BOMAG’s highly sophisticated compaction control technology is now being used successfully on the highway project to link Warsaw with St Petersburg. The system is being employed in the rural area around the border triangle of Lithuania, Latvia and Belarus. Lithuanian road contractor Panevezio Keliai won the package of works to upgrade a stretch of the E262 in Zarasai.
The project requires high quality as the E262 route links Warsaw with St Petersburg and carries a large volume of traffic, including a hig
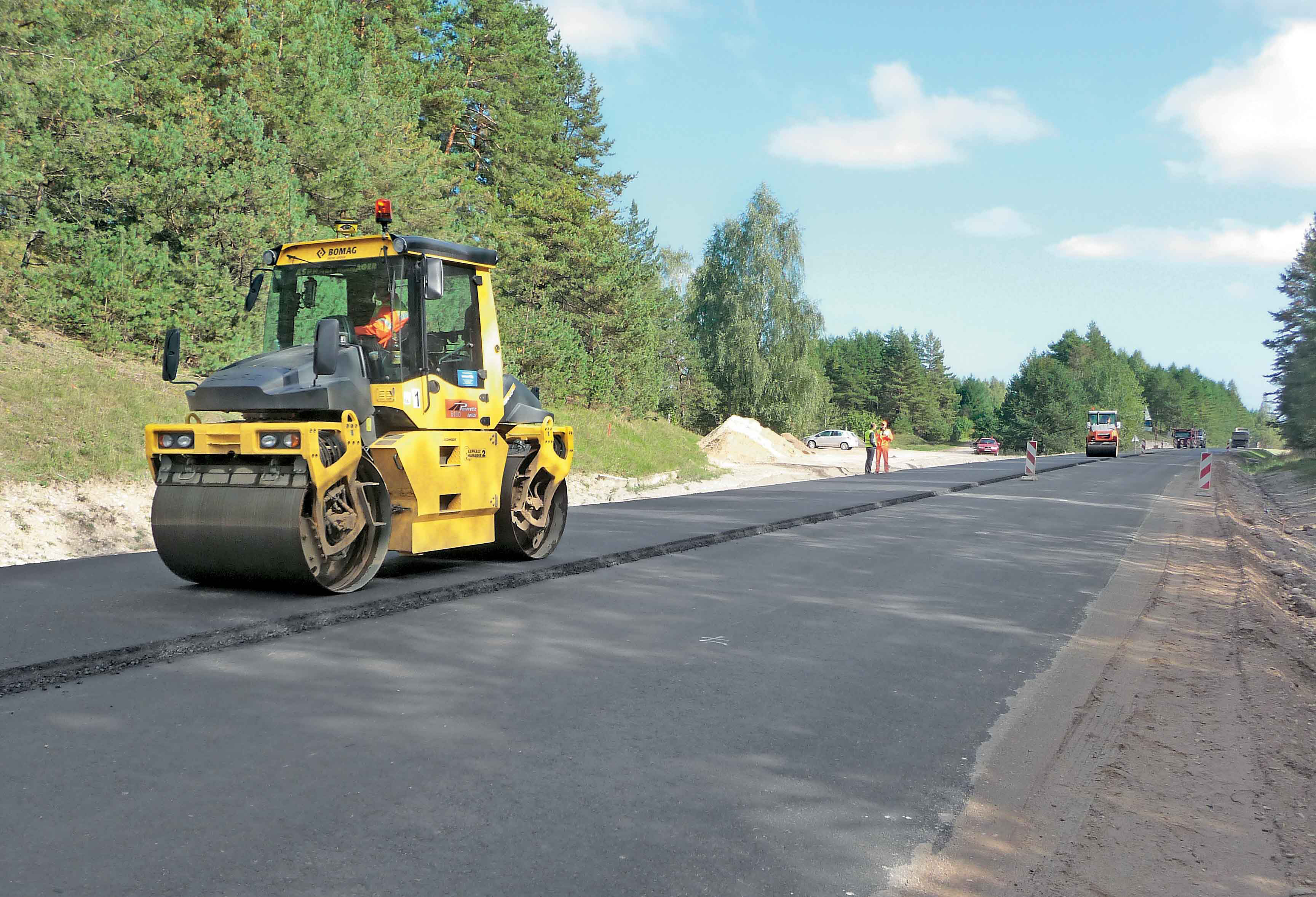
Efficient working was achieved in this remote location in Poland
BOMAG’s highly sophisticated compaction control technology is now being used successfully on the highway project to link Warsaw with St Petersburg. The system is being employed in the rural area around the border triangle of Lithuania, Latvia and Belarus. Lithuanian road contractor Panevezio Keliai won the package of works to upgrade a stretch of the E262 in Zarasai.
The project requires high quality as the E262 route links Warsaw with St Petersburg and carries a large volume of traffic, including a high percentage of heavy vehicles. As a result, Panevezio Keliai uses the172 BOMAG Compaction Management (BCM net) package to ensure the high compaction quality requirements of the project are met.
The compaction control system is used to links the machines being used and integrates a tablet PC and a GPS receiver into every single compactor. This provides the compactor operators with a continuous overview of the number of completed passes, temperatures and work progress. As well as a general overview, with the tablet PC in the cab, the operators can see the results enabling them to optimise their working schedule. The drivers can follow the development of a compaction map on the tablet. Data on passes, temperature and the EVIB value for asphalt stiffness are displayed visually and saved for documentation. The colour display shows the operator where there is still work to be done and what areas are within specification.
The contractor had BCM net installed in four rollers. Two new BW 174 AP-AM tandem rollers were equipped with the system in the factory, while a BOMAG BW 174 AP from stock and a roller from a different producer were retrofitted with the package. An advantage of this package is that it can be used on compactors from other suppliers, although it works particularly well with BOMAG machines featuring the firm’s own ASPHALT MANAGER system. This is because the ASPHALT MANAGER package measures the stiffness of the mat continuously and also sends the values to the BCM. The EVIB value in MN/m² correlates with the density and the system is able to use the BCM to see when the required density has been reached.
The proven BCM system can display and save the data of single machines but the newer BCM net package allows several machines to be connected at the same time.
Before starting compaction, the team used a778 Troxler gauge to determine the number of passes needed to achieve the required 98% density. It is common practice to pave with AC22 type asphalt to a thickness of 90mm. However care is required should the material react to vibratory compaction with deformation. On the E262 project Panevezio Keliai opted to use 10 static passes and the BCM net system has proven highly beneficial in ensuring the correct rolling pattern is achieved.
The system allows the compactor operators to concentrate on driving the machines, improving site safety. The system also provides information on the asphalt temperature on their monitor, preventing the operators from driving too early onto hot material. A further option of monitoring the asphalt temperature as it is laid by the paver has yet to be explored by the contractor but the firm is considering using this feature also.
The system is said to be easy to use and requires minimal instruction as the operators only need to switch the tablet PC on and off. The coordination of the construction processes and analysis of the resulting data is also simplified for the site manager, while preparation and post-processing can be carried out on a PC in the office.
The quantity of data that the system provides was a key factor in the firm opting for this technology. Using the information the BCM system provides is now allowing the firm to optimise its processes. Regardless of the setting selected, everything is documented: passes, temperatures, EVIB, speeds, vibration and area output. The package also helps increase safety on site, by minimising the personnel needed in the working area and providing up-to-date information on the precise location of every single piece of equipment.
All the machines are connected with each other using a broadband link and there are no lags caused by mobile telecommunications or servers, allowing real-time imaging and maximum availability. Even if the broadband connection were to be interrupted, no data would be lost and the firm has proven that the system can operate even when the machines are up to 400m apart, a factor that has been particularly important when the construction site is as remote as the E262 in Zarasai.
The project requires high quality as the E262 route links Warsaw with St Petersburg and carries a large volume of traffic, including a high percentage of heavy vehicles. As a result, Panevezio Keliai uses the
The compaction control system is used to links the machines being used and integrates a tablet PC and a GPS receiver into every single compactor. This provides the compactor operators with a continuous overview of the number of completed passes, temperatures and work progress. As well as a general overview, with the tablet PC in the cab, the operators can see the results enabling them to optimise their working schedule. The drivers can follow the development of a compaction map on the tablet. Data on passes, temperature and the EVIB value for asphalt stiffness are displayed visually and saved for documentation. The colour display shows the operator where there is still work to be done and what areas are within specification.
The contractor had BCM net installed in four rollers. Two new BW 174 AP-AM tandem rollers were equipped with the system in the factory, while a BOMAG BW 174 AP from stock and a roller from a different producer were retrofitted with the package. An advantage of this package is that it can be used on compactors from other suppliers, although it works particularly well with BOMAG machines featuring the firm’s own ASPHALT MANAGER system. This is because the ASPHALT MANAGER package measures the stiffness of the mat continuously and also sends the values to the BCM. The EVIB value in MN/m² correlates with the density and the system is able to use the BCM to see when the required density has been reached.
The proven BCM system can display and save the data of single machines but the newer BCM net package allows several machines to be connected at the same time.
Before starting compaction, the team used a
The system allows the compactor operators to concentrate on driving the machines, improving site safety. The system also provides information on the asphalt temperature on their monitor, preventing the operators from driving too early onto hot material. A further option of monitoring the asphalt temperature as it is laid by the paver has yet to be explored by the contractor but the firm is considering using this feature also.
The system is said to be easy to use and requires minimal instruction as the operators only need to switch the tablet PC on and off. The coordination of the construction processes and analysis of the resulting data is also simplified for the site manager, while preparation and post-processing can be carried out on a PC in the office.
The quantity of data that the system provides was a key factor in the firm opting for this technology. Using the information the BCM system provides is now allowing the firm to optimise its processes. Regardless of the setting selected, everything is documented: passes, temperatures, EVIB, speeds, vibration and area output. The package also helps increase safety on site, by minimising the personnel needed in the working area and providing up-to-date information on the precise location of every single piece of equipment.
All the machines are connected with each other using a broadband link and there are no lags caused by mobile telecommunications or servers, allowing real-time imaging and maximum availability. Even if the broadband connection were to be interrupted, no data would be lost and the firm has proven that the system can operate even when the machines are up to 400m apart, a factor that has been particularly important when the construction site is as remote as the E262 in Zarasai.