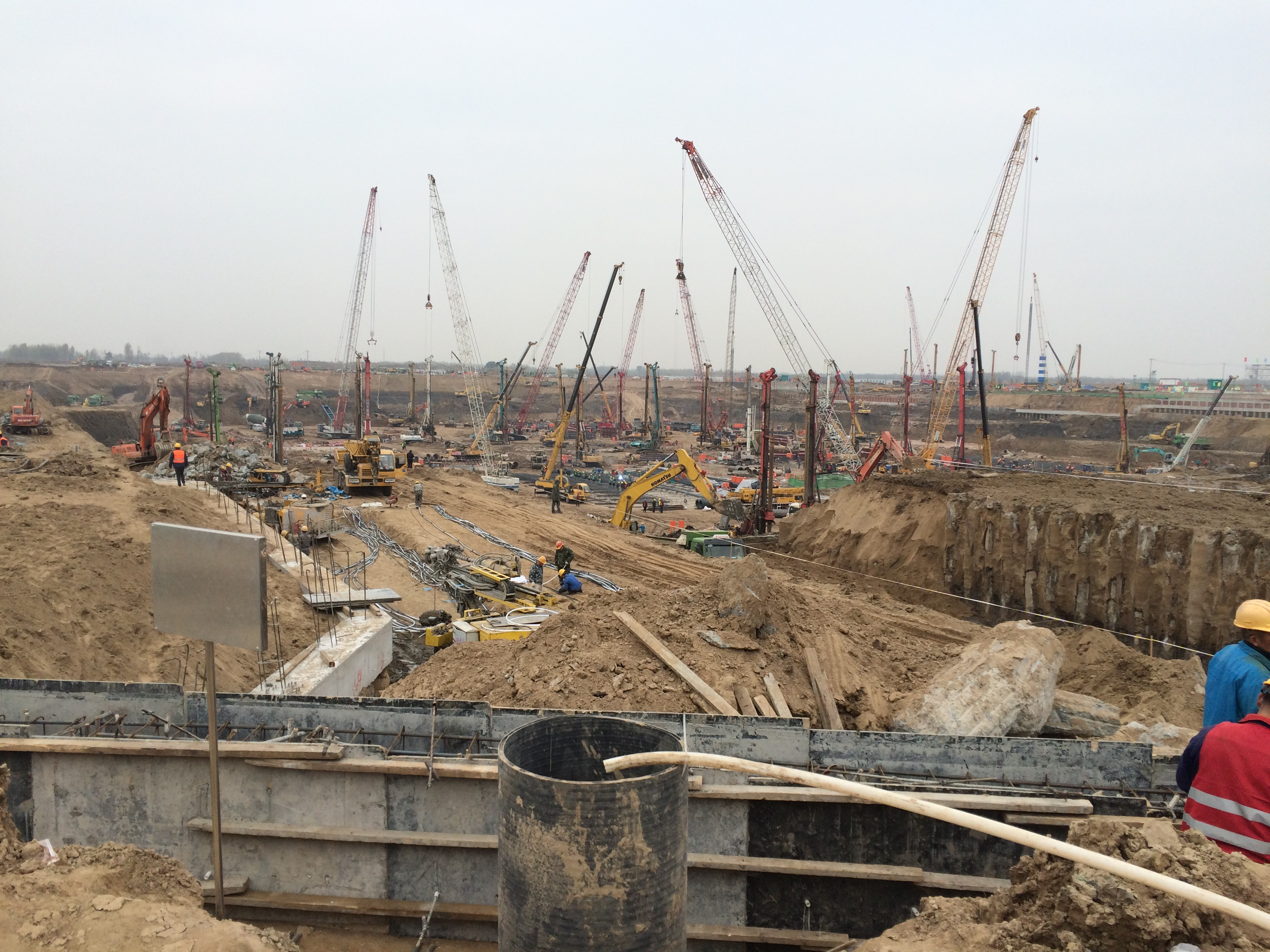
With air travel continuing to increase around the world, airport capacity is being upgraded in many major cities. Two of the world’s largest mega cities, Beijing and Istanbul, are constructing new airports to cope with growing demand. This is because the existing facilities are simply unable to cope with projected growth for aviation and some of the airports are already at capacity. However both cities have shared a common problem, the lack of a site with a suitable geology for constructing such vast facilities. As a result, airport development is now underway for both cities on sites with ground conditions best described as challenging.
Beijing’s existing airport is operating close to capacity and with flight volumes increasing, is not expected to be able to meet the city’s needs so a new facility is needed. But the large area available for construction also features soft sand and very poor underlying geology, which has provided a serious challenge with regard to stabilising the area.
Istanbul’s airport will be one of the largest in the world when complete and is intended to become a major global hub facility. The airport is needed as the existing main facility, Ataturk Airport, is now surrounded by the city and cannot be expanded. However the new facility is being built on former open pit mining sites and forest areas to the north of the city, presenting major challenges for construction.
What is of note is that advanced technologies are being used for the construction of both airports, with sophisticated compaction systems being employed for similar reasons and to deliver similar results.
Covering an area of some 42km2 and located around 46km south of the city, Beijing’s US$16 billion airport is one of the largest construction projects in the world. This work is on a massive scale and includes the diversion of a river course, while the ground conditions feature silty and sandy deposits and have required extensive preparation on the form of dynamic compaction followed by soil compaction.
The success of the technology has been recognised officially in China and Sharp said, “The Chinese Government has now standardised on automated documentation.” Before, the quality assurance methods were limited. He added, “When you look at the end to end workflow, it was successful. That part of the project is pretty much complete now. We proved the methodology for them.”
Site investigations of the conditions at the Beijing airport site showed the need for the system to be used. Sharp said, “The soil was so sandy that we thought our compaction meters weren’t working at first. It took a number of passes before we saw the values start to rise.” Sharp added that it was only when granular material was placed did the ground show significant improvement.
Using the system allowed for a greater level of consistency across the project and Sharp said, “What the CMU did was find where the soft spots and where the hard spots were.”
Sharp explained that the contractor’s best approach is to carry out the compaction work and see when the ground conditions show sufficient consolidation. However, he added that there are no empirical values for this type of compaction and that the work has to be judged on the quality of the results.
As a result, in certain areas of the project, no machines were used with the system and the data was instead hand entered using conventional methods. Sharp commented, “They didn’t get the whole value out of this because they mixed up the fleet of machines. They fell back to using pass counts. Unless you go all in and use technology on all the machines and have training for the workforce, it makes it not so easy to get a good result. We have some work to do to find a better way of doing that.”
With the earthworks now largely complete, the collection of as-built data continues at the airport site however. Information from subsequent construction activities is also being used for the BIM process to comprise the project model.
Similar advances in compaction technology have been utilised at the Istanbul Airport construction project. Located some 35km north-west of the city centre, the area was mined extensively for coal over a long period of years. As a result, the site’s topography was very uneven, with former workings and spoil spread at intervals over the 8,000ha airport site. The construction work has required shifting around 400 million m3 of soil, filling in a number of depressions in the ground and levelling the site as a whole. However, the size of the site and quantity of work needed to deliver consistency to the ground preparation work required the use of some innovative methods. A massive fleet of 136
Using the onboard compaction control technology has provided an effective way to monitor performance and log this data onto a grid, using the GPS location information. The recorded information has been collated and checked at a central laboratory and then further analysed by a consultant to ensure that the work has been carried out to the design specification. Comprehensive documentation of the site has provided the basis for an accurate model of the project, boosting the efficiency of the operation.
Both airport projects are seeing the benefits of utilising new technology to monitor compaction and ensure that specifications are met. With land for construction at a premium in many cities, it is apparent that the ability to deliver suitable ground consolidation on sites that would otherwise be unsuitable is a major step forward. Machine control systems are clearly playing a key role.
According to Sharp, acceptance of machine control technologies is now widespread in the construction sector compared with 20 years ago, when adoption was slow. He said, “Once the contractor has adopted the technology, the contractors start seeing the advantages. This process has helped them to understand.”