calculate the carbon emissions for road surface, pothole repair and now for planing too.
The difference compared to most carbon calculations tools is the accuracy. Asphalt-IQ sets up the system for each user so that specific details including the mix used, the asphalt plant it came from, the type of plant and equipment used on site and even individual crew members and their travel distances are all included.
Cook’s inspiration for the system came from the US, where some States used coloured plastic discs, which are embedded into the road surface when it is laid. The tags used for the various Asphalt-IQ systems are smart tags in that they are geolocated and will reveal the information connected to them simply by waving a smartphone over them.
Asphalt-IQ still intends to launch its Smart-A-Tags and RoadVault-IQ data storage system, which records pavement composition, thickness and laying details, in the US. However, its priority changed to target the UK market with the publication of carbon management standard PAS 2080:2023. This effectively makes carbon measurement reporting mandatory and National Highways has said that all its suppliers should be working to PAS 2080:2023 by the end of 2025.
Knowsley Borough Council in the Northwest of England has been using Carbon-IQ for 12 months. As part of its development work with the council, Asphalt-IQ created a system to record the carbon emissions for pothole repair activities. Rather than using a smart tag embedded into the road, the pothole system works with a smart card which keeps a tally of emissions from the start to end of the day.
In Germany contractor Strabag has just finished a three-month trial of the system while resurfacing Autobahn A67. It is now moving onto a second trial on secondary roads including pothole repairs and hand laying.
Small firms are also finding Carbon-IQ very useful, with five specialist UK contractors about to start using it. “At the moment, the whole carbon management process can be intimidating and confusing, especially for small companies,” says Cook. “But we have solved the problem. Carbon does not have to be this monstrous headache. And our solution will cost far less than employing a carbon accountant or consultant.”
Asphalt-IQ’s most recent launch is Planing IQ, developed with UK contractor Power Plane. Together they wanted to create something that not only recorded carbon emissions but also made the crew’s life easier. So now, rather than having to complete paperwork for permits to dig and labour returns, the foreman can do it all through the app.
“They have a tick list for the employees and the equipment and, with the smart card, you have the geolocation and the date and therefore a full digital record. We kept the time for inputting all the data to between 1.5 to 2 minutes on site otherwise you would have resistance from the crews,” he says. The app also allows notes to be made via speech-to-text and photos can be uploaded if required as part of the record.
In February, Asphalt-IQ was due to sign a deal with Infrastest Digital Solutions to distribute Carbon-IQ in German-speaking European countries. Australia and New Zealand are also in Asphalt-IQ’s sights. “Although each country is at a different stage in its carbon accounting journey, everyone will eventually realise that accuracy and practicality are the keys to driving reductions in carbon emissions,” said Cook.
Asphalt-IQ’s smart tags were initially invented to record information such as the composition of the asphalt and when it was laid, but in the UK and Europe they are proving useful for recording the carbon footprints of road surfaces
Puma’s biobinder: cost-effective carbon capture
Having launched its CarbonBind bio-binder in Australia, Puma Energy Bitumen is now rolling it out in the UK, APAC, Latin America and Africa. CarbonBind is a blend of conventional bitumen and plant-based material which Puma says sequesters around 150kg of carbon for every tonne of material laid, although that figure varies.
The big difference between CarbonBind and similar products from competitors is its cost, says Puma global technical manager Erik Denneman. “We know that we can offer it cost competitively which opens the door to do it at high volumes,” he said. “There are products on the market that have a larger carbon offset but we did not shoot for the stars. We went for what we could offer at a commercial rate and at high volumes. It’s not just a gimmick.”
While many binders containing bio-based material are based around tall oil from pine trees, Puma’s product comes from agricultural waste that would otherwise have been burned. Denneman won’t say what the waste is or where it is grown, but it isn’t in Australia or Europe. The bio-binder elements is manufactured where the waste material is sourced and processed before being transported to where it is needed via parent company Trafigura’s shipping fleet.
“The benefit of being part of Trafigura is that our biofuels trading desk has access to a lot of different feed stock materials we could assess,” said Denneman. “With this material, there is a significant carbon reduction but it does not cost an arm and a leg.”
Puma carried out the first trial of CarbonBind in December 2022 in Australia with many more roads being laid there since. In November last year Puma won the Australian Flexible Pavement Association’s (AFPA) National Innovation Award for CarbonBind, having won AFPA’s regional awards in Victoria and New Sout Wales earlier in the year. In October 2023, it laid its first trial stretch in the UK with Tarmac.
CarbonBind can be combined with other technologies. So, it can and has been combined with polymer modified bitumen (PMB), Puma’s Olexocrumb product which uses crumbed rubber to modify the bitumen, or both.
Ensuring that materials are long lasting is crucial for reducing carbon emissions, said Denneman: “The first thing we should we doing is making things last longer,” he said. “That’s the quickest way to reduce the carbon footprint.”
Rising RAP content
FM Conway reports that it has used an asphalt mix containing 92% recycled asphalt planings in a road surface for Westminster Council in London, which it says it is the highest recycled content ever for a UK road. FM Conway produced and laid 280tonnes of warm mix asphalt, containing polymer modified bitumen, in a single layer over 1,600m2 of carriageway.
By using recycled material, reducing the heat at which the asphalt was produced and using hydrotreated vegetable oil (HVO) and electricity-powered plant and equipment, FM Conway says that it reduced the carbon emissions by 78% compared to a standard specification for such a road. The residual carbon was offset through Verified Carbon Standard (VCS) units, certified by Verra, to make it a carbon neutral scheme.
Westminster City Council’s head of operations (highways), Phil Robson, said: “It is a really interesting time to be working in highways with partners, and adapting services to achieve climate resilience and low carbon emissions. The transition requires the use of offsets at this time, but we expect to see lower reliance on them over time.”
FM Conway and Westminster Council have been working on several low carbon trials, including projects to increase the percentage of RAP in mixes. In 2019, they laid a mix with 80percent RAP and in 2021, a mix with 85%.
Meanwhile, a 1.8ha (4.5-acre) parking lot at Iowa State University in the US has been repaved using 100% RAP. The difference here is the technology: cold recycling using a soybean-based product called Invigorate Plus from Colorbiotics.
Contractor Elder Corporation milled off the asphalt to a depth of between 100 and 150mm, spread it out across the car park and graded it. The milled material was then sprayed with the Invigorate Plus cold mix solution and compacted with a roller.