Modern weighing equipment helps road operators tackle the costly business of road damage caused by overloaded trucks as Patrick Smith reports. Overloading of commercial vehicles has a major impact on the life expectancy of road networks. The cost of premature road failure and repairs is a major burden on many governments particularly in developing countries where this problem diverts vital funding that could otherwise be spent on health and education.
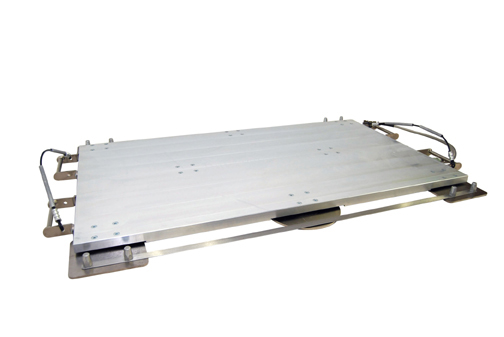
The Intercomp LS700 WIM system: 'a cost effective method to savings in avoided pavement damage'.
Modern weighing equipment helps road operators tackle the costly business of road damage caused by overloaded trucks as Patrick Smith reports.
Overloading of commercial vehicles has a major impact on the life expectancy of road networks. The cost of premature road failure and repairs is a major burden on many governments particularly in developing countries where this problem diverts vital funding that could otherwise be spent on health and education.There is also the human cost, where lives are lost on a daily basis due to vehicles being dangerously overloaded, and this affects braking, steering and vehicle stability. In many developing countries, overloading is an everyday occurrence with as many as 60% of the trucks being overloaded. The degree of overloading is also dramatic. In Europe, overloads of 5-10% are a concern, in countries such as Pakistan, India and the UAE, many vehicles are found to be 30-50% overloaded.
Countries such as India and Pakistan have developed a strategy to combat this problem which includes the installation of axle weighing systems at many of the toll stations being built along the length of the major motorways, and
The company's new Supaweigh 5000c, installed in India, is a medium speed, in-motion axle weighing system providing high accuracy weighing results even at speeds of up to 30km/hr. It has a capacity of 40,000kg per axle, and this says Central Weighing makes it ideal for the high axle loading so common in the region.
"A special load cell loading assembly makes damage by drivers determined to beat the system a thing of the past, and in addition, the instrumentation has all been tropicalised to withstand the extremes of heat, dust and rain.
"Many of the new roads are being built and managed by road concessionaires who, to some degree, gamble on the level of road damage they are likely to experience to calculate the road design and frequency of repair. In the past they have been reliant on axle surveys to give an indication of the number of axles that pass along a particular section of road. Road constructors used an assumed average axle weight of 8,100kg, called an equivalent standard axle (ESA). This is a good average in developed countries where overloading is well controlled but in developing countries, the extent of overloading makes this calculation dubious to say the least," says Central Weighing.
It gives as an example an axle load of 17,000kg (common in these countries), which has an ESA of 19.41, nearly 20 times the damaging factor of the assumed 8,100kg.
Vehicles with this level of overload will quickly reduce the life expectancy of a road by up to 70%, dependent on the construction methods applied by the road designer. In regions such as the UAE, individual axle loads of over 30,000kg are not uncommon.
One of the features of the new Supaweigh system is that it calculates the ESA level for every vehicle it weighs and produces a statistical report to give concessionaries the vital information they require.
In countries where fixed weigh stations are not an option or where drivers find every opportunity to avoid these stations, the company says it has developed a new portable truck scale system, Freeweigh, which weighs only 30kg, and consists of a weighing console, which communicates by bluetooth to two low profile weighing pads up to 30m away.
It records the weight of wheels, axles and the total vehicle as trucks are driven slowly over the system without stopping. The advanced weighing console produces an individual weight ticket customised to the requirements of any enforcement agency.
"The system stores the legally permitted weights for any vehicle combination in any country and produces an instant overload warning and print-out when any of these weights are exceeded," says Central Weighing.
Intercomp LS700 WIM SYSTEM
"In recent years, increased traffic volumes have increased the demands on roads and, in addition, the increased price of fuel has provided further incentive to overload trucks," it says.
However, it points out that there are comparatively inexpensive weigh-in-motion (WIM) devices, which are designed to capture and record truck axle weights and gross vehicle weights as they drive along, without the need for trucks to stop, thus making them much more efficient.
For example, the Intercomp LS700 WIM system is said to be a cost effective method to savings in avoided pavement damage, and this does not include the increase in safety due to detecting unsafe vehicles or increased vehicle costs due to driving on roads in need of repair. The portable system can be set up in any area that is relatively smooth and allows vehicles to reach a steady speed between zero and about 10km/hr.
Its main computer, an industrial grade laptop, is housed in a transport case along with the printer, and all cables run from the scales to receptacles in the transport case. The connectors are military approved to ensure consistent performance.
The cables are conveniently stored inside the transport case on aluminium spools, while the entire WIM system is built for a harsh outdoor environment: it can be used in climates between -10° to +50°C.
"If desired, your own computer can be used with the Intercomp software. Both law enforcement and fleet management software are available," says Intercomp.
The system is automatic and starts collecting data as soon as weight is applied to the weigh pads. The weight is stored after the vehicle has passed over the scales, and the following data is then displayed: number of axles weighed, axle spacing, velocity, classification and lists overloaded axles or axle groups. The data can be used alone or concurrently and results may be viewed on the CPU computer screen or exported as a delimited text file.
The heart of Intercomp's WIM system is the electronic strain gauge load cells, which in each scale pad work together to provide highly accurate weighing with an ultra-low 2.54cm high profile.
"Electronic strain gauge load cells were chosen for several reasons. They are accurate, have minimal hysteresis, are low profile and rarely fail because they are essentially solid state. Individual load cells can be easily replaced if needed," says Intercomp.
Electronic load cells function because wires attached to the surface of the cell will elongate when the cell is subjected to bending. The resistance of the wires will change as they are stretched, and the change in resistance is calibrated to a given force.
The load cells, in conjunction with an aluminium platform, enable Intercomp to offer a scale with a capacity of 9,000kg with a system capacity of 18,000kg. The scales feature 0.1% accuracy with static weights and +/-1% at 3m/hr or 5km/hr. The scales are also self-calibrating. Hysteresis is minimal because the cells displace such a small amount that they quickly return to their original shape.
To set up the Intercomp WIM system takes two people about 15 minutes: the scales are placed in the centre of the weighing area, and the spacers connect to the scales like a jig-saw puzzle.
"The Intercomp LS700 WIM system is a versatile tool that can be used to increase the lifespan and safety of highways by monitoring the weights of vehicles. WIM also has commercial applications," says Intercomp.