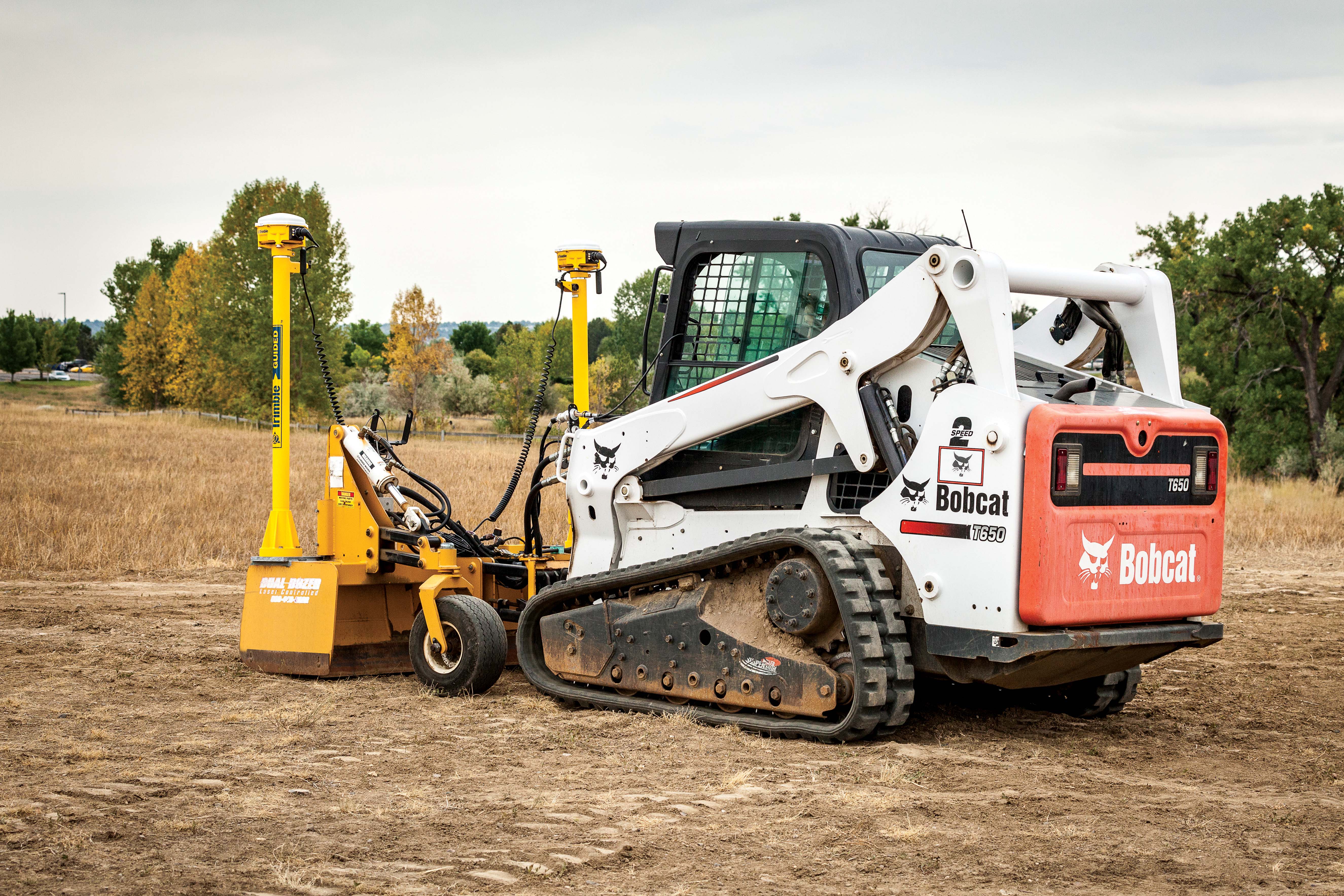
New advances in machine control systems are revolutionising the construction industry - Mike Woof writes
At the top end of the scale, work on the new Beijing Airport is benefiting from a highly sophisticated approach that will go a long way towards optimising the construction process. Trimble is closely involved with the management contractor that is working on the construction of the airport. The two are involved in a research project, which is being funded by the Chinese Government and is investigating digital construction methods. The US$16 billion airport project covers an area of some 42km2 and is one of the largest construction projects in the world, with the preparatory work including the diversion of a river course. It is highly challenging as the ground conditions feature silty deposits and are very poor, with a great deal of preparation being required to ensure that there will be no future subsidence of the site.
According to Alan Sharp, business area director for the civil engineering and construction software solutions division, this approach is allowing project design of the project to be delivered with confidence. An advanced asset management solution, this will track factors such as quality, progress and productivity. It is being used right from the start of the work on the airport site, initially for the earthmoving, dynamic compaction and soil compaction functions. As the project progresses, this methodology will continue to be used through all aspects of the construction, particularly as the early results are already proving the value of this radical approach.
The Chinese Government is pushing ahead with technology with its investment in research into digital construction and Sharp said, “We’re working with Chinese companies to track key metrics for the project.”
Because of the soft ground conditions, a key starting point for the use of the sophisticated GPS technology has been on the dynamic compaction machines. These units drop a certain weight from a certain height a certain number of times to ensure that the ground is compacted sufficiently. The displacement is tracked using sensors and Sharp said, “You’ve got real-time information.”
The sheer quantity of data available is giving the engineering team pause for thought and Sharp commented that this raises key questions, “What to do we need to know and what don’t we know? It gets into the debate as to what is the specification and what is the quality.”
In a conventional operation contractors would typically record data on paper, but this process is not always particularly accurate. Data can get mixed up or approximated. However, with the recording tools on the dynamic compaction machines, the engineering team at Beijing Airport is receiving an accurate picture of what is actually being carried out. “Now you’ve got all the information and everybody’s got visibility,” Sharp said, adding that this allows the contractor to see where problems are occurring and means positive steps can be taken to ensure that these are addressed.
He continued, “We’re taking care of correlation and it gives them a better understanding of the project than before.”
Trimble’s involvement in the airport project goes far beyond machine control and is benefiting from its investments and acquisitions, such as the purchase of the Norwegian
The method being implemented is based on the use of machine control systems but is now providing a much higher level of information than before. He said, “The constructible model is what the contractor uses. It breaks down the job into separate tasks.” He added that this goes far beyond a designer’s original 3D models also, adding in additional levels of data for costs and time, for example.
“They’re keen to make sure they get quality. We did all the data modelling for them and showed them how to analyse the data. We track everything that happens in an area and you see everything in construction layers. You can see what problems you’ve had,” he said. And the project is revolutionary in many respects according to Sharp. We feel we’re pioneering a new development.”
Rather than using all the data all the time, the engineering team is looking at managing by exception. If the dynamic compaction parameters are met, work carries on as normal. Sharp said, “If something shows up in red, you know that’s where you have to focus.”
He explained that this is changing the way a contractor operates and said, “You can’t get that from a design so you have to change the way you’re going to model.”
The BIM approach is being implemented on the Beijing Airport project, with Trimble also having revised its portfolio to suit the work being carried out. He explained, “We had to change the models so that everybody was working off the same information. Software hasn’t been mainstream for Trimble in the past but this development has been crystallised by Beijing Airport.”
Meanwhile, machine control solutions are also delivering efficiency gains at a far more basic level for the construction sector. The development of machine control systems for use on compact machines is a notable development. These can be fitted to rental machines such as mini excavators or skid steer loaders and meet the needs of customers requiring simple tools.
Scott Crozier is business area manager for site positioning solutions in the civil engineering and construction division while Jeffrey Drake is segment manager for machine control systems in the heavy construction division. Drake said, “The focus is to target to smaller contractors.”
The firm has developed 3D solutions for skid steer loaders and mini excavators, for example, which are now being taken up by customers in the rental market. For example, the firm now offers the GCS900 Grade Control System for grader attachments on
Drake continued, “It’s starting to trickle down to the smaller contractors. We’re making it simpler for them to use the technology.”
Crozier explained that basic, cloud-based design software package is also widely available and becoming highly popular in the industry for use on smaller projects. Drake said, “You can do a simple design in 10 minutes and you can export that to field software and put it into a machine. The technology allows you to use that design on compact machines like mini excavators or skid steer loaders.”
Crozier added that this offers considerable benefits for smaller contractors, as these firms are able to capitalise on the efficiency gains from using machine control systems. He said that with rental firms also now fitting the systems on some units, the safety and productivity gains can be substantial. Construction firms can take a simple design that is also georeferenced, show it to a potential client on a laptop and evaluate various issues over a project even before work starts. Crozier said, “We’re taking large site technology and boiling it down for those smaller customers.”
For larger projects, the benefits of machine control systems are well understood. The technology has allowed massive gains in output and efficiency, with this also having been introduced on road projects where implementation has been tricky in the past due to the sheer length of the construction sites. Drake said, “The connection between office and field is two- way and this data flow allows you to make better decisions. A lot of mid-large projects implement connectivity. It’s amazing on a productivity basis.”